Techtextil 2023 Provide Platform for Companies to Attract the Sustainably Minded
Market-leading innovations from over 350 exhibitors from 30 countries combined with thousands of attendees gathered for Techtextil North America and Texprocess Americas in Atlanta, held at the Georgia World Congress Center in May 2023.
The Techtextil Symposium was well-attended, highlighting functional fabrics, circular economy, medical textiles, aerospace and defense applications and nonwovens. Tech Zone Talks were presented by exhibitors, and the Tech Zone talks were mini sessions on specific niches like ChatGPT and Design, PFAS, Circular Polyment, Biocatalytic textiles, and more.
Focusing on two key Techtextil symposium discussions, the advancements and solutions to tackle textile’s well-documented environmental challenges were on aplenty from platforms and show floor presentations, spilling over into exhibitor booth discussions.
Key Symposium Notes
In Innovative Fibers for a Circular Economy, reducing plastic consumption was a high priority during one opening session for Techtextil North America. Diana Wyman of ATTCC moderated a panel that included Sonja Salmon, Ph.D., associate professor of textile engineering, chemistry and science, North Carolina State University; Harrie Schoots, consultant for Fibers52; and Andrea Ferris, CEO, Intrinsic Advanced Materials.
With expertise in bio-based textile materials and processes, Professor Salmon focused her comments on her research, Enzymatic Conversion of Cellulosic Textiles for Recycling.1 The project resulted in the successful separation of cotton from polyester in blended fabric. “We can separate all of the cotton out of a cotton-polyester blend, meaning now we have clean polyester that can be recycled,” said Salmon. “In a landfill, the polyester is not going to degrade, and the cotton might take several months or more to break down. Using our method, we can separate the cotton from polyester in less than 48 hours.”
Harrie Schoots discussed his work with Fiber52, a company focused on sustainable dye solutions for cotton. “There is a lot of talk today about recycling fibers which is good, we need to do more of this,” he said, focusing his discussion on cotton fiber as a go-to fiber with enhancements. “A lot of water is being used in today’s cotton scour and bleach process and dyeing and finishing. Fiber52™ comfort cotton brings a patent-pending technology that minimizes the use of resources at this phase.” The technology allows textile manufacturers to continue using the same machinery, but replace harsh chemicals with inexpensive bio-products, and achieve the same quality results. There is also savings on heat, energy, water, and time.
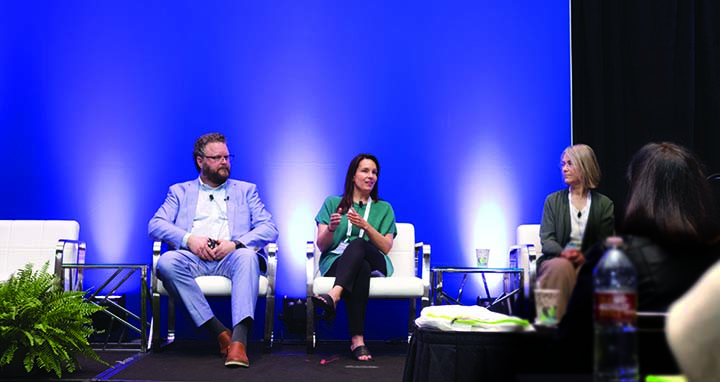
Intrinsic Advanced Materials CEO Andrea Ferris discussed the company’s advancement to eliminate micro plastics. “CiCLO® is biodegradable technology aimed to reduce the impacts of fugitive synthetic microfiber pollution in the oceans,” she said. “Our seas are truly sick. Biodegradability of plastic doesn’t always make sense, such as small single use straws, etc., but there are times when biodegradability is essential. We have an upstream solution that balances durability and sustainability.” CiCLO® technology is a sustainable textiles ingredient in the form of an additive that is combined with polyester and nylon during melt extrusion at the very beginning of the fiber-making process. When CiCLO®-enhanced fibers end up in environments where biodegradation can occur naturally, microbes are attracted to the fibers and can mineralize them at rates comparable to natural fibers, such as wool.
Delving into Nonwovens Advancements, the session was moderated by Behnam Pourdeyhimi, executive director of the Nonwovens Institute, with expert panelists Charles Vaillant, CTO/CDO, Mann+Hummel Group; Bryan Haynes, Ph.D., Technical Director Global Nonwovens, Kimberly Clark; and Jeff Strahan, Ph.D., Sustainability and Compliance, Milliken & Company.
Charles Vaillant led the discussion with vehicle filtration. Filtration support is a challenge of today’s society with the increases in air quality and regulations, notes Vaillant. “They are tightening the regs on what is acceptable for humans. Pollutants need to be reduced. Europe and North America have the cleanest air in the world, but other countries are not so good. Ultra-fine particles are numerous, invisible, and dangerous – the lungs are not capable to deal with them and they end up in bloodstream. Mann+Hummel is focusing efforts on Smart Cabin Air Filter systems, where sensors to determine the air quality inside and around the vehicle. This leads to a lasting improvement in air quality, while at the same time reducing energy consumption. They are utilizing HEPA filtration of ultrafine particles (<0,1 μm), combined with sensors that continuously control the system and monitor the air quality, making for cleaner and safer cabin air. “The traffic jam is where you need protection,” Vaillant notes. Moving towards EV filtration, M+H’s Intelligent FreciousSmart cabin air filter system provides clean air and simultaneously reduces power consumption, something the company says is a perfect concept for electric vehicles.
Brian Haynes provided a historical perspective of plastics and textile pollution. How big is this, he asked? “First disposal product was invented in 1950s. We have spent the last 70 years producing 20 trillion pounds of plastic, enough to fill 8,000 football stadiums.” Why should we care? “We eat one credit card of plastic each week. It is everywhere.” He noted that if we continue, by 2040 plastic pollution is estimated to increase 300% by 2040. “It is an industry wake-up call,” he said, that requires a very strong industry response and aggressive plans to deal with plastics. He suggests that companies look for partnerships for innovation pathways.
At Kimberly-Clark, “By 2030, we want to achieve 50% reduction in our plastic use. Eventually, we want to get to circularity with packaging, product, and waste management systems. There is no silver bullet, it will take all the above,” he notes. Labeling it “coopetition,” he believes it is going to take a combined effort to address this in the years to come, with emphasis on bio-based feedstocks, recycling, composting pathways, and other combined efforts.
“All companies here at Techtextil will be required to have science-based targets in two years,” shared Jeff Strahan in his discussion. Net zero by 2050 goals are covered in the Paris Agreement, where the EU and 194 states, totaling over 98% of anthropogenic emissions, have ratified or acceded to the agreement. Interestingly, Science Based Targets (SBTi) is a nonprofit that manages the net-zero data global data and regularly adds companies to their list at sciencebasedtargets.org, in blockchain style, on Scope 1 (direct fuel usage), 2 (indirect GHG emissions), and 3 (indirect emissions from downstream and upstream operations) stages of compliance. Milliken and Company is one of the first 50 companies to have verified net-zero targets by SBTi and is well on their way to meeting the 2050 goal. To date, they are on track to meet company Scope 1 and 2 greenhouse gas emissions goals (50.4% by 2030), and Scope 3 goals (30% reduction by 2030), which include supply chain partners.
Award-Winning Innovations
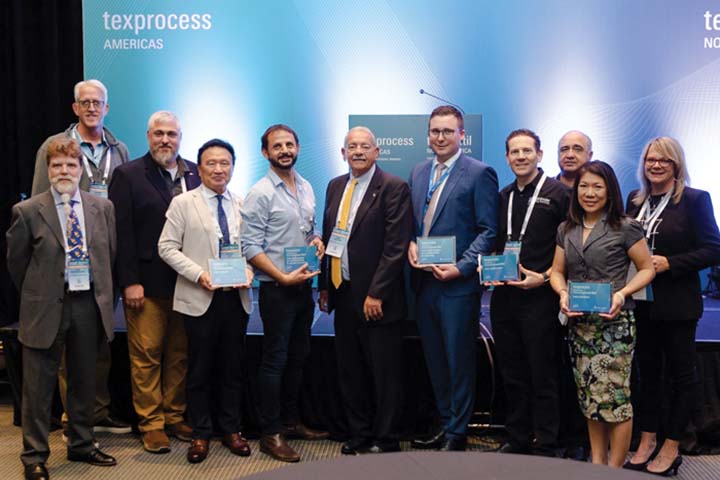
Shining a light on the industry’s cutting-edge advancements, the Innovation Awards 2023 revealed the front-runners of innovative textile technologies. “We are happy to bring the Innovation Awards to the U.S. editions of Techtextil North America & Texprocess Americas which will enable and encourage new market developments and is a testament to the ingenuity and vision of the brands participating at these shows,” says Kristy Meade, Vice President of Technical Textiles & Technology Shows for Messe Frankfurt, Inc. The award-winning developments were presented to:
New Concept Winner: Henderson Sewing Machine Co. Inc. and Matsuya R & D For the development of “The Intelligent Robot Sewing Machine with Digital Image Processing System”
New Technology Winner: SPEC and Svegea of Sweden for the development
of “SVEGEA EC-450XF”
New Application Winner: Pathfinder Cutting Technology for the Development of “FabricPro: Revolutionizing Fabric Spreading with Innovative Safety Features and Improved Operator Ergonomics”
New Product Winner: Stratasys for the development of “Stratasys J850™ TechStyle™ direct-to-textile 3D printer”
New Approaches on Sustainability & Circular Economy Winner: Henderson Sewing Machine Co. Inc. & Twine Solutions Ltd for the development of “Thread Digital Dyeing System TS-1800”
New Technologies on Sustainability & Recycling Winner: Dürkopp Adler GmbH for the development of “M-TYPE DELTA e-con”
New Technology & Digitalization Winner: SEDDI For the development of “SEDDI Textura: Real Fabrics Digitized Brilliantly with AI”