President Van Durrett and Assembly Manager Walt Puckett with a new Series 40 Cutter that is ready for shipment.
Although some segments of the North American textile industry may best be described as “mature,” in the heart of North American textile country there is one, very unique manufacturer that plays a key role in the global textile fiber industry. DM&E and its 29 employees combine technology and experience to insure the precise cut and crimp of synthetic fibers of all descriptions being produced all over the world. The DM&E customer base is global, served by agents in China, India, Mexico and Turkey. Shipments to China began in 1993 and have continued ever since.
Over 40 years ago, Van Durrett and his long-time friend, Harry Puckett, opened the doors of DM&E in Shelby, North Carolina and began by repairing and rebuilding machinery of the nearby textile mills and fiber producers. As they grew, they focused their business to become specialists in the repair and rebuilding of tow processing equipment. DM&E survived the recession years that began in 2007 and has since grown by expanding international opportunities through both the Internet as well as the readership of International Fiber Journal. According to Durrett, this is the type of business where new customers don’t just walk in the front door.
Today, the average experience of DM&E employees is 17 years. Bob Mosteller, a former machinist and now the purchasing manager, is the most senior member of the organization with 39 years of experience. Through the past decades, employees have developed an emotional connection with their work. Walt Puckett, son of Durett’s original partner, Harry Puckett, is a key member of the team and often travels to customer locations to install new equipment. The skills required for employment at DM&E means that staffing is an ongoing challenge. DM&E also works closely with the County Technical School to insure the development and training of future machinists.
The radial cutter technology replaced various early cutters that used blades to literally chop the tow. Although radial cutter technology was an Eastman innovation, DM&E acquired the tow cutter business from Lummus in Savannah, Ga. in 2000. What followed was the result of innovation at DM&E in response to their customers’ demands for cutters to produce short cut fiber of often-exotic polymers ranging from seaweed or milk derived polymers to HDPE, liquid crystal, aramids and even carbon fiber. Durrett commented that there has been a definite shift in focus from the 37mm and 51mm cut length fiber to 1.5mm and 2.0mm staple lengths for use in wet-lay applications. A radial type cutter to produce 1.0mm cut length fiber is yet to come.
In response to customer and industry demand, DM&E is producing more new cutter reels than ever before. What once was a rebuild and repair business has evolved into a company that builds complete new cutters and installs them around the world. Their “60 series” cutter has many improvements: the 5hp motor of the original design has been upgraded to 15hp with a double reduction gear and a braking system. A pneumatic pressure wheel has replaced the spring formerly used in the original design and sensors have been added to monitor the load against the cutter blades. As a result, as soon as the DM&E Quality Team complete a “60 series” cutter, it is sold and they have to start anew. All improvements enable their fiber producer customers to reliably meet the growing demand for short cut fiber in the marketplace. The core of their business today is new cutters, cutter reels and crimpers. The business model has shifted.
The manufacturing process for new radial cutter reels starts with thick circles of stainless steel supplied by their stainless steel supplier. DM&E then machines the circles on their lathes to the specifications required for their customer’s radial cutter. Slots to hold the long, stainless steel or tungsten carbide steel blades are precisely cut into the circles using EDM technology. Although some fiber producers use the same radial cutter successfully to produce different staple cut lengths by removing blades at intervals, doing so on a 600 blade radial cutter could challenge the integrity of the cutter and could lead to both a loss of quality in the cut staple fiber as well as damage to the slots of the cutter reel. Cutters for “random cut” fiber are also manufactured and rebuilt at DM&E.
Designs for other equipment come in many formats to DM&E. Customers often submit two-dimensional drawings that the company converts to 3-D designs that are then translated by proprietary software into a tool path. Each opportunity creates a new challenge in their unique business. DM&E ships about 100 rebuilt and repaired cutter reels each year and can usually complete any needed repairs within 6 – 8 weeks.
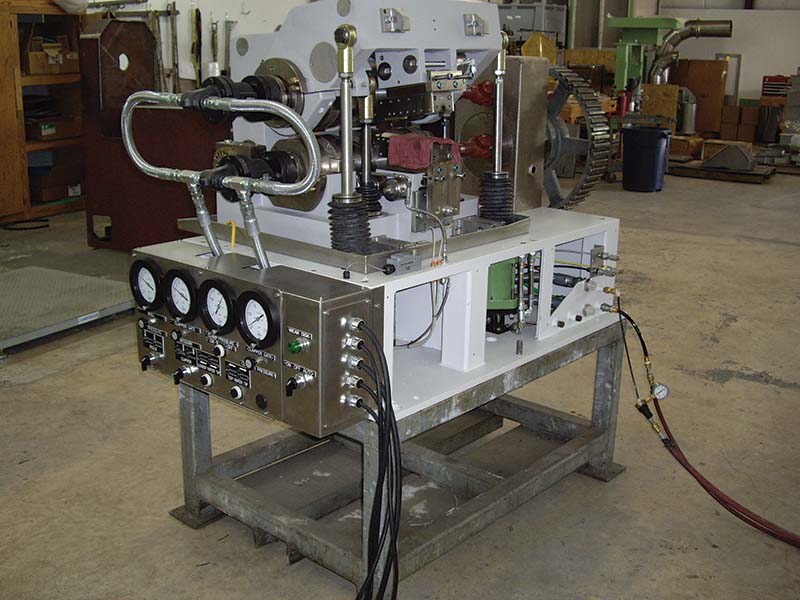
Whether simply replacing bearings, milling the rollers of a tow crimper to insure perfectly smooth surfaces or simply replacing cutter blades, rebuilding or repair is definitely cost-effective. The cost to repair a cutter reel can be as little as 5% of a new reel and the cost of rebuilding a crimper can be as little as 25-30% of the cost of new. Years ago, the “sweet spot” for DM&E was the repair and rebuilding of tow crimpers and radial blade tow cutters. Today, that “sweet spot” has changed to “new” equipment. Proving that it is much more than just “another manufacturer,” Durrett’s team have even produced engine parts for drones and experimental aircraft as well as material handling equipment used in the production of CDs and DVDs.
Above all, because DM&E technicians understand the fiber production process and have the in-depth experience, they are often able to offer production solutions to their customers’ problems. Its small size and its flexibility offer DM&E customers a distinct advantage over competitors. When Durrett and his team are asked, “Can you do it?” Well, let’s just say that “can’t do it” just isn’t in their vocabulary.
DM&E will soon celebrate the beginning of its 40th year and is planning a “birthday” party for its employees, and their families, all of whom have made DM&E what it is today, a vital part of the global synthetic fiber industry.
For more information contact: DM&E
Website: www.dmecutter.com