The textile machinery branch of Germany’s VDMA, the Frankfurt-headquartered mechanical engineering industry association, held a series of webinars showcasing the technologies of some 30 of its members between June and December 2020.
Understandably, many of them concerned the sudden demand for facemasks and PPE last year – in which meltblown polypropylene microfibers proved such a vital component. Many German companies have benefited from their government’s support of a new infrastructure program for facemasks, in which it is covering 30% of the cost of a meltblown production lines and related manufacturing and converting equipment, along with guaranteed order contracts, if the manufacturer pledges to sell exclusively into the German and European market until the end of 2023.
A second focus was on achieving savings in energy, water, and raw materials, primarily in dyeing and finishing – by far the most resource-intensive stage in textile processing.
Since synthetic fibers have been the focus of so much negative attention over the past few years due to their ecological downsides, it is perhaps timely to consider the substantial contribution that has been made to modern life by three synthetic fibers in particular – para-aramids, ultra-high molecular weight polyethylenes (UHMPWs), and not least carbon fibers.
A notable development here, is the commercialization of new spray application technologies that offer tremendous savings in terms of water, energy, and chemicals. These savings are achieved by applying only the required amount of dye or chemical finish to the surfaces of fabrics, with their precision made possible by the latest sensor-based control systems. When considering that the textile industry uses on average between 100-150 liters of water to process 1kg of textile material and some 28 billion kg of textiles are dyed annually, claimed savings of up to 90% have clear potential for the industry’s future.
The last VDMA webinar, however, held on December 2nd, featured three German companies providing essential services to the technical textiles and composites sectors – Georg Sahm (Eschwege), Herzog (Oldenberg) and Karl Mayer (Obertshausen).

Contribution
Bena Manasieva Cavus, business development manager for Georg Sahm, described her company’s specialized engineering of winders and automated bobbin handling systems designed for effectively dealing with high-performance fibers.
Since synthetic fibers have been the focus of so much negative attention over the past few years due to their ecological downsides, it is perhaps timely to consider the substantial contribution that has been made to modern life by three synthetic fibers in particular – para-aramids, ultra-high molecular weight polyethylenes (UHMPWs), and not least carbon fibers.
Aramids
Both para-aramids and UHMPWs are many times stronger than steel and were developed over 50 years ago, yet they remain crucial to industries such as many areas of ballistics protection, cut-resistant protective materials and ropes and cordage.
Para-aramids were invented at DuPont’s research labs in the early 1960s by Stephanie Kwolek, who synthesized an aromatic polymer – spun with a solvent rather than melt spun – to produce a durable and exceptionally strong fiber.
DuPont continues to lead in the para-aramids field, along with Teijin’s Twaron.
UHMWPE
Like para-aramids, ultra-high-molecular-weight polyethylene (UHMWPE) is dissolved in a solvent and then spun through spinnerets in proprietary processes developed by DSM (for Dyneema) and Honeywell (for Spectra). Successively, the spun solution is solidified by cooling, which fixes a molecular structure which contains a very low entanglement density of molecular chain.
This structure gives an extremely high draw ratio and results in the fiber’s high strength. The solidified fiber has a gel-like appearance and contains an almost 100% crystalline structure with perfectly arranged molecules, which promotes its strength, modulus, and other properties.
Polyethylene – with a carbon-to-carbon molecular structure like that of a diamond – creates a continuous filament that can be pound-for-pound 10 times stronger than steel, yet light enough to float. In the mid-1980s, AlliedSignal (purchased by Honeywell for $15 billion in 1999) introduced Spectra and DSM introduced Dyneema as the first commercially available extended chain, high-modulus polyethylene fibers, but the two companies eventually clashed over these head-to-head competing products.
In May 1999 Honeywell and DSM agreed to settle a long-running patent claim disagreement that had restricted both from freely selling Dyneema and Spectra and since then, both have been the leading UHMWPE brands throughout the world.
Carbon
Carbon fiber, meanwhile, has proved crucial in composites for the aerospace, automotive, wind energy and sporting goods sectors, to name just four major applications.
Its origins can be traced as far back as the 1860s, when Thomas Edison baked cotton threads or bamboo slivers at high temperatures, carbonizing them into an all-carbon fiber filament used in one of the first incandescent light bulbs to be heated by electricity.
It was not until the beginning of the 1960s, however, that carbon’s usefulness began to be fully exploited, using polyacrylonitrile (PAN), and also rayon, as the precursors.
Carbon fiber composites are now increasingly being employed in the aerospace sector, having grown from representing 10% of the weight of an aircraft body 20 years ago to more than 50% in the latest models, such as the Airbus A350 and Boeing 787 Dreamliner. For similar high strength and lightweighting properties, carbon composites are now employed in many automotive components.
Georg Sahm
During the VDMA’s December webinar, Manasieva Cavus said that effective winding is an essential component in the high-speed production of such expensive high strength fibers, with each specific fiber requiring special attention and having certain weaknesses.
“Aramid is not strong against UV for example, and UHMPWs don’t like water,” she said.
To compensate, Sahm has developed the YarnStar 3+ system for high-speed unwinding, coating, cooling, and winding to add functionality to the fibers, such as hydrophilic/phobic, antibacterial or flame retardant properties, color flexibility and softness/hardness.
The company has also been long established in the processing of carbon fibers for the composites industry, with solutions for PAN precursor yarns, carbon fibers, prepregs and towpregs.
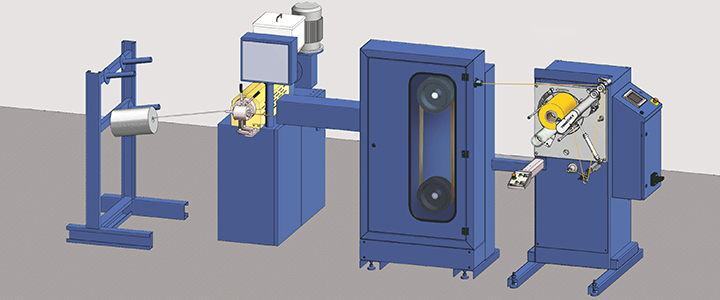
Herzog
Sahm frequently partners with Oldenberg-based Herzog, which is a global leader in the braiding technologies that are employed widely in the creation of “near net shape” carbon preforms – 3D textile structures as close to the shape of the final finished component as possible – with key customers in the automotive industry including BMW, Mercedes, and Porsche. Suppliers to Airbus and Boeing are likewise partners for aerospace components.
Herzog managing director Janpeter Horn said that while braiding looks complicated, it is really quite simple, involving the building up of three, four or more yarns in oblique directions to their edges. It can be likened to a Maypole system.
“It’s a two-step process exploiting centrifugal forces to create structures with unique characteristics, which can have high flexibility and high torsion stability under load,” Horn said. “The fibers are secured by interlocking with equal load division throughout the length of product in both biaxial and triaxial configurations. There are so many markets for these braided products that we have delivered more than 550 types of customized machine to over 60 companies.”
In addition to composite preforms, he added, two other key growth areas for braided textiles are ropes and medical products.
Weight savings
“The ability to replace steel with high-strength fibers has resulted in ropes that have 75% less weight with all of the advantages that brings in terms of towing, mooring, anchoring, and lifting and lowering,” said Dennis Behnken, Herzog’s head of sales. “In addition, ropes made from these fibers have ten times the working life of steel equivalents.”
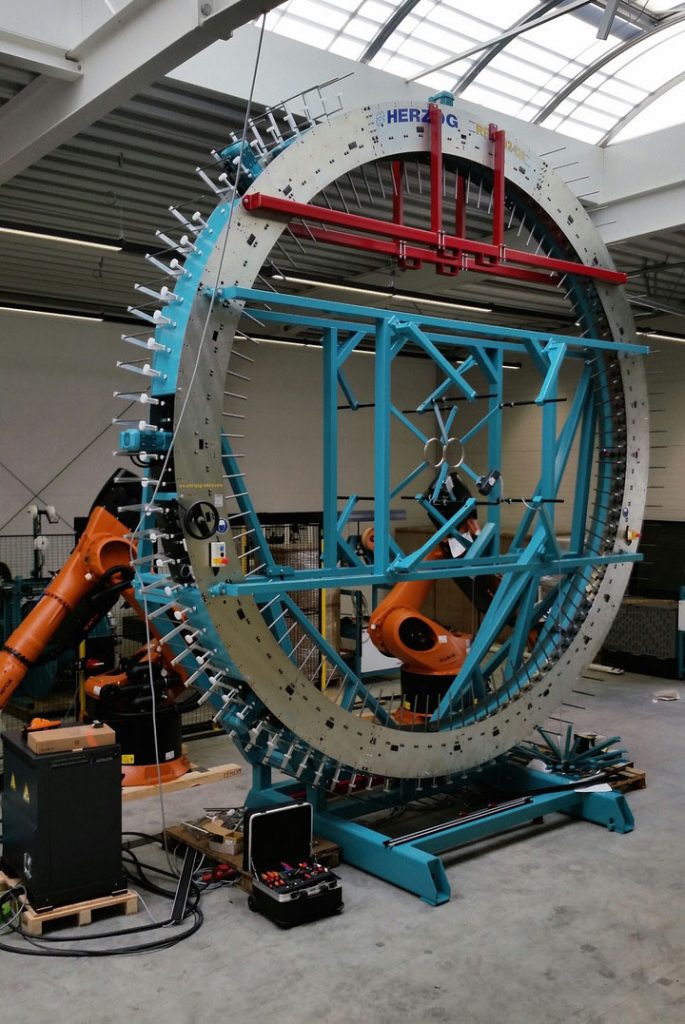
To further enhance high-strength fiber braided ropes, Herzog has developed a temperature-controlled heatsetting unit, which can be integrated directly into its braiding lines to further enhance the physical properties of the rope structures.
In medical products such as sutures, artificial ligaments and stents, braided fabrics are increasingly the preferred choice for their flexibility, in terms of the customized shapes and patterns that can be achieved and the specialized fibers that can be accommodated.
“The body is in many ways like a car,” said Horn. “You can replace or repair more or less every part and there are lots of applications where textile materials have advantages.”
Like Sahm, Herzog has been challenged during 2020 to rapidly develop new digital solutions based on remote installations, as well as virtual trips by customers to its Oldenberg HQ.
Karl Mayer
As the leading manufacturer of warp and knitting machines, Karl Mayer’s Technical Textiles business unit continues to expand its portfolio.
The company’s weft insertion machines exploit a three-yarn system in which weft and warp yarns are held together by a knitting yarn, with all of them laid straight, without crimp.
Typical applications for the fabrics produced on these machines include cut-protection fabrics, coated substrates for advertising, glass fiber fabrics and plaster grids for the construction industry, as well as roofing substrates and geotextiles.
NCF (non-crimp fiber) systems are biaxial or multiaxial machines in which the orientation within the yarn layers is optimized for maximum reinforcement in fabrics for composites based on glass and carbon.

Spreading
The company’s fiber spreading units were introduced a few years ago in response to the carbon fiber industry’s development of high tow carbon fibers consisting of up to 50,000 filaments in a fiber bundle.
“Carbon fiber is very expensive and these fibers are much cheaper, but compared to traditional 6k and 12k fibers they have some disadvantages,” said Karl Mayer sales director Hagen Lotzmann. “They are heavier, and it is more difficult to impregnate them with resins. Our spreading units turn them into unidirectional tapes, which makes them easier to impregnate, but also significantly lowers their aerial weight for the final application. The carbon tapes are then further processed on our multiaxial machines.”
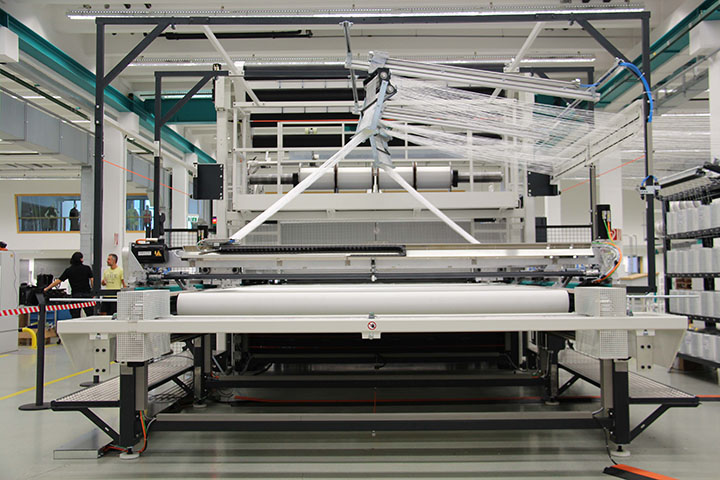
In the latest development of this spreading technology, at ITMA 2019 in Barcelona Karl Mayer introduced a spreading machine with an integrated impregnation unit to produce continuous fiber reinforced thermoplastic tapes.
“Unlike our other machines, which are producing fabrics which then have to be further coated or cut and shaped, this machine produces a semi-finished product,” Lotzmann said. “Such composite parts based on tapes are now employed in a wide number of industries including aerospace, automotive, industrial pipes, marine and sporting goods. We have sold the most machines for composites to the wind power sector, but increasingly we are involved in the development of customized solutions with customers who are looking for diversification, and to enter into niche, higher-margin markets.”