Advances in Textile Recycling – Both Mechanical and Chemical – Define Circular Systems of the Future
A detailed study of the available recycling options for textiles – either mechanical, thermal or biochemical – and their varying levels of industrial readiness, was prepared for the European Commission by the Belgian research institute Centexbel back in 2020.
It came ahead of the Commission’s Strategy for Textiles, which is calling for all textile products on the EU market to be durable, repairable or recyclable – and largely made of recycled fibers – by 2030.
Beginning in January 2025, the problem of garment waste will be proportionately thrown back at the brands putting their products on the EU market.
No longer allowed to be either landfilled or incinerated, over seven million tons of waste textiles will have to be separately collected each year within the EU and will be paid for by the brands via the introduction of a new Extended Producer Responsibility (EPR) scheme.
Technology Combination
The Centexbel study stresses that while businesses pursue the ‘Holy Grail’ of closed-loop recycling, established open-loop systems already successfully re-process textile waste into usable products and a combination of reuse and closed and open-loop solutions will be required to comply with the new strategy.
Many nonwovens are already based on long-established open-loop mechanical recycling processes, currently largely from industrial waste by-products, but with the potential to be made from post-consumer waste too.
For the automotive industry for example, recycled fibers are employed to make insulating webs for sound and heat insulation, hard-pressed parts for floors, doors and seat linings, luggage compartment and boot linings and some filter media.
In the furniture industry, recycled fiber applications include mattress covers and webs, seating padding, wallcoverings and wiping cloths, in addition to carpet backing and underlay.
There are also extensive applications in building and construction for recycled fibers, in a range of insulation products and as filling materials.
Many of these products are often considered ‘second life’ materials and their manufacture has been somewhat demeaned by being termed ‘downgrading’, by champions of a fully circular economy.
In reality, effectively doubling the life of any product that can’t enter a fully circular system will be extremely useful in attempting to meet the near-term goals of the EU’s Textiles Strategy.
Gold Standard
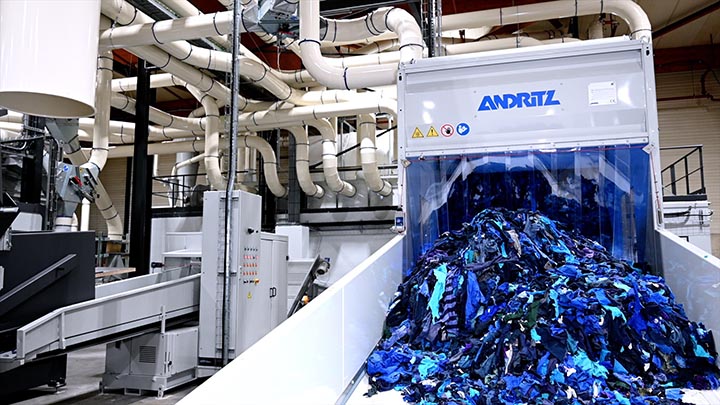
Things have now moved on considerably since Centexbel’s 2020 report and the Gold Standard for mechanical recycling is without doubt Nouvelles Fibres Textiles, based in Amplepuis, France, which has been established in partnership with machine builder Andritz Laroche and sensors specialist Pellenc and was inaugurated in November 2023.
Sorting has been identified as a major bottleneck in the recycling industry, and during a web talk organized by the textile machinery branch of Germany’s VDMA on March 26th this year, Charles Junker, head of sales at Andritz Laroche, observed that the challenge is to be able to automatically classify garments in order to maximize the value of the fibers they contain.
The Nouvelles Fibres Textiles system employs a sequence of processes to consistently refine the textile waste, starting with a sorting line for full garments, a second for cutting and secondary sorting, and then on to a cleaning and tearing line.
Even with the latest fiber-to-fiber chemical recycling methods being commercialized, only 30-40% content can be incorporated into yarns for conventional spinning, and we are already achieving 100% in many high-value nonwoven products.
Mixed Waste
Junker provided an example of how the system handles a bale of cotton and cotton polyester denim waste clothing.
In the first step – after garment spreading to avoid overlapping – the system can be set to separate all cotton items that are more than 90% blue in color from the rest, removing all non-cotton and other colored items and producing a second bale.
This is then cut into clips and fed through the second line to remove everything remaining that is not cotton or blue, such as pocket linings, and then baled again.
The cleaning and tearing line then removes all other remaining impurities such as buttons and zipers, to result in a bale of 98-99% pure fiber.
Junker said the Nouvelles line will soon be at the stage of handling three tons of material an hour, and by the end of this year is targeting six tons an hour.
“Mechanical recycling is an immediate response but won’t be the only solution,” he said, adding that Andritz is now working with Rieter on the development of a refined system for the production of recycled yarns and also on chemical recycling treatments.
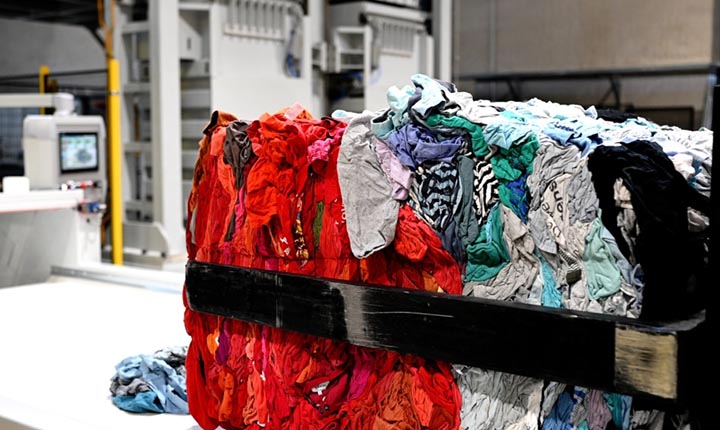
“Nonwovens companies are early movers in looking at the potential of post-consumer waste, realizing that there’s going to be a big demand for the relatively pure waste from mill operations,” Junker said. “The nonwovens industry should be proud of the applications for recycled fibers it has already developed. Even with the latest fiber-to-fiber chemical recycling methods being commercialized, only 30-40% content can be incorporated into yarns for conventional spinning and we are already achieving 100% in many high-value nonwoven products.”
Monomers
Chemical recycling routes meanwhile promise to achieve the conversion of synthetic fibers back to their component polymers or monomers at an unprecedented scale and a frontrunner here, has been Eastman Chemical, headquartered in Kingsport, Tennessee.
In March this year Eastman announced that it had already achieved on-spec initial production at its new molecular recycling facility in Kingsport and is now generating revenue from the operation.
The company, which has also just signed a deal with leading outdoor brand Patagonia, expects to ramp up production of the new facility over the coming months and to achieve approximately $75 million in earnings from it this year. Once fully operational, it will have an annual capacity of 110,000 tons.
A second plant in Port-Jérôme-sur-Seine in Normandy, France, is planned for start-up in 2026 and will also have an initial capacity of 110,000 tons in its first phase, rising to 200,000 tons in the second phase of development. The company plans to have a third plant at a location yet to be decided in the USA also operational by 2026, which will bring its total polyester recycling capacity to 330,000 tons by that time.
Methanolysis
Via a chemical process it calls methanolysis, Eastman’s polyester renewal technology enables waste to be broken down into its molecular building blocks and then reassembled to become virgin-quality material without compromising performance. Eastman is enabling the potentially infinite use of materials by keeping these molecules in production, in a material-to-material high-yield loop. The waste plastic can be converted into virgin quality food contact polyesters with lower greenhouse gas emissions than traditional methods.
“By demonstrating molecular recycling at this scale, we have solidified our position as a leader in the creation of a circular economy,” said Eastman CEO Mark Costa. “Demand for recycled materials at virgin-quality levels from our new plant is strong and we are excited to announce this significant milestone in our journey.”
SK Group
Paris-headquartered water solutions leader Suez his also partnering with SK Geo Centric (SKGC), a subsidiary of the South Korean chemicals giant SK Group, to establish a €450 million PET plastic and fiber recycling plant in Saint-Avold, France, based on the technology of Loop Industries.
With commissioning planned for 2025, the new recycling facility will manufacture 100% recycled and infinitely recyclable virgin-quality PET resins with a planned capacity of 70,000 tons per year.
Loop Industries, headquartered in Montreal, Canada, owns patented and proprietary technology that can depolymerize PET plastic and polyester fiber waste currently of little or no value, including plastic bottles and packaging, carpets and textiles of any color, transparency or condition, and even ocean plastics that have been degraded by the sun and salt. The resulting monomers are filtered, purified and polymerized to create virgin-quality Infinite Loop-branded PET resin suitable for use in both food-grade packaging and fibers. The monomers can be recycled infinitely without degradation of quality, the company claims.
The French project will follow on from the first Infinite Loop manufacturing facility which is being built in Ulsan, South Korea, and will also have an annual capacity of 70,000 tons.
In January 2024, UK-headquartered investment firm Reed Management announced it will provide financing of $66 million to Loop Industries, with the aim of further rapidly accelerating the production of 100% recycled polyester fibers and PET plastics in Europe.
Scaling up
The Eastman and Suez/SK projects alone will establish the chemical recycling of an annual 400,000 tons of polyester and as such serve to illustrate the key advantage of chemical fiber recycling routes in scaling up, especially for synthetic fibers.
It would take many, many mechanical recycling operations to equal the capacities that these projects will bring to market. At the same time, there is not the same level of sorting required, since in many chemical recycling methods proposed, the materials are being taken back to their original constituent monomers.
Mechanical recycling, on the other hand, is well proven and demonstrably cost-effective for new players who may be considering entering what will be a rapidly expanding market in the next few years.
Centexbel’s White Paper on Textile Fiber Recycling Technologies can be downloaded at www.centexbel.be