The year 2018 can be considered an annus horribilis for plastics, including synthetic polymer and fiber-based products that rely on such materials.
The issue of microplastics in the oceans generated a mountain of negative publicity and calls for far-ranging action against the industry and, at the same time, the publicity surrounding so-called ‘fatbergs’ created, in part, by flushed single-use plastic products continued. Even the humble teabag was the subject of successful consumer campaigns to see the elimination of plastics from it.
Commitment
These issues have led to, among other things, the New Plastics Economy Global Commitment, which in October 2018 saw more than 290 of the world’s leading packaging brands committing to ensure that 100 percent of their plastic packaging can be reused, recycled or composted by 2025.
A more recent signatory to the commitment, in June this year, is Berry Global, which is both the largest nonwovens producer in the world and at the same time purchases around seven billion pounds of plastic resin annually.
“At Berry, we stand behind the power of plastics and are placing a priority on creating a more sustainable future,” said Tom Salmon, Berry Chairman and CEO. “We are innovating our products to encourage recyclability, the use of recycled content, and light weighting. In conjunction with the Ellen MacArthur Foundation, we are proud to accelerate the transition towards a circular economy.”
Separately, Berry’s executive vice-president for product management and innovation, David Parks, has called for the industry to be braver in standing up for the good that plastic-based products do for the world.
“In the plastics industry, it’s no exaggeration to say our products save lives, protect food supplies, reduce infection risks at hospitals, and enhance quality of life,” he said. “The dialogue of ‘plastics equals bad’ is simplistic and erroneous. We have a lot to be proud of in this industry and together we can communicate the benefits and possibilities of plastics.”
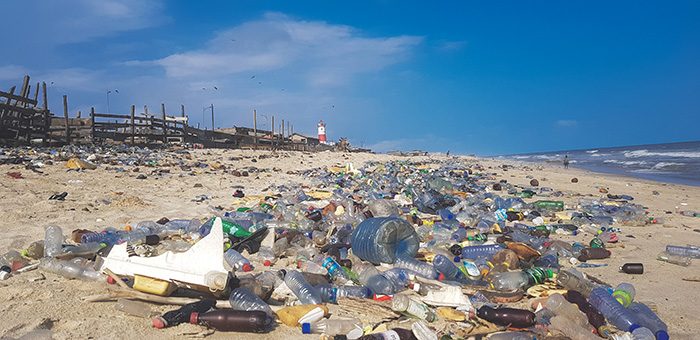
AEPW
The start of 2019 also saw the foundation of the Alliance to End Plastic Waste (AEPW0), which has grown to include 39 major companies who are committing a combined $1.5 billion over the next five years to initiatives aimed at eliminating plastic waste in the environment. In addition to Berry, they include BASF, Braskem, Clariant, Covestro, Dow, DSM, ExxonMobil, Formosa Plastics, Henkel, LyondellBasell, Mitsubishi, Procter & Gamble, Reliance Industries, SABIC, Sumitomo and Total.
AEPW initiatives include the City Partnerships project for developing end-to-end waste management systems which is underway in India, Indonesia, the Philippines and Vietnam, and the Global Information Project, which is developing an open source, science-based database that will provide users with reliable and actionable plastic leakage information.
It is also providing funding to support the New York-based Incubator Network to develop and promote technologies, business models, and entrepreneurs aimed at preventing ocean plastic waste and improving waste management and recycling. The intent is to create a pipeline of projects for investment, with an initial focus on South and Southeast Asia.
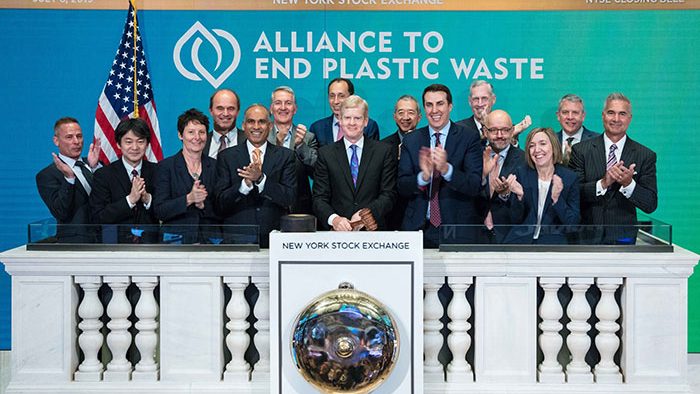
Economic resource
Speaking for the AEPW at the 5th Annual Sustainability and Circular Economy Summit held in Washington on August 15th, Haley Lowry, global sustainability and end-user marketing director at Dow, said that viewing plastic as waste is unacceptable.
“We need to view it as an economic resource,” she said. “In a circular economy, we all need to think about how we can use this valuable resource over and over again. There is ample opportunity for innovation to address plastic waste, starting with designing products that have greater ability to be recycled and reused, as well as developing new recycling technologies and infrastructure.”
Status quo
The AEPW, however, has not been without its critics from the start, including inevitably Greenpeace.
“This is a desperate attempt from corporate polluters to maintain the status quo on plastics,” said Graham Forbes, its global plastics project leader. “In 2018 people all over the world spoke up and rejected the single-use plastics that companies like Procter & Gamble churn out on a daily basis, urging the industry to invest in refill and reuse systems and innovation. Instead of answering that call, P&G preferred to double down on a failed approach with fossil fuel giants Exxon, Dow and Total, which fuel destructive climate change. Make no mistake, plastics are a lifeline for the dying fossil fuel industry, and this goes to show how far companies will go to preserve it.”
Speaking for the AEPW at the 5th Annual Sustainability and Circular Economy Summit held in Washington on August 15th, Haley Lowry, global sustainability and end-user marketing director at Dow, said that viewing plastic as waste is unacceptable.
Loop
There can be little doubt, however, that solutions are being sought with a new urgency and there are already some very promising new technologies at a commercial stage, such as that of Canadian start-up Loop Industries.
Loop’s process allows plastics of no or little value – PET plastic bottles, packaging and textiles of any color, transparency or condition, and even plastics retrieved from the oceans that have been degraded by sun and salt – to be diverted, recovered and recycled endlessly into new, virgin-quality PET that even meets FDA requirements for use in food-grade products.
As such, it has attracted $35 million in venture backing and the attention of major corporations including Coca Cola, Danone, Evian, L’Oreal, and Pepsico. It is also currently building a new plant in the USA with Indorama Ventures (IVL) – one of the biggest, and certainly the most diversified, manufacturers of synthetic fibers and fiber feedstocks in the world.
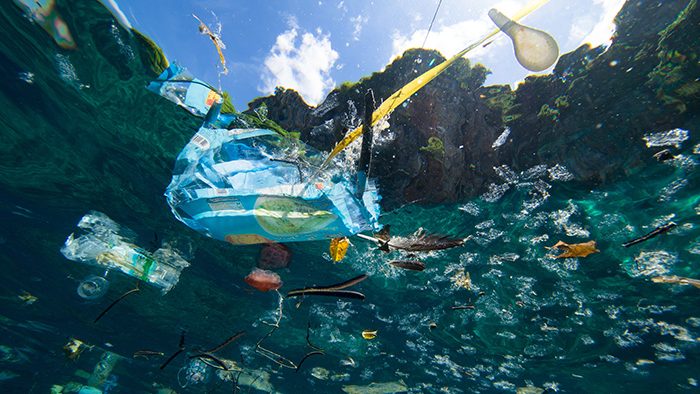
Ioniqa
IVL also has a partnership with Ioniqa, which is building its first 10-000-ton PET plastic upcycling factory in Geleen, The Netherlands. It will shortly start converting PET waste into high-grade, pure PET raw material, initially for food packaging, having a further partnership with Unilever.
A clean-tech spinoff from the Eindhoven University of Technology, Ioniqa’s cost-effective process exploits smart fluids and a unique separation process to recover virgin with which new high-end PET can be manufactured via polymerization.
Bio-PP
Bioplastics, which don’t have petrochemical origins and degrade over time, could also provide a partial solution to the plastics problem, although they are also not entirely without an environmental price; to grow the necessary plants or bacteria as raw materials requires fertile soil and fresh water, which many countries don’t have in abundance.
In an important new development, LyondellBasell, one of the world’s largest plastics, chemicals and refining companies, and Helsinki-headquartered Neste, the biggest producer of renewable diesel from waste and residues, recently announced the first parallel production of bio-based polypropylene (PP) and bio-based low-density polyethylene (PE) at a commercial scale.
The joint project used Neste’s renewable hydrocarbons derived from sustainable bio-based raw materials, such as waste and residue oils. The project successfully produced several thousand tons of bio-based plastics, which are approved for the production of food packaging and are being marketed under the brands Circulen and Circulen Plus.
LyondellBasell’s cracker flexibility allowed it to introduce a new renewable feedstock at its site in Wesseling, Germany, which was converted directly into bio-based PP and PE. An independent third-party tested the polymer products using carbon tracers and confirmed they contained over 30 percent renewable content.
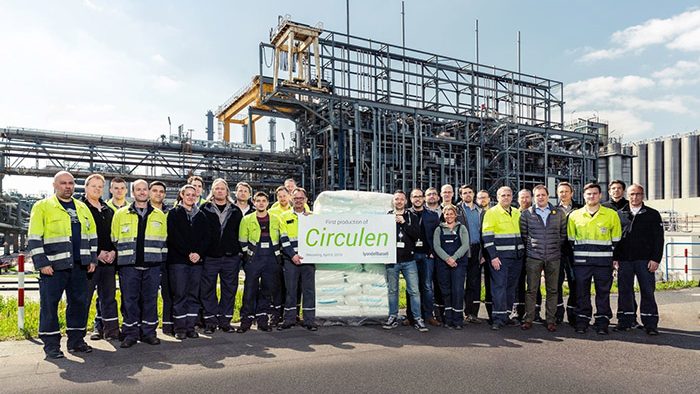
Production
European Bioplastics predicted global bioplastics production capacity is set to increase from around 2.1 million tons in 2018 to 2.6 million tons in 2023, with PLAs (polylactic acids) and PHAs driving the growth.
PHAs have been in development for a while and are now entering the market at a larger commercial scale, with production capacities set to quadruple in the next five years. These polyesters are bio-based and biodegradable and feature a wide array of physical and mechanical properties.
Production capacities of PLA are meanwhile set to double by 2023. PLA is an extremely versatile material that features excellent barrier properties. High-performance PLA grades are an ideal replacement for several conventional fossil-based plastics, such as polystyrene and polypropylene.
In the largest single capacity expansion for bioplastics, Total Corbion PLA, a 50/50 joint venture between Total and Corbion, has now started up its 75,000 tons-per-annum PLA bioplastics plant in Rayong, Thailand.
Barriers
Bio-based, non-biodegradable plastics, including drop-in solutions for PET and PA (polyamide) which have only partial bio content, currently make up around 50 percent or one million tons of the global bioplastics production capacity.
Although bio-based feedstocks seem like they have potential to reduce emissions and reduce recycling requirements, their total market share is dwarfed by traditional petrochemical plastics and the barriers to their widespread adoption are considerable, according to a new report Biobased Polymers 2018-2023: A Technology and Market Perspective, from IDTechEx.
Firstly, the transition from laboratory to industrial scale production is far from straightforward. A conservative approach to production methods and the complexity of high-volume fermentation do not marry well. In addition, there is a dearth of capital investment to help academic innovators and early stage start-ups expand production, both from VCs and from governments. This absence of funding is compounded by the fact that many bio-based products are more expensive to manufacture, certainly in the short term, and possibly into the long term as well, until economies of scale start to bring down the cost of production. Finally, public awareness and willingness to pay more for a ‘greener’ product hampers demand.
“Recognition of the downsides of plastics has entered public consciousness, but when faced between a choice of a cheaper petrochemical plastic and a bio-based competitor with a hefty green premium, too often consumers are opting for the lower cost product,” IDTechEx concluded in its report.