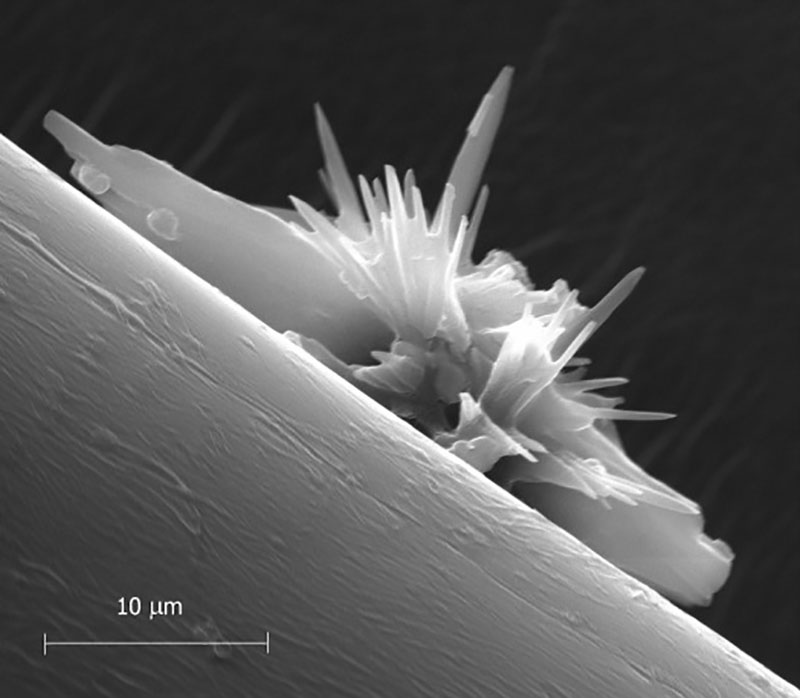
As a common class of material, polypropylene (PP) is widely acknowledged for its excellent resistance to harsh chemical environments, though it is sensitive to oxidizing agents. With biofouling remaining an inevitable phenomenon, people depend on local authorities to keep thoroughfares safe. Concrete steps and ramps at the ocean can be particularly hazardous when covered in algae. Durability is also a serious issue along with health and safety aspects and economic costs. The repair or replacement of deteriorated materials is both labor and capital intensive. At a study site in the northwest of England the local authority has been using dairy hypochlorite (DH) to manage biofouling, mainly algae, on its public sidewalks and promenades. The author has monitored the use of sodium hypochlorite (NaClO) for ten years on the Fylde coast and details here the effects of this aggressive chemical upon the innovative use of PP fibers within a marine concrete matrix, showing untreated smooth micro fibers, without fractures and free from defects.
The global market for NaClO is nearly two billion metric tons, growing at about 2% annually. North America alone consumes more than 6.8 million metric tons of NaClO (bleach). About two thirds of it is used in the form of detergent, the remainder goes into disinfectant applications. It comes into contact with polymer fiber concrete not only as an anti-fouling strategy at sea defenses, but also in swimming pool construction (U.K. and Japan), water treatment plants across the globe, residential development (U.S.) and fiber reinforced concrete storage tanks and pipelines. The handling of NaClO requires clear understating and knowledge of safety handling and storage precautions. The U.K. authority uses DH to control biofouling (microorganisms) on concrete steps, public ramps and walkways on an industrial scale. DH is a chlorine-based disinfectant used primarily for routine disinfection of milking parlors, conduits, dairy utensils and general cleaned surfaces. Hypochlorite is the salt of hypochlorous acid, it is corrosive and hazardous for the environment; it causes severe burns, eye damage and is very toxic to marine life. DH is 10-20% NaClO (chlorine bleach or bleaching agent) when fresh, with a 1% stabilizer of Sodium Hydroxide (NaOH) (aka caustic soda). When used, environmental precautions are mandatory due to the fact this product is extremely hazardous.
There is insufficient research on the short and long term effects of NaClO on synthetic fibers within marine concrete, and no published guidance available. Although widely used as a cleaning agent, NaClO has been long suspected by the water and wastewater industry to cause harm to polymer filtration membranes and various marine equipment manufacturers. The overall aim of this introductory study was to examine the changes occurring in synthetic fiber properties due to NaClO exposure.
Research into polymer fiber scaffolds for tissue engineering applications used NaClO to purposely alter the morphology of fibers. Higher porosity showed by NaClO treated fibers indicated that polyvinal alcohol (PVA) and NaClO acted synergistically as porogens (1). Other work showed how NaClO caused the oxidation of the hydroxyl groups of PVA, thus facilitating the biodegradation of the polymer (2). Within textile manufacture, it is understood NaClO penetrates into fabric and damages cellulosic fibers, and well accepted that it is harmful to synthetic fibers (3).
Methodology
Samples of PP micro fibers, circular in section, and 18 microns in diameter were treated with a modest 2.5% NaClO solution. The macroscopic changes were observed by scanning electron microscopy (SEM) and energy dispersive x-ray analysis (EDX) to visualize qualitatively the surface and profile changes, elements along with deteriorations. Characterization by attenuated total reflectance fourier transform infrared spectroscopy (ATR-FTIR) was undertaken to identify the chemical functional groups affected.
Industrial conditions
The PP fibers are submitted to NaClO solution as part of a cleaning procedure to combat biofouling on concrete steps. The fibers are used as reinforcement and crack control within marine concrete, forming sea defenses in the U.K. Many fibers protrude from the surface of the concrete, exposed to power washing, NaClO and tidal impact.
Solutions
Two solutions were used throughout the experimental tests. A NaClO solution (2.5%) was prepared by diluting concentrated NaClO (Wako Pure Chemical Industries, Ltd). A solution of NaCl 3.5% was used as artificial seawater. Fibers were treated 10 times to mimic a 6-month maintenance regime. A treatment consisted of a fiber being covered with 50 ml of NaClO and left outdoors in a petri dish in direct sunlight for 2 hours. After drying, the fibers were immersed in 50 ml of artificial seawater and left in direct sunlight for a further 2 hours. Finally the samples were washed in distilled water 4 times to reveal the original surface. This sequence replicates the concrete surface fiber conditions at the study site, being bleached, and then submerged by the ocean.
Results and Discussion
At the time of manufacture (2005), the study site was the first to utilize synthetic fibers in a marine concrete. Due to the nature of construction of the revetment armor, many synthetic fibers are exposed at the surface of the concrete. The images reported here confirmed the formation of crystals and are representative images of attachment and growth upon synthetic fibers examined from the study site. Symmetrical crystal attachment and growth, developed on micro fibers, considerably altering the fibers profile. The potential influence of crystals, reported here for the first time, on synthetic fibers used at the site could have a serious effect on the durability of this type of marine concrete. This type of concrete is being promoted beyond the U.K., into Europe, Japan and across the U.S. Crystal attachment and growth to one side of a microfiber gives it an irregular shape, and increasing the diameter of the fiber by 50%.
When a chemical reaction takes place, there is a change in the chemical structure of a polymer often causing a change in molecular weight and a loss in physical properties. Chemical analysis by ATR-FTIR demonstrated that treated PP fibers underwent structural alterations. Analysis of ATR-FTIR spectra of the untreated and treated fibers revealed the appearance of new bands in the spectra near 1711 cm-1 and 1740 cm-1 of the treated fibers, which is attributable to C=O groups. This indicates the possible creation of aliphatic ketone and/or carboxylic acid moieties after treatment. As a result, the structural and chemical properties of the PP fiber were modified when exposed to an asthenic NaClO solution.
The exposure of polymers to crystal attachment and growth may lead to diminishing the bond between materials. Their existence at the cement interface disrupts or distorts the fiber by growth. SEM analysis into fiber performance and the change in their physicochemical properties has been previously observed (4).
SEM Micrograph, shows an interesting irregular morphology, which consists of a protuberant microstructure of irregular-shaped columnar pores with crystalline walls interconnected to each other. The crystal samples studied were varied in appearance with an average size of about 50 μm in size. EDX analysis indicated that the 28.87% Cl (weight), 9.98% Na were the major elements consistent with NaClO. The occurrence of crystalline structures, particularly attached to fibers creates an expansive, damaging force. This crystallization pressure produces tensile stresses causing disruptive expansion (5). The effects of this shrinking and swelling during drying periods and moisture intake, will accelerate the mechanical deterioration process of the fiber bond and cement. Expansion and micro cracking will also affect the bond between fiber and cement, being a paramount consideration in the design stage.
It was observed that the fiber surface deformed, fractured and developed deep elongated grooves. The growth of crystals damages the fibers and after washing of the polymer fiber, degradation clearly appeared. Therefore it becomes more susceptible to water/microbial transport, tidal impact and power washing. Due to the non-polar nature of the PP fibers, and their lower surface free energy, compared to cement paste, a gap is generated between the fiber and the cement matrix (6). In this void, moisture could permeate around the fibers, thereafter, following submersion; drying will facilitate disruptive crystals growing at the fiber/cement Interface Transition Zone. As more and more fibers are exposed to hydrodynamic forces (whether tidal impact or power washing) and microbial forces, eventual liberation of fibers takes place, leaving many voids within the concrete. This in turn creates a more porous and algae-susceptible surface and a lack of water tightness. In this situation, the fibers having left the matrix do not increase toughness of the concrete armor as intended, leading to an increase in permeability and paving the way for further deleterious chemical interactions between seawater and cement hydration products.
Conclusions
Macroscopic fluctuations were observed by SEM visualizing qualitatively the surface and profile variations of the samples along with deteriorations. Characterization by FTIR undertaken identified the chemical functional groups affected. As a result, the structural and chemical properties of the PP fiber were modified when exposed to an asthenic NaClO solution.
Examination of current standards revealed that many of the test methods for quantifying the degradation of polymers examine a single degradation mechanism in isolation. By exposing the fibers to NaClO, H2O and seawater, the writer has replicated ‘real life’ study site conditions and highlights the need for amendments to the current U.K. guidance on the use of Synthetic-fiber-reinforced concrete. The potential influence of NaClO crystals on the durability of PP fiber reinforced concrete, now widely used across the world, clearly warrants further investigation.
Based on the findings of this research, regular use of DH on the concrete revetment armor steps should be avoided and further experimental research undertaken to examine the wider use of this material and how NaClO affects it. Lessons could be learned from other [U.K.] authorities that purposely do not use such harmful chemicals. The neighboring Wyre Council does not use DH combined with power washing, but uses a periodic application of an environmentally- friendly-sprayed biocide treatment on revetment steps- Training should also be considered for the operatives of cleaning machines, bearing in mind alternative procedures, which take into account the material and environmental consequences of current practices.
Acknowledgement
The author wishes to convey gratitude to Professor Shin-Ichiro Suye, University of Fukui, Department of Frontier Fiber Technology and Science in Japan and to Professor Satoshi Fujita and students Onon Batnyam and Arata Kato for their assistance.
References
1. G. Meneghello, B. Ainsworth, P. De Bank, M.J. Ellis, J. Chaudhuri. Effect of Polyvinyl alcohol and sodium hypochlorite on porosity and mechanical properties of PLGA hollow fibre membrane scaffolds. European Cells and Materials. Vol 16. Suppl. 3, p 82, 2008.
2. R. Jayasekara, I. Harding, I. Bowater, G. Lornergen. Biodegradability of selected range of polymers and polymer blends and standard methods for assessment of biodegradation. Journal of Polymers and the Environment .13. (3), pp 231-51, 2005.
3. S. R. Karmaker. Chemical Technology in the pre-treatment process of textiles. Textile Science and Technology. 12. Elsevier Science (Netherlands). p168, 1999.
4. T. Artham, M. Sudhaker, R. Venkatesan, N. C. Madhaven, C. K. Murty, M. Doble. Biofouling and stability of synthetic polymers in sea water. International Biodeterioration and Biodegradation. 63, 884-890, 2009.
5. D. Bonen, S. Sarkar. Replacement of Portlandite by gypsum in the interface zone and cracking related to crystallization pressure. Ceramics Transactions. 37, pp49-59, 1993.
6. J. Faran. Introduction: The Transition Zone – Discovery and Development. RILEM Technical Report. London. E&FN Spon. 1996.