The nonwovens industry supplies a diverse range of products to multiple markets. Many of these products, especially those that target consumers, such as hygiene products and wipes, are largely designed for single-use application. In terms of the lifecycle of these products, the end of life choices for most nonwovens are largely three-fold: landfill, incineration, or waste in the environment, which can negatively impact both terrestrial and marine habitats. For packaging, which is a major application for plastics, approximately one-third of plastics are leaked into the environment, while 40% goes into landfills. Only 10% of plastics are recycled, with just 2% undergoing closed-loop recycling. Arguably,i it is the appearance of waste in natural environments—so-called leakage—that is causing us to rethink the materials that we use and how we dispose of them.
The COVID impact
The disruption to the global economy caused by the coronavirus (COVID-19) pandemic has been overwhelming. It may also have had an effect on environmental policy by pressing the pause button on the problem of waste plastic. This is partly the result of governments and regional administrations who have pushed back deadlines for implementing bans on certain plastics. Prior to COVID-19, we witnessed a concerted effort by brand owners along with governments, coupled by strong consumer demand, to transition to more environmentally friendly materials. We also saw the ban of single-use plastics, most notably, plastic bags and foodservice items such as straws and utensils. The world was changing and changing rapidly.
Today, many of these initiatives have been relaxed. As a result of the pandemic, we have witnessed a surge in on-line shopping, which typically comes delivered in an over-engineered packaging format, creating new streams of packaging waste. Disposable plastic bags at supermarkets have returned because reusable bags are now considered to pose a health risk. According to the International Solid Waste Association, since the start of the COVID-19 crisis, single-use plastic use is up nearly 300%.ii Interestingly, along with the increase in plastic use, we are seeing considerable effort to promote the idea of plastics recycling as a means of mitigating waste. For example, a recent article in the Harvard Business Review points out that recovering waste plastic could represent a trillion dollar opportunity.iii
The most notable product and perhaps the poster child of consumer waste is the disposable facemask. Prior to COVID-19, facemasks were largely worn by healthcare providers. Today, many regions, cities, and countries require the use of facemasks for anyone in public spaces. These requirements, and steps to mitigate the transmission of COVID-19, have expanded the disposable facemask market by nearly 10-fold, turning a $800 million a year market into a $75 billion a year market. Unfortunately, many of these masks are improperly disposed of and become a source of pollution.
Bio-based plastics
In light of this backdrop, why should anyone be interested in bio-based plastics? Perhaps the interest rests with consumer perception. Europe generally leads the world in environmental initiatives, especially with regards to materials. Currently, the European Union’s Strategy for Plastics in the Circular Economy and its Directive on Single Use Plastics Products propose sweeping restrictions on plastics and could adversely impact a whole range of bio-plastics and manmade fibers.iv But, how do European consumers regard bio-based plastics? A recent study of 281 consumers in Germany showed that consumers look very favorably on products that claim to be bio-based and recyclable and would prefer these over fossil-based products.v Paradoxically, they were less certain about how to dispose of these products, especially if they were identified as being compostable, biodegradable, or biobased. Similarly, 90 percent of Canadians worry about plastic pollution, according to a 2019 Angus Reid poll, but none of their large-city residential programs accept compostable plastics.vi
Another European study showed that participants were unfamiliar with the concept of bio-based. While they associated positive attributes, such as “naturalness” and “environmental friendly” with bio-based products, they also had negative environmental associations, including the distrust of companies marketing bio-based products and the potential for “greenwashing.”vii What is striking is that even in Germany, which is a leader in materials recycling, only 12% of German consumers said they had product experience with bio-plastics.viii
Bio-plastics could be a big hit with consumers, if they get a better understanding of the benefits of bio-plastics. Bio-plastics could also be a big hit with brand owners if these bio-based materials can truly deliver a more environmentally friendly and sustainable materials platform. Remember, brand owners are not only influenced by consumers, they are being directed by their boards and their investors to deliver on specific goals related to the environment, society, and governance. Going green, through the adoption of bio-plastics, plays into a narrative that supports these goals. In this context, one can say that the future of bio-plastics will arguably be decided by three important factors:
- Legislation
- Competition from the incumbents
- Benefits vs cost
Legislation
With regards to legislation, political policies are driving towards more sustainable solutions and a circular economy. The recent provisional agreement for an EU directive on single-use plastics to address marine litter has been a catalyst for other countries to follow suite. According to the World Resources Institute, over 100 countries have placed restrictions on plastics and many are working to phase out single-use fossil-based plastics within the next five years. While some of these initiatives have been postponed or put on hold due to COVID-19, they are unlikely to remain so once the pandemic is under control. Last but not least, beginning 2021, the EU will impose an €800 per ton tax on plastic packaging that is not-recycled.
Competition
In terms of the potential competitive response from incumbents, rest assured that the plastics industry is not standing still. The World Economic Forum projects that plastic production is expected to almost quadruple between 2020 and 2050 (Figure 1). The American Chemistry Council says the U.S. industry plans to spend $47 billion on new plastics-production capacity over the next decade. The industry realizes that unless solutions are found, the problem of plastic waste will only worsen as global demand for plastics increase, and this will only reinforce the negative perception of plastics by consumers and governments alike.
According to the World Economic Forum, by 2050 there will not only be more plastic than fish in the ocean, but the plastics industry will consume 20% of the world’s total oil production and 15% of its annual carbon budget. According to the Center for International Environmental Law, emissions from plastics production and incineration could account for 56 billion tons of carbon emissions between now and 2050, which is almost 50 times the annual emissions of all of the coal power plants in the U.S.ix
In light of these predictions, numerous examples of companies and consortia, like the Circular Plastics Alliance, which comprises over 200 signatories, are emerging to try and find solutions to the problem of plastic waste. In Italy, for example, over half of the plastic packaging collected from sorted bins is sent for mechanical recycling to make new products. The remaining portion of mixed post-consumer plastics, known as plasmix, is not suitable for recycling and mainly ends up in cement plants, where it replaces fossil fuels, with the remainder sent to landfill.
To find alternative uses for plasmix, a consortium headed by Eni and Veralis are converting waste plastic to chemical feedstocks using gasification and pyrolysis technologies (Figure 2). This upgrading process will not abate carbon emission if fossil-based plastic are ultimately used as fuel. However, if the plastics can be converted to chemical feedstocks, the opportunity to create a self-sustaining circular pathway for plastics would emerge.
In the United States, the Advanced Recycling Alliance for Plastics, sponsored by the American Chemistry Council (ACC), has a similar consortium-based effort to convert post-consumer plastics into chemicals, fuels and other products. In a recent report, the ACC claims that if advanced plastics recycling and recovery facilities in the U.S. were widely adopted, the processes could result in 40,000 U.S. jobs, as much as $2.2 billion in annual payroll and $9.9 billion in economic output.x
However, the challenges to recycling are quite formidable, including the lack of material standardization and product recyclability, the volatility of customer demand and waste material markets, insufficient sorting quality, and feedstock contamination. Consequently, investments for new infrastructure and conversion processes are limited, especially under the COVID-19 environment.xi
Benefits vs Cost
There are a number of new technologies emerging that have the potential for disrupting the state of bio-based plastics. These so-called second- and third-generation manufacturing platforms are based on low-to-no cost waste materials, such as forest and agricultural residue and carbon dioxide captured from flue gases, to produce chemicals, which can then be processed into bio-based plastics.
One might expect that if a consumer article is labeled as compostable, it implies that the supply chain infrastructure exists for it to be collected and composted. However, bio-plastic waste management is challenged by the absence of consistent waste collection systems, poor communication on how to properly dispose of compostable plastics, and the lack of an established system of guidance or labeling for consumers.
A smorgasbord of plastic options
The result of considerable effort in R&D has created a wealth, and in many cases, a confusing array of material choices. These can be characterized in terms of their chemical origins—fossil-fuels or bio-based—and whether they are bio-degradable or not. Confusion occurs because, for example, a fossil-based plastic, such as PVOH (polyvinyl alcohol), is biodegradable, while a bio-based plastic, such as PEF (polyethylene furanoate), is not biodegradable, while other bio-based plastics can be bio-degradable but not necessarily compostable.
Unlike petroleum-derived plastics, many bioplastics, are biodegradable. Some, like polylactic acid (PLA), which is an aliphatic polyester, are biodegradable at industrial compositing facilities. This means that composting temperatures above 60 C for an extended period must be maintained for the plastic to decompose. Others, like thermoplastic starch, polybutylene succinate (PBS), and the polyhydroxyalkanoates (PHA), are bio-degradable in natural environments. Thermoplastic starch is water soluble, which limits its applications. Whereas, PHB (polyhydroxybutyrate), the simplest PHA, represents the standard for biodegradability of high molecular weight polymers. Commercial grades of PHB have properties that are very similar to those of polypropylene and its high degree of crystallinity makes it fully water resistant.
With regards to linear polyesters, the leading bio-based replacement for PET is PEF. At the manufacturing level, the synthesis route is like that of PET, where terephthalic acid is substituted by FDCA (Furandicarboxylic acid). This results in the production of a high-quality plastic made entirely from plant-based industrial sugars. Avantium is arguably the leader in PEF development. Their so-called YXY approach is based on a multi-step synthetic pathway, which begins with the fermentation of C6 sugars, and other bio-feedstocks, to produce FDCA, which then is polymerized with bio-ethylene glycol.
PHAs are also linear polyesters produced by bacterial fermentation of sugars or lipids. Their most common type is the PHB from sugar cane. Plastics with PHAs are readily biodegradable, even in cold seawater. Whereas PEF is bio-based but not bio-degradable, PHB is both bio-based and biodegradable, and biodegradable in a reasonable timeframe. Although PHAs have been extensively researched, commercialization costs and technical application hurdles have made its application to high-volume markets challenging.
As one lifecycle expert recently commented, compostable plastics are an example of where there is a risk of false sustainability claims.xii One might expect that if a consumer article is labeled as compostable, it implies that the supply chain infrastructure exists for it to be collected and composted. However, bio-plastic waste management is challenged by the absence of consistent waste collection systems, poor communication on how to properly dispose of compostable plastics, and the lack of an established system of guidance or labeling for consumers. Unintentionally, compostable plastics could contaminate conventional plastics recycling. The reality is that most composting facilities are optimized to handle organic waste, and most do not accepting bioplastics.
In spite of this, the confluence of rising regulatory measures to protect the environment, consumer demand for environmentally friendly products, and brand-owner initiatives to meet sustainability goals is generating enormous pressure on value-chain participants. Bio-based plastics are attractive because they can have lower carbon footprint than petroleum-derived plastic, they are generally perceived as being more environmentally-friendly and sustainable, and they address certain end-of-life challenges created by “leakage” because some can readily decompose in the environment. Material suppliers are clearly trying to develop products that have lower environmental impact than current offerings, and manufacturers of both industrial and consumer goods are examining the lifecycle impacts of their material choices. An issue with suppliers, and startups alike, is their inability to scale up conversion to approach large-volume markets and to do it while competing with commodity petroleum-based plastics.
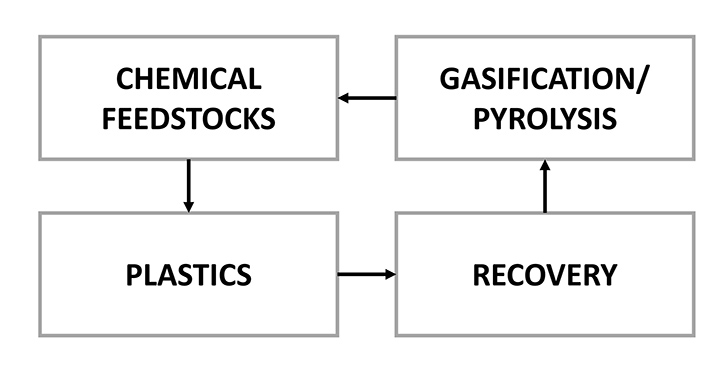
The paper model
Wastepaper recycling could be a role model for plastics. Arguably, one of the major drivers in the history of paper recycling in the United States, and North America broadly, was Chinese investment in linerboard mills in the 1990s, and the beginning of wide-scale importation of U.S. waste paper by the Chinese. As shown in Figure 3, that plus other factors allowed wastepaper recovery to more than double since 1990, from about 29% to 66%. Of the nearly 67 million tons of wastepaper generated annually, 44.2 million is recovered and recycled. Contrast that with plastic, where over 35 million tons of waste is generated and only 3 million is recovered and recycled.
Could 2020 be a tipping point in the history of plastic recycling, akin to paper? Ironically, China may have a role to play in the future of plastic recycling. In 2019, China decided to ban imports of 24 categories of solid waste, including certain types of plastics, citing environmental and health concerns. A recent study estimated that 111 million metric tons of plastic waste will be displaced by China’s new policy by 2030.xiii As the researchers point out, all that waste will have to go somewhere else!
One vision on what to do with all this waste plastic has at its centerpiece the Advance Plastics Recycling facility or APR. Although plastics waste is mostly sourced from industrial rather than municipal solid waste, post-consumer waste recycling is most impactful. Currently, municipal solid waste is sorted at Materials Recovery Facilities (MRF). There are about 300 MRFs throughout the U.S. These process municipal waste and recover recyclables, with any residual material sent to either landfill or incineration. Under current MRF operation, most recovered plastics are downgraded, with the exception being polyester, which has a relatively robust market, particularly as a feedstock for fabrics. Unlike the MRF, the APR would be equipped with technologies that can recover waste plastic of sufficient quality that the bulk of the ARP waste stream could be directed to the production of chemical feedstocks.
As mentioned earlier, a number of waste plastics to chemical feedstock process technology platforms are being demonstrated today. These include bioreactors that would convert plastic to chemicals via microbial digestion and pyrolytic systems, which could also be used to produce chemicals and fuels.
It is not clear how waste plastic to fuels would be beneficial to the environment, as the petroleum-derived carbon in the plastic would be liberated to atmospheric CO2 once combusted. What is clear is that all things being equal composite materials will be more challenging to recover than those that are made from a single material. For example, personal care nonwovens, which often contain a blend of manmade fibers and natural fibers, will be harder to separate, than a spunbond fabric made entirely from polypropylene. Arguably, adding bio-based polymers to a product, while potentially lowering its carbon footprint, may make it more difficult to recycle.
What could be emerging as a success story for plastics recycling is PET. Because of its intrinsic value, PET is recovered at a relatively high rate and there many examples of mechanical recycling of PET including use of rPET as a feedstock for nonwovens production. This is a great example of a potentially closed loop for plastics.
The difficulty with composites
With regards to composite materials, take for example, a paper-based hot-cup. Each year, the world consumes and discards more than 250 billion paper cups. Once used, these cups enter the waste collection stream and typically end up in a landfill or incinerator. The cradle-to-grave story of the paper cup is being challenged by consumers and brand owners as being unacceptable and unsustainable. The paper cup is just an example of a product under siege, but it could easily be a facemask made from nonwovens, a diaper or a wipe.
The paper cup is a composite material, a layer of cellulose-based paperboard and an extruded film of LDPE. Cups are ubiquitous and they have some serious design flaws when viewed from the perspective of waste management. First, only the paper component is biodegradable. Second, it is difficult to recover because most recycling outfits and their customers do not want to handle food waste. Third, if it does find its way into a recycling stream, the largest consumer of wastepaper, namely, recycled paper mills, do not want wastepaper that is contaminated with plastic.
Replacing LDPE with polylactic acid would seems like a potential solution to the problem of cup waste. PLA is bio-based polymer so one would assume that it would offer an advantage in waste management. The reality, however, is PLA is biodegradable only under control conditions at industrial composting centers, which as discussed earlier are not widely available and do not readily accept bio-based plastics.xiv
This is why a number of companies, led by Starbucks, along with Coca-Cola Company, Yum! Brands, Nestlé and Wendy’s, as well as a host of NGOs, including The World Wildlife Fund, joined together to create the NextGen Cup Challenge, offering up to $1 million in funding to innovative solutions providers to address the problem of cup waste. One of the more promising approaches has been the development of novel aqueous coatings, which enable a more effective means for recovering the fiber component of the cup. This open innovation approach could be a model for any product category.
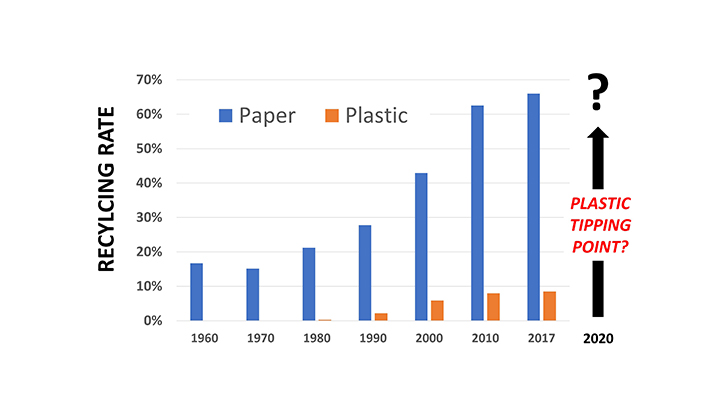
Solutions for leakage
Arguably, leakage, the waste plastic that is all too visible in both terrestrial and marine environments, is a great driver behind our re-thinking of the plastics value chain. Clearly, we must develop ways for containing the problem of leakage. Improved collection, storage and reprocessing infrastructure is essential for addressing these problems, especially in light of the anticipated growth in plastics consumption. Of course, the big question is “who will pay for the infrastructure needed to collect and process this material?”
Many, including leading non-government organizations, believe that bio-plastics will be a major part of an overall strategy for reducing plastic waste. For example, the MacArthur Foundation posits an aspirational goal of developing “a bio-benign plastic packaging material that would reduce the negative impacts on natural systems when leaked, while also being recyclable and competitive in terms of functionality and costs.” However, they admit that biodegradable plastics “rarely measure up to that ambition.”xv
What does this all mean for bio-plastics?
As the global economies begin to recover from the impacts of COVID-19, the demand for bio-based plastics is likely to increase significantly. The drivers for growth will be renewed concerns for the environment and the need to reduce leakage. This should create enormous demand for bio-plastics that can biodegrade in nature, and especially in sea water. Additionally, regulatory frameworks, such as those emerging in the European Union, which penalize fossil-based materials, will spur demand for all bio-based plastics, provided the bio-based substitutes can be shown to provide real lifecycle benefits. As consumer and regulators become better educated on green-washing strategies, companies may be surprised by the outing of such strategies. Lastly, the global plastics industry is not standing still. It is actively developing strategies for recovering and reusing waste plastic. The expectation is that new recycling infrastructures will emerge to create a more rational approach to plastics use, one based on circular rather than the current linear model. The challenge will be defining what constitutes an acceptable level of leakage, because clearly 100% waste recovery is unlikely. Those industries and sectors that use lifecycle data as a basis for material choices and develop robust waste recovery strategies will create formidable winning points of differentiation for their products and businesses.
References
i. Hillmyer, M., “New Approaches to Solving the Plastics Dilemma,” National Academy of Science, Annual Meeting, April 26, 2020.
ii. The Economist: https://www.economist.com/international/2020/06/22/covid-19-has-led-to-a-pandemic-of-plastic-pollution
iii. Choi, A., “Why Plastic Waste is a C-Suite Problem,” Harvard Business Review, April 21, 2020.
iv. Directive (EU) 2019/904 of the European Parliament and of the Council of 5 June 2019 on the reduction of the impact of certain plastic products on the environment, OJ L 155, 12.6.2019.
v. Taufik, D., Reinders, M.J., Molenveld, K., Onwezena. M.C. (2020). “The paradox between the environmental appeal of bio-based plastic packaging for consumers and their disposal behaviour,” Sci. Total Environ. 705, 135820. DOI: 10.1016/j.scitotenv.2019.135820
vi. Devlin, M., “It’s Greenwashing: Business left frustrated as pricey bioplastics still end up in landfills”, The Globe and Mail, July 8, 2019.
vii. Sijtsema, S.J., Onwezen, M.C., Reinders, M.J., Dagevos, H., Partanen, A., Meeusen, M. (2016). “Consumer perception of bio-based products—An exploratory study in 5 European countries,” NJAS-Wagen. J. Life Sci., 77, 61-69. DOI: 10.1016/j.njas.2016.03.007
vii. https://www.mdpi.com/2071-1050/12/2/675/htm
ix. NPR, “Plastic Has a Big Carbon Footprint,” Retrieved from https://www.npr.org/2019/07/09/735848489/plastic-has-a-big-carbon-footprint-but-that-isnt-the-whole-story.
x. Maile, K., (2019), “ACC report: Advanced plastics recycling has potential $10B impact.” Retrieve from www.recdyclingtoday.com/article/advances-plastics-recycling-chemical-recycling-has-potential-10-billion-economic-impact/
xi. Kirilyuk, M., et al., “The European recycling landscape – The quiet storm?”, McKinsey & Company, Aug. 13, 2020.
xii. Chadwick, P., “Greenwash or good practice?”, PackagingNews, 7 August 2020. Retrieved from https://www.packagingnews.co.uk/features/greenwash-good-practice-special-report-07-08-2020
xiii. Brooks, A.L., et al. (2018). “The Chinese import ban and its impact on global plastic waste trade,” Science Advances, 4(6), Vol. 4, no. 6, eaat0131, DOI: 10.1126/sciadv.aat0131.
xiv. European Bioplastics (2019). Industrial Composting. Retrieved from https://docs.european-bioplastics.org/2016/publications/fs/EUBP_fs_industrial_composting.pdf.
xv. The New Plastics Economy: Rethinking the Future of Plastics, Ellen MacArthur Foundation.