Polyacrylonitrile (PAN) is a polymer with exceptional resistance to sunlight and chemicals. It is usually used as textile owing to its soft and wool-like touch.
Most PAN textiles are produced by the wet-spinning process, where the polymer is dissolved in a solvent to be then extruded into a bath of fluid. The polymer solidifies in this bath in fiber form and is used after certain post-treatment steps for the production of jackets or shirts and home textiles.
Moreover, wet-spun PAN fibers are the precursor material for the production of high-performance carbon fibers, which are used in technical applications such as sports cars and wind turbines. Wet-spun PAN fibers account for about 10.2% of the global production of manmade fibers.[1, 2]
While PAN is a preferred material for many applications, the situation for fiber producers is deteriorating. In recent years, two trends can be observed that are putting pressure on global PAN fiber manufacturers.
The first trend is the declining market share of PAN in the global manmade fiber market, together with increasing cost pressures on PAN fiber manufacturers. The second trend is the increasing awareness of worker safety and consumer protection, both within and outside Europe.
One current program of the European Union that addresses the safe handling of chemicals in industry is the REACH (Registration, Evaluation, Authorisation and Restriction of Chemicals) legislation in which carcinogenic and mutagenic substances are strictly regulated and, in some cases, banned from industrial use.
Need for alternatives
For the production of PAN fibers, solvents are needed to dissolve the polymer and to convert it into compact fibers. However, the solvents mostly used are highly hazardous to health. For this reason, these substances are restricted by the REACH legislation in Europe; there is a similar regulation in China.
In particular, the allowed exposure limits of the solvents in the air are to be further reduced, even though the limits are already very low. If the regulations come into force as planned, the solvents will probably no longer be available for fiber production. Fiber producers outside Europe are also affected by the new regulations if they wish to import their goods into Europe.[4]
The REACH legislation thus has a far-reaching effect on the PAN fiber market and is forcing many manufacturers to think about the use of alternative, REACH-compliant solvents.
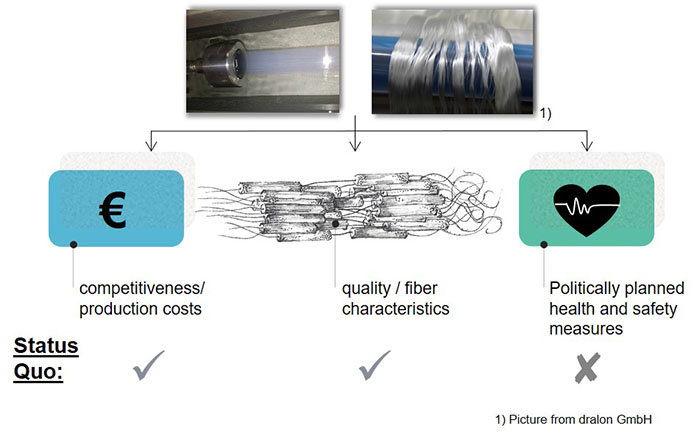
However, the above-mentioned trends complicate this step. Owing to cost pressures in the market, the process change must not lead to higher production costs and the conversion costs must be as low as possible for PAN fibers to remain competitive compared with other fibers.
Research aim
For future REACH-compliant production of PAN fibers with a less toxic solvent needs to be identified, which will allow an economically competitive production process. Moreover, it should be available for use in existing production plants and the fiber properties should not decrease to avoid excessive costs or losses in market share. Keeping this in mind, the available alternative solvents for the fiber manufacturing process were investigated and compared.
Approach
In a first step, the state of research on the available solvents was considered. Promising solvents were then chosen regarding economic potential, potential hazards and performance in the wet-spinning process, with the most promising solvent selected.
The associated process was investigated technically, and a detailed cost analysis conducted. Moreover, technological solutions were developed and investigated to reduce production costs and improve fiber qualities. Finally, an evaluation was made in comparison with the current industrial standard process.
Alternative solvents
Both dimethyl sulfoxide (DMSO) and sodium thiocyanate (NaSCN) can be used as REACH-compliant solvents for PAN fiber production. The results from the theoretical, financial and practical investigations were the basis of a technical/economic analysis, where the process variants with NaSCN and DMSO were compared with the standard solvents, with the results shown in Figure 3.
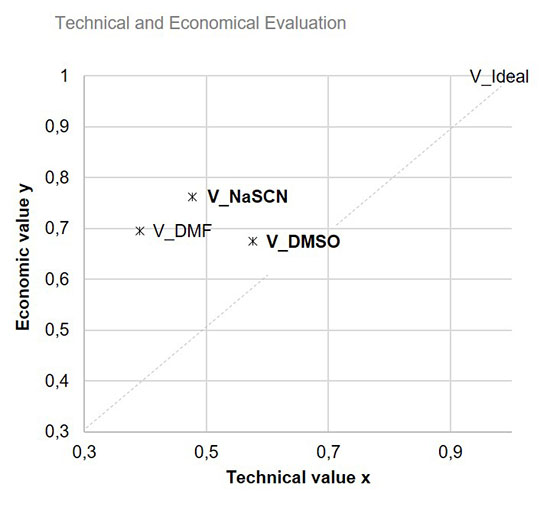
It can be seen that the technical value is better for both solvents compared with the standard process. NaSCN shows a higher economic value and is thus the favorable alternative solvent.
Cost savings
NaSCN enabled cost savings of 8.6% compared with the current standard process. These savings can be achieved by using a more efficient water recovery process, developed with industry partner Herberger Wasseraufbereitung. Thus, the use of NaSCN is reasonable in terms of strategic and economic aspects and the fiber quality is comparable to the current standard processes.
DMSO can be used as a less-corrosive alternative for older, less corrosion-resistant production plants. It is also an interesting option owing to its good handling properties.
The research showed that the change of solvent is linked to significant technical and financial risks. However, there is also good potential to improve the sustainability and work safety of the process with the use of alternative solvents and to stay financially competitive at the same time. The detailed results were published as a Ph.D. thesis.[5
References
- Gupta, A.K., Paliwal, D.K. & Bajaj, P. (1991) J. of Macromol. Sc., Polymer Reviews 31.
- Derkov, A.T. & Budnitskii, G.A. (1993), Fiber Chemistry, Vol. 25, p. 3-7.
- Schematische Darstellung zum Thema “So funktioniert REACH” (https://www.chemie.com/fileadmin/_processed_/b/2/csm_So_funktioniert_REACH__1__d1a41dd6f1.jpg), Zugriff 28.11.2019.
- European Chemicals Agency (ECHA), Helsinki (Hrsg.): Internetportal der ECHA mit allen relevanten Information zur REACH-Verordnung; (https://echa.europa.eu/de/registry-of-restriction-intentions/-/dislist/details/0b0236e1844d552a), Zugriff 03.03.2020.
- Peterek, S.A., (2021) “Kosteneffizientes Nassspinnen von Polyacrylnitrilfasern mit alternativen Lösungsmitteln,” Shaker Verlag, ISBN 978-3-8440-7653-0.