Digital transformation and Industry 4.0 will increasingly impact the competitiveness and economic success of small and medium-sized enterprises in the future.
Within this changing work environment, companies face several challenges. Besides the implementation of software and digital solutions, further competences of employees, as well as their motivation and confidence towards digitized processes, need to be ensured.
To overcome this barrier, smart model and learning factories, such as the Digital Capability Center (DCC) Aachen, have been developed, offering a variety of training and support companies following their path towards Industry 4.0.
DCC Aachen
The DCC Aachen was founded in 2017 in cooperation with the ITA Academy, Aachen, Germany, and McKinsey & Company, USA, together with leading technology partners. It depicts digital transformation along the entire supply chain in an interactive and realistic way. Its learning and demonstration environment with direct access to textile production conditions and processes enable action and problem-oriented learning.
The center demonstrates Industry 4.0 along the entire textile production chain for the production of a smart wristband. All stages of the supply chain are covered, from order intake to product development, production and service. Several digital solutions were implemented at all of these stages.
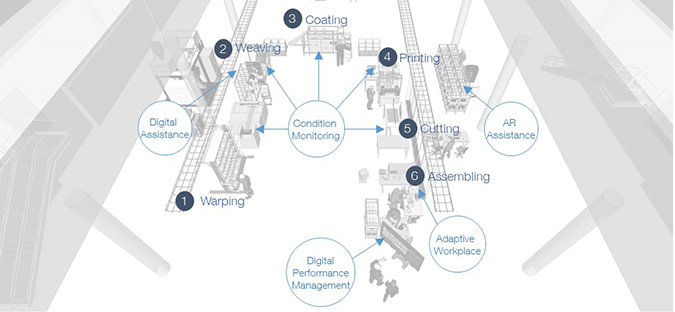
Digitized textile supply chain
The DCC learning factory simulates the production of a real product – a smart wristband. Not only does the model factory demonstrate the potential of Industry 4.0, the wristband itself is also a smart product.
The wristband includes various functions regarding human-to-machine communication. Machines or working stations are set up individually based on the employee identification. For example, table heights, orders, working instructions as well as machine rights can be adjusted as they are saved on the wristband’s radio-frequency identification (RFID) chip.
Production of the wristband includes six stages, which are presented in the DCC: weaving preparation (warping); fabric production (weaving); finishing (coating and digital printing); assembly (cutting, sewing and packaging); and quality control. At each stage several digital solutions are demonstrated.
One of the digital solutions at the DCC is condition monitoring, which offers comprehensive information on the production processes. Its aim is to minimize machine downtimes by 50% as well as minimizing scrap by 80%.
Real-time data is collected by internal as well as external sensors, which is displayed on the employees’ tablet computers or smartphones. An alarm is set off as soon as the process diverges from the preset parameters.
The data is extracted from the programmable logic controller (PLC). As the PLC is not extractable in some cases, additional external sensors can provide the required data from the machines. The extracted data from all machines and sensors is collected by middleware. An Internet of Things (IoT) platform is used to visualize the collected data as well as the machine connectivity.
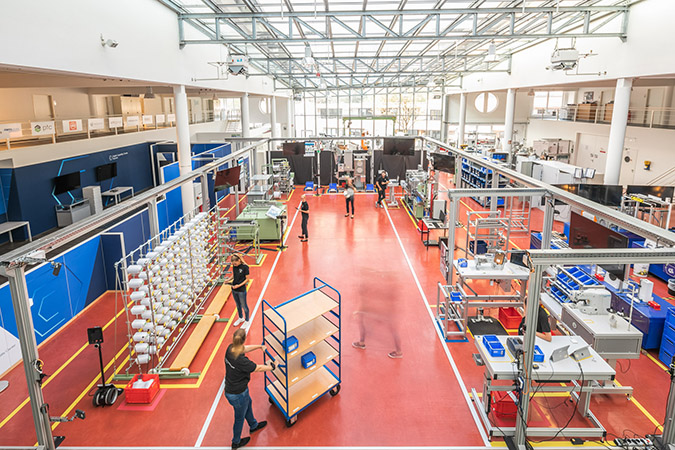
Condition monitoring
With condition monitoring during the warping process, the employee can get all quality control information when logging on to the machine. Various sensors collect data on yarn tension and knots, vibration and abrasion, temperature, humidity and light. The collected data enable a faster reaction on problems during the warping process and offer a databased-decision basis.
Another digital solution is digital assistant systems, which can reduce setup time-related machine downtimes by 75% as well as required training by 50%. For example, unexperienced or untrained employees can get the required help for machine usage from this system.
After warping, the elastic woven fabric for the wristband is produced on a needle tape loom. Working instructions on weaving parameters and machine commissioning are provided to employees through a digital assistant system, with instructions based on the employee’s training level. Solving upcoming problems, such as a broken thread, can be supported by augmented reality and step-by-step instructions.
In the finishing process, the woven fabric will be heat-set and coated. With machine learning, asset optimization such as the adaptation of energy consumption is automatically regulated.
Customized fabric
In the next step, digital printing, the fabric can be customized: production of a lot size of one is therefore possible. The layout of the wristband can be designed and ordered at the digital printer via an app. The data is converted into a QR code that is printed onto the wristband. As a result, each wristband can be identified and allocated to its order. After printing, a camera controls the printing quality via artificial intelligence (AI), before the printed fabric is cut into wristbands at size-specific marks.
For the stage of assembling, the DCC demonstrates a number of combined digital solutions: adaptive/individualized workplace design; cycle time measurement; and digital assistant systems. Through digitalized solutions divergence in cycle times can be reduced by up to 80% while productivity can be increased by 25%.
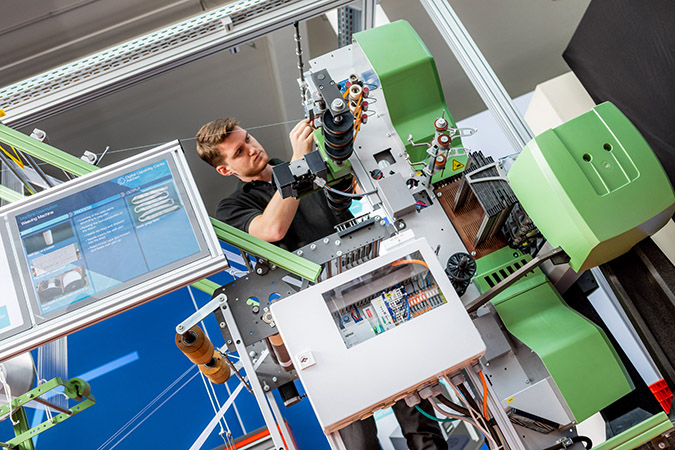
Assembling and logistics
At the assembling stage of the DCC, employees are guided through the process step by step by a video assistant system. By logging on to the machine the working station adjusts to the employee’s needs, e.g. table height, language and comprehensiveness of instructions, etc., which ensures, for example, increased ergonomics and work safety.
The DCC also demonstrates digital solutions regarding logistics, in this case the material supply of all process stages. This is achieved with the help of augmented reality using Google Glass smart glasses, which can increase the productivity of the logistics process by 25% as well as the quality of the process.
The items in stock are equipped with RFID tags. Employees wear a wristband that includes an RFID reader, which recognizes correct or incorrect item picking. In the case of incorrect picking, the employee receives acoustic and visual feedback. The error rate in the logistics stage can be decreased by 60%.