Scandinavian countries are currently leading the pack when it comes to new developments in the sustainable production of fibers and moving towards the establishment of circular manufacturing and supply chains.
The region’s long heritage in forestry and paper production has led to the introduction of a number of new sustainable cellulosic fibers made from waste inputs, with some already at an advanced stage.
In February this year, for example, Spinnova announced a partnership with Suzano – the world’s largest wood pulp producer – to build a $60 million commercial scale Spinnova fiber production facility in Finland. The Spinnova program is being backed by apparel brands such as the Stockholm-headquartered H&M Group, the Danish clothing company Bestseller, Finnish fashion house Marimekko, and Norwegian outdoor brand Bergans.
Bio2
During March, at the virtual Pitti Uomo clothing show, Finnish designer Rolf Ekroth premiered the first fashion collection made from Bio2 Textile – a new straw-based textile fiber developed by Fortum Bio2X.
Fortum, the Finnish state-owned energy company headquartered in Espoo, Finland, is involved in many initiatives to drive the fast and reliable transition to a carbon-neutral economy.
Its aim with Bio2X is to produce high-value products from agro-residues and woody biomass to replace fossil-based raw materials, using the “fractionation” technologies developed by biorefining technology company Chempolis, of Oulu, Finland.
The region’s long heritage in forestry and paper production has led to the introduction of a number of new sustainable cellulosic fibers made from waste inputs, with some already at an advanced stage.
Infinna
In April, regenerated cellulosic fiber developer, Infinited Fiber Company (IFC), announced it was also looking for a location in Finland to build a $260 million plant with an annual capacity of 30,000 metric tons of its Infinna regenerated fiber. The company is currently negotiating offtake agreements with several global fashion and textile brands and believes agreements will be in place before the end of 2021, securing the factory’s entire output capacity for several years.
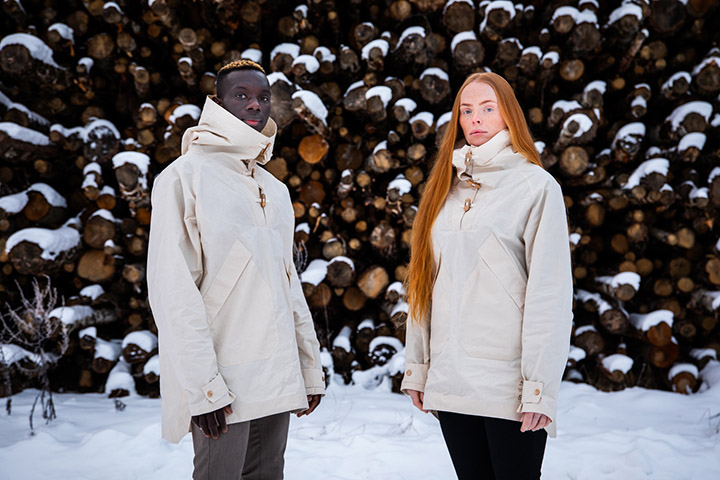
Easy win
For apparel brands, sustainable new fibers are an easy marketing win, but it is not so easy to explain the complex processes such fibers are subjected to, in order to turn them into textiles.
However, many of the environmental benefits these new cellulosic fibers can potentially deliver may actually be lost in the further processing of textiles – and especially in conventional dyeing and finishing. These operations currently involve many washing and drying process steps, which add a huge burden to the overall carbon footprint of finished garments.
We aRe SpinDye
This is another area that is being addressed in Scandinavia, and H&M has already featured new designs dyed with the We aRe SpinDye process, developed by WRSD, of Stockholm, Sweden.
This process involves melting color pigments and a mass of recycled polyester together prior to extrusion, to create homogenously colored yarns without the use of water.
WRSD works exclusively with recycled polyester made from post-consumer water bottles or wasted clothing, allowing for a truly circular production method and importantly, multiple fabrics can be made from a single yarn source for exceptional resource efficiency and very little waste.
By using WRSD’s technology when dyeing textiles, water consumption is said to be reduced by 75% and chemical consumption by as much as 90% compared with traditional dyeing of fabric.
“More companies in the fashion industry are now paying attention to the negative environmental effects of dyeing textiles, which is a global problem that needs more attention,” said WRSD CEO Andreas Andrén. “It has been fantastic to work with pioneering and brave designers to show that it is possible to create fantastic garments with our resource-efficient coloring method. We want to stress that color and process can no longer be ignored.”
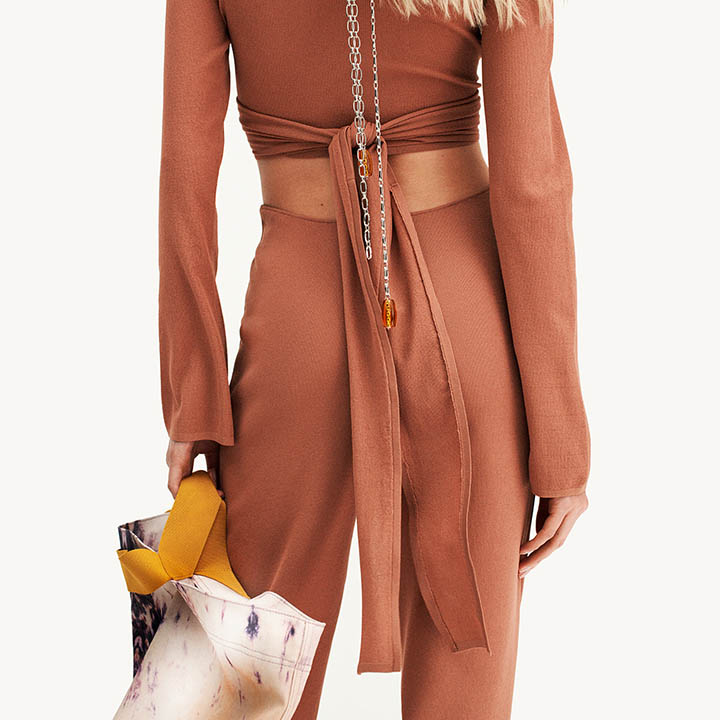
TexCoat G4
Three members of TMAS – the Swedish textile machinery association – are also actively developing new resource-saving technologies for dyeing and finishing.
In 2019, Baldwin Technology, which has its global headquarters in St Louis, Missouri, but its product and technology center in Arlöv, Sweden, introduced its TexCoat G4 system – a non-contact spray technology, which brings numerous advantages compared to conventional methods of applying finishing chemistry. The chemicals are uniformly distributed across the textile surface and applied only where required – on one or both sides of the fabric.
With the TexCoat G4, 100% of the over sprayed chemicals are recycled and because only the necessary amount is applied to the fabric to start with, a reduced wet pick-up level of 50% can be achieved.
The TexCoat G4 also allows complete tracking and control of the process to guarantee consistent quality, with recipe management including automated chemicals delivery, precise coverage selection and automated speed adjustment and fabric width compensation.
The system can process a wide range of low-viscosity water-based chemicals, such as flame retardants, water and oil repellants, softeners and anti-microbials.
Baldwin immediately secured major orders for the TexCoat G4 on demonstrating it at the ITMA textile machinery show in Barcelona in June 2019, and deliveries have continued throughout 2020 and 2021, despite the disruption caused by COVID-19.
However, many of the environmental benefits these new cellulosic fibers can potentially deliver may actually be lost in the further processing of textiles – and especially in conventional dyeing and finishing.
Thread coloration
Coloreel has meanwhile just raised over $10 million in new financing to support the market expansion and growth of its instant thread coloration technology.
Initially targeting the embroidery market, Coloreel technology enables the high-quality and instant coloring of a textile thread while it is actually being used in production and can be paired with any existing embroidery machine without modification, while also making it possible to produce gradients in an embroidery for the first time.
Based on a CMYK ink system, Coloreel’s advanced rapid color formulation software and high-speed drive technology allow a single needle to carry out what previously required many multiples of them to do – and with much more consistent stitch quality.
In addition, existing thread dyeing plants can add a single solid color to a thread, but by instantly coloring a white base thread during production, Coloreel enables complete freedom to create unique embroideries without any limitations in the use of colors. Color changes along the thread can either be made rapidly from one solid color to another, or gradually, to make smooth transitions or any coloring effect desired.
This provides big benefits when it comes to sustainability. There is a significant reduction in wasted inks, while water usage is minimized, and production speeds are increased. The technology allows set-up and lead times to be reduced as well as significant flexibility in production schedules, while eliminating the need for large thread inventories.
Coloreel has recently delivered units to companies in Europe, the United States and Asia, and has also partnered with the world’s largest distributor of embroidery machines, American Hirsch Solutions, which has already installed the technology at a number of customers in the U.S.
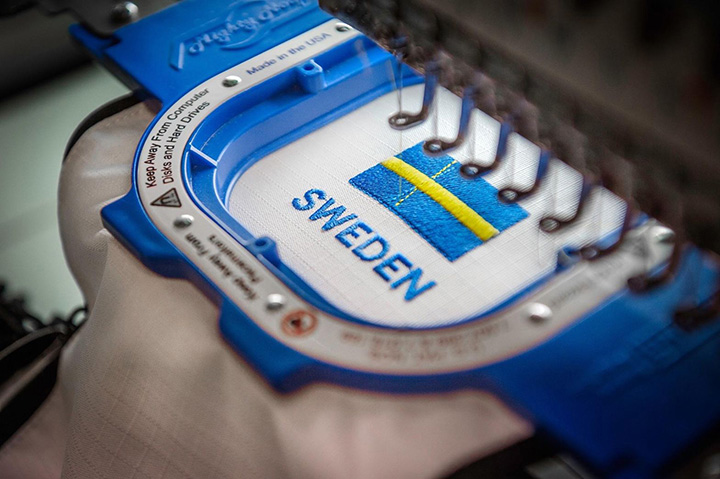
Dye-Max
Also achieving rapid progress is imogo, which has just installed its first industrial-scale Dye-Max spray dyeing line at the plant close to Borås of Swedish commission dyeing company 7H Färgeri – the Nordic region’s most complete dyeing and processing plant.
The new line has a working width of 1.8 meters with an operating speed of up to 50 meters for the reactive dyeing of cellulosic fiber-based fabrics. In addition, it can carry out the application of a wide range of fabric pre-treatments and finishing processes, providing the company with unbeatable flexibility in production.
With the potential to slash the use of fresh water, wastewater, energy, and chemicals by as much as 90% compared to conventional jet dyeing systems, the Dye-Max has gained considerable attention since the concept was outlined and a prototype machine constructed in 2019.
H&M is amongst the companies to have already tested the technology, which has resulted in the launch of a men’s suit for the brand’s Innovation Story Rental collection. The focus for imogo in the coming 12 months is to adopt the technology for polyester dyeing and large-scale tests will start this summer with a leading Turkish producer.
Neste
New Scandinavian developments also include the creation of established synthetic fibers from bio-based inputs.
Attempts to produce a viable bio-polypropylene (PP), for example, have been made over the years – most notably by Procter & Gamble working with Braskem of Brazil – but have proved unsuccessful.
Now Neste, based in Espoo, Finland, is producing bio-based alternatives to conventional fossil-based feedstocks for the production of polymers and chemicals and in the past two years has been working with two of the major European PP manufacturers – LyondellBasell, one of the world’s largest plastics, chemicals, and refining companies globally, headquartered in Rotterdam, the Netherlands, and Vienna, Austria-headquartered Borealis. Both have announced progress with technologies for producing bio-PP from agricultural waste.
With its proprietary NEXBTL technology, Neste claims it can utilize nearly any bio-based oil or fat as a raw material, including lower-quality waste and residue oils, to produce various premium-quality renewable products.
Based on its technology, LyondellBasell has introduced the parallel production of bio-based polypropylene and bio-based low-density polyethylene at a commercial scale, using Neste’s renewable hydrocarbons derived from sustainable bio-based raw materials, such as waste and residue oils.
Borealis is now using Neste’s 100% renewable propane produced with NEXBTL technology as a renewable feedstock at its facilities in Kallo and Beringen in Belgium. From this, it has created an entire portfolio of applications based on renewable-PP called Bornewables, commercially launched in March 2020.
Bornewables products are said to offer the same properties as conventional PP and to be fully recyclable.
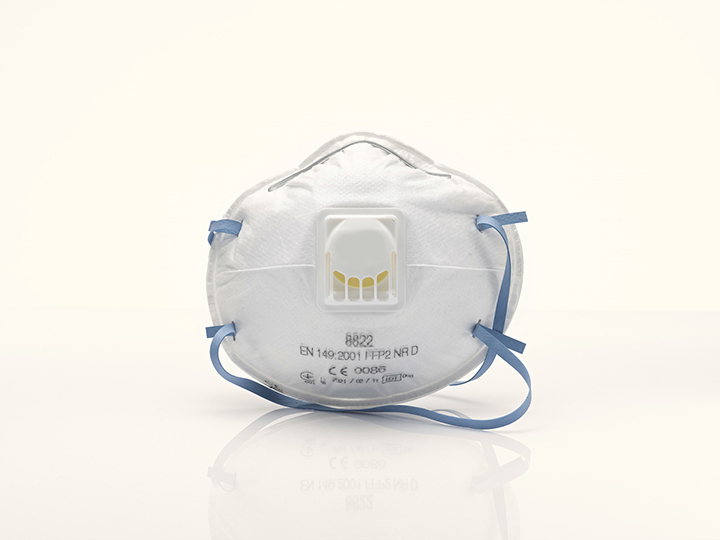
SABIC Trucircle
Nonwovens can largely avoid the dyeing and finishing processes involved in the production of conventional woven or knitted fabrics for apparel and in Denmark, Fibertex Personal Care, headquartered in Aalborg, has been shipping ISCC bio-based nonwovens since December 2020.
This marks a major milestone in the development and expansion of a supply chain for bio-based polymers from a major manufacturer of spunmelt nonwovens for the absorbent hygiene products market.
The range of nonwovens fabrics is based on a high-purity, recycled plastic developed with SABIC (Saudi Basic Industries Corporation), the multinational chemical manufacturing company headquartered in Riyadh, Saudi Arabia.
The fabrics are made from SABIC Trucircle circular PP, which uses feedstock derived from previously used plastics.