Solutions to Environmental Impacts of Current Materials
Today, the world’s nonwoven production is dominated by petroleum-based resins, most prominently polypropylene (PP) and polyethylene terephthalate (PET). But bio-based materials have also gained significant momentums in recent years due to their advantages in sustainability and low carbon footprint – the global efforts for carbon reduction, environmental protection, as well as less reliance on oil and petrochemicals have provided key driving forces to the growth of nonwoven fabrics made of bio-based materials such as cotton, viscose, and polylactic acid (PLA).
However, the disadvantages of bio-based nonwoven fabrics in performance, cost, and efficiency still inhibit their growth in various product segments and applications. Currently, researchers are working on new solutions to tackle these problems, covering sections from fiber treatment, nonwoven structures, composites, modifications, to customized processing methods and equipment for bio-based nonwoven production.
Bio-based materials for nonwoven production include three major types: bio-based natural fibers, regenerated fibers, and bio-based synthetic resins.
Natural fibers include plant fibers, animal fibers, and mineral fibers. Plant fibers (e.g., cotton, hemp, flax, jute) and animal fibers (e.g., wool, silk) are bio-based, while mineral fibers (e.g., asbestos) are not. Regenerated fibers include regenerated cellulose (e.g., viscose, lyocell), protein, and chitosan fibers. They are all biodegradable. Bio-based synthetic resins are produced by chemically or biologically synthesizing renewable organic materials such as corn, sugarcane, and straws. Polyhydroxyalkanoates (PHAs), polybutylene succinate (PBS), and PLA are bio-degradable, while the bio-based editions of polytrimethylene terephthalate (PTT), polyethene (PE), polyamide (PA), PP, and PET are not.
Plant Fibers
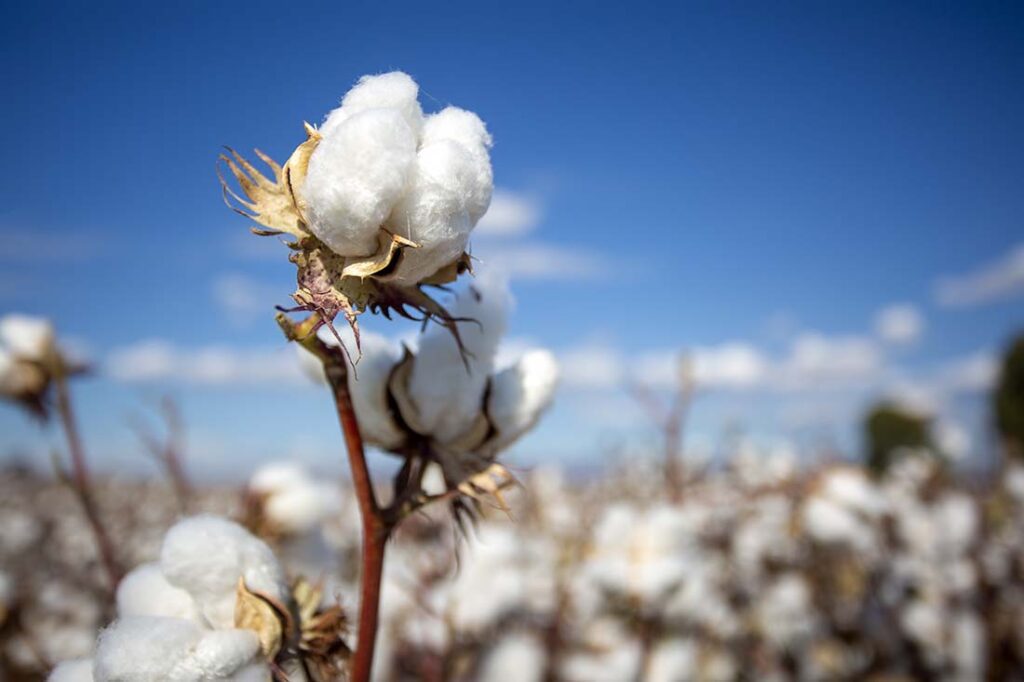
Cotton is the most widely-used plant fiber for making nonwoven fabrics. It played an important role in the early stage of nonwoven industry and has been in the spotlight again because of recent advancements in green production.
As a natural fiber, cotton has many good characteristics: it is bio-based, biodegradable, comfortable, and processable, and has good absorbency, among many other benefits. However, cotton also has its own problems, even in the environmental field where it claims to be “natural” and “green.” For example, its cultivation requires extensive land use, vast amounts of water consumption, and significant use of pesticides and fertilizers. Another example is that the cleaning and treating process that turns cotton fibers to nonwoven raw materials also consumes a substantial amount of water, chemicals, and energy.
The cultivation problems can be solved by using organic cotton, although at a premium price, while the cleaning and treating problems require innovated methods such as mechanical cleaning and vision systems. For example, the Greenwood, MS-based WildWood Cotton Technologies (WCT) has a mechanical cleaning process, which cleans cotton fibers without using water, chemicals or process heat, for its unbleached Tru-Cotton grades for nonwoven production. Recent research and development in this section may also incorporate vision systems with deep learning (DL), a branch of machine learning (ML) and artificial intelligence (AI), into the cotton cleaning and purifying process, aiming to further improve efficiency and purity, according to the technologies under development by China’s Xi’an Polytechnic University and several other universities and companies.
At the same time, conventional cotton nonwoven producers are also working on optimizing their cleaning and treating process to consume less water, chemicals, and energy. Other innovations for cotton nonwoven fabrics include improving their tensile strength, biocompatibility, antibacterial property, softness, and other performances, while turning the whole cotton nonwoven manufacturing process to a greener way by energy saving.
On the other hand, bast fibers (e.g., hemp, flax, jute) are regarded as an alternative to cotton in nonwoven production because they use less arable lands, water, pesticides, and fertilizers. However, the patterns and characteristics of bast fibers often have negative impact on production efficiency and nonwoven fabric properties – they are very coarse and difficult to be processed, and often require extensive treatment before being put into nonwoven production lines. Therefore, pretreatment technologies become a pivot for bast fibers being used.
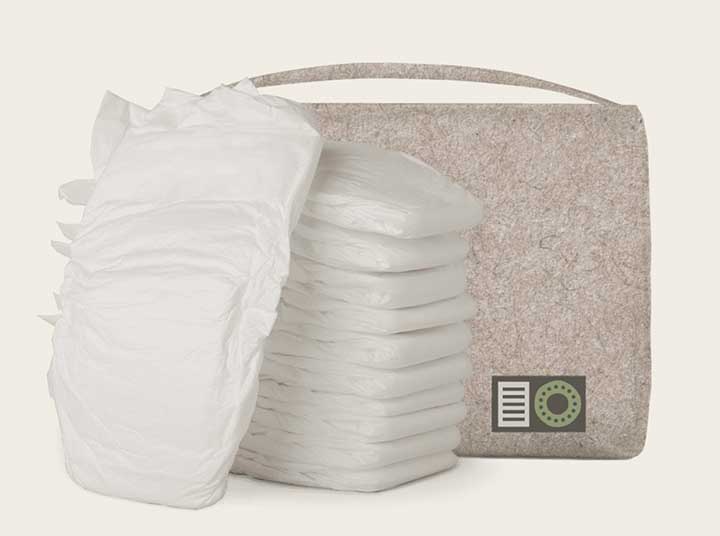
a circular, soil-to-soil lifecycle. Photo courtesy of BFT
The Canada-based Bast Fibre Technologies (BFT) is one of the active developers in this field. The company has a patented technology that treats bast fibers to provide crimps – using a portion of these treated bast fibers in nonwoven production will secure the desired properties and performance of the final nonwoven fabrics.
Recent research and development from other companies and universities mainly focus on customized equipment for bast fiber-based nonwoven fabric production, and formulas or composites for additional or improved characteristics such as flame retardants, abrasion resistance, antibacterial property, and liquid absorbency.
Animal Fibers
Animal fibers, such as wool and silk, are often too expensive to be used in nonwoven production. Therefore, researchers use two methods to reduce their costs:
The first method is to use reclaimed or discarded animal fibers and cuttings. Reclaimed wools and cuttings have created a substantial recycling market in some countries, but discarded wools are also everywhere – for example, the wools of some species of mutton sheep are low-quality and often discarded directly because there is no place to sell. These recycled animal fibers at low costs are suitable for nonwoven production after appropriate treatment.
The second method is making composite nonwoven fabrics of animal fibers with other less-expensive bio-based materials such as cotton and regenerated cellulose. For example, the China-based Suzhou Xianchan has a patented technology for producing spunlace composite nonwoven fabric from silk and less-expensive natural fibers or regenerated fibers. With only a small portion of silk being used, the final nonwoven fabric has a surface, touch, and luster similar to natural silk, while maintaining its bio-based and biodegradable advantages.
Some researchers combine the advantages of above two methods. For example, Xi’an Polytechnic University has developed a composite nonwoven fabric for packaging applications from reclaimed wools, polylactic acid (PLA), and wood-pulp cellulose through a wet-laid process. Similar research from other universities and companies show that composite wool-based nonwoven fabrics can be used in medical, sports, protective, automotive, and other applications.
Regenerated Cellulose Fibers
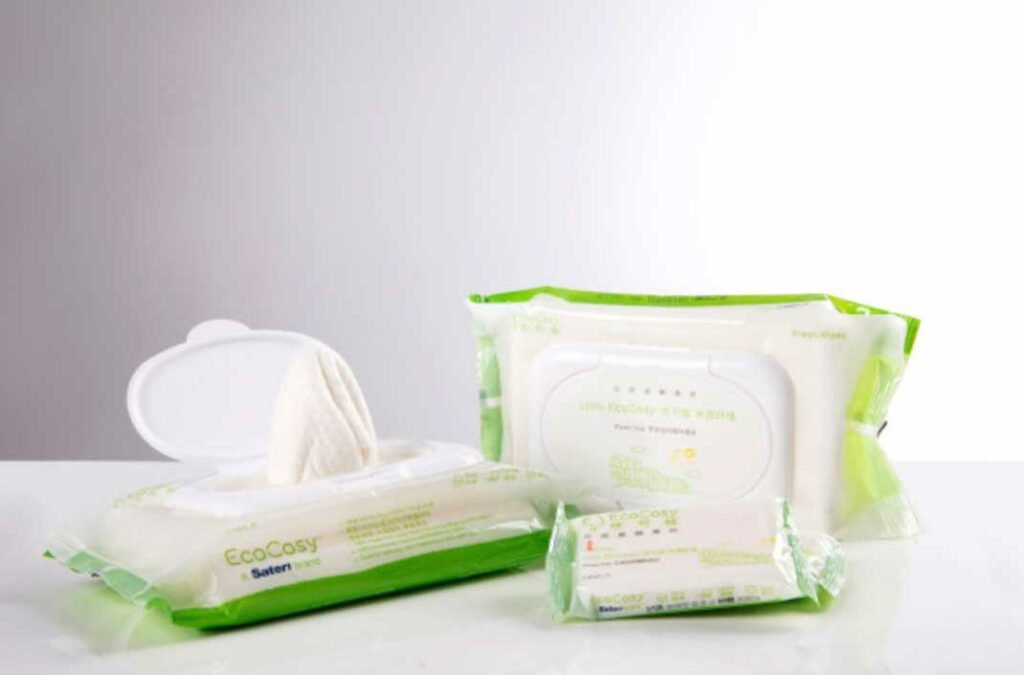
Regenerated cellulose fibers have long taken a considerable market share in nonwoven production. Today regenerated cellulose manufacturers provide many different products and grades for nonwoven production. These grades include the Austria-headquartered Lenzing’s VEOCEL™ Lyocell fibers, a certified net-zero carbon footprint, the China-based Sateri’s EcoCosy® viscose rayon fibers, and other cellulose fibers from Kelheim Fibres GmbH (Germany), Birla Cellulose (India), Shanyou (China), among many others.
But regenerated cellulose fibers have their own environmental problems. The manufacturing process may involve washing and bleaching with chlorine, or other chemicals which exacerbate pollutants.
In addition, the pretreatment process for regenerated cellulose fibers before nonwoven production often causes problems such as surface damage and strength reduction. Current research and development mainly focus on solving these problems. For example, the China-based Chenyang, a nonwoven producer, developed an equipment for cleaning while protecting viscose fibers before they are put into nonwoven lines.
Protein and Chitosan Fibers
Protein materials have also made some progresses in nonwoven production recently. For example, in addition to being used as a natural fiber in nonwoven production, as mentioned above, reclaimed wools are also used to extract keratin, a protein that can be used for making nonwoven fabrics.
Chitosan is a chemically cellulose-like biopolymer processed from chitin, the world’s second largest natural polymer after cellulose in terms of annual production volume.
According to the patented technologies developed by China’s Wuhan Textile University and several other institutes, protein nonwoven fabrics originated from reclaimed wools could exhibit excellent antistatic property, good abrasion resistance, and several other benefits.
Researchers also use chitosan as a raw material, along with bamboo-pulp fibers or other bio-based fibers, in making multiple-component nonwoven fabrics. Chitosan is a chemically cellulose-like biopolymer processed from chitin, the world’s second largest natural polymer after cellulose in terms of annual production volume, which indicates its potential of abundant supply globally in the future.
Protein and chitosan nonwoven fabrics are currently not been available in the market at a large scale. But these two types have been used in modifying other commercialized bio-based or petroleum-based nonwoven fabrics to increase the finish products’ biocompatibility, antibacterial performance, and other properties.
Bio-Based and Biodegradable Synthetic Resins
Bio-based synthetic resins will be the fastest-growing segment among the three major bio-based nonwoven types, although their current market size is still far smaller than natural fibers and regenerated fibers. It is where many are placing priority in the race to create a closed loop value chain (Figure 1).
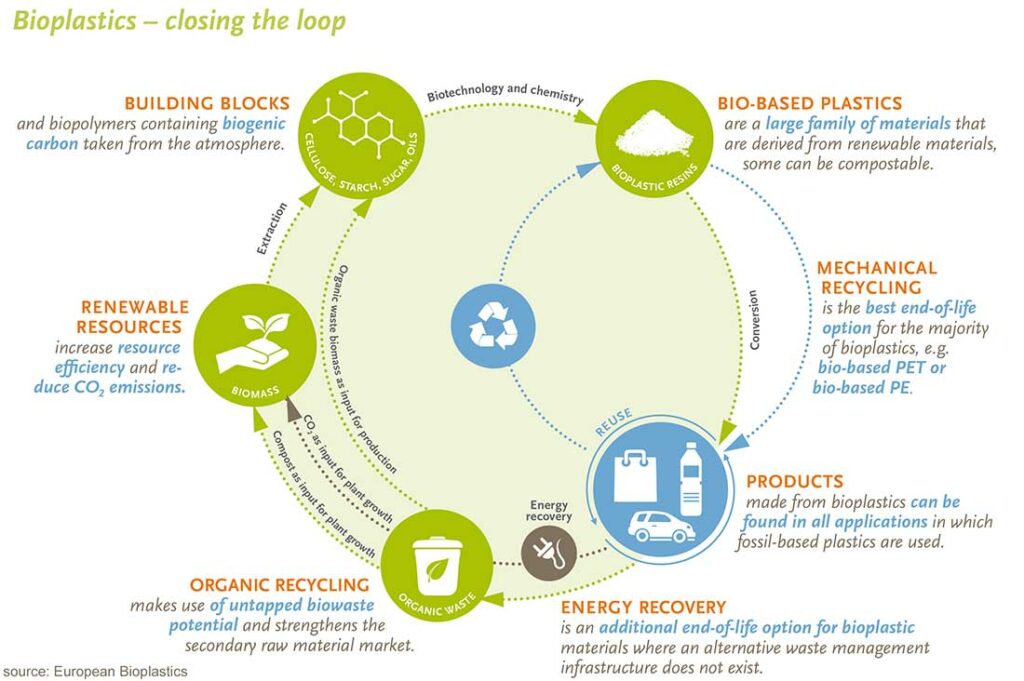
PLA is the most promising one is this segment. European Bioplastics e.V. forecasted that the global PLA capacity could be fivefold from 460 thousand metric tons in 2022 to 2.38 million metric tons by 2027, which will provide substantial amounts of raw materials for bio-based nonwoven production (Figure 2).
Unmodified PLA has disadvantages such as brittleness and low heat distortion temperatures. Therefore, it is often modified through chemical or physical modification methods or blended with other resins to improve their tensile strength, tensile modulus, thermal stability, biodegradability, biocompatibility, and other properties before being used in nonwoven production. For example, the Brazil-headquartered Fitesa produces spunmelt nonwoven from a blend of bio-based PE and bio-based PLA. However, as bio-based PE is not biodegradable, the nonwoven’s biodegradability decreases. Other companies and institutes have developed similar solutions that blend PLA with bio-based PTT or other non-biodegradable resins.
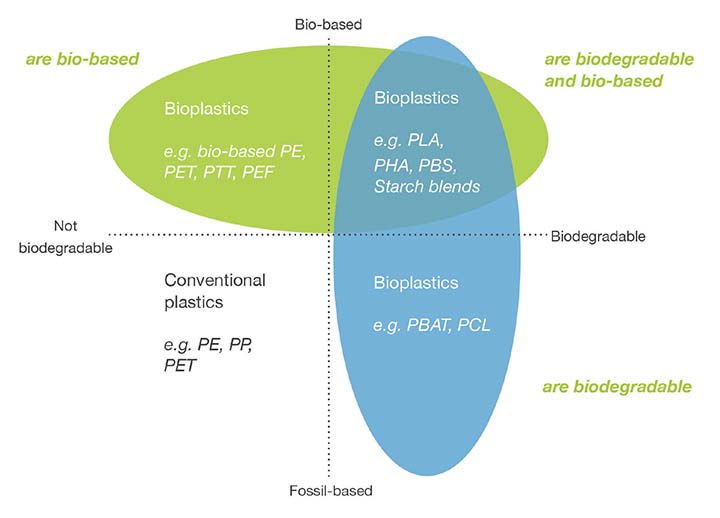
PLA manufacturers also face problems about nonwoven equipment. Most of the nonwoven equipment available in the market today are for the production of PP, PET, PA, PE, and other conventional petroleum-based nonwoven fabrics.
The China-based Dalian Hualun Nonwoven Equipment Engineering Co. Ltd. (Hualun), a nonwoven equipment developer and manufacturer, concluded that PLA nonwoven equipment should be specifically designed to prevent fiber breakage, improve web softness and uniformity, and increase tensile strength, compared to other conventional nonwoven equipment.
Hualun is the manufacturer of a PLA nonwoven production line operated by the Hong Kong-headquartered U.S. Pacific Nonwovens Industry Ltd. in its Dongguan, China-based facility. This line has an annual capacity of 2,800 metric tons with widths of 2.4 meters and weights ranging from 17 to 150 grams per square meters (gsm).
Polyhydroxyalkanoates (PHAs) are also promising bio-based synthetic resin for nonwoven production, with a potential production of million metric tons per year in the future. The most prominent commercially available PHAs are polyhydroxybutyrate (PHB) and polyhydroxybutyrate hydroxyvalerate (PHBV). However, the capacity and development of PHAs are still in the early stage. Currently global consumption of PHAs for both woven and nonwoven fabrics stays at only around 1,000 metric tons per year.
Pure PHAs nonwoven fabrics have similar problems as their PLA counterparts: brittleness, low tensile strength, etc. In addition to chemical and physical modification methods, researchers are also trying to use innovated structure to solve these problems.
For example, the China-based Zhuhai Maidefa Biotechnology Co. Ltd. (Maidefa) developed a three-layer structure to enhance the performance of their PHAs nonwoven fabrics. Researchers from the company found that excessive tensile deformation in both weft and warp directions would happen when a PHAs nonwoven is under external force. The excessive deformation at that level would limit the use of PHAs nonwoven fabrics in many applications.
To solve the problem, the researchers develops a three-layer structure, which includes two PHA surface layers and one base layer made of cotton fabric in the middle, with a thin cotton fabric covered the edges of the nonwoven long wise. The base layer, bonded to the surface layers with starch adhesive, and the covered fabric, stitched to the nonwoven with cotton yarns, provide enhanced strength to the nonwoven fabric. An additional benefit of this structure is that it helps prevent the roughness and unevenness of fabric edges. Maidefa was founded in 2019 as one of the early developers for PHAs nonwoven. It received approximate $10 million of series-A funding in 2022.
Multiple-component nonwoven fabrics made of PLA and PHAs or PBS are also under development. Researchers from Jofo, a major global nonwoven producer, and other companies show that spunmelt nonwoven fabric made of blends of PLA and PHAs or PBS have benefits of less brittleness, larger elongation, and higher softness, compared to those spunmelt nonwoven fabrics solely made of PLA resins.
Bio-Based but Non-Biodegradable Synthetic Resins
Alternatively, the bio-based but non-biodegradable synthetic resins such as PP, PET, PE, and PA may gain more market shares from their petroleum-based counterparts in the near future. Although being non-biodegradable, they still have a significantly reduced carbon footprint.
Their main advantage is that their petroleum-based counterparts have had very mature methods and equipment for nonwoven production readily available in the market, which is relatively easy to be adapted for corresponding bio-based nonwoven production.
As global chemical giants such as Braskem, LG, Borealis, and LyondellBasell have unveiled their ambitious plans on bio-based PP, whose petroleum-based counterpart has grabbed nearly half of the global nonwoven production, this segment may see a significant growth in the following decade.