Industrial Actions for Sustainability
As a Spanish polyester industrial yarn producer located in Barbastro, northeast Spain, in close proximity to the Pyrenees, Brilen Tech, S.A., has focused on growth and transformation programs initiated since 1996. Brilen has carried out a series of activities aimed at achieving sustainability, including these milestones that set the stage for high tenacity polyester yarn developments:
Establishing a starting point for improving sustainability, product life cycle analysis and transparency were the main goals. The most representative yarns produced by Brilen have been analyzed to obtain their Environmental Product Declaration, audited, certified and made available at Environdec. Brilen was the first company to certify the EPD of high tenacity polyester yarn through this prestigious entity.
Each capacity increase, from 2000 to the most recent in 2023, has been performed based on state-of-the-art technology, to ensure productivity, energy savings and optimal performance. Brilen treats 100% of the process water by MBR technology to eliminate contaminants and discharges.
The Environmental System based on ISO 14001, introduced in 2007, was completed by ISO 50001 for Energy Management Systems certification in 2019. 21% of this energy has been certified by SGS as renewable energy due to the installation of a photovoltaic plant for self-consumption initiated in 2020.
As a chemical company producing polyester chips, the entire industrial site supports Operation Clean Sweep, a global initiative from the plastic industry to reduce potential leaks of microplastics like pellets, flakes or powdered resin into the environment.
The commissioning of our Intermodal Terminal (TIM) has reduced CO2 emissions into the atmosphere by more than 80% due to the change in the transport of raw materials from road to rail, between the ports of Barcelona and Bilbao and our Barbastro plant. Additionally, this development facilitates hybrid transport using trains and trucks for our products, offering environmental advantages.
In 2023, a new rPET plant was inaugurated at the Barbastro industrial site. Equipped with the latest technology from Erema and fed with bottle flakes, Renovapet reliably supplies post-consumer recycled PET, enabling Brilen to achieve vertical integration for this special material.
Throughout 2024, the study on a post-industrial recycling plant will be conducted to explore the feasibility of closing the loop with a completely circular production of high tenacity polyester yarn.
All these initiatives are supporting the company in achieving more sustainable products with objective data.
More Durable Materials for a More Sustainable World – GLE-UV
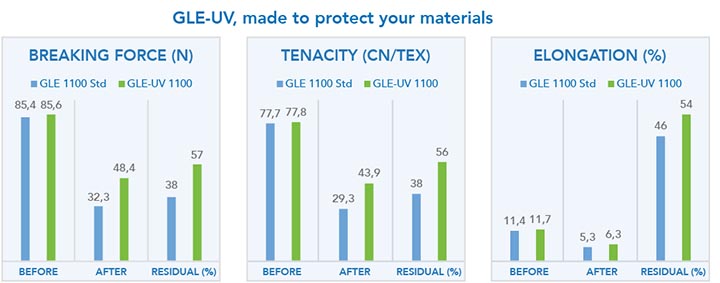
One of Brilen’s goals in the last year was to increase the durability of polyester industrial yarn in the environment while minimizing any loss in mechanical properties.
This goal has been achieved through the incorporation of an innovative additive during the spinning process. Consequently, the yarn now has a lower probability of breaking during utilisation, increasing the lifespan of products and reducing the need for substitution.
Two samples, one of standard high tenacity polyester yarn (GLE) and the other with this innovative additive (GLE-UV), underwent testing both in their original condition and after being exposed to ageing, in accordance with EN 12224:2001, a standard for Geotextiles and Geotextile-related products.
Subsequently, both sets of results were compared.
GLE-BIO is a yarn that biodegrades into methane at the end of its lifecycle, which, when properly captured, can be used as green energy.
On the graphs below, the breaking force of both GLE and GLE-UV can be observed before undergoing ageing, showing a notable similarity. However, after exposure, the decline in physical resistance for the standard GLE is much higher, retaining only 38% of the residual force compared to 57% for GLE-UV. Similar data can be seen in tenacity (breaking force per titer) and elongation, with the standard GLE exhibiting lower elongation after exposure.
The main benefit of our GLE-UV yarn lies in its durability as the material’s initial force can be sustained for a longer period. This means calculations would require a lower confidence margin due to the lower degradation of the material, saving yarn and waste.
GLE-BIO – Energy From Your Product
Organic materials undergo biodegradation in landfills, resulting in the production of biogas (methane) and biomass. This biogas production occurs continuously, 24 hours a day, every day of the year, as it converts materials into clean and sustainable green energy.
In today’s context, textile products do not always have the option of being recycled after use. In fact, a significant portion of plastic waste is typically sent for incineration, generating energy but also contributing to greenhouse gas emissions.
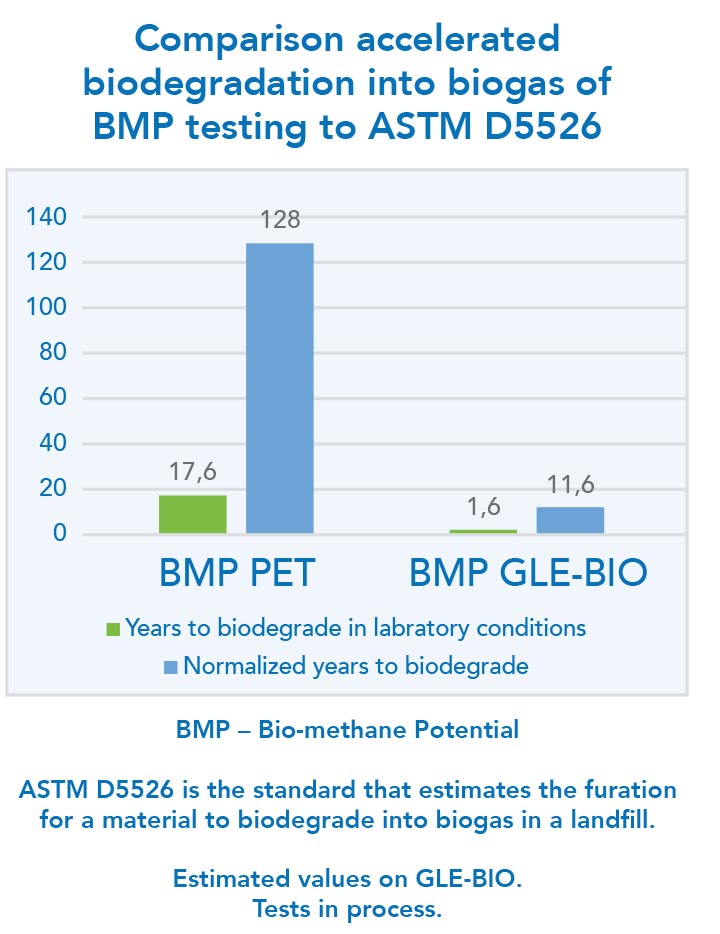
What Brilen proposes with fabrics made with GLE-BIO is a new sustainable solution, involving the recovery of post-consumer material and its conversion into green energy, specifically methane.
GLE-BIO is a yarn that biodegrades into methane at the end of its lifecycle, which, when properly captured, can be used as green energy. This material is not decomposed by oxygen or UV rays but only when exposed to a biologically active environment. Mechanical properties are maintained until biodegradation initiates upon contact with a biological aerobic or anaerobic environment.
To determine the biodegradation capacity of this yarn, testing was conducted according to ASTM D5526. This test estimates the time it takes for a material to biodegrade into biogas in a landfill. This is a long-term test that replicates the low heat, high pressure, limited oxygen, lack of light and low moisture conditions found in landfill environments.
Comparing standard GLE or just polyester (polyethylene terephthalate) material with GLE-BIO, it is evident that PET degrades in approximately 128 years, while GLE-BIO could biodegrade in only 11.6 years.
Low SHA Portfolio – Low Energy Consumption for an Ultra-low Shrinkage Yarn
Industries such as the cable market, textile architecture, composites, technical textiles and other polyester high tenacity applications require high tenacity yarns to have the maximum reinforcement, with the lowest shrinkage, to prevent defects in the final product when heated.
Until now, the best performance in shrinkage for polyester has been achieved in a two-step process: spinning and drawing to orient and crystallize the polymer, providing the low shrinkage properties expected. But these two steps process have a higher energy consumption and cost, as additional manipulation and time are required for the second production step.
Since March 2022, energy costs have increased exponentially, particularly in Europe, prompting Brilen to increase efforts on this project. Brilen has developed technology to offer the market a very low shrinkage high tenacity yarn, similar to the two-step production but with lower energy, time and resource consumption, as it is produced in a single step.
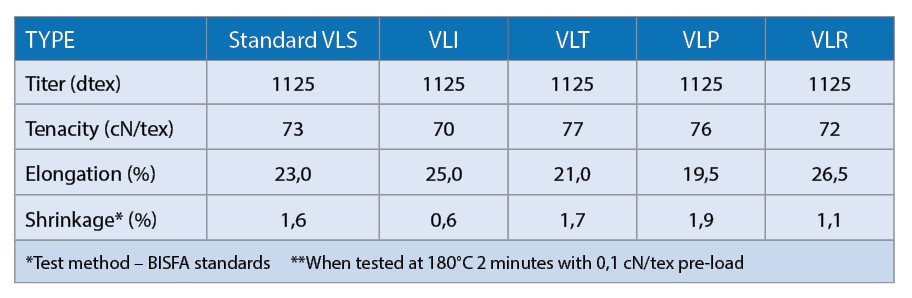
Brilen, Samca Group and Innovation
The company, with a production capacity of 26,000 tons per year, is part of Samca Group, a family-owned company with a €1.8 billion turnover and 4,000 employees, mainly in Spain. The group has a presence in mining, renewable energies, ceramics, agri-food, agri-chemical, logistics, real estate development, plastic polymers and synthetic fires.
This sector diversification facilitates vertical integration between polymerization and spinning processes. The synthesis of polyethylene terephthalate is conducted by NOVAPET, a sister company located in the same industrial plant in Barbastro, with a plate capacity of 260,000 tons per year. Novapet’s main activity is the production of PET to produce pre-forms for plastic bottles by the sister company Noven. Operating on the same industrial site, Renovapet, with a capacity of 15,000 tons per year, supplies post-consumer recycled polyester and is expected to be Global Recycled Standard certified in January.
High tenacity polyester is not the sole product produced by Samca Group, since the same vertical integration can be found at Zaragoza industrial plant through Promyde, focused on polymerization of polyamide 6 and polyamide 6.6, and Nurel, European leader in polyamide 6 and polyamide 6.6 textile yarns. Promyde develops and produces polyamide for injection or spinning. Additionally, at the Zaragoza industrial plant, biopolymers are developed with the company Inzea, with a production capacity of 25,000 tons per year.
All these companies have a common transversal Research, Development and Innovation department. Depending on the management of Samca Group, this department harnesses all synergies from the companies in a multidisciplinary group.