How the Hygiene Industry is Becoming More Sustainable Through Adhesive Innovation
Sustainability is increasingly important in today’s world. Manufacturers of absorbent hygiene products face significant challenges. They must combine environmental compatibility with the highest product quality while minimizing the carbon footprint of their products. Advanced technologies and collaboration along the value chain are opening up new ways to increase production efficiency and lay the foundation for a circular economy. But how do you make products more sustainable without compromising quality and performance?
Absorbent hygiene products such as diapers, adult incontinence products and menstrual care are in constant contact with the skin. This results in a wide range of requirements for product development and manufacturing: consumers demand products that are safe and effective, do not cause irritation, are free from harmful chemicals and allow freedom of movement. Demographics are also driving the need for adult incontinence products as the world’s population ages. Declining birth rates, later childbearing and fewer children are leading to a shift towards premium products over cheaper brands.
In recent years, demand for another product attribute has increased across all age groups: Sustainability. There is a desire for products that are made from natural materials, contain bio-based ingredients, are biodegradable, and have no negative impact on ecosystems.
Between Innovation and Sustainability: Materials and Processes for the Hygiene Industry
All these requirements present the absorbent hygiene industry with a decisive turning point. It is faced with the challenge of developing innovative and sustainable materials and processes for all needs. These should include different types of absorbent hygiene products: for example, fully flushable and biodegradable products, reusable solutions such as washable incontinence and period underwear, and disposable hygiene products such as sanitary towels. The design of sustainable hygiene products includes materials such as bamboo, recycled fibers and PLA, which need to be qualified and integrated.
For manufacturers, the goal is to meet these consumer demands as well as fulfill their own sustainability goals. These include reducing the carbon footprint, minimizing energy consumption and reducing production waste – without compromising operational efficiency.
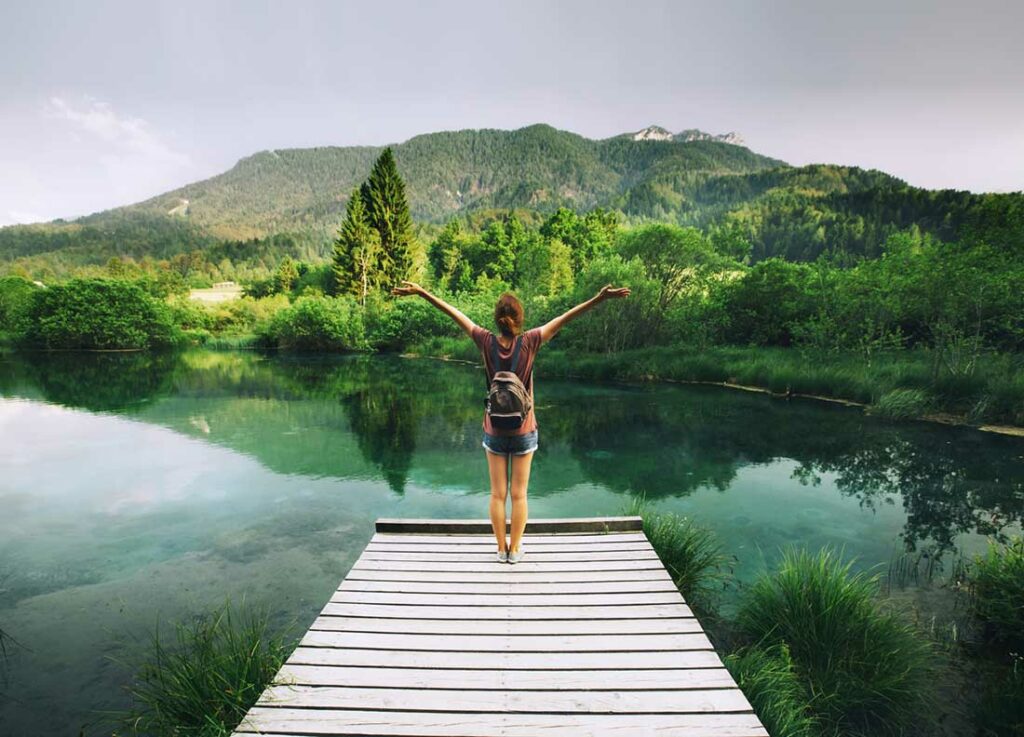
Example: The Ecological Impact of Baby Diapers
Baby diapers illustrate the potential for sustainable production in the hygiene industry. Every minute around the world over 300,000 disposable nappies enter landfills, incineration or pollute the environment, according to BBIA UK, most of which are made from fossil-based materials. Plastics derived from petroleum and cellulose processed with fossil fuels dominate the material composition and thus contribute significantly to the ecological footprint.
Analysis of the CO2 contribution shows that materials account for about 50 percent, the manufacturing process for 10 to 15 percent and the end of life for about 35 percent of a product’s total CO2 emissions. These figures underscore the urgency of minimizing dependence on fossil-based materials and pursuing alternative approaches.
Adhesives as a Key Element of Optimization
Adhesives play a crucial role in this context. They are an essential component of most hygiene products, from diapers to incontinence products to feminine hygiene products. Adhesives are used to bond the different layers of these products, provide elasticity, and ensure product functionality. Their selection and application therefore have a direct impact on product quality, processing efficiency and, ultimately, the environmental impact of the final product.
Given this central role, adhesive technologies play a key role in managing the balancing act between meeting consumer demands and achieving sustainability goals. Innovative adhesive solutions
developed specifically for the absorbent hygiene industry offer the opportunity to optimize production processes, save energy and reduce the use of raw materials.
To achieve greater sustainability, cross-industry collaboration along the value chain is essential. Manufacturers, raw material suppliers, disposers and recyclers must work together to create closed-loop systems that enable the environmentally sound disposal and recycling of hygiene products.
Bio-Based Materials Reduce Carbon Footprint
Bio-based materials are becoming increasingly important in the manufacture of hygiene products to minimize the environmental footprint and at the same time meet consumer demand for sustainable products. These materials, which are derived from renewable resources, offer a sustainable alternative to conventional raw materials based on fossil fuels. Henkel is a pioneer in the development and implementation of bio-based solutions with its Technomelt® DM ECO products. These adhesives consist of more than 60 percent bio-based materials. In addition to the reduction of CO2 emissions in the manufacturing process, the compatibility of these adhesives with bio-based substrates is another decisive factor. Technomelt DM ECO adhesives offer optimum adhesion to a wide range of bio-based materials, making them a key component in the manufacture of sustainable hygiene products.
Another innovation is Henkel’s Technomelt DM COOL series. These adhesives have been specially developed for use at lower temperatures and are therefore particularly suitable for use with bio-based films, which can be sensitive to the higher temperatures of conventional hot melts. The lower application temperatures reduce the risk of damage to the bio-based films, contributing to longer life and higher quality of the end product. At the same time, they enable significant energy savings due to their lower application temperature, which in turn reduces the carbon footprint of production.
Improving Production Efficiency for Greater Sustainability
As well as having a positive impact on product quality and sustainability, adhesives can also help to optimize production processes in the absorbent hygiene products industry. The focus is on energy consumption and waste generation. Henkel’s Easyflow® system uses micro-chubs in a non-sticky, free-flowing form that are automatically fed into melters. They remain in solid form until needed. This “melt-on-demand” functionality allows the adhesive to be melted precisely as needed. This results in energy savings of about 23 percent compared to manual replenishment. There is no need to keep the adhesive at a high temperature all the time, and employees do not have to constantly open the tank lid, preventing colder ambient air from entering the melting system. This results in lower operating costs and a reduced carbon footprint.
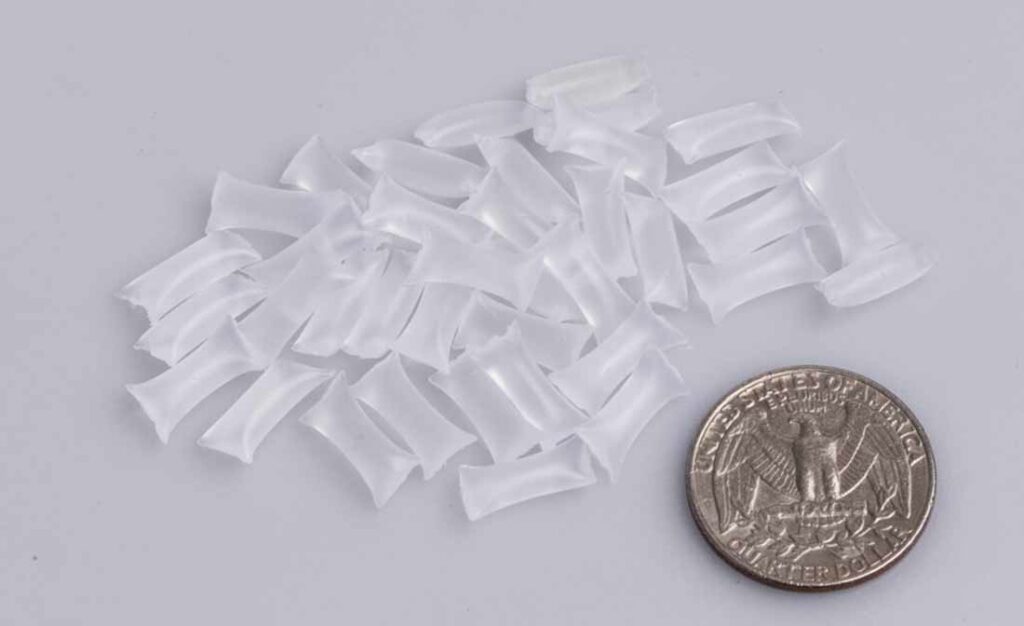
In addition, the closed system helps prevent contamination and foreign matter from entering the adhesive. This significantly reduces problems such as clogged nozzles and filters that would otherwise require frequent maintenance. The resulting increase in production efficiency and product quality reduces waste by up to 40 percent, significantly reducing material loss. Another advantage of the Easyflow system over conventional technologies is the increased yield of olefin-based adhesives. This increase in efficiency reduces adhesive consumption by about 15 percent compared to rubber-based products. In addition, the ability to deliver the adhesive in large, recyclable big bags instead of individual cartons results in a significant reduction in packaging waste.
End-of-life Management – Sustainable Beyond Use
Another important aspect of sustainability in the hygiene industry is the handling of products at the end of their life cycle, known as end-of-life management. The disposal of hygiene products can have a significant impact on the environment, especially if they are not biodegradable or contain harmful chemicals. For example, according to Science of The Total Environment, 12 billion pads and seven billion tampons are discarded each year in the United States.
A key element in this process is compostable adhesives, such as those offered by Henkel with Technomelt DM RE. These products not only meet the high performance and safety requirements for the manufacture and use of hygiene articles, but also the compostability requirements of ASTM 6400, the standard specification for labeling plastic materials that are aerobically composted in municipal and industrial facilities. With a bio-based content of over 64 percent, these adhesives not only help reduce the use of fossil resources, but also allow the end products to be composted after use, returning them to the natural cycle.
To achieve greater sustainability, cross-industry collaboration along the value chain is essential. Manufacturers, raw material suppliers, disposers and recyclers must work together to create closed-loop systems that enable the environmentally sound disposal and recycling of hygiene products. This collaboration is critical to developing effective collection and recycling processes that recover valuable materials and reduce waste. Through continued dialogue and collaboration between all stakeholders, the end-of-life management of hygiene products can be significantly improved, ultimately reducing the environmental footprint and promoting a more sustainable and responsible industry.
Conclusion
The absorbent hygiene industry faces the challenge of reconciling growing consumer demand for sustainable products with the need for sustainable production. Innovative adhesive technologies, especially bio-based and compostable adhesives such as Henkel’s Technomelt DM ECO and DM RE, are leading the way. They not only provide an effective response to environmental and economic demands, but also make a significant contribution to reducing the carbon footprint and conserving natural resources. By integrating these sustainable adhesive solutions, manufacturers can improve the entire lifecycle of their products, from manufacturing to disposal.
Critical to the success of these efforts is industry-wide collaboration along the value chain to ensure sustainable development from product conception to end-of-life management. By embracing advanced adhesive technologies and promoting a circular economy, the industry is moving toward a more sustainable future that both meets the needs of consumers and protects the environment.