Not so long ago, sustainability was the buzzword in the fiber industry with several companies announcing progress in terms of recycling or using bio-based alternatives. The hope is that the coronavirus crisis will provide the catalyst for developing more sustainable supply chains going forward.
The COVID-19 pandemic has forced fashion retailers to drastically reduce costs and shift priorities; many orders have been cancelled, which has largely hit developing countries. The concern is that recent sustainability initiatives could be shelved as revenues plummet and profits are slashed, with workers laid off and supply chains collapsing.
However, some analysts remain positive, making the case that the current retail hiatus offers an opportunity for the fashion industry to re-evaluate its products and processes to enhance efficiency, thus driving sustainability and environmental improvements in the long term. Reliance on a lengthy and geographically diverse supply chain could also be reassessed, with brands bringing production closer to home.
Fashion threatens the planet
The fashion industry is one of the world’s biggest polluters, contributing some 10% of global greenhouse gas emissions owing to its long supply chains and energy-intensive production processes; it is also estimated to produce around 20% of the world’s wastewater.
Further, with apparel production doubling every 10-15 years, the average consumer buying 60% more garments compared with 15 years ago, and each item being kept half as long, more than 80% of clothing is destined for landfill or incineration after an increasingly short period of use. In addition, less than 1% clothing is currently recycled to produce new items, resulting in a loss of more than US$100 billion worth of materials each year.
Environmental challenge
With the continuing rise of fast fashion and the ongoing demand for fiber-based products, producing more sustainably sourced raw materials is key to reducing the fiber industry’s environmental impacts.
In its 2017 report, A New Textiles Economy, the Ellen MacArthur Foundation cited making more effective use of resources and moving to renewable inputs as one of four core ambitions to achieve the vision of a new global textile system.
But while the major brands remain tight-lipped in the short term about their future sustainability commitments (undoubtedly with more pressing problems to overcome), many research institutes and technology startups are tackling the fiber industry’s environmental challenges.
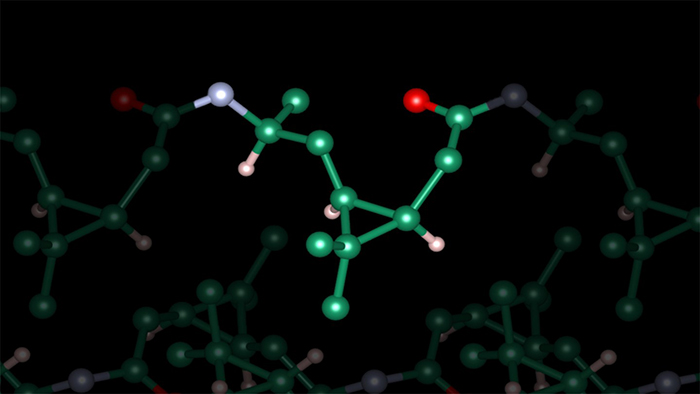
Polyamide alternative
Polyamide (PA), the first totally synthetic fiber to be made into consumer products including apparel and carpet, was developed by DuPont more than 80 years ago. It is thought to be responsible for an estimated 60 million tonnes of greenhouse gas emissions a year through traditional production that begins with crude oil.
Until now, there have been just a few “green” alternatives to crude-oil based PAs, such as PA 6.10, PA 10 and PA 11 produced from castor oil plant (Ricinus communis) seeds.
Researchers from the Fraunhofer Institute for Interfacial Engineering and Biotechnology (IGB) in Straubing and the Technical University of Munich (TUM), Germany, have now developed a new family of PAs from a byproduct of cellulose production that offer new and improved functionalities.
The new PA is based on 3-carene, which comprises two rings fused to one another. The chemists at TUM and IGB modified one of the rings such that it can be opened up, producing a polymer, while the second ring remains intact.
Instead of a linear polymer chain, as in traditional PAs, the resulting chain can bear many small rings and other side groups, giving the polymer completely new functions. For example, they melt at higher temperatures than crude oil-derived PAs. In addition, the new compounds can be produced transparently as well as in a partially crystalline manner.
The researchers say 3-carene can be distilled at a high purity and comparatively low cost from the turpentine oil produced as a byproduct of the forestry industry, which does not compete with food production, unlike the use of castor oil as a starting material.
Renewably sourced polyamide
Meanwhile, California, USA-based Genomatica and Italy’s Aquafil have produced the first tonne of 100% renewably sourced PA from plants. The technology is based on fermentation: Genomatica engineered a microorganism and production process that ferments the sugars found in plants to make the chemical intermediate for PA 6, which is then converted into PA 6 polymer chips and yarn by Aquafil in Slovenia.
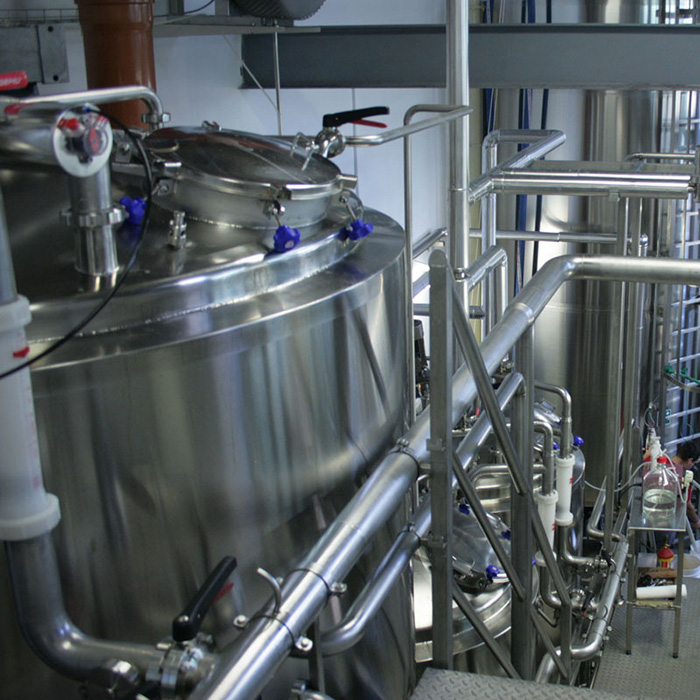
Genomatica’s bio-based nylon has the potential to reduce greenhouse gas emissions in a US$10 billion global industry that produces more than 5 million tonnes of PA per year, to make carpet, clothing, vehicle interiors, engineered plastics and food packaging.
Aquafil and Genomatica have also announced a multi-year agreement to create sustainable caprolactam, a key ingredient to producing 100% sustainable PA. The collaboration aims to develop Genomatica’s GENO CPL process to make caprolactam using plant-based renewable ingredients, rather than crude oil-derived materials.
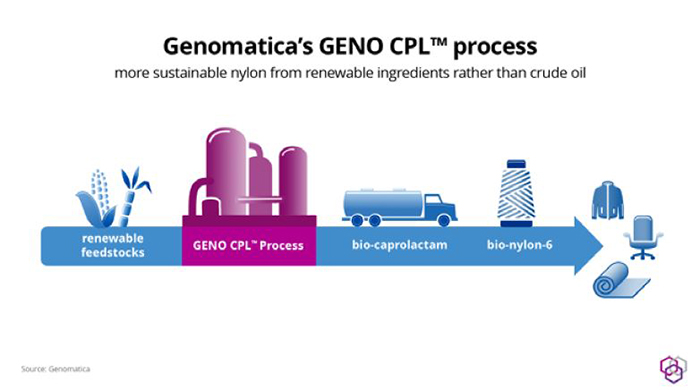
Take-back program
In another development, Aquafil has been producing Econyl PA made primarily from recycled nylon carpets and fishing nets, which is said to reduce the global warming impact of PA by up to 80% compared with PA made from oil.
The company is now partnering with brands such as Napapijri (an Italian premium casualwear brand owned by VF Corp) in a take-back and recycling program. After a minimum of two years after purchase, to ensure adequate use, customers can return jackets to Napapijri, which are then recycled into Econyl PA; customers receive a voucher to purchase a new jacket made from recycled material.
Bio-based Dyneema
As part of plans to source at least 60% of its feedstock from bio-based raw material by 2030, bio-based Dyneema, an ultra-high molecular weight polyethylene fiber, is now available from DSM.
UPM Biofuels supplies the bio-based feedstock – UPM BioVerno, a 100% renewable naphtha from the residue of the wood pulping process, which is then processed by SABIC to make renewable ethylene.
DSM applies a “mass-balancing” approach to create the bio-based Dyneema fiber that is said to be identical to its conventional counterpart at the molecular level. The new bio-based material will carry the ISCC Plus certification and will not require re-qualification of downstream products.
Bio-synthetic benefits
At February’s Texworld Paris event, Céleste Lilore, director of industry engagement for Textile Exchange, a non-profit organization focused on accelerating sustainability in the textile value chain, made the case for synthetic fibers as a key part of the whole sustainability movement.
Bio-synthetics and recycled plastics are increasingly being used as sustainable resources. Demand for bio-synthetics – polymers based on renewable resources rather than fossil fuels– is expected to double by 2050, while the market share of recycled polyester – the world’s mostly widely used fiber with a market share of more than 50% – increased from 8% in 2007 to 14% in 2017 and continues to rise. Recycled polyester also uses 30-50% less energy to produce than conventionally produced polyester.
Although several brands are already using recycled textiles on a limited scale, most are not sourcing post-consumer textile waste. The fashion industry’s current focus on achieving recycled-content targets is mainly centered on using recycled post-industrial textile inputs.
Most recycled materials used in clothing are not recycled from textiles, but from plastic bottles or nylon fishing nets. While this is good news for the environment, particularly the world’s oceans, this solves waste problems in other industries, not in textiles and fashion.
Chemical recycling
Traditional mechanical textile recycling processes tend to degrade fiber quality, resulting in lower-value potential end-uses or a requirement to mix recycled fibers with virgin fibers.
Chemical garment recycling technologies are now being developed by several companies and research institutes using chemical solvents to break down used clothing into virgin-quality fibers. The solvents can often be reused continuously.
Re:newcell of Sweden, for example, has developed a process that uses chemical solvents to dissolve fabrics such as cotton and viscose to create Circulose pulp, which can be extruded into new fibers and spun into yarn.
However, much of this technology is still at the research and development and pilot stages. Barriers to its large-scale adoption include finding reliable material sources, the need to collect, sort and prepare the materials prior to recycling, and the high capital required to build large processing plants, as well as the energy needed to recycle textiles.
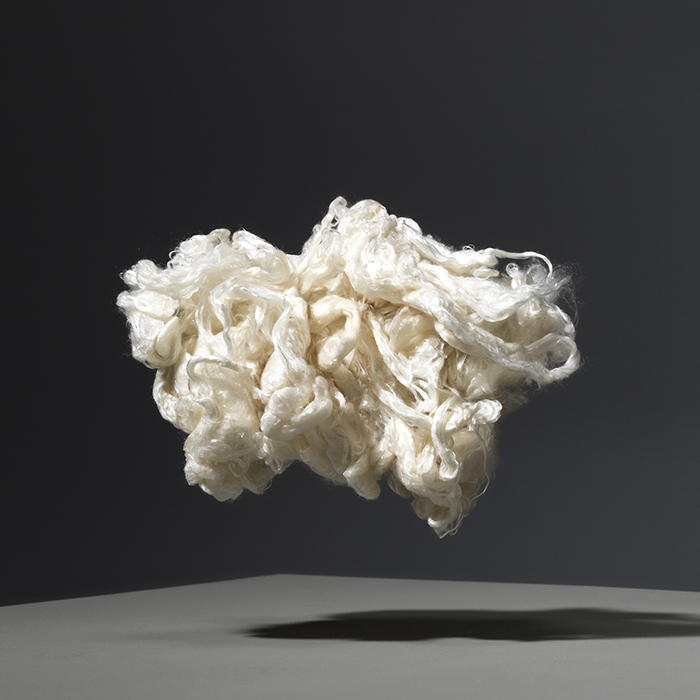
NIR-based sorting technology
A Netherlands-based consortium including textile collectors, sorters and recyclers is ready to commercialize a near infrared-based technology to process non-reusable textiles into feedstock for textile recycling.
Fibersort works by categorizing textiles into different fractions (currently 45 in total) based on fiber composition and color, and can sort around 900 kg of post-consumer textiles per hour.
Over the past few years, the technology has been optimized, tested and validated to prepare it for commercialization, according to project partner Circle Economy. Sorted materials are now commercially available for other organizations to test their potential for textile-to-textile recycling.
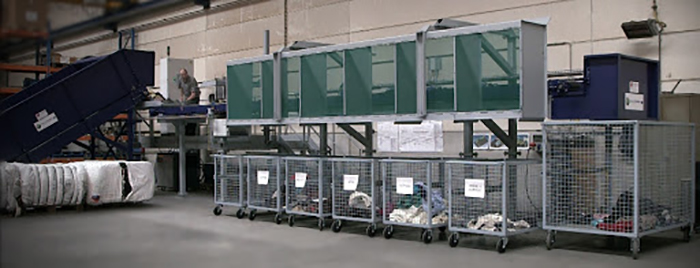
Investors in recycling
Tyton BioSciences has received US$8 million from four firms investing in its recycling technology that transforms used textiles into pulp and polyester monomers for fiber and yarn producers to make new yarn.
The U.S.-based company separates polyester and cotton from discarded clothing using a hydro-thermal process, in which the polyester is broken down into its raw materials and the cotton is broken down into pulp to be made into various cellulosic fibers.
The investors include Tin Shed Ventures (the investment arm of the outdoor apparel brand Patagonia), Marubeni Americas, Card Sound Capital and Alante Capital.
Meanwhile, the H&M Foundation is investing almost €6 million in the Hong Kong Research Institute of Textiles and Apparel (HKRITA), a research facility that is developing separation and recycling solutions for blended fabrics.
HKRITA has already developed a method for recycling textiles that uses water, heat and chemical solvents, and in September 2018 opened a pre-industrial scale facility in Hong Kong using the technology, which the institute is looking to license.
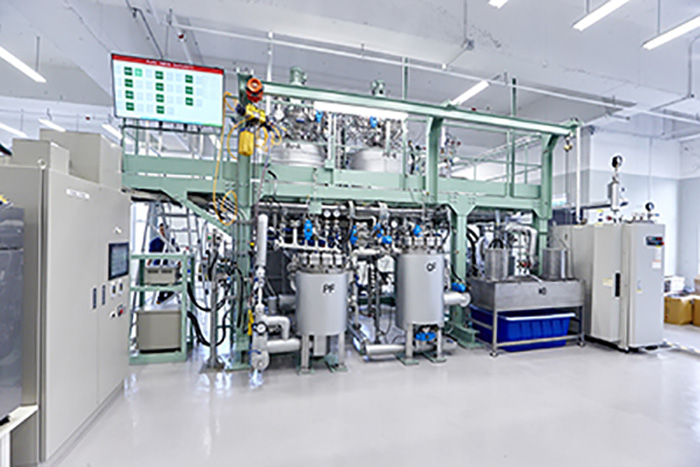
Fabrics from recycled ocean plastic
In the sportswear sector, Adidas is to launch new fabrics made from recycled polyester and marine plastic waste following its success with the Parley for the Oceans initiative.
The European sportswear manufacturer first partnered with the scheme in 2015 and gradually increased production of shoes using marine plastic waste to make more than 11 million pairs in 2019, although still only a fraction of the group’s total of over 400 million pairs.
Adidas will continue to make Parley-branded shoes and clothing from ocean-sourced plastic in 2020 and will also launch Primeblue fabric containing Parley marine waste that it will use in existing ranges. In total, the German firm will produce 15-20 million pairs of shoes using ocean plastic in 2020.
Adidas says it wants more than half of the polyester it uses to be recycled in 2020, increasing to 100% by 2024. In addition to the ocean plastic initiative, the company will start labeling products made from 100% recycled polyester from other sources as Primegreen later this year.
Recycled upholstery fabric
Beaulieu International Group’s Tessutica business has developed a range of upholstery fabrics made from pellets that come from marine plastic waste. After use the new Greencare fabrics can then be fully recycled back into pellets.
The recycled and recyclable upholstery fabrics are certified under the Global Recycle Standard label, and are made with recycled yarns from regular post-consumer polyethylene terephthalate bottles from the oceans and landfills and upcycled cotton from garments. The fabrics are produced as part of the Seaqual project, which brings plastic waste back into the manufacturing chain.
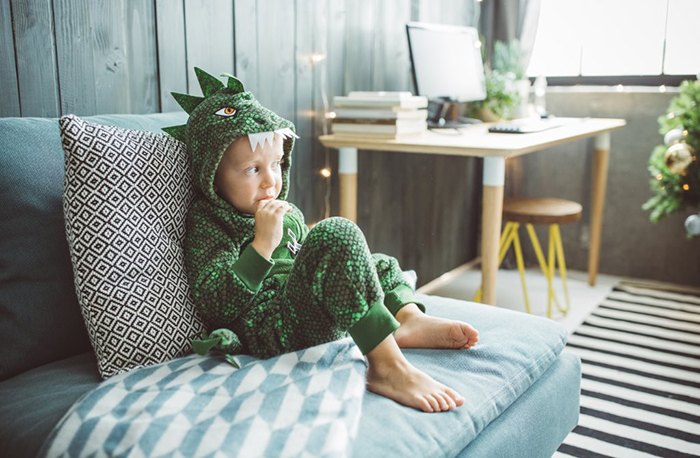
Recycled viscose
China-based Sateri, part of Royal Golden Eagle (RGE), is now producing viscose fiber from textile waste on a 35,000 tonnes/year commercial production line.
The fiber comprises a mixture of dissolving pulp made using recycled post-consumer textile waste from Södra of Sweden and wood pulp certified by the Programme for the Endorsement of Forest Certification.
Trialed at Sateri’s Linz Nanjing yarn spinning mill using Siro compact and vortex systems, the new fiber has been shown to be compatible with existing spinning technologies, with no adjustments to existing processes or parameters required. Further, the fiber is said to have good spinning efficiency, yielding even yarns that exhibit good tenacity.
The cotton is derived from Södra’s OnceMore process for separating cotton from polyester/cotton blends. The resulting cotton fibers are then added to its wood-derived textile pulp.
In August 2019, RGE invested in Finnish start-up Infinited Fiber to scale up its technology for recycling cotton-rich textile waste and other pulp-based materials into cellulosic fibers. A 500-tonnes/year pre-commercial plant in Finland and customer training center is due to open in 2020.
Earlier, a memorandum of understanding was signed with Re:newcell for technical cooperation and production trials of viscose using recycled cotton, with the aim of industrial-scale production by 2025.
Then in October 2019, RGE announced a US$200 million investment over the next 10 years to support research into alternative cellulose or plant-based feedstock and closed-loop manufacturing.
Sateri is now working with several dissolving pulp producers on various novel technologies in the drive towards a circular bio-economy. It will be partnering with spinners, clothing manufacturers and fashion brands to launch the recycled viscose fiber later this year.
First garments from eco-collaboration
Finnish companies Marimekko and Spinnova have launched the first apparel products using new sustainable materials from a collaboration on wood-based textiles that started in 2017.
The prototype outfits made of “transformational sustainable fabrics” include a denim-like jacket and bag as well as a striped jersey top. Both the woven and the jersey fabric are made of Spinnova fiber mixed with cotton and/or lyocell.
According to Spinnova, the new technology means that wood pulp can be spun into a textile fiber without regenerating, dissolving or using harmful chemicals, which makes it less environmentally harmful than viscose or cotton production. Additionally, 99% less water is used than in cotton production. Post-consumer, the fabric is said to biodegrade quickly.
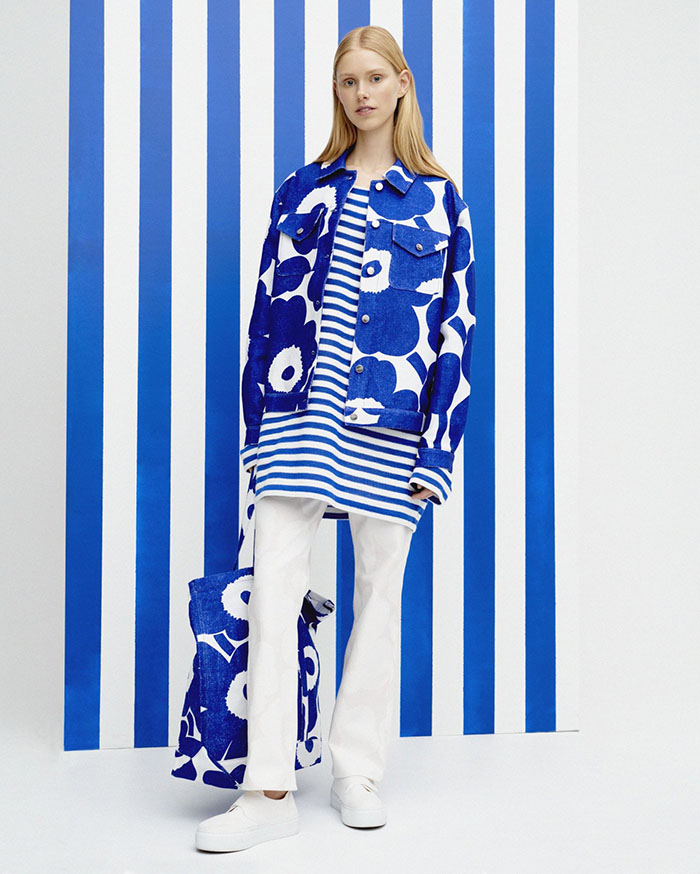
Sustainable goals
Mango aims to use 100% sustainably sourced cotton in its clothing by 2025 and will increase the use of recycled polyester in its garments to 50% by that date. The Spanish fashion company also plans to increase the proportion of other sustainable fibers in its production within the next five years and that 100% of the cellulosic fibers it uses will be from “controlled sources” by 2030. In 2019, the company produced 18 million garments with sustainable characteristics, twice the rate of the previous year.
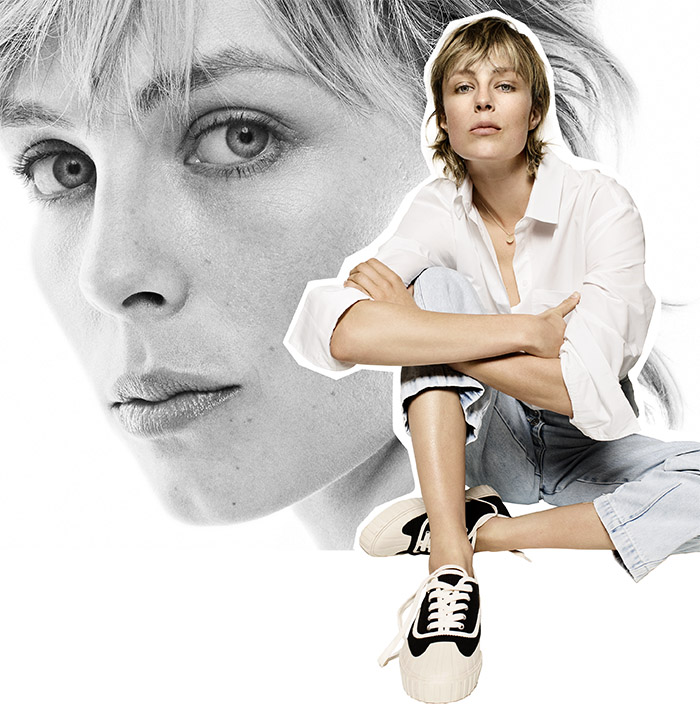