Textile Innovation Emerges from Industry Gatherings as the Stars of the Show
In the past year, startup companies have been gaining valuable exposure at textile industry exhibitions and conferences, showcasing fiber alternatives along with digital tools and concepts behind a rapidly expanding arsenal of new technologies and services.
For example, at the major ITMA 2023 textile exhibition in Milan, Italy, in June, hosted a special Start-Up Valley display area featured the work of 16 new companies, while at the Dornbirn Global Fiber Conference (GFC) in Austria in September, some 25 companies took part in the 3rd Innovation Days side event.
A further 17 startups together comprised the special Innovation Zone at the Performance Days functional fabrics fair held at Messe Munich in Germany in October, while six companies received Startup Awards at the annual conference of the Swiss-based International Textile Manufacturers Federation (ITMF) held in Keqiao, China in November. INDA’s RISE conference in September at North Carolina State University, meanwhile is completely dedicated to the NextGen materials under development for the nonwovens industry.
With so many new developments going on, it’s difficult to predict which ones will have a significant impact. Here, we attempt to highlight some we believe have the staying power to effect change.
Rubi Laboratories
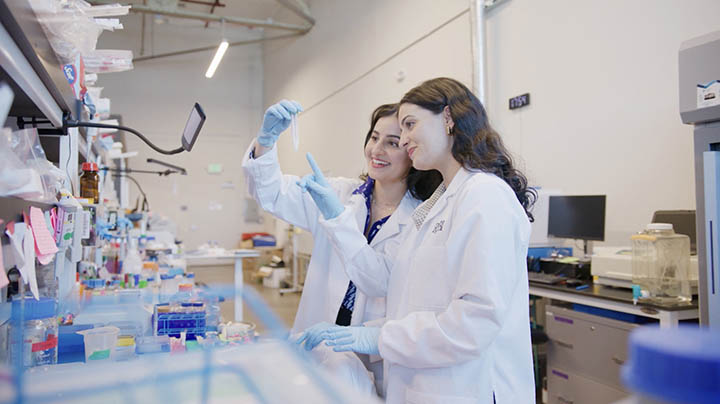
Following its participation in the Fashion for Good Global Innovation Program in 2022, California startup Rubi Laboratories has certainly been attracting a lot of attention on the fibers front. Rubi is employing synthetic biology to make new cellulosic fibers from carbon waste emissions via a patent-pending fully enzymatic process.
Having already gained the strong support of a number of major brands including H&M and Patagonia, in June 2023 Rubi unveiled the first-ever cellulosic yarn that is carbon-negative, water and land-neutral, naturally biodegradable and made directly from carbon emissions. A month later, the company announced that it was involved in trials for garment prototypes with retail giant Walmart.
Walmart’s EVP of sourcing Andrea Albright is particularly enthusiastic about the potential. “When I toured the Rubi facility, I got to see the carbon capture process first-hand and it felt like magic – this creation of something seemingly out of thin air,” she said. “Rubi founders Neeka and Leila Mashouf have taken inspiration from how trees ‘eat’ CO2 to create the cellulose and have figured out a way to mimic this natural process in the lab. The process – like trees – captures and converts carbon emissions and turns them into a new cellulose raw material.”
Work is now underway to explore how Rubi’s technology can be integrated at a larger scale in the Walmart supply chain, with the aim of major apparel collections appearing in stores at some point in the future.
LanzaTech
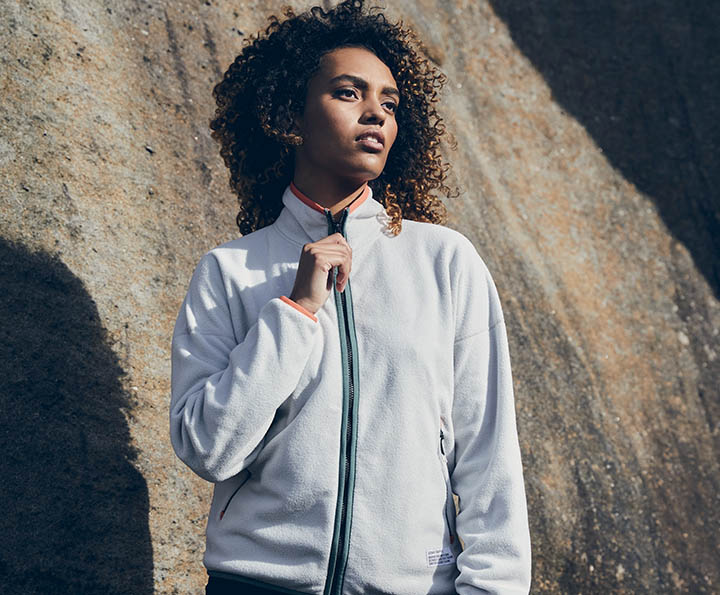
Already some way down this road, is LanzaTech, which began as a New Zealand startup back in 2014, has subsequently grown rapidly and is now headquartered in Skokie, Illinois.
The company is developing alternatives to synthetic polyester fibers, rather than cellulosics, and employs a combination of biotechnology, artificial intelligence and innovations in mechanical and chemical engineering to manufacture chemicals. Its process recycles waste carbon into sustainable versions of raw materials such as ethanol, which is a building block for many other chemicals including polyethylene and monoethylene glycol (MEG). MEG is a key ingredient in the manufacture of PET polyester. With the company’s technology, ethanol from pollution can be converted into the material needed to make textiles that would otherwise be made by extracting virgin fossil carbon.
LanzaTech has partnered with petrochemical company India Glycols Limited (IGL), a global leader in ethanol to glycol production, to convert its CarbonSmart Ethanol into MEG, and Far Eastern New Century of Taiwan to use the MEG in PET fibers production.
During 2023, outdoor brand Craghoppers has launched its new CO2Renu sustainable fleece collection comprised of 30% LanzaTech recycled carbon-derived PET and 70% PET from recycled plastic bottles. It is now available both online and in stores.
LanzaTech has also partnered with Swiss sportswear brand On this year, for the Pace Collection, based on a new polyester material called CleanCloud which also incorporates the MEG monomer made from captured carbon emissions.
“Yesterday’s emissions are today’s apparel,” said LanzaTech CEO Jennifer Holmgren. “There is enough carbon above ground to make nearly everything we need. We are proud to be enabling the circular
carbon economy by creating an eco-system of like-minded partners such as Crag-hoppers and On.”
naNea
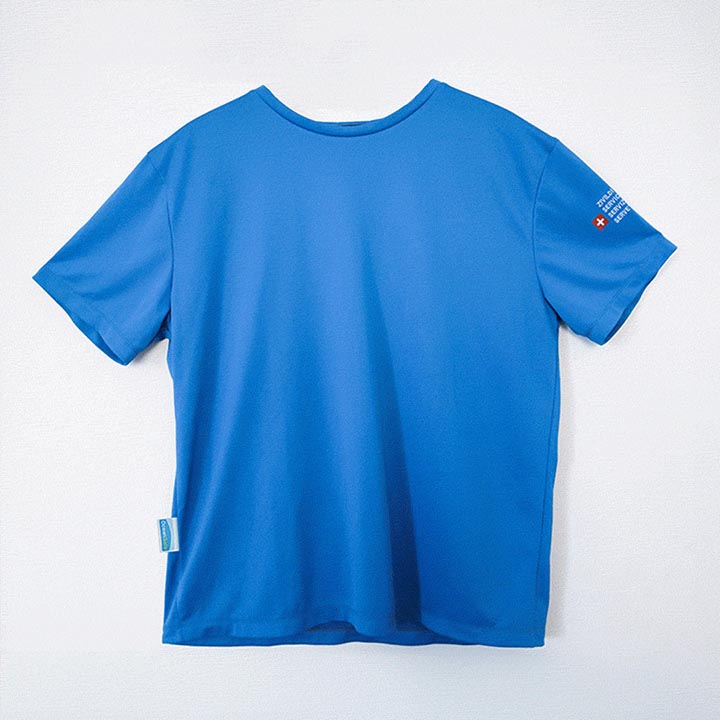
Still on the subject of new polyesters, OceanSafe, based in Berne, Switzerland, is another startup which has been making a notable impact in 2023.
The company’s naNea, while still itself a synthetic, is a next generation replacement for PET polymer that at the same time is inherently biodegradable in water, soil and landfill. In ocean water, 93% of it will biodegrade in just 99 days. It is the first and only synthetic material to date to have received the stringent Cradle-to-Cradle Gold certification.
The polymer is already being turned into fibers and yarns that have all the favorable processing and performance properties of PET polyester, yet are circular, biodegradable, compostable and toxin-free.
According to marketing manager Matthias Fuchs, naNea products are high performing, durable and highly scalable, and as volumes go up, the price will only come down.
“The polymer is a drop-in solution for polyester manufacturers and fibers and yarns made from it can be fully woven or knitted and dyed and finished conventionally,” he said.
In November, OceanSafe claimed the 2023 Design Prize Switzerland in the Circular Design category for the Dual-Circuit t-shirt, developed in collaboration with ZIVI, the Swiss Federal Office for the Civil Service.
The t-shirt meets all of ZIVI’s requirements for durability, performance and comfort in wear and professional care and will be supplied to ZIVI workers in 2024. OceanSafe and ZIVI are now collaborating on a national take-back system and the establishment of advanced processes to allow for complete depolymerization at end of life, extracting all essential raw materials to produce new textiles of
the same quality.
CiCLO
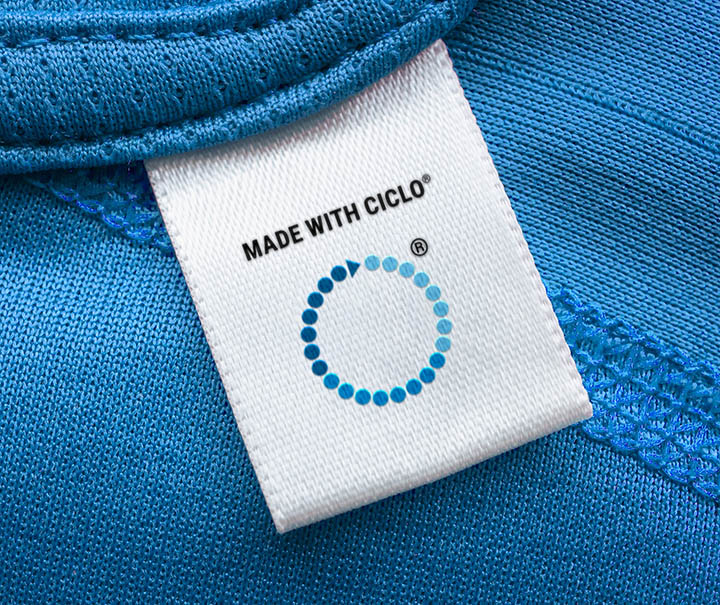
An extremely important introduction to the fibers market, which, while it can’t do anything about the plastic microfibers already in the oceans, can ensure future synthetic fibers such as polyester and
nylon do much less damage, is CiCLO, developed by Silicon Valley startup Intrinsic Advanced Materials.
CiCLO is a sustainable additive that is combined with polyester and nylon during melt extrusion. It creates countless biodegradable spots in the matrix of the plastic, where microbes that naturally exist in certain environments can break down the materials just like they do with natural fibers. What remains are natural biogases and biomass.
In partnership with Parkdale Mills, Intrinsic has now established a network of 45 certified fiber and yarn manufacturers to ensure quality assurance and traceability in the supply of CiCLO.
There is really no reason why any manufacturer of conventional synthetic fibers should not now be incorporating it into their production.
Rheon
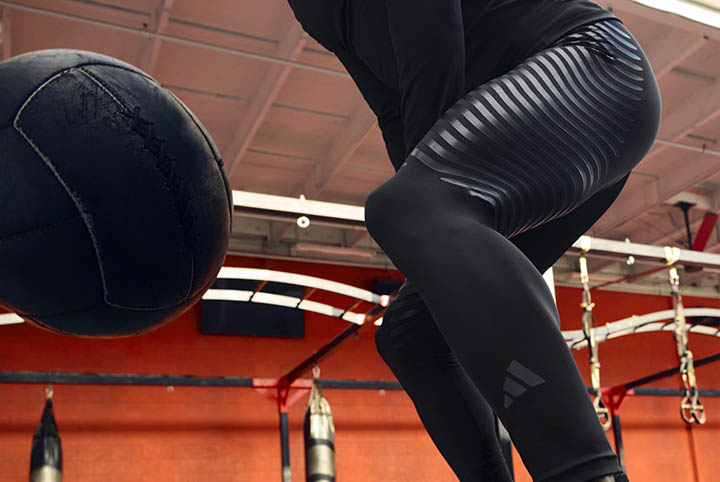
As a rare example these day of a new material developed for its performance properties rather than sustainable benefits, Rheon by Rheon Labs is a reactive superpolymer with a number of potentially major applications, as a naturally soft and flexible material that when subject to force exhibits instant stiffness.
In its construction, the thermoplastic elastomer composite is a chemical colloidal suspension bringing together two very different ingredients to create new properties. The effect can be likened to sand and water, in the way that when walked on, a wet beach is very soft, but when running, it becomes glass-hard.
As such, Rheon enables the creation of new garments that can react dynamically to the body’s movement, to provide support exactly where and when needed, and the faster the body moves, the more the technology engages.
Rheon Labs, a 2017 spin-out from Imperial College London, envisages three key uses for the new material – in applications for muscle support or simply to enable athletes to run faster, in garments designed for injury prevention, and as soft tissue support in a new generation of sports bras.
Historically, the support provided by bras has been associated with high compression, but also discomfort. Bras reinforced with Rheon work in a fundamentally different way to provide support
and comfort by dramatically reducing the breast tissue displacement that occurs during movement. On a systems level, Rheon can absorb four times more energy than standard thermoplastic elastomers (TPEs).
Rheon also promises to enhance elite sports performance, where the difference between winning and losing can be down to a matter of seconds, or even less.
The company has been working with the University of Wisconsin on the concept of “muscle shearing,” aimed at reducing wasted energy to boost performance. This work has involved wrapping straps of Rheon around the essential muscle groups – primarily the quads and hamstrings – and analyzing the micro-movements of a runner going through the gait cycle in order to create a dynamic support system.
The idea is to turbocharge properties through a data-driven system based on the collection of muscle movement data in combination with that relating to soft tissue density and bone structure.
This concept has now been taken up by Adidas, with Rheon support structures to be found in two of the brand’s releases during 2023 – Adizero Control sleeves and shorts for running and Techfit Control long-sleeved tops and pants for training.
Colorifix
In other areas of the textile chain, Colorifix, the developer of a unique fabric-dyeing process based in Norwich, UK, was the recipient of a 2023 ITMF Innovation Award and was also a finalist in this year’s Earthshot Prize, narrowly missing out on the £1 million winning prize.
The Colorifix process uses the DNA codes for colors found in nature and teaches microbes to recreate them as natural dyes. It begins with identifying a color created naturally by an animal, plant or microbe and then, using DNA sequencing, identifying where the color is coded in the genetics of the organism. The DNA code is translated into engineered microorganisms enabling Colorfix to produce the pigment just as it is made in nature and transfer it to fabrics.
The idea originated from the work of founders Jim Ajioka, and Orr Yarkoni on the development of tools for molecular genome analysis at Cambridge University. While testing a biosensor for assessing the arsenic contamination of drinking water in Nepal, the two learned about the enormously destructive impact of dyeing processes on water. Together they realized that instead of just monitoring contamination, they could devise a solution – a sustainable way to dye textiles using synthetic biology.
Colorifix natural dyes cut chemical pollution by 80%, and when applied to fabrics require far fewer rinses than synthetic dyes, ultimately saving vast quantities of water. Already gaining traction in the fashion industry, Colorifix has ambitions to dye 15% of the world’s clothes by 2030, helping big manufacturers make good on their sustainability targets.
The company has secured £18 million in investment to support expansion further into Europe and Asia and implement its technology into the supply chains of several leading players in the global fashion industry.
Velum
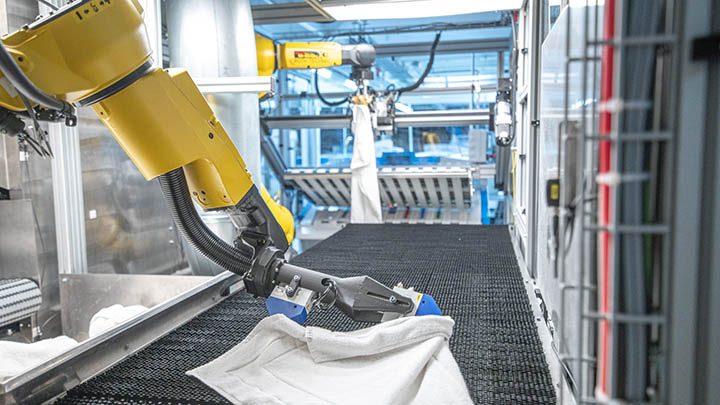
Finally, to the industrial laundry. Sewts introduced Velum, its artificial intelligence and computer vision software, developed to automate currently labor-intensive processes in laundries, at the ITMA 2023 Start-up Valley.
A first Velum unit has been operational at Greif Textile Mietsysteme in Wolfratshausen, Germany, since November 2022. Greif provides a rental laundry service via a network of ten plants throughout Germany, each processing up to 100 tons of textiles per day, making them some of the largest laundries in Europe. As such it is an ideal partner for the first-time use of robotics in this market.
A significant number of further Velum systems are about to become operational and Sewts is addressing a target group of almost 25,000 companies worldwide.
Velum currently processes an average of 500-600 items per hour and through over-the-air software updates, its range of functions is continuously being expanded.
Industrial laundries wash and dry textiles in a highly automated environment to cope with the large quantities of dirty linen, but still require manual work for a few gaps in the automation chain. Most notably, each folding machine requires an employee to feed the laundry and spread it out without any wrinkles.
It has been estimated that 30% of the personnel costs in laundries is accounted for by equipping folding
machines and at the same time, labor shortages are one of the most pressing issues of our time and especially prevalent in tasks that involve repetitive manual work. The Sewts Velum system has been designed to provide a solution, feeding towels and other terrycloth items into folding machines to close the gap. Inhouse developed AI analyses the textile and translates these findings into robotic commands. Velum is optimized for adaptability and handles all towel sizes without restrictions in respect of color or texture.
“With Velum, we have succeeded in launching an absolutely new kind of product,” said Alexander Bley, co-founder and CEO of the Munich-based company. “Since 2019, we have been working on technology for the automated processing of deformable materials, such as textiles or foils. These have so far been excluded from progress in automation technology due to their complex material properties. Velum is now proving that it is possible to automate the handling of shape-unstable materials in industrial processes in an economically profitable way.”