Radial quenching systems such as the EvoQuench create an even, turbulence-free airflow and therefore guarantee gentle yarn handling and even quenching. This makes it the perfect system for microfiber spinning.
Even in the case of the last five-year plan by the Chinese government, the focus was on sustainable and innovative technologies. Only systems that promise technological and ecological value-added are approved for import. And the same applies to the provision of loans. With this, the highest-capacity market for manmade fiber manufacturing has set an extremely high standard for spinning technologies.
The decommissioning of numerous dye works in China no longer complying with ecological standards increased the demand for spin-dyeing solutions. The most important benefits of spin dyeing lie in the evenness of the dyeing results and in the ecologically considerably cleaner process.
Spin-dyeing – the clean solution
Energy efficiency and CO2 emissions are important factors for the filament yarn spin-dyeing process using the Oerlikon Barmag 3DD: to this end, a piece dyeing process requires around 30 times as much energy as the master batch dyeing process, while also emitting approx. 30 times more CO2. Furthermore, the spin-dyeing process uses no water and hence creates no corresponding wastewater whatsoever.
In addition to this, master batch dyeing results are also more even, which is why textiles dyed using this method are preferred in the particularly critical automotive sector as well. The only disadvantage: the flexibility with regards to the color diversity is not as great as in the case of piece dyeing. However, there are also solutions available for this. With the help of additive injection and mixing systems, master batches and additives can be introduced into the melt path at various points between the reactor and the spinning positions. Thus, the variety of yarn to be simultaneously manufactured can be increased dramatically.
EvoQuench – the core component when spinning microfibers
Microfilament yarns are yarns with filament titers of less than 1 dpf. Those with individual filaments of less than 0.5 dpf are described as super-microfilament yarns. Conventional melt spinning processes currently permit process-reliable and simultaneously efficient filament titers of down to 0.3 dpf.
The spinning system determines the quality of the microfilaments. Here, it is above all the quality of the spinning unit and the quenching unit that plays a decisive role. The shortest possible residence time for the polymers in the spinning beam is also important.
A decisive success factor is even yarn cooling: the thinner the filaments, the more difficult it is to guarantee this. Radial quenching systems such as the EvoQuench create an even, turbulence-free airflow and hence guarantee gentle yarn handling and even quenching. Among other things, this results in excellent uster values, hence extremely even filament yarns. Perfect downstream performance and uniform dye pickup are the benefits.
To this end, the EvoQuench system offers the most innovative quenching technology available. In contrast to standard cross-flow quenching, the air is symmetrically guided from the outside to the inside of the filament bundle. This is particularly successful due to the twin-chamber system used in the EvoQuench: the first chamber carries out the pre-distribution of the air, while the second chamber then generates the optimum uniformity of the air intake from all sides. For this reason, the filaments are particularly evenly cooled along the entire length of the yarn surface.
A further benefit of the EvoQuench is its considerably lower energy consumption: radial quenching consumes 60-80% less process-air than cross-flow quenching. Oerlikon Barmag’s radial quenching units can be used for manufacturing microfilaments and commodity yarns from 0.3 dpf up to 3 dpf. Hence, the component is e-save certified and makes a sustainable contribution towards the ecological balance sheet of the spinning system.
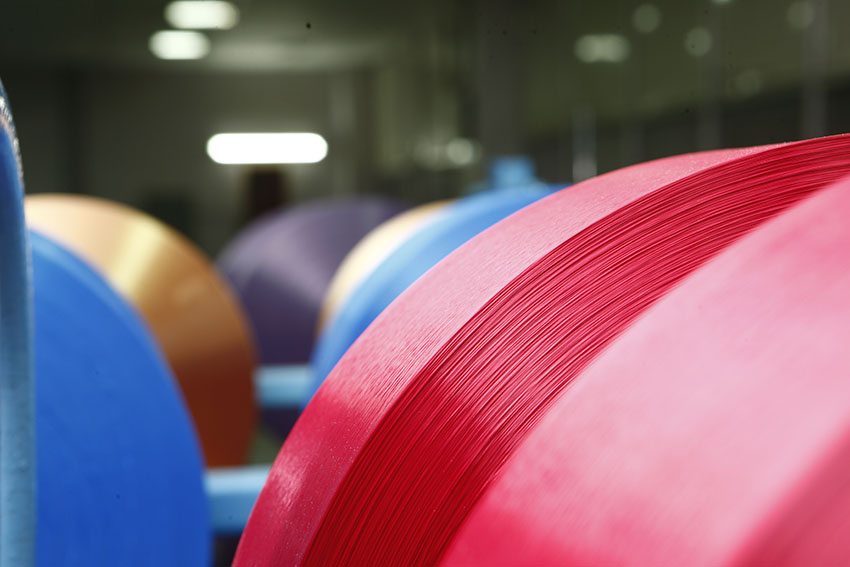
Spin-dyeing with EvoQuench
In the case of spin dyeing polyester POY or FDY using the EvoQuench system, the particular focus lies on the long, stable duration of use for the sieves installed in the EvoQuench. This ensures a highly consistent yarn quality over long production periods and makes a considerable contribution to reducing downtimes and consumption costs.
The dyes deployed in spin dyeing are – with the exception of black – generally azoic dyes or organometallic complexes. These aromatic-based molecule systems can, in part, decompose at the high melt temperatures and evaporate directly underneath the spinneret.
While this evaporation does not result in lower durability and evenness when using a cross-flow quenching system, increased contamination of the sieves could well result in lowering their service life and the evenness of the yarn.
For this reason, the special design for spun-dyed yarn protects the sieves against contamination caused by evaporating dye particles. Important design criteria was easy and fast cleaning during routine pack wipe cycles.
This new development from Oerlikon Barmag now makes spin dyeing polyester POY and FDY possible and efficient under practicable marginal conditions when using the EvoQuench radial quenching systems.