With the Climate and Biodiversity Clocks Ticking, Scandinavian and Nordic Companies are Pioneering Innovation Toward Low-Impact, Circular Textile Production
As fiber producers search for new ways to transition the textile industry away from petroleum-based raw materials, a lot of effort is taking place in Finland.
Geographically a Nordic nation, but culturally Scandinavian, this northern European country with a strong heritage in the forestry and paper industries has, along with neighboring Sweden, been quietly helping to further integrate recycling and to close the loop within the textile industry.
While some clothing and home textile items are reused by family and friends, sold through online marketplaces or in second-hand shops, or donated to charities or non-profit organizations, the vast majority end up as waste and either incinerated or sent or landfill.
Of the textiles that are collected separately, most are exported for sorting and reuse – only a tiny fraction of end-of-life textile waste is fiber-to-fiber recycled, which represents a major loss of materials and resources.
Although as yet there is no organized collection system for recyclables, several initiatives are happening in the Nordic countries, where automated sorting and recycling facilities are beginning to emerge.
At the same time, a number of start-ups across the region have secured major investment capital to demonstrate that recycling textiles can be both achievable and profitable, as well as ethically responsible.
Spinnova’s wood fibers are sourced from sustainably managed forests and are said to require 99.5% less water to produce than traditional cotton.
Spinnova Starts Production
Finland-headquartered sustainable fiber manufacturer Spinnova has announced that its first commercial factory is now in production and that it has already drawn up business plans for a second plant.
Founded in 2015, the company produces fibers from wood and waste, including leather, textiles and food, without the use of harmful chemicals.
Compared with cotton, which requires large amounts of water and pesticides to grow, Spinnova’s wood fibers are sourced from sustainably managed forests and are said to require 99.5% less water to produce than traditional cotton.
Further, Spinnova fibers are 100% biodegradable and compostable, eliminating the need for disposal and therefore reducing the impact on the environment. Moreover, the fibers can be recycled in the production process without any loss of quality.
Spinnova’s first production-scale factory, at Jyväskylä, Finland, was built in partnership with pulp producer Suzano and aims to be making one million tonnes of fiber annually within 10 to 12 years.
Construction of the 2,000-m2 Woodspin joint-venture spinning facility began in June 2022 with an investment of around €2.2 million, with Switzerland-based Rieter chosen as the technology supplier.
The facility will produce yarn made of Spinnova fiber for use in product development projects with brand partners – several high-profile fashion brands are already integrating the fiber into their fabrics.
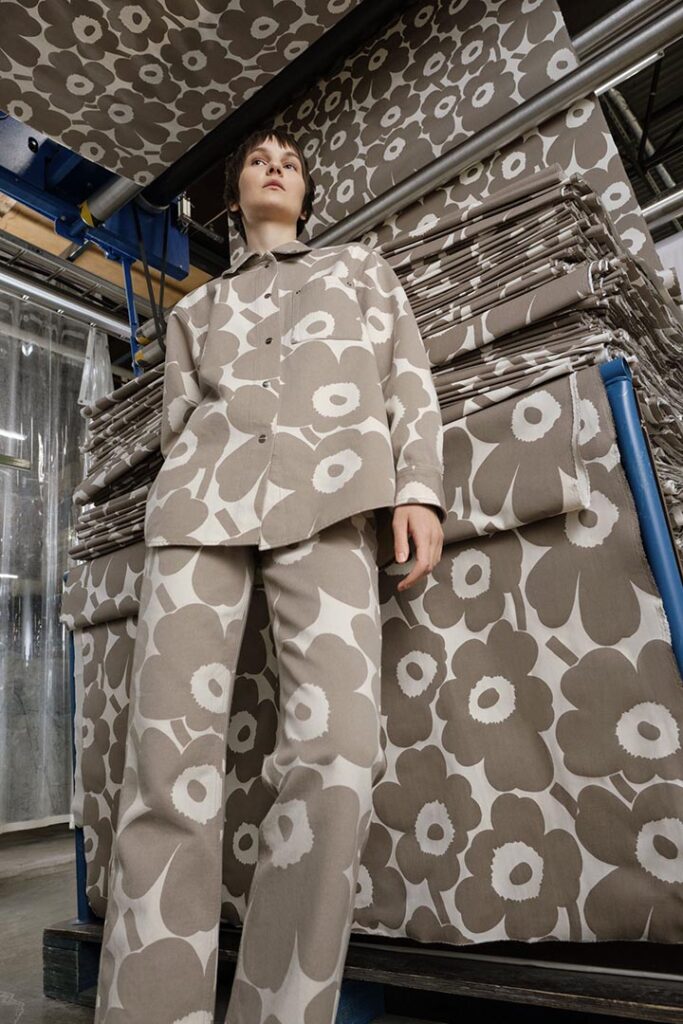
For example, the first commercial product with Adidas – the Adidas Terrex HS1 mid-layer hoodie – was available for consumers online and in select retail outlets from last July.
Marimekko launched a capsule collection of three products made with Spinnova fiber – the first time the fiber was used in a fabric with a printed pattern – while Bestseller’s Jack & Jones brand launched trousers made from a blend of Spinnova fiber and cotton.
With Halti, Spinnova announced the launch of a water-resistant and windproof parka, which is expected to go on sale at retail stores this spring. The parka is dyed with Imogo’s sustainable dyeing technology. In addition, Spinnova has continued its cooperation with The North Face, Bergans and Icebreaker among
others.
The new Woodspin factory started producing fiber in February and production will gradually increase throughout this year. Spinnova’s textile development work is continuing, and the company plans to launch its first products using Suzano micro-fibrillated cellulose (MFC) from wood pulp as the raw material.
The fiber used in the 2022 product launches was produced on Spinnova’s pilot line using MFC from Scandinavia. At the same time, Suzano has been ramping up its own MFC production for the Woodspin factory launch.
Meanwhile, new brownfield and greenfield sites are currently under evaluation and, once further investment is finalized, Spinnova expects that the next Woodspin plant will be completed after 2024.
At the end of 2022, the Respin pilot line built by Spinnova produced fiber from leather waste raw material.
Following the success of pilot trials, Spinnova and shoe and leather goods producer Ecco have agreed to proceed towards commercializing the product and to commence a feasibility study and pre-engineering of the first commercial factory, which is planned to be located in the Netherlands.
Spinnova is also continuing to develop other raw material sources and to evaluate applications beyond apparel, such as durable textiles for home furnishings and automotive upholstery.
Earlier, Spinnova announced it had received a grant of up to €1.6 million for its research and development work from Business Finland from October 2022 to December 2024. The grant amount represents 50% of the project’s total cost estimate of €3.2 million.
The development project focuses on follow-up research of Spinnova technology and fiber, targeting new application areas and product segments, such as composites and nonwovens.
For example, the project includes continuous natural filament development, which will allow Spinnova to be used in new types of textile products and to explore the composites sector.
In addition, the project includes the development of scalable, environmentally friendly dope-dye technology where the Spinnova fiber is dyed before yarn production. Compared with conventional dyeing, the dope-dye method significantly reduces the use of water, energy and chemicals, said the company. The utilization of non-toxic natural dyes in textile dyeing is also being explored in the project.
Infinna Roll-Out Delayed
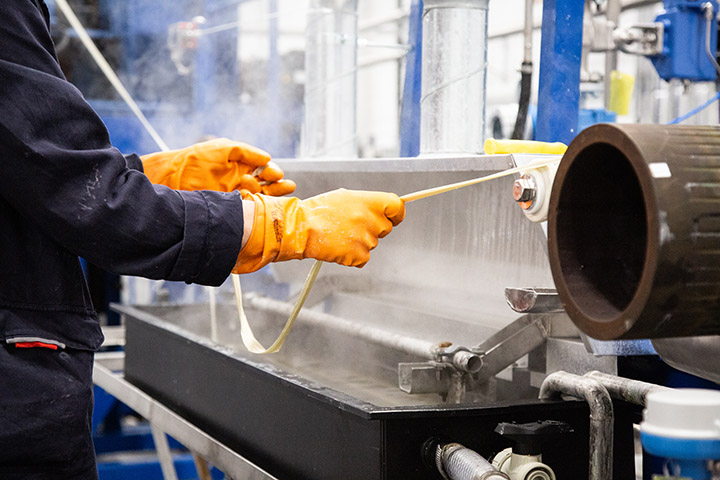
Work to build Infinited Fiber’s first commercial-scale Infinna fiber factory in Kemi, in northern Finland’s Lapland region, is continuing since the site, at a discontinued paper mill at Stora Enso’s Veitsiluoto industrial site, was announced last June.
The company expects construction work to be at full speed later this year, with the main equipment contracts also signed in 2023.
Total investment for the facility has been estimated at around €400 million, with the creation of 270 jobs. However, limited component availability caused by the COVID-19 pandemic and the war in Ukraine have prolonged delivery times for some of the key equipment and machinery needed for the factory. As a result, the first commercial Infinna deliveries from Kemi are now expected to begin in January 2026.
Infinited’s technology turns cellulose-based raw materials, such as cotton-rich textiles, used cardboard or rice or wheat straw, into Infinna, a premium textile fiber with the natural, soft look and feel of cotton. The fibers can be used in a wide range of woven and nonwoven textiles, from jeans to t-shirts and wipes.
During fiber spinning, Infinited uses urea and water to transform waste pulp into fibers. Like Spinnova, its process avoids the chemical solvent carbon disulfide, which is typically used in man-made cellulosic fiber production and known to be neurotoxic. But unlike Spinnova, which uses wood pulp, Infinited generates its own pulp from waste textiles.
Infinited currently operates pilot facilities in Espoo and Valkeakoski, Finland, with a combined nominal capacity of 150 tonnes per annum. The planned flagship factory will have an annual capacity of 30,000 tonnes – equivalent to the fiber needed for about 100 million t-shirts – and will use textile waste as feedstock.
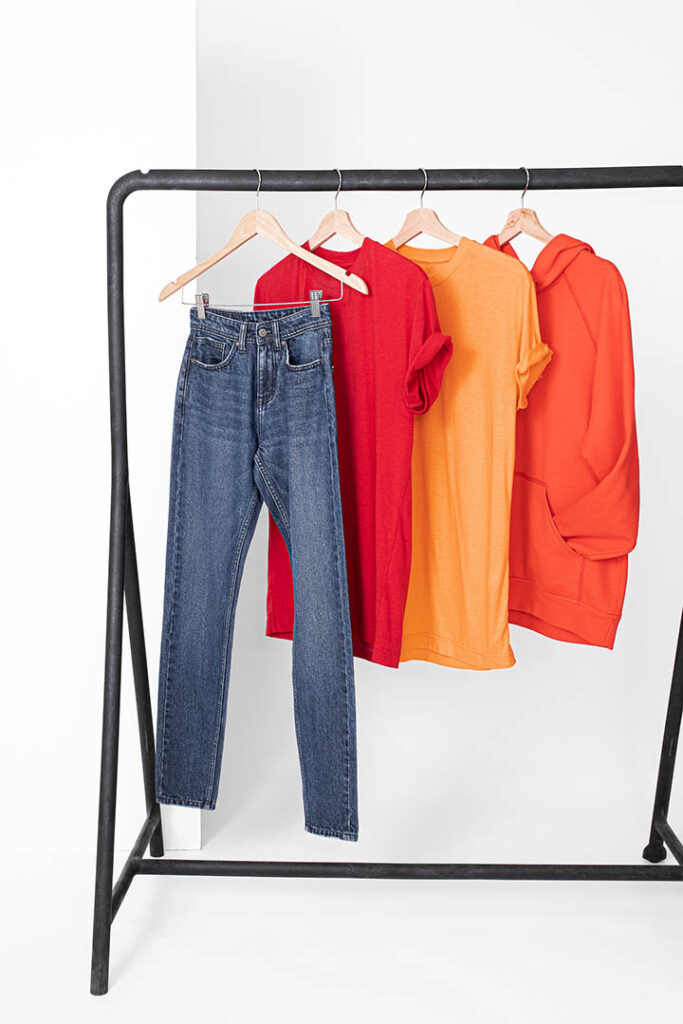
Infinited estimates that annual demand for cotton-like recycled fiber will exceed 4.5 million tonnes by 2030, with the currently announced capacity commitments indicating demand significantly exceeding supply.
To tackle this imbalance, the company is aiming to accelerate Infinna capacity build-up by shifting from a pure licensor position towards actively advancing the next Infinna factories through partnerships, targeting an annual production capacity of 500,000 tonnes of fiber by the end of the decade.
The company has now initiated a site search for the next two Infinna factories. It expects one of these to be in Europe and the other in Asia.
Sustainable Plant-Based Fiber
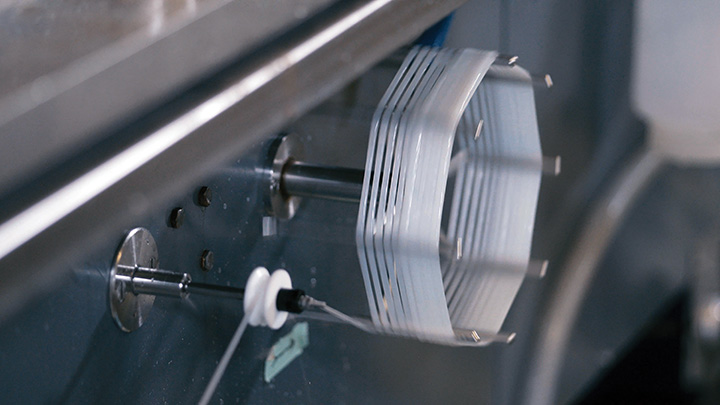
Six months after the first wet-spinning experiments with Nordic Bioproducts Group’s cellulose dissolution method, the Finnish start-up has successfully spun a new plant-based textile fiber at the University of Tampere.
The company is a spin-off from Finland’s Aalto University and the proprietor of the patented AaltoCell technology. Its new fiber, called Norratex, is manufactured from forest industry by-products, textile waste and paper pulp, but without any toxic chemicals or expensive solvents.
Nordic Bioproducts has also announced the launch of a collaboration with CMPC Ventures, the corporate venture arm of CMPC, one of the world’s largest producers of pulp.
In Nordic Bioproducts’ method, the cellulose is first hydrolyzed in an environmentally friendly and cost-effective manner, after which the fiber is further processed into a viscose-like textile fiber.
Nordic Bioproducts began to develop a cost-effective and scalable textile fiber manufacturing process in 2020 in collaboration with the University of Tampere.
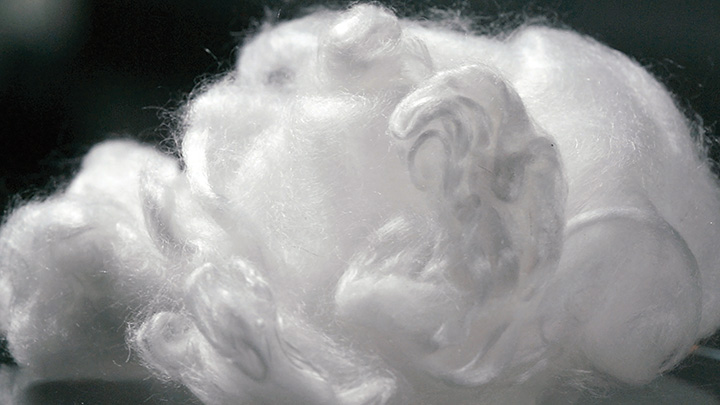
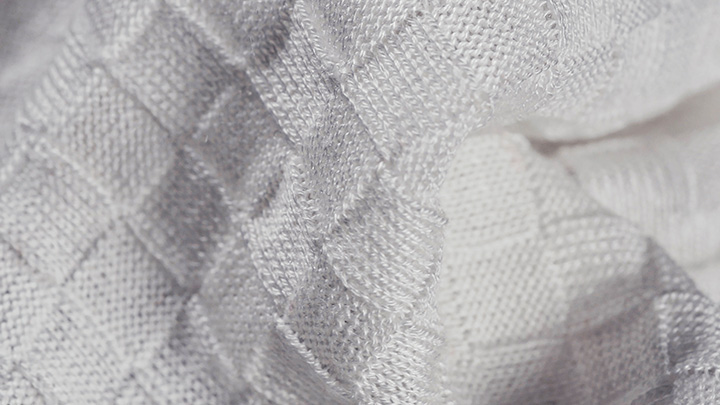
The Norratex method can utilize a wide range of raw material sources, including forest industry by-products, textile waste and ordinary paper pulp. This represents a significant advantage over traditional viscose, which is made from dissolving pulp that can cost up to 30% more than paper pulp, says the company.
The fiber’s properties have been described as “close to viscose, with cotton-like properties,” but with the longer-term potential to become a replacement for polyester.
As well as offering a drop-in solution for existing viscose plants, the new fiber also offers a route to the recycling of mixed material textiles because, on a laboratory scale at least, natural fibers can be neatly separated from plastics into clean fractions.
A €30 million pilot production plant will now be built in Lappeenranta in south-east Finland, close to six existing pulp manufacturing plants, with an annual capacity of around 10,000 tonnes of Norratex fiber.
Renewcell Signs Agreements
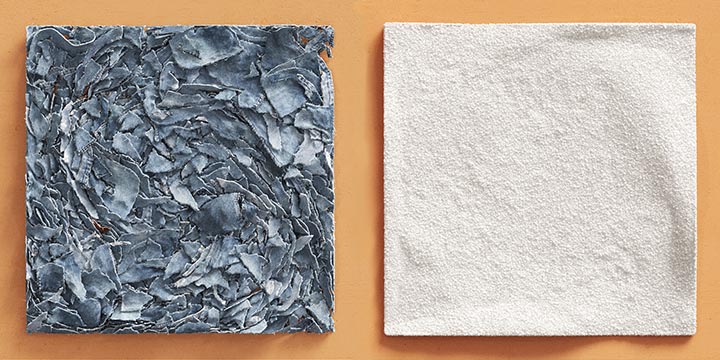
Based in neighboring Sweden, Renewcell is converting an abandoned wood pulp mill into a textile pulp factory, with plans to recycle the equivalent of more than 1.4 billion t-shirts a year by 2030.
The company’s product is Circulose – a recycled dissolving pulp made from 100% high-cellulosic content textiles sourced from both post-consumer and post-industrial waste, using patented industrial-scale process technology developed at Sweden’s KTH Royal Institute of Technology.
Circulose is a direct replacement for the wood pulp currently used by fiber producers to make staple fiber or filament viscose, lyocell, modal, acetate or other man-made cellulosic fibers, which can then be spun into yarns or woven or knitted into fabrics.
Renewcell started up its commercial-scale textile-to-textile recycling plant for the production of Circulose in Kristinehamn, Sweden, in August 2022. With a current annual capacity of 60,000 tonnes, the company is expanding this to 120,000 tonnes by the end of 2023/early 2024.
Further ahead, it has operational targets of 250,000 tonnes in 2026 and 360,000 tonnes in 2030 – around 7% of projected viscose demand – when it aims to have 30 global clothing brands launching products with fibers manufactured from Circulose pulp.
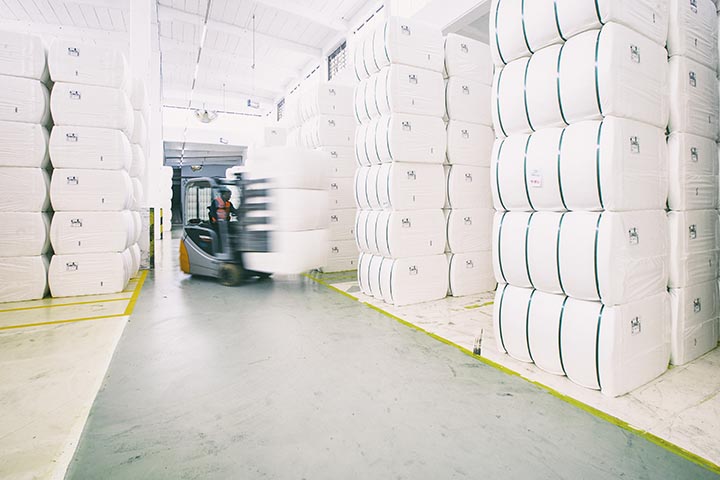
Austria-based specialty fiber producer Lenzing recently signed a multi-year supply agreement, which includes the sale of 80,000–100,000 tonnes of Renewcell’s Circulose dissolving pulp to Lenzing over a five-year period for use in the production of cellulosic fibers for fashion and other textile applications.
Renewcell has also signed a letter of intent with U.S. cellulosic acetate fiber producer Eastman for a collaboration to develop Naia Renew ES yarns sourced from Circulose, and has announced a partnership with Swiss innovator HeiQ AeoniQ to develop a commercial Circulose-based yarn as a replacement for the polyester and polyamide markets.
Circular-Based Fashion
As part of their strategic partnership to promote circularity in fashion, Lenzing and Swedish pulp producer Södra, together with Portuguese yarn and fabric manufacturer Riopele, are developing textiles made from recycled and sustainably produced materials. These will be used for key pieces of fashion brand Filippa K’s spring/summer 2024 collection, which will be presented this autumn.
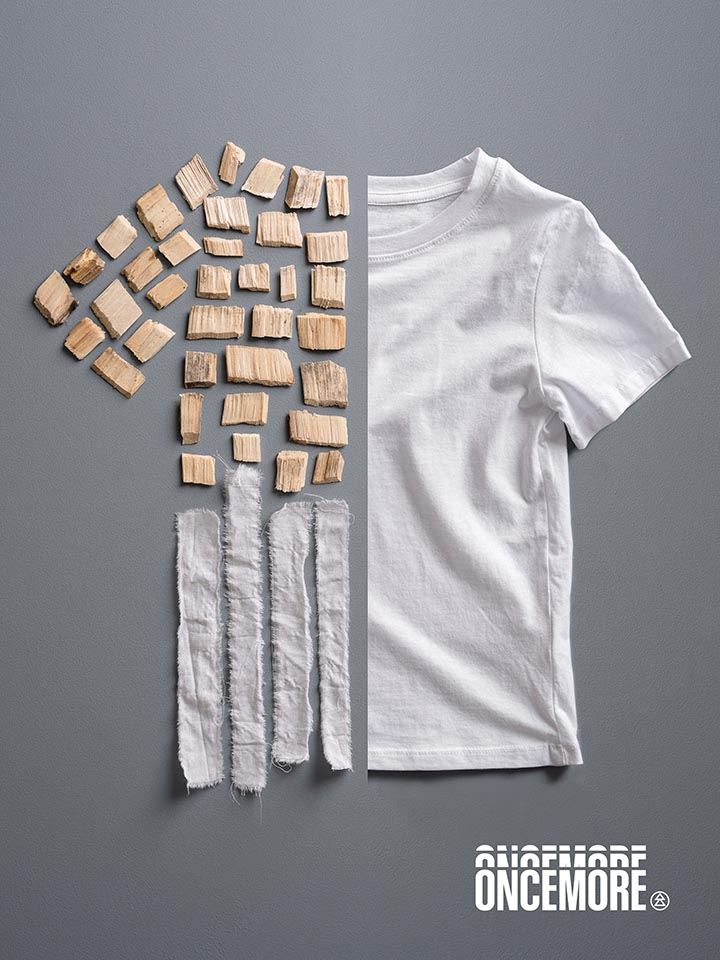
This is the first fashion collection worldwide to contain Tencel x Refibra lyocell fibers based on the OnceMore pulp brand, which was jointly developed by Lenzing and Södra for the large-scale recycling of textile waste from blended fabrics. The lyocell fibers are produced by Lenzing using its Refibra technology in a closed-loop manufacturing process.
Market Demand Growing
The demand for environmentally responsible textile fibers is constantly growing, and the market for sustainable man-made cellulosic fibers is expected to increase by more than 10% over the next decade. Competition in this field is accelerating and these first industrial players are already commercializing their products and moving towards industrial-scale production.
Initially, fibers for fashion applications will be the main target, but nonwovens and technical textile end uses are also on the horizon, as Spinnova’s recent grant for R&D indicates. Many more innovators will be needed, however, to meet the growing market demand.