Synthetic fibers account for more than 60 percent of the world fiber market, and their ongoing growth is supported by comparatively low crude oil prices in recent years despite increasing geopolitical risks in key oil-producing regions. Superior fiber properties and growing awareness on plastic waste currently lead to an unprecedented size of new raw material capacity for manmade cellulosic fibers.
Polyester is the leading fiber material in the synthetic business, benefiting from quite low crude oil prices recently. The OPEC basket price in the quota-free period since 2005 averages at about 74 dollars per barrel. The recent average since 2015 is even 20 dollars lower than that, and a clear recovery was not yet visible after the dramatic contraction starting mid-2014.
The main polyester feedstocks are paraxylene (PX), purified therephthalic acid (PTA), which has almost entirely replaced dimethyl terephthalate (DMT), and mono ethylene glycol (MEG). The past development including an outlook until 2022 is illustrated in Figure 1. (A further breakdown into major markets and regions is available in the textile yearbook. See below for details.)
Massive investments have targeted the Chinese market, and most of the future capacity additions will be realized there to successfully pursue the long-term strategy of backward integration. Nevertheless, a missing linkage between the fiber and petrochemical sector has been witnessed in former times, and a similar bottleneck at present exists for paraxylene following tremendous expansions of downstream PTA capacity. The enlarged foreign PX sourcing offers potential for neighboring industries to export higher quantities into China. This opportunity, however, will not last as Chinese PX capacities are scheduled to more than double in the foreseeable future, which will cause headaches to today‘s main PX exporting nations threatened by higher self-sufficiency. Main reasons for accelerated PX capacity additions beyond import substitution are the Chinese ban on plastic waste imports, which fuels demand for polyester feedstocks, low oil prices make virgin material more economically viable than recycled plastic, and delays in mega projects, i.e. three Chinese projects with a joint capacity in excess of 10 million tonnes.
In addition, polyester raw material investments planned until 2022 are further expected in a small number of countries. New PX capacity is expected for the Middle East, Saudi Arabia and United Arab Emirates, as well as three facilities in Asia – Brunei, India and Indonesia. An expansion in the United States from a new cracker and aromatics project with global scale is also currently in the planning stages with a final decision expected by the end of 2019.
Two PTA projects with joint 2.5 million tonnes capacity are in the pipeline for India and the U.S., while Portugal restarted a plant in mid-2018 that was idle since late 2015. The MEG industry will experience a stronger contribution of investments beyond China. Five projects for the U.S. from foreign investors, and one new plant each in Brunei, India, Malaysia and Saudi Arabia are projected to come online in the next couple of years with a joint capacity of seven million tonnes. Main driving force for Chinese capacity growth is the syngas route, and coal-to-MEG may amount to almost half the installed capacity in China by 2022 from zero ten years ago. However, it needs to be considered that coal has lost its cost advantage after the oil price crash in 2014, and such plants are not compatible with the government‘s campaign against pollution.
The manmade cellulosic fiber segment continued its breathtaking recovery that began in 2002, marking a new all-time high last year at almost seven million tonnes. The staple fiber business in particular has outperformed the entire market of synthetic staple fibers in every year since the financial crisis, thus recording higher dynamics for the 10th consecutive year. The growth momentum for viscose staple fibers is believed to accelerate when taking into account global investments, superior properties of this fiber type including its biodegradability, increasing media response to plastic waste from oil-based fibers, improved security of supply over natural fibers, growing awareness of consumers for environmentally safe clothing, and a limitless raw material supply. Meanwhile, acetate tow will further soften due to ongoing shrinkage of cigarette shipments unless it successfully manages to enter new markets.
The brisk viscose fiber demand explains rising upstream dissolving wood pulp investments that are predicted to witness an unprecedented size of new capacity around the globe in 2019 (Figure 2).
U.S. capacity was the largest until 2017 before Asian investments took the lead. Plants in the region are located in Brazil, Canada and the U.S. Three new plants in the Americas are expected to come on-stream by 2022, with investments targeting debottlenecking and conversion to specialty grades.
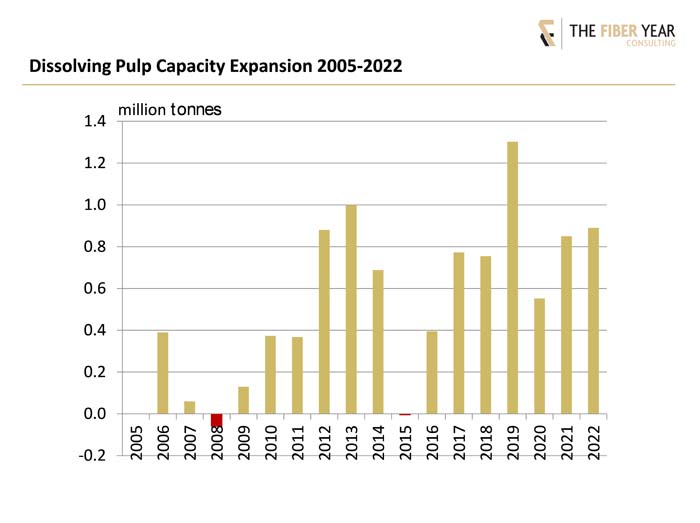
Asia, housing a quarter of world capacity in 2015, is predicted to expand its share to more than 40 percent from 2019. Expansions will be realized in China, Indonesia and Laos, while the remaining industries will be stagnant apart from small debottlenecking in Japan.
Dissolving wood pulp capacity in Europe is spread over nine countries with a joint capacity of nearly two million tonnes. Two new mills are projected to start-up, with further investments are planned for debottlenecking and full-scale production of a Spanish plant after a five-year closure.
The only dissolving wood pulp capacity on the African continent is located in South Africa at three facilities of the world’s largest manufacturer. A debottlenecking project by 50,000 tonnes was completed in late 2018, and another debottlenecking investment by 120,000 tonnes is scheduled to be completed in late 2020.
This article is based on material abstracted from the textile yearbook, The Fiber Year, which covers global trends in manmade and natural fiber production, including nonwovens and unspun materials. The Fiber Year provides trade data for main markets and contains several contributions from industry experts in the area of biopolymers, cotton, wool, viscose and synthetics, nonwovens as well as ITMF textile machinery shipments. A table of contents is available at www.thefiberyear.com.
In the next installment of “The Fiber Year” column, the global development of spun and filament yarns will be highlighted.