Recently, Reicofil introduced the latest generation R5 technology, providing five major benefits in output, quality, efficiency and uptime all centered around intelligence to maximize productivity, reliability and efficiency.
The Reifenhäuser Group, known as The Extrusioneers, is a family business that has been in operation for more than 100 years with 1,500 employees worldwide. The company specializes in the design, manufacture and supply of complete cast and blown film extrusion lines and components, as well as spunmelt nonwoven lines.
Reifenhäuser’s Reicofil technology is well known globally for the production of nonwoven fabrics for hygiene, medical, filtration, absorbents, furniture/bedding and other technical and industrial products. Recently, Reifenhäuser introduced the latest generation of its Reicofil system – the R5 – providing five key benefits in output, quality, efficiency and uptime all centered around intelligence to maximize productivity, reliability and efficiency.
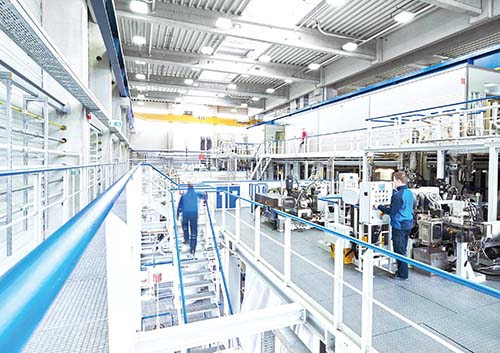
- Machine output – The R5 significantly raises the output bar with up to 270 kg/h per meter width for spunbond fabric even up to 330 kg/h/m for R5 Tech and up to 70 kg/h per meter width for meltblown, allowing for maximum production speed even for higher basis weights. Previously unheard of line speeds are now the norm, as R5 runs up to 1,200 m/min conveyor belt speed, which can be fully utilized in production translating into a +30% increase in line speed.
- Web quality – Even at these very high throughputs and speeds, R5 lines produce webs with much improved overall uniformity, mechanical properties and softness, while reducing hard pieces in the web by 90%. An optimized laydown and improved process stability enhances web quality while significantly reducing fiber contamination around the line. An included vision inspection system and modeling capability monitors production and simultaneously grades the fabric displaying real-time results on the line human machine interface (HMI).
- Efficiency – Known for a long history of reducing specific energy consumption for each new line generation, the R5 process takes this to another level reducing energy consumption for composite lines by up to 15%.
- Uptime – The R5’s intuitive Operation Center (HMI) allows for a failsafe line operation and faster product changes. In addition, machine design changes to improve routine maintenance and cleanings result in quicker PM cycles reducing downtime and increasing productivity.
- Machine intelligence – In the future, not only will line operators and process engineers know Reicofil machines inside and out, the system itself will become an expert. It will know its status; it will be able to predict the effects of parameter changes; and it will communicate with other systems while learning and acting autonomously to fulfill the production targets.
For details on how to submit your company’s technology for consideration as a “Technology Spotlight” in IFJ, contact Matt Migliore at mmigliore@inda.media or +1 919.459.3754.