Plastics play a major role in our lives. They are widely used in many sectors and applications, but at the end of their lifecycle they become waste that needs to be managed properly.
Given the steady rise in the consumption of plastic materials and the subsequent generation of huge amounts of waste, the European Commission has established tighter restrictions to address this issue and foster a more circular model in industry and society. The aim is to keep resources in the production system and decrease dependence on non-renewable raw materials.
Although the amount of post-consumer plastic waste that is landfilled has decreased by 44% since 2006, 996 million kg of plastic were landfilled in 2018 – 38.8% of all post-consumer plastic waste.¹
Textile waste is one of the least-treated plastic waste streams and tends to end up in a landfill. One of the main reasons why this type of waste is not currently recovered, apart from collection and sorting issues, is its high complexity in terms of variety of composition, which makes it difficult to recycle mechanically. It is therefore necessary to develop suitable alternative recycling methods that can be used to recover textile waste.
The RESPECT project (Development of Sustainable Recycling Processes for the Plastics Industry) was carried out under a grant agreement (IMDEEA/2020/67) and funded by the Valencian Institute of Business Competitiveness (IVACE).
Textile waste is one of the least-treated plastic waste streams and tends to end up in a landfill. One of the main reasons why this type of waste is not currently recovered, apart from collection and sorting issues, is its high complexity in terms of variety of composition, which makes it difficult to recycle mechanically.
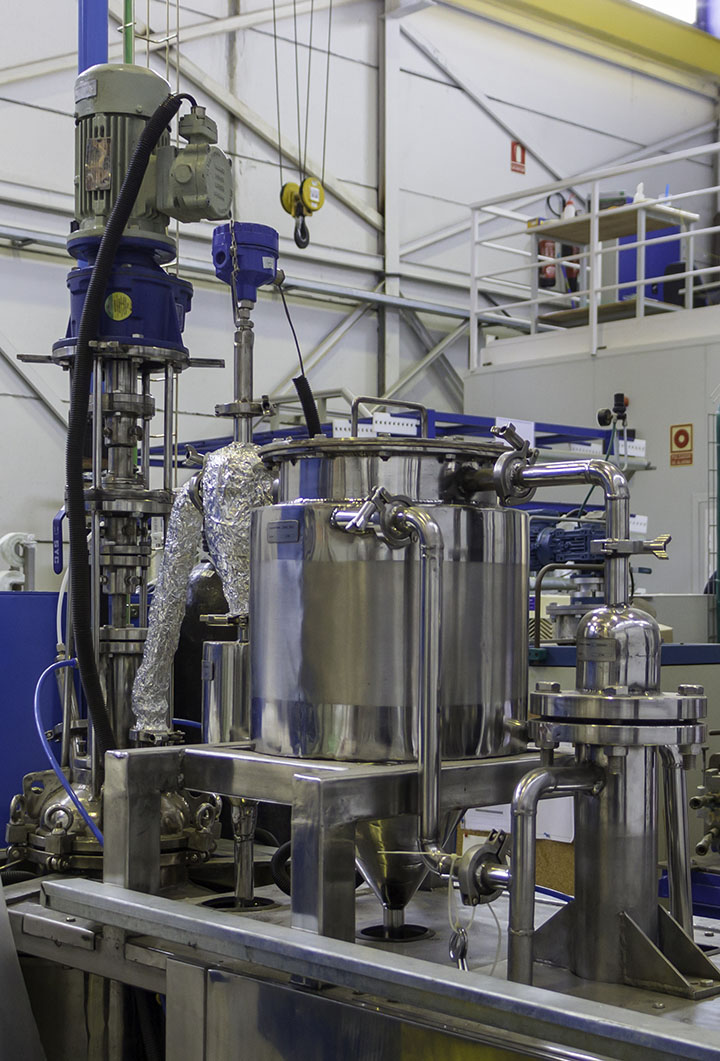
The RESPECT solution
The RESPECT project proposed the development of new technologies to recover complex plastic waste, such as textiles, by combining mechanical and chemical recycling techniques.
The aim of this project, which recently ended, was to develop new separation and recovery processes for complex plastic waste within the framework of the circular economy, and to transfer and disseminate these processes to the plastics industry in Spain’s Valencian community to strengthen the competitiveness and circularity of its business network.
For this purpose, separation tests were carried out with a real textile waste stream to detect and separate waste according to its composition and thus facilitate subsequent recycling. The technique employed consisted of a physical separation based on the continuous identification, detection and automatic classification of materials using near-infrared spectroscopy. Separation performance of nearly 60% was achieved for garments made of polyamide (PA) and 80% for garments made of polyester.
Once the textile waste was separated according to its composition, it was recovered using chemical recycling, which consists of several processes designed to break the polymer chains and obtain monomers and compounds of interest to industry that can be used to obtain recycled raw materials. The processes studied were solvolysis, pyrolysis and biological cracking.
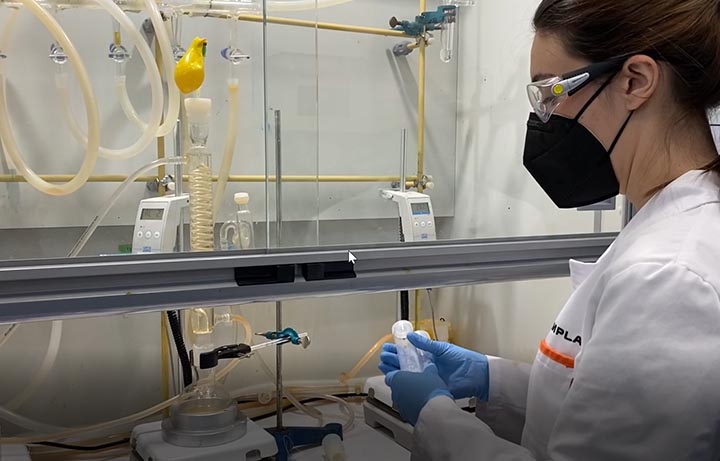
In the case of solvolysis, the waste comprised mainly polyester and cotton and was treated using different catalysts to obtain high recycling yields. (In fact, the separation rate for polyester and cotton was nearly 100%.)
Depolymerization of polyester was carried out with a yield of nearly 70%, resulting in monomer bis(2-hydroxyethyl) terephthalate, which can be used directly for the synthesis of new polyethylene terephthalate or unsaturated polyester resins.
The pyrolysis process was used to recover garments made mainly of PA. In this process, chemical decomposition of the materials was carried out in the absence of oxygen at high temperatures.
Garments made mainly of PA and elastane were put inside the pyrolysis reactor to obtain three different streams, all of which are of interest to industry. The first (more than 10% of the total) is a solid stream with a high carbon content that can be used for active carbon and carbon black synthesis. The second (nearly 50%) is a liquid stream with a composition that makes it recoverable as a fuel; it can also undergo chemical processing to produce monomers for the plastics industry. The third (almost 40%) is a gas stream, which can be recirculated as a power supply for the process itself.
Biological cracking tests are being carried out, but no conclusive results have been obtained.
In conclusion, the combined use of the different technologies studied in the RESPECT project increased the level of recyclability of plastic textile waste and made it possible to:
- reduce the amount of plastic textile waste in landfills;
- reduce dependence on non-renewable raw materials;
- reduce energy consumption and carbon dioxide emissions when obtaining virgin materials;
- recover textile waste and obtain raw materials of interest to industry; and
- foster the circular economy in the plastics industry and particularly the textile industry.
Research and development of new recycling technologies can help expand the field of application and process more waste, regardless of its complexity. While there are limitations on mechanical recycling for certain types of waste, chemical recycling can provide access to new fields.
References
1. Plastics Europe (2020), “Plastics – the Facts 2020. An analysis of European plastics production, demand and waste data.”