Commercial Recycling of Textile Materials That Contain Elastane Presents a Number of Challenges, Especially Ahead of the EU’s Forthcoming Directive on Used Textiles
Each person in Europe gen-erates on average around 15 kg of textile waste each year, mostly used clothing and home textiles, which creates disposal problems, either by incineration or landfill, both inside and outside Europe.
At the same time the textile industry has recycling challenges: less than 1% of apparel worldwide is currently being recycled back into garments (fiber-to-fiber recycling), although more than 14% is made into other materials.
Europe currently has a garment collection rate of 30-35%, with much of the unsorted waste exported outside Europe, particularly to Africa, according to a 2022 study by McKinsey. In addition, most fiber-to-fiber recycling technologies have strict input requirements, with some demanding mono-fiber apparel only.
Challenge of Mixed Textiles
Under the European Union’s Waste Framework Directive, used textiles must be collected and recycled throughout the EU from January 1, 2025. However, the recycling of mixed textiles can be challenging – especially if they contain elastane (also known as spandex).
Many of the yarns and fabrics used to manufacture clothing are easily recyclable when in 100% form, such as pure cotton, polyester or polyamide, but the introduction of elastane in materials, even if only in small quantities, makes recycling using conventional methods difficult, if not impossible.
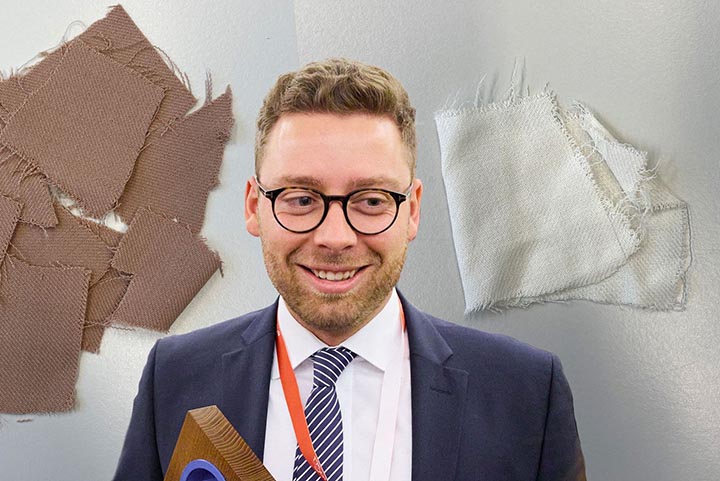
According to Emanuel Boschmeier, a researcher at the Institute of Chemical, Environmental and Bioscience Engineering, Vienna University of Technology (TU Wien), Austria, elastane is so elastic
(as the name suggests) that shredders used to shred textiles before recycling cannot cope with it: elastane leads to soiling, blockages and clumping in the machines.
High Elastane Content
Speaking at last September’s Dornbirn Global Fiber Congress, Jean Hegedus, director of sustainability at the Lycra Company, USA, asserted that some garments with an elastane content of 2-5% can be mechanically recycled, while garments with 5-10% elastane content are typically being recycled into such items as insulation for buildings and the interiors of automotive seating – the main issue is clothing with more than 10% elastane content.
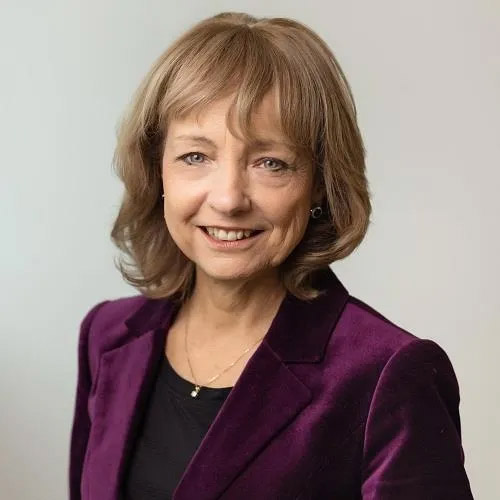
There are several challenges for recycling garments that contain elastane:
- Accurate, computerized fiber sorting and pre-processing are not yet available at scale, making fiber identification difficult;
- Fabrics with elastane can sometimes clog filters, forcing shut-downs and system clean-outs;
- Depending on the specific recycling technology and what chemicals are being used for purification, elastane can sometimes affect the viability of companion fibers.
Scaling the circular economy for textiles will require updated scanning and sorting technologies, recycling systems that can handle fiber blends that include elastane and scalable systems that can help reduce costs and increase output, said Hegedus. If these barriers can be overcome, McKinsey estimates that by 2030 fiber-to-fiber recycling could handle 18-26% of gross textile waste worldwide.
To address the elastane recycling issue, the Lycra Company is developing a Lycra fiber that can be easily extracted from clothing, collected and re-spun into new garments, and is working with selected recyclers on several technologies for recycling various Lycra fiber blends, such as with cotton, polyamide and polyester.
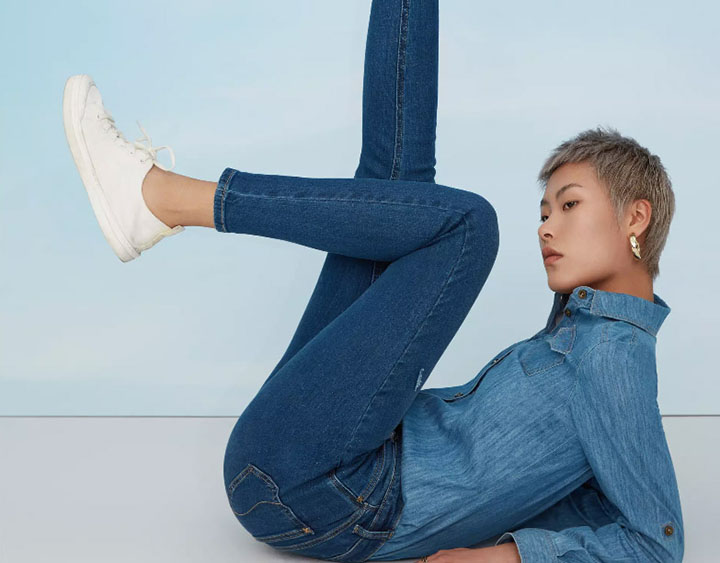
Eventually, this could be combined with the company’s bio-derived technology so that bio-derived Lycra fiber could be recycled from garments. However, when using recycled elastane, Hegedus noted that maintaining optimum molecular weight is critical to both fiber spinnability and performance.
Lycra T400 EcoMade Fiber
Also presented at Dornbirn was Lycra T400 – a stretch fiber although not an elastane. It is an elasterell-p bicomponent yarn (an elastomultiester polyester comprising polyethylene terephthalate and polytrimethylene terephthalate) that adds elastane-free stretch to fabrics. Around 15-18% of the fiber content of Lycra T400 EcoMade is sourced from plant-based materials, such as corn.
The Lycra Company has started trials with a recycler using glycolysis, a well-known chemical recycling method, to evaluate blends with polyester, which showed that Lycra T400 does not disrupt standard polyester recycling streams.
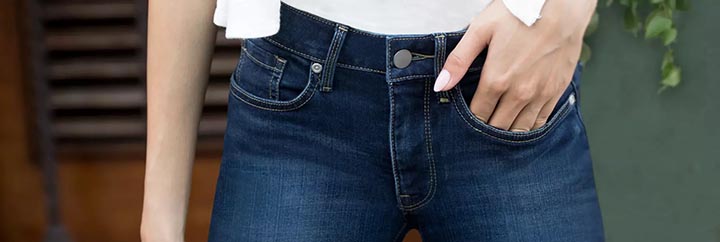
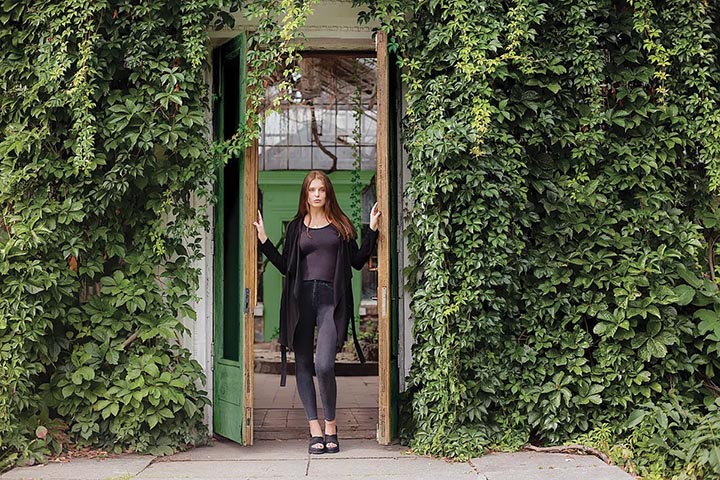
Further, the fabric performance of the recycled fiber was found to be acceptable and, with slight adjustments during chip production, could achieve aesthetics comparable to a control fabric.
Another trial is looking at depolymerizing dyed fabrics of standard polyester and Lycra T400 back into its monomers for separation and reuse to make new fibers.
Processing Agent
Meanwhile, Teijin Frontier, the Japan-based Teijin Group’s fibers and products converting company, has developed a technology to eliminate polyurethane (PU) elastane fibers from discarded polyester apparel.
The technology features a new processing agent used during the pretreatment phase of the chemical recycling process, which helps improve the quality of the recycled polyester fiber. In addition to removing the elastane fiber, the new technology eliminates foreign materials such as dyes.
The company has been conducting tests of this technology since October 2022 and is working with the supply chain to establish a comprehensive ecosystem including used clothing collection, sorting and recycling, with the aim of expanding the scope of fiber-to-fiber recycling.
The new technology swells the PU elastane fibers, breaks their chemical bonds and dissolves them. For system cost control and environmental load reduction, the processing agent can be collected and reused. Recycled polyester materials generated by this method can be used in the existing chemical recycling process, said Teijin Frontier.
Detection Method
With the EU’s forthcoming directive on used textiles, improved recycling processes are urgently needed to deal with the huge volume of used textiles in an efficient and environmentally friendly way.
TU Wien has developed methods that not only better detect elastane and in a more environmentally friendly way than previously, but can also separate elastane gently, allowing the recovery of other fibers undamaged. The key is determining the right solvent.
The first step was to find a reliable and fast method to accurately detect elastane contents in textiles. “During our research, we discovered that no such method existed until now,” said Boschmeier. “The usual test method uses a solvent that is classified as harmful to health and is also extremely time-consuming.”
A novel elastane quantification tool has now been developed, based on mid-infrared spectroscopy, which measures how much elastane is actually present in a garment.
Harmless Solvent
The next step was to find a method to separate elastane from other fibers. The TU Wien researchers experimented with different solvents and carried out theoretical studies, finally coming across a harmless solvent that selectively removes the elastane, leaving the reusable fibers intact.
A patent application has been filed for the method in which materials such as polyester or polyamide can be virtually completely recovered – even the solvent itself can be recovered and reused.
Further, when wool is combined with polyester and elastane, the individual components can be reused. The wool is broken down with enzymes under mild, harmless conditions, producing an amino acid cocktail that can be utilized in the cosmetics industry or in fertilizer production. In the next step, elastane is separated, and recyclable polyester remains.
PU-Based Elastomer Alternative
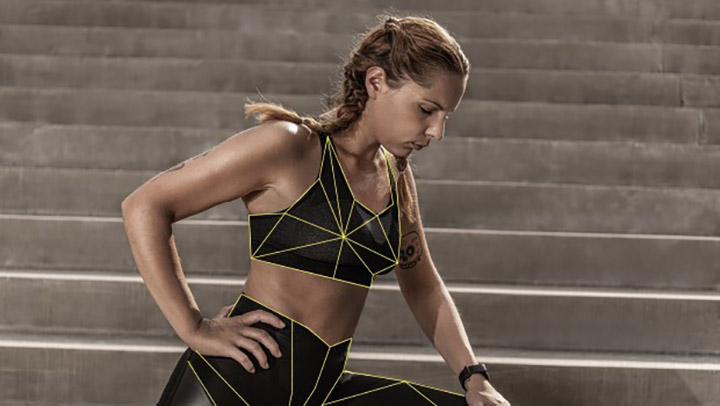
Since the late 1960s, the textile industry has predominantly relied on elastane to impart elasticity to fabrics. However, a relatively recently introduced polyolefin-based elastomer – XLance (pronounced “excellence”) – differentiates itself from the polyurethane-based structure of traditional elastane.
“This ensures that garments made with XLance maintain their stretch and performance for a longer period, underscoring the importance of durability in sustainability, especially in a world where more than 90% of textile waste finish up in landfills,” explained Costantino Colnaghi, chief executive officer of XLance, Novara, Italy, in a recent interview.
Additionally, XLance uses a melt spin production system, in contrast to the dry spin method for elastane. The company has also invested heavily in research and development to enhance the recyclability of garments made with XLance, said Colnaghi.
NIR Sensor Technology
At present, used textiles are sorted almost exclusively by hand. For fiber-to-fiber recycling, currently the most sustainable textile recycling option, the key is to sort textiles by fiber composition. However, this cannot be reliably done manually – by feel – especially with fiber blends.
Annika Datko, a bachelor’s graduate at the Institut für Textiltechnik, RWTH Aachen University, Germany, has demonstrated how used textiles can be sorted by fiber composition using near-infrared (NIR) sensor technology. This is already state of the art for recycling plastic waste but is still in its infancy when it comes to sorting used textiles.
The process works by irradiating a textile sample with NIR light. Based on the wavelengths of the reflected light picked up by the detector, a material-specific spectrum can be created that resembles a fingerprint.
Datko compared the spectra of textiles with different fiber components. She was able to prove that it is possible to differentiate between different fiber compositions using NIR and that the method has an average mean error of just 4% on a laboratory scale.