Extreme Recycling and the Short Fiber Challenge
Switzerland ranked top in the list of the world’s most innovative countries for the 12th year running in 2022, keeping the USA in second place, according to Vancouver, British Columbia-based media company Visual Capitalist, using data from the United Nations’ WIPO Global Innovation Index.
This ranking may come as a surprise to many since globally, four of the five biggest R&D spending companies – Amazon, Alphabet, Microsoft and Apple – are all in the USA.
Switzerland’s intellectual property rules, however, are considered world-class and they are complemented by strong collaboration between universities and industry. In addition, the country attracts top talent thanks to its high quality of living.
The Waste Issue
Innovation was very much to the fore at a press event held in Bern from March 16-18, 2023 by industry association Swiss Textile Machinery, ahead of this year’s ITMA exhibition in Milan from June 8-14. A key focus, not surprisingly, was on sustainable production and specifically new processing options for textile waste.
“The separate collection of this waste will become mandatory for all EU member states on January 1, 2025, when its landfilling or incineration will be banned,” explained association president Ernesto Maurer. “A major aim is to greatly increase the use of fiber-to-fiber recycling from the current pitifully low level of just one per cent.”
Switzerland is the base for two of the leading manufacturers of conventional textile spinning technology – Saurer and Rieter – and both outlined the challenges of accommodating recycled fibers in their production lines.
Spinning

“Today only between 30-35% of textiles are collected separately, but by 2030 the aim in Europe is that up to 80% will be recycled in some way and that the share of fiber-to-fiber recycling will grow to 18-26%,” said Saurer’s managing director Marcus Rennekamp. “A high degree of contamination, lower production speeds and a lot of personnel intervention are all common consequences of using recycled short-staple fibers in a rotor spinning mill.
“Extreme recycling is the new challenge for yarn producers, with ultra-short fibers bringing conventional spinning machines to their limits. We have developed a patented performance kit for dealing with these ultra-short fibers and the first trials using it have shown an increase in production of more than 30%.”
Fully automatic rotor spinning essentially consists of four key processes – spinning, winding, automatic piecing (splicing) and the automatic doffing (removal and replacement) of yarn packages, or bobbins.
On the Saurer Autocoro spinning machine, the first three processes have been integrated into each individual spinning position through individual drive technology and the new doffing cleaning units (DCUs) on the Autocoro 10 system have been designed to help spinners to achieve both higher yarn quality and personnel efficiency.
Clean Rotors
When doffing a package, rotor cleaning is carried out simultaneously by the DCUs which travel from spinning position to spinning position. Up to eight DCUs can be configured differently on Autocoro machines depending on the machine length, package size, yarn count and raw material.
Each DCU can be precisely adjusted to the quality requirements of its lots and work areas and the most important task in the context of yarn quality assurance is to clean the rotors, both pneumatically and mechanically. On the Autocoro 10, this is now even more efficient, with cleaning processes digitally controlled using the latest linear motor technology. A new movement mode for the cleaning scraper has been integrated, and its positioning in the rotor groove is more precise and significantly more efficient thanks to an additional circuit.
Patented
This new cleaning technology loosens and removes even the most stubborn dirt and sticky residue in the rotor to leave them impeccably clean and leading to a more reproducible yarn quality, regardless of fiber type.
During market launch tests, the cleaning technology proved effective for all fibers that are difficult to spin, including recycled and regenerated types.
A patent on the DCU has now been granted and the new rotor cleaning system will be integrated into all newly delivered Autocoro 10 systems from Summer 2023, as well as being made available for retrofitting to older machines.
“We have achieved an energy consumption reduction of 38% on Autocoro systems over the past decade and we are now responding to the latest challenge of the five million tons of recycled fibers that will need to be accommodated by spinners in the next five years,” Rennekamp concluded.
Saurer sold more than a million spindles on deliveries of its Autocoro spinning units in 2022.
Options

Franziska Häfeli, head of marketing and systems for spinning machine specialist Rieter, outlined the options for recycling via either mechanical tearing, which is already established, or by emerging chemical recycling processes for both cotton waste and blends which break down fibers into their chemical building blocks. This can involve, for example, spinning new fibers from pulp in processes being largely developed in Scandinavia, or the melt spinning of recycled PET pellets to make new polyester yarns.
Virgin cotton, she said, has an average short-fiber content of 24.6%, but short-fiber content in recycled pre-consumer yarn waste has an average short fiber content of 46.9%, which makes turning it into new yarns challenging.
Rotor and Ring
Many Rieter customers, however, have been processing such yarn waste for decades, with the preferred option being on the company’s R37 or R70 rotor machines.
“Many of these spinners have not even claimed to be using this recycled material and have included it purely for making raw material costs,” Häfli said. “Rotor spinning is best suited for processing yarns with a high short-fiber content but there is also now an increasing demand for recycled ring yarns which need a higher tenacity to go into weaving, but fiber counts for soft touch fabrics are the goal.
This, however, is very difficult due to the neps and high short fiber content.”
This problem is considerably greater when it comes to post-consumer waste, even if it is comparatively pure, she added.
A batch of fibers from recycled white 100% cotton t-shirts, for example, will have an average short-fiber content of 71.3%, with an average fiber length of just 9.8mm.
Texcircle
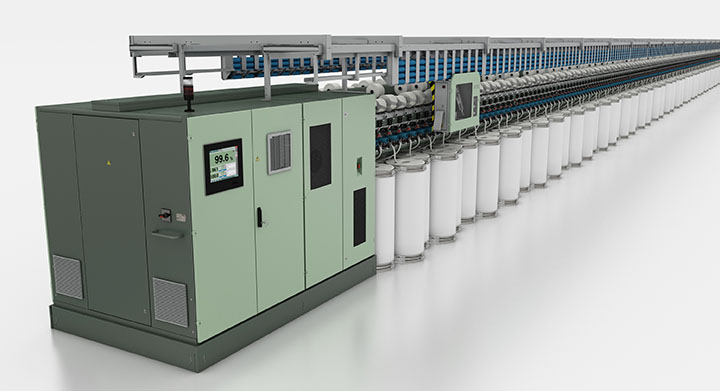
Rieter has been involved in the two-year Texcircle project with partners Coop, Lucerne University, Rieter, Rohner, Ruckstuhl, Texaid and Workfashion, to explore the potential of integrating different types of recycled waste into textile supply chains.
Funded by the Swiss Innovation agency Innosuisse, other project partners include the Federal Office of Civilian Service (ZIVI), Nikin and Tiger Liz Textiles, with additional support through collaborations with nonwovens producer Jakob Härdi and yarn spinner Marchi & Fildi.
At the Bern conference, six prototypes at various stages of the production process were displayed from the project, the result of joint developments spanning design, collection and sorting trials through to tearing and spinning production trials.
The project was able to recycle 2.5 tons of pre- and post-consumer textile waste into product prototypes, with Swiss sock maker Rohner already commercializing sports socks made from 50% ring spun yarns made from a consignment of surplus ZIVI t-shirts and unworn pants from Coop bakeries, along, with 50% Lenzing Refibra, which also consists of recycled post-consumer waste and regular virgin cellulose.
Other prototypes included a sweater knitted from recycled denim jeans with Rieter rotor yarns, with the percentage of recycled fibers between 70 and 90%, and carpet made from old winter coats with a wool content of at least 70%. Prototype bags and fleeces were also developed from raw materials including shredded old black t-shirts and polyester padding collected by Texaid and processed by Jakob Härdi.
Building on its findings, Rieter plans to unveil a number of new developments related to recycling and system integration through digitization at ITMA 2023, with a focus on cost per kg of yarn, raw material, energy consumption and automation. It will also extend its Com4 branding program to include certain recycled yarn content ranges.
Reference Manual
A third Swiss company, Uster Technologies, also plays a crucial role in the conventional fiber spinning world.
The Uster Statistics have become the industry benchmark for achieving and guaranteeing quality in yarn spinning. First introduced as a three-page document back in 1957, the reference manual now includes some 4,500 graphs and process parameter guidelines and the 2023 edition will include a section on the processing of recycled fibers for the first time. Now available as an app, the 2022 edition has been downloaded more than 23,000 times.
Uster’s executive vice-president of marketing and business development Sivakumar Narayanan said that a major bottleneck in spinning with recycled yarns is achieving the necessary quality.
“Spinning yarn blends of virgin and recycled fibers is a much bigger challenge than any other commonly used blend, but the results can still be acceptable with comprehensive quality testing, know-how and experience,” he said. “The use of mechanically recycled fibers in spinning has specific quality considerations – such fibers have a higher short fiber and nep content and may often be colored, particularly if post-consumer material is used. It’s also true that recycled yarns have limitations in terms of fineness.”
Officially, a yarn can be branded “recycled” when spun with more than 20% recycled fibers, according to the Global Recycled Standard (GRS), a voluntary product specification for tracking and verifying the recycled content of materials in a final product.
Awareness of the risk of yarn quality deterioration with recycled fiber blends means that quality control is the only way to assure customer satisfaction and even then, the task is far from simple.
Blends
“Blending virgin and recycled cotton together is well known as a challenge for spinners,” Narayanan said. “The smartest spinners and world-class processes simply can’t overcome the fact that some important quality parameters will be adversely affected and even the most sophisticated spinning machinery won’t fix the problem. Awareness of the risk of yarn quality deterioration with recycled fiber blends means that quality control is the only way to assure customer satisfaction and even then, the task is far from simple. When spinning new materials, Uster strongly recommends taking both numeric test results and graphic evaluations into account, to eliminate the risk of problems in further processing.”
Cooperation
“The experience of spinners around the world combined with the latest technology in quality control and analysis systems, represent a promising basis for the future,” concluded Ernesto Maurer. “The new reality of the need for closer communication and cooperation will include all players from fiber to fabric. It’s an essential debate for everyone – and the member companies of Swiss Textile Machinery are ready to assist in accelerating this transformation.”
Further new developments were presented at the Bern conference by the companies Autefa, Benninger, Bluesign, Crealet, Heberlein, Itema, Jakob Müller, Loepfe, Luwa, Retech, Santex Rimar, Stäubli, Steiger and Swinsol.