Behind the Scenes at Şafak Technical Textile – A Legacy Technical Textile Producer to Watch
International Fiber Journal spoke with Simon Papo, President of the Board, and Ceki Papo, COO, of Şafak Technical Textile, a leading technical textile manufacturer located in Tuzla, Istanbul Province, Türkiye. We discussed the company’s long history and exciting new developments – including a groundbreaking sustainable advanced textile. Since its founding in 1958 by Mr. Jak Papo, this three-generation family business has been dedicated to solving complex textile problems.
Şafak operates with 30,000 square meters of factory floor space, producing over two million meters of textiles per month, and exporting to around 30 countries across five continents. The primary sectors served include automotive, aviation, marine, railways, outdoor upholstery, shoes and bags, sportswear, wall coverings, and more. The company is diligently working on digitalization, implementing a sustainable manufacturing system, traceability, carbon footprint calculations, and life cycle assessment analyses. Here is their story.
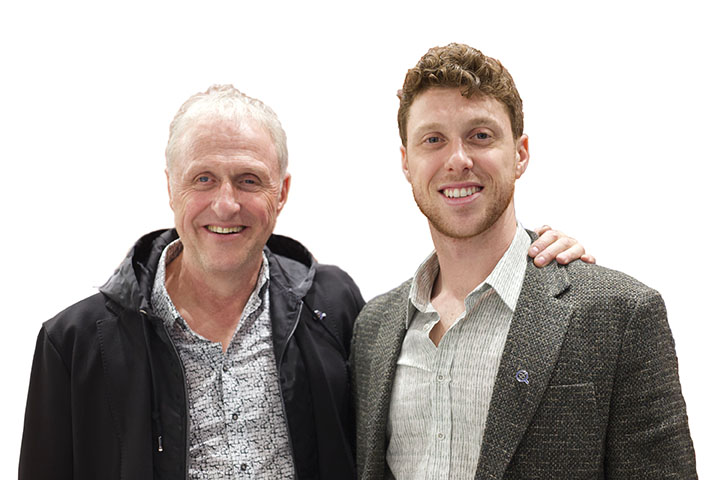
International Fiber Journal: Give us a history of your family business, and its legacy.
Simon Papo: Şafak Technical Textile was established in 1958 by my father, Jak, before I was born, as one of the first circular knitting production facilities in Türkiye. In 1972, we became the first company in Türkiye to produce synthetic leather backing for a large German company, for whom we were the sole supplier. This milestone paved the way for what we do today. In the early 1990s, the Turkish synthetic leather market began booming, and we have remained the main technical backing supplier ever since.
I joined the company in 1987 after completing my studies in mechanical engineering with a focus on robotics and automation at the Technion, Israel Institute of Technology. The company was focused on technical textiles, though we didn’t refer to them as such back then. I always urged my father to pursue the technical direction to gain a stronger competitive advantage. Our company’s hallmark is innovation; we don’t copy and paste – we create unique materials, a key focus for our research and development unit.
IFJ: Being a family business, how has the company evolved with the generations?
Simon: We have always prioritized R&D and innovation. Our history is filled with milestones that demonstrate success in various projects. For instance, in 2004-05, Trenitalia (Italian railways) needed a synthetic leather product for their seats that had challenging mechanical strength requirements. Achieving this required an unconventional approach. Inspired by Da Vinci’s dome, which carries itself, we developed a solution that had a similar self-supporting knit structure.
Looking ahead, I am proud that my son, Ceki, who studied at the Johns Hopkins University, chose to join the family business, seeing the bright future we have. My other son, Erel, will join us next year after completing his studies in computer science and applied mathematics at the University of Southern California. We consistently produce solutions to our clients’ complex challenges, adding value to their needs. We are very excited about the future.
We created a water-based impregnation-like process to replace the DMF, eliminating harmful chemicals. Corium™ was born from this innovation, requiring significantly less water in production and avoiding chemicals under regulatory scrutiny.
IFJ: What is the process working with Şafak clients – your ‘competitive edge.’
Ceki Papo: We pride ourselves on our customer service. While we produce tangible technical textiles, we understand that high-quality service must accompany our products. Our R&D service is our competitive edge. We rarely say no to challenges; instead, we strive to find solutions, defining ourselves as solution providers. This approach often entails developing new equipment and optimizing production flows to provide our clients with a competitive edge.
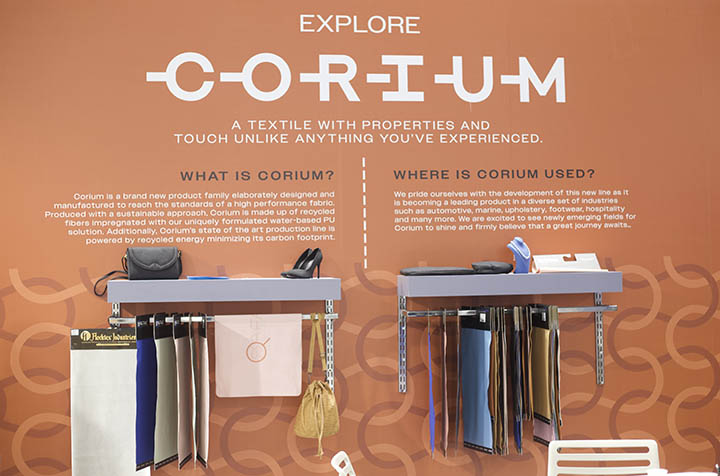
IFJ: Tell us about Şafak’s product innovation, Corium™ – why is it a never-seen-before textile?
Simon: Over the years, we have delved deeper into the synthetic leather business, which involves coating or coagulating processes. Polyurethane resin coagulation, typically done with DMF, faces potential bans in Europe. Seeking alternatives, we were inspired by the 1970s Italian automotive interior applications to develop a similar end-product but through a completely different manufacturing process.
We created a water-based impregnation-like process to replace the DMF, eliminating harmful chemicals. Corium™ was born from this innovation, requiring significantly less water in production and avoiding chemicals under regulatory scrutiny. Additionally, our state-of-the-art production line uses recycled energy recovered from our exhaust gasses. Hence, Corium™ products are environmentally responsible, made from recycled fibers combined with water-based PU.
Today, Corium™ has numerous applications across various markets, becoming one of Şafak’s flagship products.
IFJ: You also created your own machinery to produce it, correct?
Simon: Yes, we built our own machine because the process we came up with is unique. No existing machine could produce Corium™ as we needed, so we developed our own.
IFJ: What are your plans for Corium™?
Ceki: The potential of Corium™ is larger than we initially imagined. While we are meeting current contracted demands, its applications span wall coverings, upholstery, automotive, footwear, and more. We are in the early stages of this journey, building the right team to address technical, sales, and marketing challenges to supply various industries simultaneously with one product family.
IFJ: Share more about your sustainability efforts.
Simon: In 2012, we were the first to produce fully recycled textiles for a global leading sports shoes brand for the London Summer Olympics, using recycled polyester. That was a pioneering project in Türkiye’s recycled textiles industry.
Ceki: Our sustainability efforts gained momentum in recent years. We have advanced our digitalization journey with an in-house developed ERP system and are expanding our IT team with new software engineers. Traceability is at the core of our new system, allowing us to track production parameters and ensure target parameters match the realized ones. Our goal is to complete life cycle assessments and carbon footprint calculations using our system, sharing this data with clients to support their sustainability tracking.
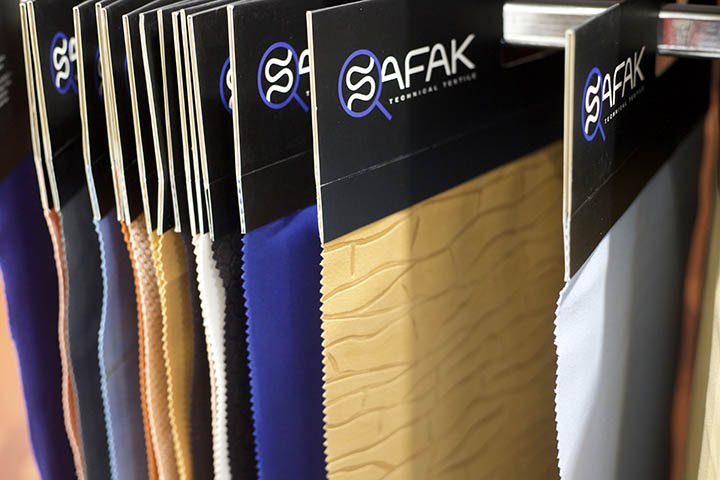
IFJ: What is the structure of your team?
Ceki: Our unique team structure distinguishes us, placing R&D and engineering at the core of our business operations. As we continue to develop innovative digital solutions, our organizational framework is evolving to better manage daily tasks and workflows. This evolution is leading us to expand our team with an increasing number of computer scientists and engineers, strengthening our capabilities and driving our progress forward.
IFJ: How does your company work with universities and students?
Ceki: For several years, we’ve collaborated with Istanbul Technical University, known for its renowned textile engineering department. We benefit from their guidance and mentorship on R&D projects and use their accredited textile laboratories for physical and chemical tests. Additionally, we are collaborating with Shenkar College of Engineering and Design in Tel Aviv to create a hub that combines academia and industry, assisting students in realizing their dreams in textile design and manufacturing.
IFJ: Your tagline is, “Quality is not visible at first glance.” What does that mean?
Simon: At first glance, one cannot fully appreciate the innovation and customization that define our approach. This motto signifies that the depth of our commitment to quality and the advanced technological processes we employ are not immediately evident. It requires a deeper look to truly understand the precision, innovation, and customization embedded in every product.
Note: Şafak Technical Textile will be exhibiting in the U.S. at the Advanced Textiles Expo on September 24-26, in Anaheim, CA.
For more information visit www.safaktekstil.com.tr