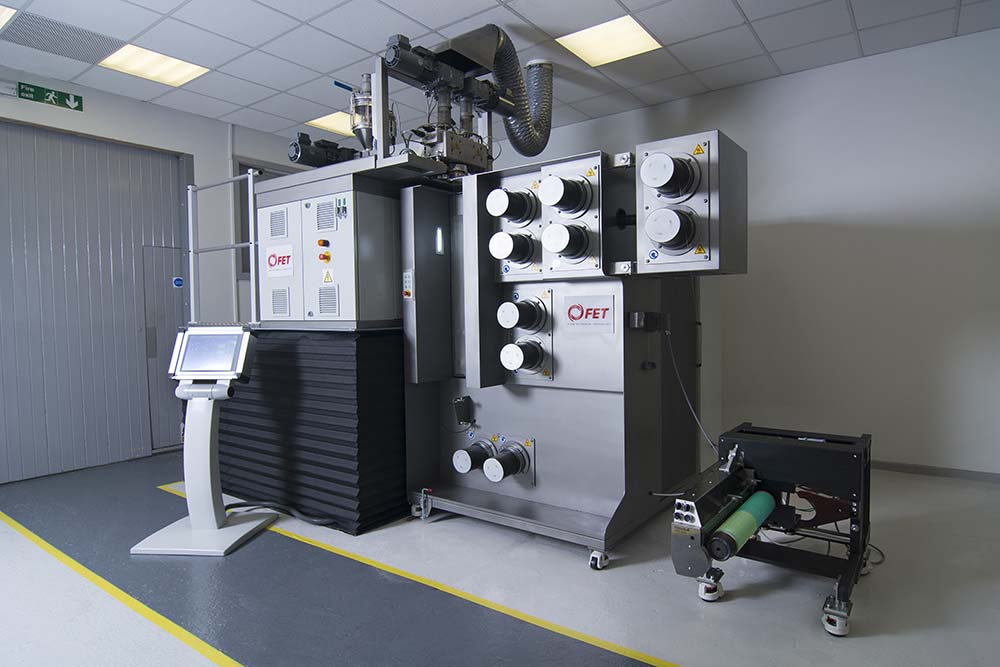
Demand for antimicrobial fibers, textiles and apparel is forecast to continue its strong growth, with consumer demand fueled by growing awareness of the importance of personal hygiene and the health risks posed by certain microorganisms.
Technical challenges
This development presents challenging demands on the fiber processing sector. A particularly efficient and cost-effective manufacturing route is the melt spinning of fibers from resins premixed with bioactive materials
However, producing yarns by this method also presents many technical and engineering issues which must be overcome. This includes achieving activity, sustained delivery and dispersal of the active in the fiber while maintaining adequate tensile properties in the base fiber/yarn.
Fibre Extrusion Technology (FET) of Leeds, UK, has considerable expertise in this field. Founded in 1991, FET is a supplier of high-performance equipment for the manufacture of technical textile materials and works closely with high-value clients in developing processes and designing equipment to produce technical fibers for specialist industrial and biomedical applications.
This includes the application of resorbable resins such as polyglycolic acid (PGA), poly-L-lactic acid (PLLA) and their copolymers used in biomedical applications such as surgical sutures.
Processing options
There are various processing options that produce antimicrobial fibers in different formats. However, the specific format selection needs to consider the bioactive delivery as well as all the other functional and aesthetic requirements of the end product.
An important aspect is the filament diameter as this determines such factors as the path length for diffusion and surface area, and limits the size of bioactive particulates.
FET offers a choice of three meltspun processing options: multifilament, monofilament and nonwoven.
Multifilament yarns are made up of many small-diameter filaments. The individual filaments are usually within the range of 8-60 µm and the number of filaments can range from single figures to 200 or more.
Multifilament yarns are generally characterized by flexibility and high surface area. They can be used directly to produce knitted, braided or woven products and can also be chopped to produce staple fibers.
Monofilaments have larger diameters that those comprising multifilament – usually greater than 50 µm – and are generally intended for use either singly or in small bundles.
Typically, they differ from multifilament yarns by having a much lower surface area for equivalent linear density and higher breaking loads per filament.
Meltspun nonwovens are the next processing option, comprising two main formats: spunbond and meltblown. To produce spunbond fabrics, filaments are extruded, drawn and laid onto a moving carrier. Meltblown fabrics are comprised of a randomized array of filaments with diameters much smaller than with spunbond, typically ranging from 1-40 µm.
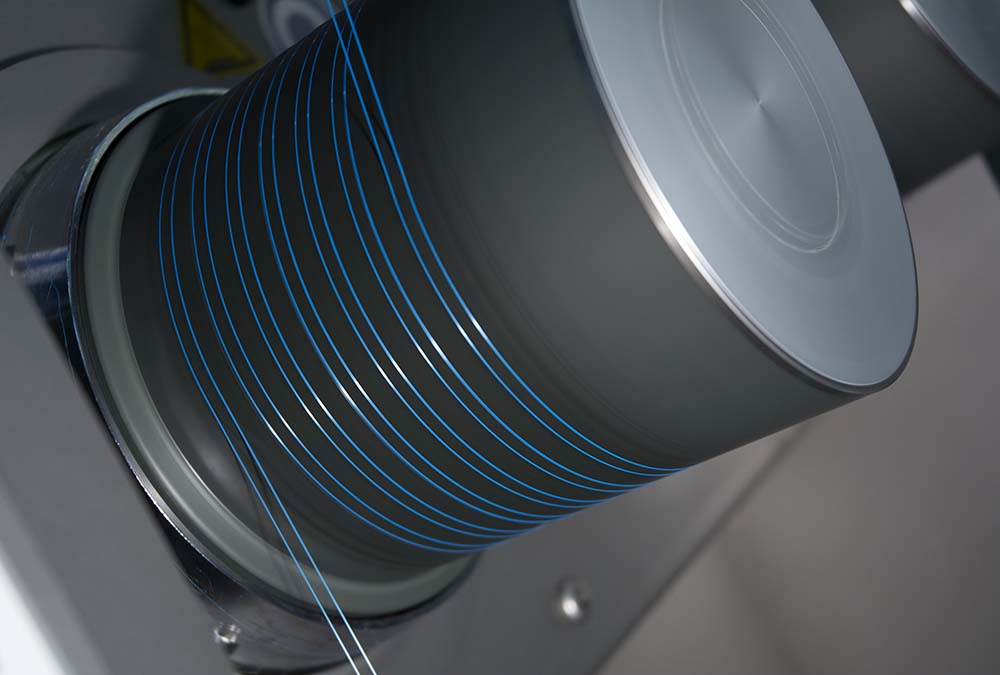
Material options
There are two main material options available: degradable and non-degradable. The degradable option is sometimes selected as a route to sustained delivery. For non-degradable, the full range of filament-forming thermoplastic resins are available to choose from.
Popular choices remain polyolefins, polyamide and polyester for applications such as mosquito nets and antimicrobial apparel.
Processing considerations
There are three principal processing considerations that pose a challenge for manufacturers:
- Dispersal and distribution
- Activity and degradation
- Release and surface exposure.
Processing technologies offered by FET, such as the highly successful FET-100 series of multifunctional laboratory and pilot melt spinning systems, can overcome many of these issues, helping to strike the right balance between financial and technical constraints.
Core/sheath bicomponent melt spinning technology can be used to put the bioactive material only in the sheath. This requires less of the bioactive material, which is of particular use where it is expensive or where the dose needs to be limited.
It is also useful when the bioactive needs to be delivered from a specific polymer that lacks the appropriate physical properties required by the product.
Tri-component technology is also an option for cases where the specific bioactive system requires a more complex delivery system.
High pressure liquid injection (HPLI) is an innovative injection and dispersing system for dosing liquid additive formulations into the polymer melt stream for fiber spinning.
The active ingredient is dispersed into a carrier fluid as a solution or suspension, then injected and mixed into the polymer melt. The injection and mixing takes place between the extruder and the fiber spinning head.
These technologies can provide several benefits. The risk of degradation to thermally sensitive actives can be reduced as the active compound is no longer exposed to the time, temperature and shear of the extruder barrel.
There can be improved dispersion of the active materials, especially nano-particulates as this can be carried out as a separate, low-temperature mixing operation into the carrier fluid.
The ability to run the extruder on virgin polymer significantly reduces losses of the active materials during start up and purging.
Other benefits include the elimination of extruder “slip” often encountered with liquid additives at high addition rates and also the elimination of the need to adjust extruder settings when switching between additives.
There are of course some bioactive materials and carrier polymers that are inherently incompatible with a thermal extrusion process. For this group of materials, FET can still offer options for delivery in a fibrous format.
The wet/gel spinning technology is used in the FET-200 system. In this process, the carrier polymer is made ductile by combining with a solvent to form a solution or gel that can be spun at ambient temperatures. The spun fibers are then passed through a series of coagulation and washing stages before being drawn to develop the required tensile properties.
This process is applicable where thermal extrusion is not an option; examples include ultra-high molecular weight polyethylene (UHMWPE) or protein-based fibers such as synthetic silk.
Polymer coating is another option. In this process, the base fiber is produced first and then coated with a polymeric solution containing the bioactive.
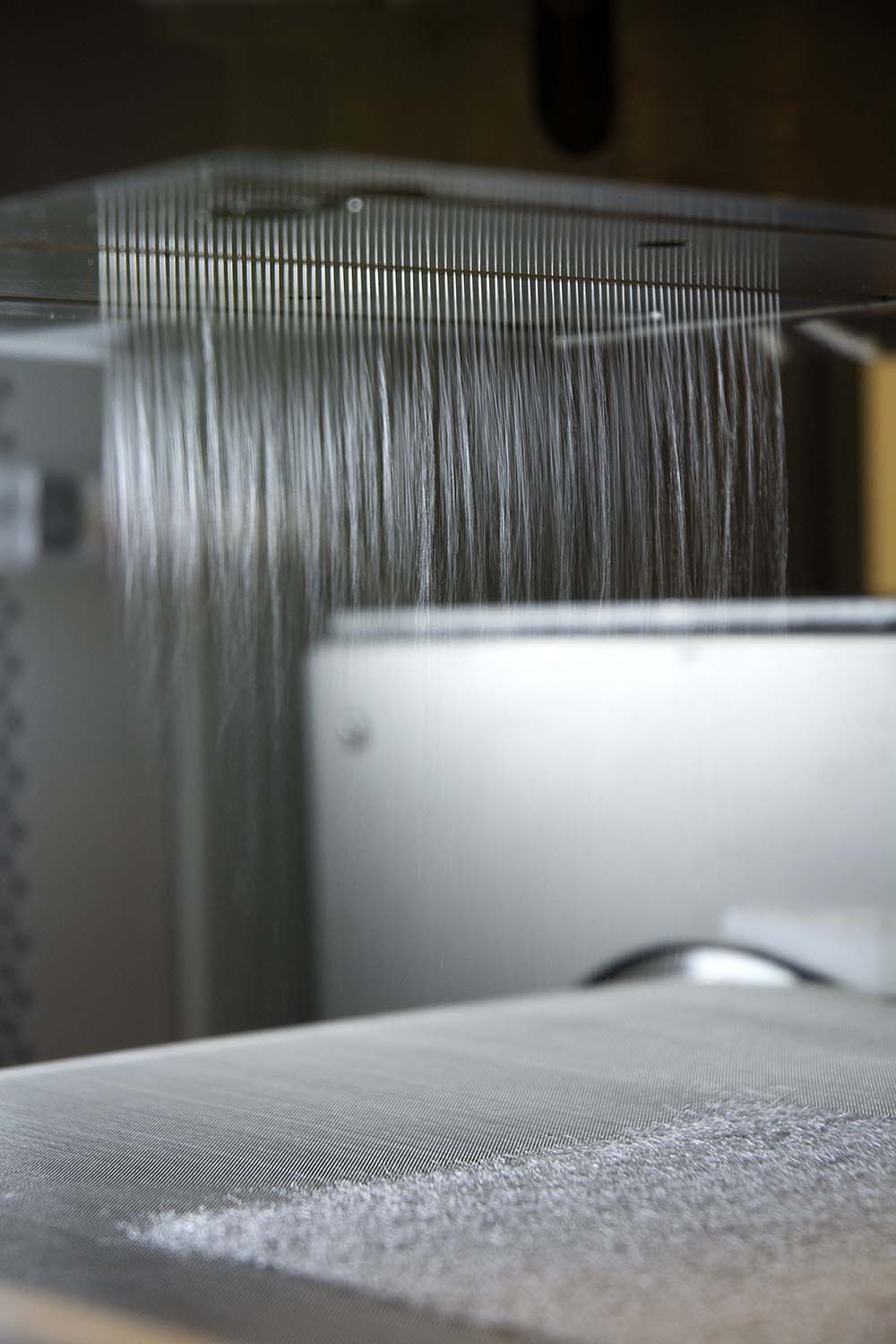
Solutions through collaboration
Such an array of challenges can only be successfully overcome through close cooperation between customer and manufacturer.
A good example of this is when a customer approached FET with a new insecticidal compound intended for use in anti-mosquito nets. They wanted to include the compound in a polyolefin monofilament and had already attempted to produce the filament by conventional methods, but found the bioactivity had been destroyed during processing.
After discussion, it became clear that the HPLI system had the potential of delivering a filament with all the properties required for this application. A short study on FET’s pilot lines confirmed the feasibility of producing the yarn by this route and showed that bioactivity could be preserved.
This work also identified some challenges in accurately metering the active ingredient and attaining the sustained delivery necessary to comply with World Health Organization standards
FET worked on the engineering design of the injection valves and also the formulation of carrier liquid. The investigations culminated in a successful pilot manufacture of the yarn and eventually to installation of the process in the customer’s factory.
This achievement would not have been possible without FET’s newly upgraded Process Development Laboratory. This in-house laboratory facility is a vital element of the business, enabling a high level of equipment and process development for customers requiring multifilament, monofilament or nonwoven fiber production.
Installed in this facility is a complete range of pilot fiber spinning lines, including both mono- and bicomponent configurations, and capable of facilitating all aspects of fiber research and development.
The research and development team has substantial capability to produce fibers from many types of polymer including those containing bioactive additives.
For more information contact:
Fibre Extrusion Technology Ltd
Tel: +44-113-253-7676
Email: sales@fetuk.com
Website: www.fetuk.com