DILO Launches New MicroPunch Needling for Lightweights Technology at ITMA 2023
In news off the ITMA 2023 expo floor, the DILO Group – Engineering for Nonwovens unveiled new groundbreaking MicroPunch Needling for Lightweight technology that solves a significant problem in manufacturing of lightweight nonwoven materials. “We have come to this launch with an advanced economic and environmental solution,” said CEO Johann-Philipp Dilo during the launch.
“MicroPunch overcomes hydroentanglement issues, saves money on energy, water, and waste is low.” IFJ caught up with company CEO Johann-Philipp Dilo to get more details to this amazing development, and how the industry can utilize the technology.
IFJ: Explain the core problem this tech solves for the industry?
Johann-Philipp Dilo: After two decades of development work Dilo now offers the MicroPunch technology to enlarge the range of applications of needled products into the low weight sectors. Here staple fiber nonwovens are mainly offered as hygiene or medical products like wipes for personal care or single-use garment, operation covers, etc. However, also many technical applications for nonwovens exist in the lower weight range and even the garment and bedding applications could profit from nonwoven material which is produced at high production rates and low energy consumption. So far, this has been dominated by products typically water entangled. This high-speed process is currently considered ideal for such fine fleeces consisting of fine fibers below 1 dtex up to about 3.3 dtex having weights of ca. 30 up to 100 g/m².
Needling, on the other hand, has been ideal more in the upper weight range above ca. 100 g/m² and going as high as several kilograms/m², normally with coarser fiber. Due to the enormous range of textile parameters, like fiber material, fiber fineness, staple length, crimp and surface features together with machine parameters like stitching density, depth of penetration, needle fineness etc., the number of parameter combinations is immense and makes needling adaptable to a very large number of different products and their applications. The hydroentangling process, however, has many limitations in that weights above 100 g/m² are normally excluded as are fibers above 6.7 dtex fineness. From that perspective, hydroentangling addressed foremost the low weight range with fine fiber for hygiene and medical products with the exceptions in some technical fields, coating substrate and roofing material. Given that situation, it was only natural to study the market for such hygiene products with their share of total nonwoven production. Wipes for personal care, industrial and domestic applications cover almost 30 % of all staple fiber drylaid nonwovens.
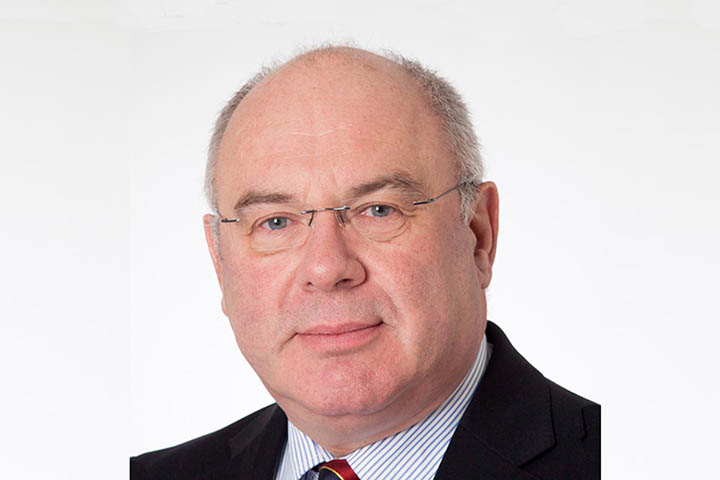
At the same time the amount of energy necessary per kilogram of nonwoven material is very high within the hydroentangling process. A lot of electrical power is required to reach a high water pressure forming the water jets, to vacuum the material, get water out of the fleece, pump the water through filtration systems and also gas to dry the material when leaving the water jet area.
Additionally of concern is the amount of water consumed through the drying process and the wastewater. This is a considerable amount which is of particular concern when water resources are shrinking. The high energy consumption is responsible for a large part of the total costs.
Considering all costs, the costs of the fibers which leave the system as a non-recyclable filter cake is again to be accounted for. Also, the edgetrim material typically strongly consolidated is difficult to reopen and to recycle. All in all, the described shortcomings of water entangling motivate for an alternative which has been found in MicroPunch intensive needling. A much smaller amount of electrical energy is needed for this process, no water is consumed, no gas-heated drying applied and fibre consumption is reduced. Cost comparisons have shown energy savings in a region of ca. 75 %. Overall cost savings are possible between 25 and 50% depending on the weight of the material. As a conclusion, the problems MicroPunch can solve for the industry are a tremendous reduction of energy consumption, water consumption and fiber waste. This is reflected by an overall cost reduction per kilogram of manufactured material.
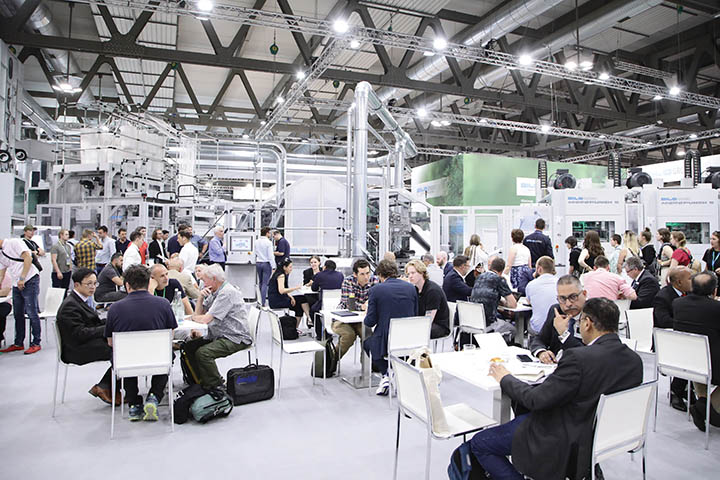
IFJ: Can you tell us how it was developed?
Dilo: MicroPunch is an advanced and modified intensive needling method which was developed by Dilo around 2005, at the time using a needle density of 20,000 per meter per board, applying fine barb needles. This has given good results for lightweight material with a high abrasion resistance, good drape and softness for liquid absorption, generally apt for hygiene and medical applications. The economics at the time, however, with the necessity to invest in a total of six needlelooms per line where not convincing enough.
MicroPunch is applying a large number of needles with up to 45,000 needles per meter per board in three needlelooms of four boards each which has made necessary a solution to equip the needles in a board more economically. This was solved by the invention of our needle module X22 with 22 needles in one module which can be mounted in cassettes of a so-called container board at only 15 minutes per meter per board. Together these have defined the ingredients for a breakthrough in the economics of the new intensive needling method “MicroPunch”.
The ratio of power and energy needed to produce 1 kilogram of material is uniquely low. The number of application sectors is extremely high.
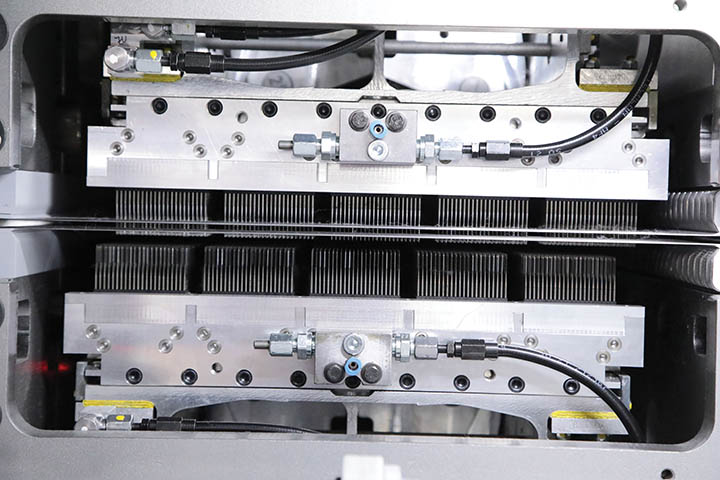
IFJ: Is anyone using the tech now?
Dilo: Since this technology is brand new and presented to the public for the first time at ITMA 2023 in Milan, marketing of this whole technology has only just started, yet already created a lot of interest in many sectors like hygiene, medical, technical, garment, upholstery and automotive.
IFJ: What segments is it best suited for?
Dilo: It is best suited for a weight range of 30 to 120 g/m² and therefore applicable in the sectors as described above with a focus on wipes for personal care, cosmetic pads, household and industrial use.
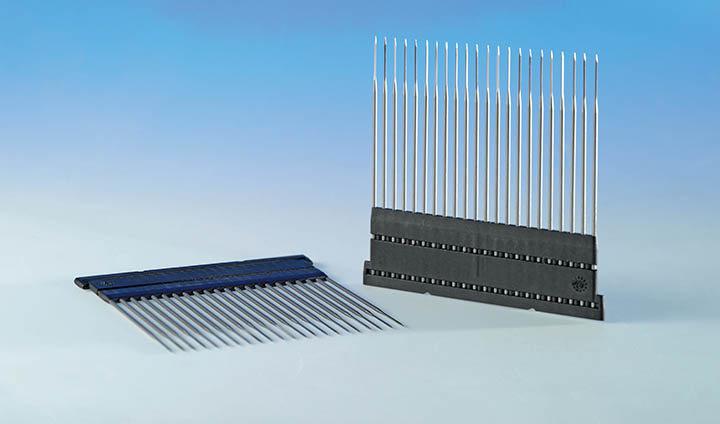
IFJ: How does it work with other Dilo solutions?
Dilo: Dilo is a specialist for complete needling lines. Therefore, a MicroPunch line is offered including fiber preparation with bale opening, blending, fine opening, dosing and air systems engineering for dedusting and pneumatic conveying of fiber flocks to the individual machines. Furthermore, preferably random cards are applicable in order to have a fiber orientation not only in running direction but also in cross direction. This is preferred to allow needles to catch fiber from various directions into the stitching channel in order to consolidate the fleece. After the card the needling units for pre-needling and finish-needling follow either directly after the card exit or when a crosslapper is integrated after a drafting frame. It may result in products with an MD:CD strength ratio of 1. This is a positive feature for many applications. After the needling station the end of line units for winding, longitudinal and cross cutting are added together with packaging or palletizing for roll good.
IFJ: Any other unique details that are interesting for readers to know?
Dilo: Historically, needling as a technology to consolidate staple fiber fleece was not among the so-called modern technologies to attract a whole lot of public awareness or esteem. For many years, it was almost considered as outdated, slow and old-fashioned. Yet, the machine builders have developed this technology which was invented in England in the 19th century to a modern state-of-the-art industrial manufacturing technology for nonwovens which has proven to be highly productive, cost-efficient and energy efficient. The ratio of power and energy needed to produce 1 kilogram of material is uniquely low. The number of application sectors is extremely high at the same time. The needling technology has dominated many nonwoven sectors particularly those at medium to high weights. The MicroPunch approach to penetrate also the low weight area cannot only be considered to reduce the energy consumption but also be viewed as a strategic tool to take a share of the low weight sector and thus provide a sound basis for a positive future of needling in general.