Low-Cost Fibers for a Diverse Range of Commodity Products
Far from being the most glamorous fiber on the market, polyolefin fibers are nevertheless an important material for the technical textiles industry, particularly for absorbent hygiene products.
Compared with other synthetic fibers, such as polyester, polyamide and aramid fibers, polyolefin fibers are often cheaper, mainly due to their lower feedstock costs and more efficient production methods. And although they may not possess certain high-end properties, their low prices have made them popular in many mass-market consumer and industrial applications, such as nonwovens, carpets, synthetic turf and geotextiles.
Polyolefins
Commonly perceived as commodity polymers and largely used in packaging, polyolefins are a group of thermoplastics that include polyethylene (PE) and polypropylene (PP). They are produced by polymerizing ethylene and propylene respectively, which are mainly obtained from oil and natural gas, but can also be derived from renewable resources, such as sugarcane.
The word “olefin” is derived from the French “oléfiant” (oil-forming). An olefin is commonly known as an alkene (ethylene, propylene, isoprenes, butenes, etc.), which is a hydrocarbon containing a carbon-carbon double bond.
Polyolefins are used in a wide range of industrial end-uses, including agriculture, building and construction, consumer goods and appliances, industrial packaging, medical and healthcare, and transportation. According to Plastics Europe, their versatility has made them the most largely used type of plastics, representing almost 50% of the European plastics consumption.
There are basically four types of polyolefins:
- Low-density polyethylene (LDPE), used for cling film, carrier bags, agricultural film, milk carton coatings, electrical cable coating, heavy-duty industrial bags
- Linear low-density polyethylene (LLDPE), used for stretch film, industrial packaging film, thin-walled containers and heavy-duty, medium and small bags;
- High-density polyethylene (HDPE), used for crates and boxes, bottles (for food products, detergents, cosmetics), food containers, toys, petrol tanks, industrial wrapping and film, pipes and housewares;
- Polypropylene (PP), a commodity plastic with the lowest density, used for food packaging, microwave-proof containers, carpet fibers, garden furniture, medical packaging and appliances, luggage, kitchen appliances and pipes.
Compared with PE, PP has superior mechanical properties and thermal resistance but less chemical resistance – it is usually tough and flexible, especially when copolymerized with ethylene.
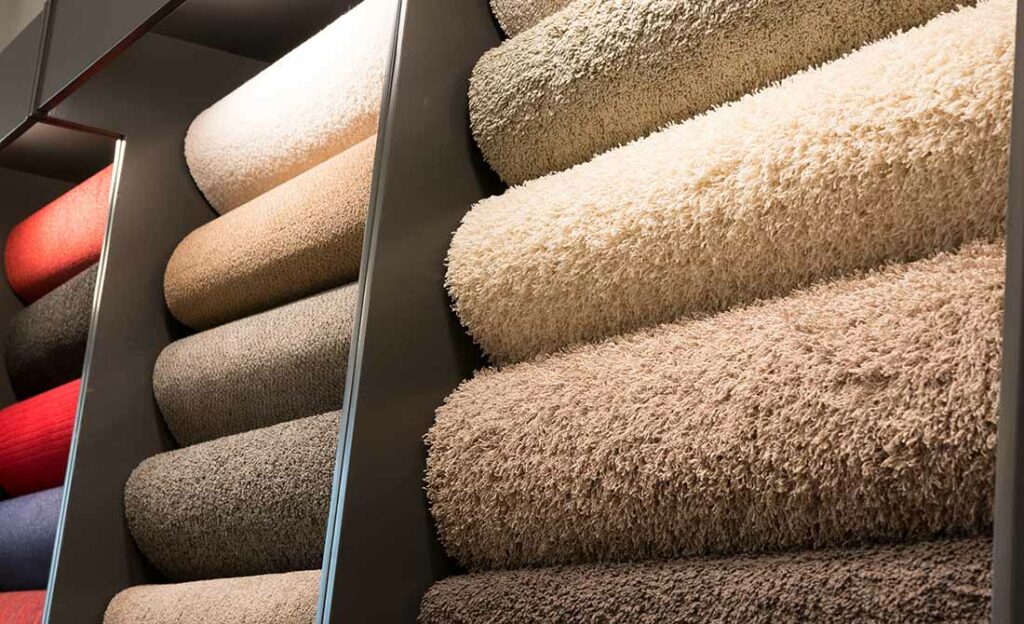
Polyolefin Fibers
Polyolefin fibers, which include spunbond nonwovens, account for just 5-6% of all synthetic fibers consumed worldwide. China is the largest producer, followed by Europe and the Americas.
According to Statista, global production of PP fibers reached 3.1 million tonnes in 2022, a rise of 2.3% compared with 3.03 million tonnes in the previous year. Lucintel estimates that the polyolefin fiber market was valued at US$9.3 billion in 2023, with a growth forecast of 4% annually over the next seven years, to reach an estimated US$26 billion by 2030. Meanwhile, European production of polyolefin fibers was estimated at around 860,000 tonnes in 2023, according to CIRFS, the European Man-Made Fibres Association.
Polyolefin fibers are primarily aliphatic polymeric hydrocarbons that are composed of at least 85% by mass of ethylene, propylene or other olefin units. PP is considered by far the more significant polyolefin fiber than PE.
Polyolefin fibers are durable, chemically resistant, lightweight, economical and functional. They exhibit strong hydrophobicity, strong resistance to sunlight, weather resistance, excellent wicking effect and good chemical resistance, which makes them suitable for consumer products such as carpets and synthetic turf, nonwovens for personal care, sanitary and medical applications, agricultural fabric, construction sheeting, automotive fabric, geotextiles, filtration media and industrial wipes, as well as filter cloths and ropes, with potential application as reinforcement for concrete.
Polyolefins also offer potential as nanofibers and have been used in various high-performance applications, such as oil-water separation, bio-filtration, personal protective equipment, drug delivery and power storage, where a small fiber diameter is essential.
PP and PE are also available as bicomponent fibers, characterized by their low melting points and low specific density, especially for use as a mechanical binder in nonwoven products.
Polyethylene Fibers
Polyolefin monofilament extruded from LDPE was the first polyolefin textile fiber developed in 1930s. However, these LDPE fibers gained limited commercial acceptance owing to their coarseness and poor mechanical properties, as the fibers were derived from the low molecular mass polymer.
Some HDPE fibers and ribbons were commercialized at that time, although their use was restricted owing to their low resilience, poor softening range and high deformation against stress (creep). Nevertheless, these coarse monofilament/ribbon-like polyolefin fibers were widely utilized as outdoor fabrics, protective clothing, filter fabrics, ropes, webbing, nets, cordage, conveyor belting and seamless medical tubes.
Meanwhile, commercial ultra-high molecular weight polyethylene (UHMWPE) fibers were developed in the mid-1980s, with fibers such as Dyneema (DSM) and Spectra (Honeywell) finding use in high-strength demanding applications, including antiballistic fabrics, deep-sea mooring ropes and braids, and medical devices.
Polypropene Fibers
PP was first discovered in 1951 and commercially appeared as a superior plastic material in 1957, with the first PP monofilaments for textiles appearing in the market in the late 1950s. PP in the form of staple fibers and multifilament began to be produced in small quantities in the early 1960s in Italy, the UK and the US; continuous PP tape yarns (ribbon) with high strength began production from extruded film in the late 1960s.
By the early 1970s, the growth of PP tape and nonwoven fabrics had virtually eliminated the use of traditional jute yarn and fabrics in carpet backing and sacking cloth, with many cords, ropes and twines prepared from natural fiber spun yarn also being substituted by PP tape yarns.
Capacity Additions
In 2023, PP fibers and raffia accounted for 36% of total PP demand, while PE fibers and raffia accounted for less than 3% of total PE demand.
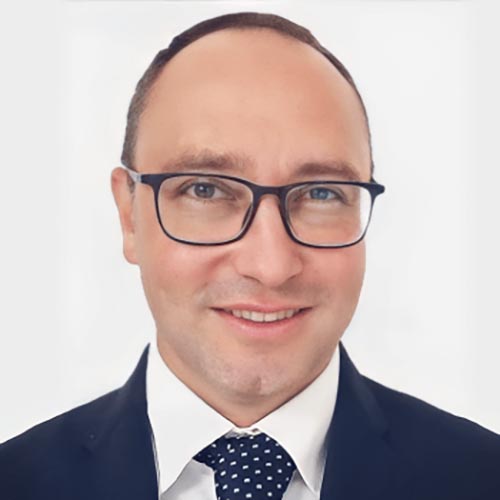
According to Fabrizio Galié, associate director of Chemical Market Analytics, an oversupply of PP capacity was seen in 2022–2024 with 13.6 million tonnes in excess of demand, with a further 7 million tonnes of capacity in excess of demand forecast for 2026–2028. This will inhibit operating rate recovery, which is estimated at below 80% by the end of the decade, he said at a CIRFS webinar earlier this year.
Meanwhile, PE supplies will continue to lengthen in the short–medium term, with global operating rates likely to be challenging for the LLDPE and HDPE sectors up to 2030.
As a result of weak economic fundamentals and the large-scale capacity expansion cycle leading to surplus capacity, Galié expects lower demand for polyolefins over the medium term, with a focus on operational efficiency and cost optimization and rationalization for high-cost producers.
Carpet Recycling Initiatives
The European Union (EU) is the second largest carpet market globally with production worth around €4 billion in 2022. However, end-of-life carpet is a bulky waste stream with its own challenges for disposal and/or recycling.
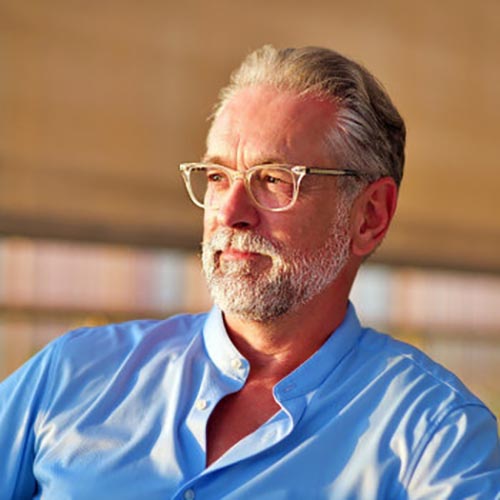
Dr. Hans-Peter Breuer, managing director of both the European Carpet and Rug Association (ECRA), based in Brussels, Belgium, and the Gemeinschaft umweltfreundlicher Teppichboden (GUT), based in Aachen, Germany, estimated the total EU market volume (production + imports) of carpets and textile floorcoverings in 2022 at around 961 million m2, valued at €5.4 billion.
Of the 880 million m2 of floorcoverings valued at €4.2 billion that were consumed in the EU in 2022, the main products were tufted carpets (302 million m2 worth €2.2 billion) and woven carpets (248 million m2 worth €807 million).
PP was the major fiber used in the EU tufted carpets market in 2022 with a 44% share (in square meters) followed by polyamide with 37%.
With a lifetime of 8-25 years for wall-to-wall carpets, depending on the carpet construction, floorcoverings ultimately produce a lot of waste at the end of their life, estimated at around 800 million m2 a year in the EU by 2030, said Breuer.
He outlined several recycling concepts at the CIRFS webinar, including PolySep, which involves the separation of polymers from composite structures such as carpets, and a number of other initiatives from European yarn and carpet producers.
Synthetic Turf Developments
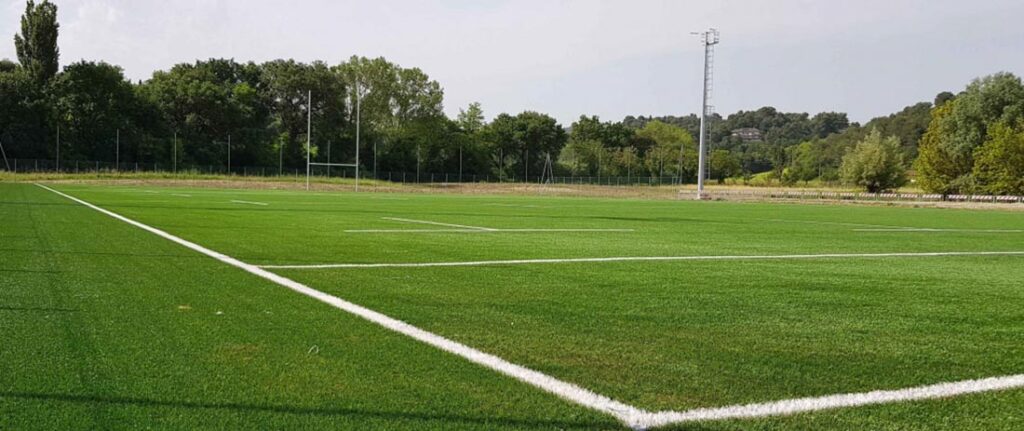
Synthetic turf for sports and landscaping applications is another significant consumer of polyolefin fibers within the floorcoverings sector. Stefan Diderich, director general/chief executive officer of ESTC, the EMEA Synthetic Turf Council, noted that the first synthetic turf sports field (for hockey) in the 1960s was manufactured from polyamide (the first major installation was at the Houston Astrodome in 1966), with PP being introduced in the 1970s and PE in the 1990s.
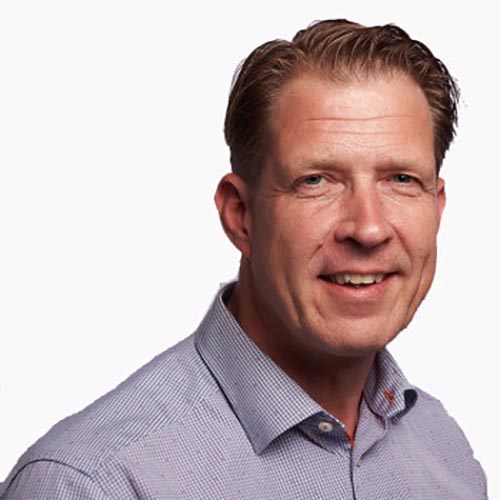
Today, the main construction for sports fields is 90% PE/10% PP for the face yarns and 90% PP/10% other fibers for the backing, with shock-pads made of PE/polyurethane foam. Meanwhile, landscaping turf represents 55% of the EMEA (Europe, Middle East and Africa) market by volume.
The EMEA synthetic turf industry is also looking to circularity with a drive towards single polymer turf systems, which would enable clean lawns and sports fields to be recycled into other alternative PE products as well as new turf. At the same time, ESTC members are starting to manufacture new synthetic turf using yarns made from plastic that originates from other sectors.
Diderich mentioned two initiatives currently on the synthetic turf market that use recycled content, such as a recycled fiber core with a virgin fiber outer layer. The use of biobased and/or biodegradable polymers are also being examined.
The industry is also working to increase the number of carpet recycling facilities for end-of-life processing (the 11 current recycling facilities across Europe have a collective processing capacity of more than 4.3 million m2 – equivalent to 500,000 full-size football pitches).
The release of microplastics from fiber wear and polymeric infill is also under scrutiny. The synthetic turf industry says it is committed to mitigating concerns about microplastic contamination in both the sports and landscaping sectors.