Ahlstrom Introduces a New Dual-Layer Filtration Technology for Longer Lifetime and Reduced Size of Air Intake Filters
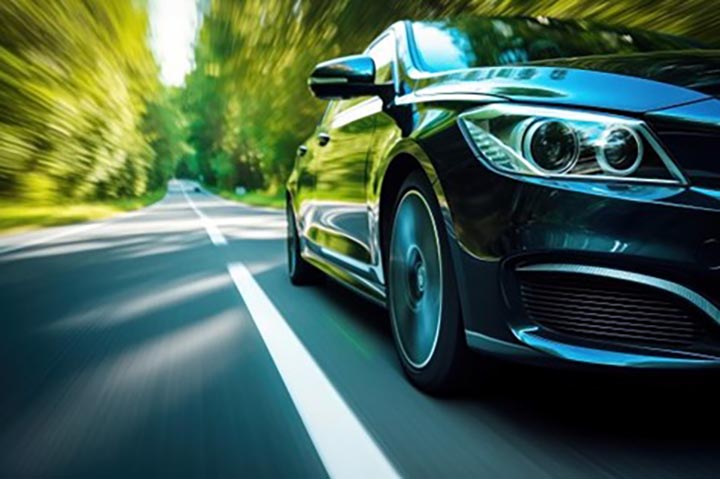
The quality of air intake is a substantial factor in the overall performance of today’s engines. An efficient air intake filtration supports optimal operation, preventing particulate contaminants from entering the engine while optimizing fuel consumption and reducing engine wear. In this context, a longer filter lifetime is a key benefit as it ensures continuous removal of contaminants while extending service intervals and minimizing environmental impact.
Ahlstrom introduces a new dual-layer filter media technology, available globally, that represents a leap forward in filtration and is a perfect solution to comply with future market needs. The dual-layer design offers up to double dust holding capacity compared to the single-layer design, as each layer serves a distinct purpose to optimize the overall retention of particles in the depth of the material.
In automotive engine air intake applications, the technology has proven to extend by over 50% the filter lifetime in the same configuration. It also offers the possibility to reduce both size and weight of the filter element in vehicles where these parameters are important.
Dual-layer filter materials are designed to comply with current and future engine air intake specifications, including fuel cells. The media can be customized with flame retardancy properties to increase safety in use without compromising performance. The technology is highly adaptable and can be extended to filter air and liquid in many other transportation and industrial applications.
“Leveraging our advanced manufacturing processes and know-how, Ahlstrom’s dual-layer filter media are setting new standards for filtration performance on the market,” says Tamara Quatrano, VP of R&D and Product Development for the Filtration division. “They can be adapted to different environments, and they not only purify and protect but also contribute to a more sustainable future,” she continues.
For more information, please contact Tamara Quatrano, Vice President, R&D and Product
Development, Filtration, tamara.quatrano@ahlstrom.com.
Americhem Introduces nShield® for Textiles and Synthetic Fibers
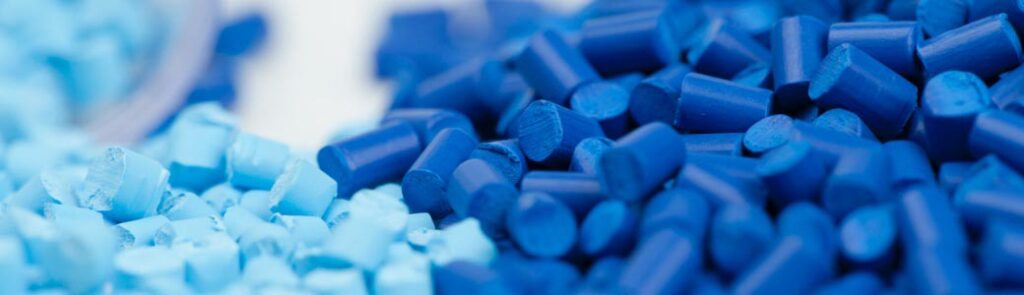
Americhem, Inc., a global leader in innovative polymer solutions, is advancing its global sustainability campaign with the launch of nShield®, a natural antimicrobial and odor control treatment for textiles and other synthetic fibers. nShield® is formulated as an antimicrobial masterbatch containing a plant-based, renewable-sourced solution. Delivered in pellet form, it is specially designed for synthetic fiber applications such as textiles, carpets, and nonwovens. The masterbatch incorporates natural essential oil into a carrier system, ensuring protection of the active substance during heat processing. This novel approach aids fiber manufacturers in establishing a sustainable supply chain, enhancing environmental stewardship, meeting regulatory obligations, and cultivating a more adaptable and intelligent supply network.
Peppermint oil, a key ingredient in nShield®, provides a natural, renewable, and sustainable alternative to the harsh chemicals traditionally used in textiles. This substitution not only enhances ingredient sustainability but also preserves fabric longevity while reducing environmental impact. By unlocking antimicrobial and odor control properties within textiles, Americhem’s peppermint oil-based additive reduces the need for frequent wash cycles, conserving energy and preserving water. nShield® has been proven to inhibit microbial growth and provide longer-lasting odor control for up to 50 washes.
The masterbatch is suitable for synthetic fibers such as PET, nylon, and polypropylene. It has successfully passed antibacterial testing standards, including ISO 20743, JIS L 1902, AATCC 100, and GB/T 20994. Moreover, nShield® complies with EPA and BPR regulatory requirements, and its active ingredient (peppermint extract) is fully traceable.
With high thermal stability, excellent dispersion, and ecological friendliness, nShield® sets new industry benchmarks for performance and sustainability in antimicrobial masterbatches. Its ability to provide superior antimicrobial protection while maintaining environmental integrity makes it a game-changer in the realm of sustainable polymer solutions. By introducing this plant-based innovation, Americhem helps fiber manufacturers optimize their supply chains for sustainability and regulatory compliance while advancing environmental stewardship.
The addition of nShield® to Americhem’s product portfolio demonstrates the company’s commitment to driving sustainable innovation in polymer solutions. Their continued efforts aim to establish a more resilient and intelligent supply network, enhancing adaptability to shifting consumer demands and regulatory landscapes.
Please contact Robert Baldy, Business Director Fibers and Packaging at rbaldy@americhem.com for more information.
ANDRITZ at the Forefront in Sustainable Nonwoven Products and Solutions
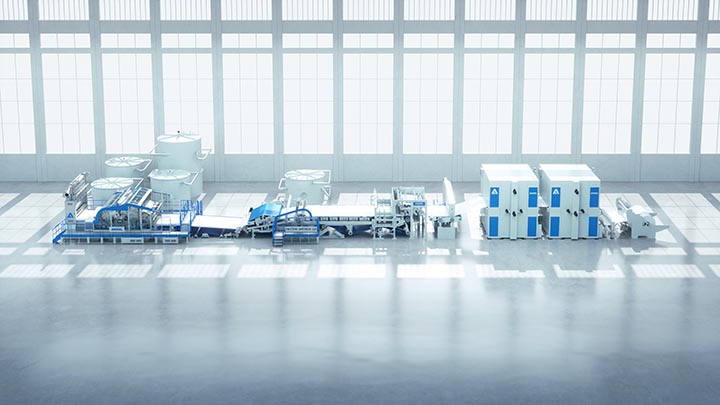
When speaking of our environment, climate crisis, environmental pollution and resource scarcity are three of the most urgent challenges of our time. And time is the crucial factor here. To create a better future for our children and grandchildren, we must build a new and greener economy. We at ANDRITZ are doing everything to drive this change: We enable our customers to make the world a greener place with our sustainable products and solutions. To underline this, we have just recently announced our “FOR THE CHANGE” initiative, which combines sustainable technologies and solutions, making them visible to the market.
One great example is the ANDRITZ nonwoven processes for biodegradable wipes. It includes all technologies available on the market, like AirlaceTM, spunlace, WetlaceTM and WetlaceTM CP, with one goal in mind: reduction and elimination of plastic components, while maintaining the high-quality of the desired product properties.
ANDRITZ complete production processes for this kind of wipes can perfectly handle a blend of fibers, such as cellulose, viscose, lyocell, cotton, hemp, bamboo, or linen.
With the latest acquisition of Dan-Web in Denmark, ANDRITZ completes this range with the airlaid/AirlaceTM technology. Airlaid forming can perfectly process short fibers, like wood pulp, which allows to manufacture products with high content of natural raw material including biodegradable and flushable wipes. By combining this with the hydroentanglement technology, plastic fibers and chemical additives can be avoided.
Moreover, ANDRITZ also has the expertise to offer the full spectrum of upgrades and retrofits for existing production lines. For instance, spunlace producers can upgrade their lines with a wetlaid or airlaid forming unit to open new business opportunities and achieve greater flexibility in terms of product variants. ANDRITZ advises its customers on the selection of the right technology and the most suitable upgrade according to their process, constraints, and future requirements.
Another market example is the increasing demand for flushable, plastic-free wipes and their technologies. In recent years, the threat of plastic pollution and stricter regulations from governments and industry associations has increased. The ANDRITZ WetlaceTM technology produces a 100% sustainable wipe that precisely meets customer needs and flushability guidelines and supports the strong move away from plastic and synthetic materials.
ANDRITZ Textile Recycling Enters a New Era
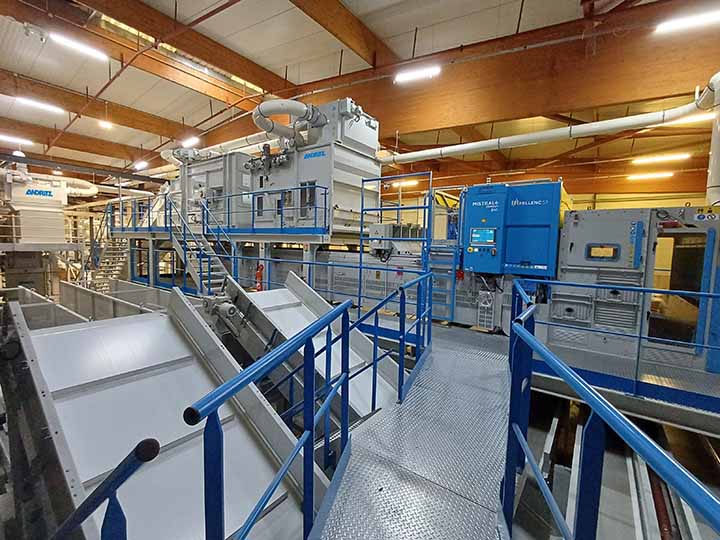
Textile recycling in Europe is now evolving with a sense of urgency as it becomes clear that the discarding of garments and apparels of clothing represent a major threat to the environment. Governments are now catching up with the threat; in Europe, the latest regulations mean that the whole fashion and clothing industry has to completely rethink how textiles are managed at end-of-life. ANDRITZ has been aware of the situation for some time and has been working on solutions and innovations to counter the challenge. In its latest move, the company has partnered with textile experts in France to launch a major revolution in automated sorting for further recycling into new products.
It is estimated that around 7.5 million tons of textiles are discarded in Europe every year. Currently only 2.2 tons are collected, with the rest going to landfill or incineration. Due to new regulations, the volume of textiles collected is estimated to rise by 4.5 – 7.2 million tons by 2030.
“The new regulations mean that by 2025, all European countries will no longer be able to dispense of clothing by landfill or burning,” says Alexandre Butte, General Manager, ANDRITZ Laroche. “All of these countries will have to have collection systems in place by that time.”
Addressing the Challenges
To address this dramatic upscale of regulations, French startup company, Nouvelles Fibres Textiles, has recently launched a revolutionary new industrial-scale line in Amplepuis (central France). This unique line is designed to speedily and autonomously sort discarded garments by color and composition utilizing the very latest in digital and infrared technology. The entire line has been supplied by ANDRITZ, with infrared technology supplied by French company Pellenc ST, also a partner in the new venture.
Added to the sorting of garments, the line will remove non-textile parts of garments including zippers and buttons and start the first stage of tearing. The remaining sorted garments are then sent on for further processing by textile producers for further tearing and on to either spinning for the production of new products, including nonwovens and composite materials.
The goal of Nouvelles Fibres Textiles is to trigger the circular economy at an industrial scale when it comes to the sorting and recycling of textiles in France. The technology used in the new demonstration plant, supplied by the partners, ANDRITZ and Pellenc ST, represents the missing link to the industrialization of textile recycling.
Textile Sorting: A Mammoth Task for All Partners
Although the recycling of textiles is nothing new in the industry, the main challenge has been the automating of the sorting process. As can be imagined, this sorting is a demanding task, simply because of the range of composition, colors and sizes involved. Nouvelles Fibres Textiles, decided to take on this mammoth task, but it needed help; and this is where ANDRITZ, with its vast experience in the recycling industry and the building of complete manufacturing lines, joined the challenge, together with specialist
provider of infrared sensors for sorting, Pellenc ST. All four companies are now in partnership on the project which will see the line running on 60% commercial operations with 40% of time set aside for R&D.
The plant was launched at the end of 2023 to an audience of guests from all over Europe, and included politicians, industry players, universities, and textile technical institutions. The event included a demonstration of the line, as well as speeches from the partners of the project and a panel discussion featuring major customers of the textile industry in France, including the French supermarket giant Auchan.
The First Step in a Long Journey
The new automated textile sorting and recycling plant represents the first step in a journey that will see millions of tons discarded textiles collected, sorted and recycled for making new products in the future. As a signal to the opportunities ahead, Nouvelles Fibres Textiles has already laid the foundations for a full-scale recovered textile preparation plant which will have an annual capacity of 25,000 tons of post-consumer textile waste planned for start-up in 2025.
Benoit Rombaut, Technology Director, ANDRITZ Laroche, says, “The line is the first and important milestone of a long journey. In France, due to tightening regulations and the increased collection rate of 60% of all textiles manufactured, there is now around 240,000 tons of textiles for recycling. In three years’ time this will raise to 300,000 tons. This means that we need at least another 12 high-capacity sorting and recycling lines to cope with the demand.
Andritz One-Stop-Shop for Textile Circularity
ANDRITZ has huge experience in the recycling of textiles, with both mechanical and chemical solutions. Now with its expertise in sorting, complete lines from collected textiles to full recycling is possible, representing a revolution in circularity for the industry.
“At ANDRITZ we are completing our goal with the new line,” says Butte. “We can now provide a one-stop-shop for our customers and provide complete lines for textile recycling from sorting to mechanical or chemical recycling.”
BASF Acrodur® Range of Products for Sustainable Solutions for Nonwovens
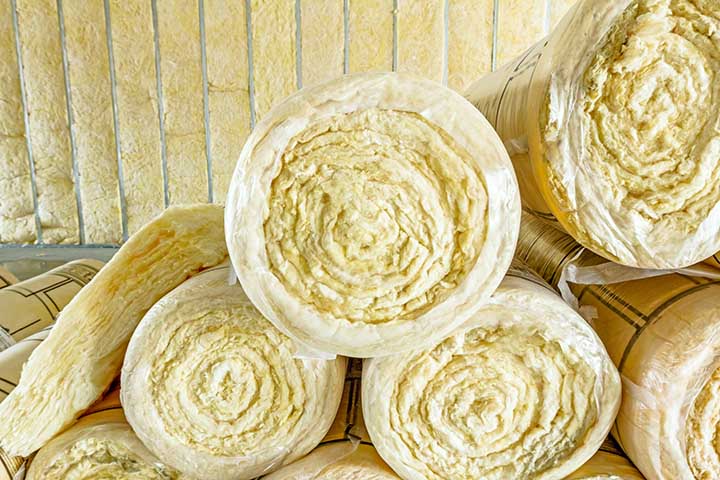
BASF’s Acrodur® portfolio offers a range of high-performance products that serve as innovative and low-emission alternatives to conventional formaldehyde-based resins, such as phenol, melamine, and urea resins. Acrodur products have outstanding wet and dry strength, excellent adhesive properties, and the ability to reinforce natural, glass, and synthetic nonwovens, as well as cork and other particles.
Acrodur products are water-based, which eliminates the need for organic solvents, reducing VOC emissions and environmental impact. Unlike traditional formaldehyde-based resins, Acrodur does not release any toxic or hazardous substances during the cross-linking process. The only by-product is water, making it a safe and environmentally friendly choice. These factors contribute to a healthier and safer environment for both workers and end-users.
Furthermore, Acrodur offers high thermomechanical stability after curing, making it suitable for applications that require durability and resistance to high temperatures. It also exhibits excellent compatibility with flame retardants, pigments, and fillers, allowing for versatile customization options. The water-based nature of Acrodur makes it compatible with various application methods, including foulard, curtain-coating, blow-line impregnation, and spray application.
Acrodur utilizes thermosetting resin technology and is B-stage curable, giving producers flexibility with manufacturing timing. Its outstanding binder properties enable the incorporation of a high percentage of natural fibers in components, contributing to the development of sustainable and lightweight products.
BASF’s North American portfolio contains three products that span multiple fiber types and application needs. Acrodur PLUS 2580 is a solution polymer that provides excellent heat resistance and stiffness with very low color. The high solid composition also helps contribute to lower transportation costs. Acrodur 950 L is also a solution polymer that provides excellent heat resistance and stiffness and can be used in a variety of glass fiber applications. Finally, Acrodur DS 3515 is a dispersion polymer that provides excellent thermal stability, flex modulus, and hydrophobicity.
In summary, BASF’s Acrodur products are sustainable solutions for a variety of nonwovens. Its water-based and formaldehyde-free composition, combined with its outstanding strength properties and application versatility, make it a superior alternative to formaldehyde-based resins. Acrodur not only improves the properties of the finished product but also ensures safe working conditions during production. By choosing Acrodur, manufacturers can enhance sustainability claims, reduce emissions, and contribute to healthier indoor environments.
Bast Fibre Tech (BFT) Scales Up Sero™ Regenerative Fibres to Meet Growing Demand for More Sustainable Materials
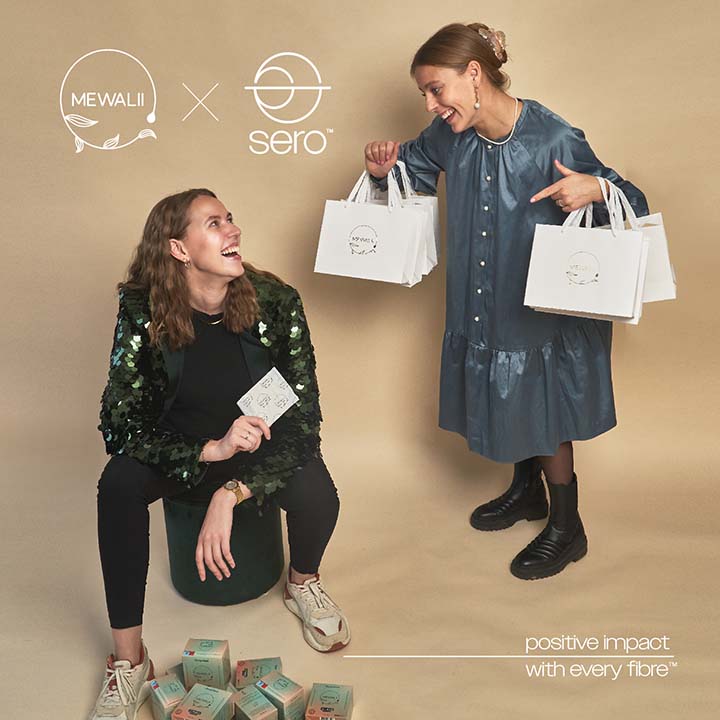
The textile industry faces a critical challenge to reach its climate goals, with raw materials contributing two-thirds of its harmful climate impact, according to Quantis Environmental Sustainability Consultancy. To align with ESG targets and anticipated legislation, companies must transition to lower-impact raw materials. To address this need, regenerative material systems company BFT produces Sero™ natural performance fibres at an industrial scale at their two wholly owned mills in Europe and North America.
Sero™ Natural Fibres: Rooted in Regenerative Practices
The Sero™ materials portfolio encompasses a range of natural, low-impact fibres, including hemp, cotton, and flax. Hemp cultivation plays a vital role in regenerative agriculture as it sequesters large amounts of carbon, improves soil health, and supports ecosystem diversity. Hemp significantly reduces the carbon footprint of Sero™ products and facilitates the creation of nature-positive fabrics. Noel Hall, Executive Chair of BFT, emphasizes, “Sero™ fibres are a Climate+ solution, meaning our partners not only address their decarbonization goals but also their plastics reduction and forest preservation targets.”
Achieving Performance Excellence with Sero™ Regenerative Fibres
While Sero™ regenerative fibres are natural, they are engineered as technical performance fibres that match or exceed the properties of the materials they replace. Their strength and versatility ensure products meet desired standards without compromising softness, absorbency, breathability, or durability.
To drive widespread adoption, regenerative fibres must be designed as a drop-in solution for existing nonwoven and textile platforms. Manufacturers appreciate the cost-effectiveness and ease of production with Sero™ fibres for eco-friendly everyday care and hygiene products, apparel, and home furnishings. The inherent properties of Sero™ fibres makes them an excellent blending partner that adds unique performance benefits.
Collaborating for Positive Impact: Sero™ Partners with Period Care Brands
BFT collaborates closely with fabric industry partners to create circular, nature-positive products. Noel says: “Partners like Hempress Hygienics (US) and Mewalii (DK) are using Sero™ fibres in their products to revolutionize the femcare industry. Together, we make healthy and eco-friendly period choices accessible to the mass market.” Mewalii’s hemp period pads are made with 75% Sero™ regenerative hemp fibres, offering a comfortable, absorbent, and climate-friendly option that is better for both people and the environment.
“With Sero™, let’s collectively shape the textile future with fibres that give back to nature and humanity, and begin to repair the damage done to our planet” Noel closes.
Join us in creating regenerative products and learn more about Sero™ fibres at Serofibre.com.
Berry Global’s Chicopee rMicrofibre Made from 100% Recycled Materials
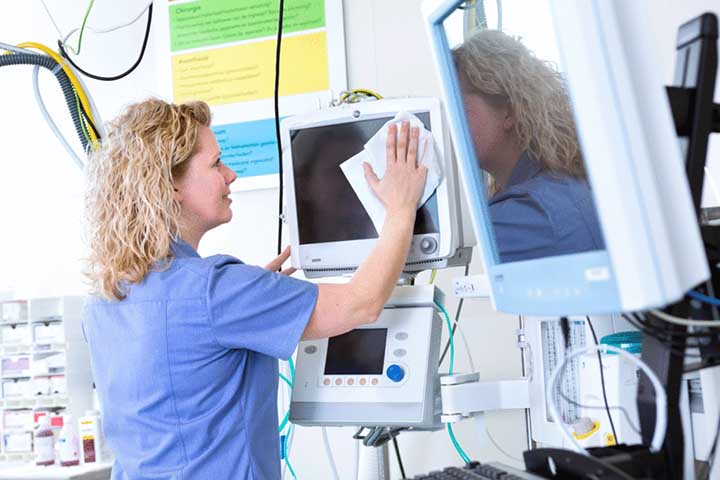
Made from 100% recycled materials, Berry Global’s Chicopee rMicrofibre stands as a groundbreaking solution in the nonwoven wiping industry, being the first and only wipe made entirely from 100% post-industrial recycled (PIR) and post-consumer recycled (PCR) fibers. Reducing the carbon footprint of the wipe and giving new life to recycled materials, rMicrofibre is unlike alternatives available on the market. Often, these products do not contain 100% recycled materials and lack pure microfiber, including blends with viscose that compromise performance. rMicrofibre remains unrivalled, ensuring sustainable and superior cleaning. This innovation aligns perfectly with sustainability goals, supporting the EU Green Deal’s chemical strategy to cut greenhouse gas emissions by at least 55% by 2030 through reduced chemical usage while maximizing cleaning efficacy and sustainable cleaning solutions.
Certified to achieve an astonishing 99.97% bacteria removal using just water, rMicrofibre acts as a powerful bacteria magnet, trapping unseen bacteria and dirt in its fibers. By splitting fibers into microfibers > 80% finer than reusable alternatives, rMicrofibre ensures superior surface contact, magnetically removing bacteria and dirt that may otherwise be missed. This not only guarantees exceptional cleaning results but also minimizes the risk of cross-contamination in high-risk environments.
With touchscreens becoming ubiquitous in modern facilities, the demand for effective cleaning solutions is higher than ever. rMicrofibre wipes excel in delivering streak-free cleaning on glass, stainless steel, mirrors, and touchscreens, effectively removing greasy fingerprints and reducing the risk of bacteria transfer. Their 100% microfibre composition allows for enhanced absorption, enabling the removal of up to 20% more natural oils compared to other wipes, making them ideal for phones, tablets, and monitors.
Designed for short-term use to mitigate the risk of cross-contamination, rMicrofibre wipes ensure maximum hygiene without compromising on practicality. Unlike reusable alternatives, which have been shown to retain dangerous levels of bacteria even after laundering , rMicrofibre offers a cost-effective and environmentally friendly solution to maintain cleanliness in high-traffic areas which are prone to cross-contamination. This includes workspaces, healthcare facilities, airports, hotels, and restaurants, targeting surfaces such as door handles, touchscreens, monitors, glass, and stainless steel. By reducing laundry requirements and maximizing cleaning efficacy, these wipes provide a cleaner and safer environment for users in high-traffic and traffic areas.
The New BW Converting VERTIS Series Converting Machinery: Sustainability is Part of Our Innovation
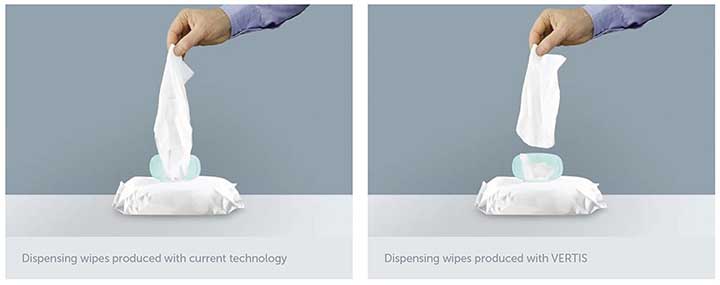
In today’s rapidly evolving consumer landscape, sustainability has become a paramount concern across industries, including the wipes market. Heightened environmental awareness and a surge in consumer demand for eco-friendly products have posed significant challenges for companies. The pressure to innovate and offer sustainable solutions that meet both performance and environmental criteria has never been greater.
As businesses adapt to these changing consumer preferences, the importance of sustainability in the wipes market cannot be overstated. Companies are proactively embracing sustainable practices to differentiate themselves in a competitive market while also contributing to broader environmental goals.
Our Group is no exception. The Hygiene Division of BW Converting has developed the new VERTIS interfolder for wet wipes, which not only meets consumer expectations but also addresses environmental concerns head-on.
Market analysis reveals several key trends driving the wipes market. The increasing popularity of single-use wet wipes projects significant growth, but it also presents environmental and economic challenges. Consumers often flush wipes that are not compatible with municipal sewer systems, leading to poor environmental outcomes. Non-renewable plastics and materials that do not biodegrade under disposal conditions further exacerbate these challenges, prompting the need for tough regulations. Innovative solutions are required to address the main environmental and technical challenges associated with flushable and non-flushable wipes.
Consumers’ quality perception and requirements are enduring and demanding. Disposable single-use wipes present environmental, technical, and social challenges. In response, our company has developed cutting-edge technology to improve the quality and sustainability of wipes.
Our new converting technology VERTIS enhances the final product quality and consumer experience. With features such as a small footprint, zero-speed auto-splice system, and precise add-on lotion system, the VERTIS sets a new standard for hygienic and efficient wipes production.
The benefits of our technology are manifold. Its unique design results in a superior user dispensing experience, with better pop-up and folding capabilities. Simplified operation, small footprint, and Smart Touch© technology make it easy to use and maintain. Moreover, our VERTIS interfolder stand is compatible with biodegradable materials, reducing environmental impact. With its fully servo system, it ensures durability and flexibility, capable of recording data and settings for future machine learning and repeatability.
For more information about our innovative solution and how it can benefit your business, please contact us at nonwovens@bwconverting. com. We are committed to driving sustainability in the wipes market and invite you to join us in this journey towards a greener future.
Exposome Partners with Industry in Effective Waste Water Treatment & Industrial Air Pollution Abatement
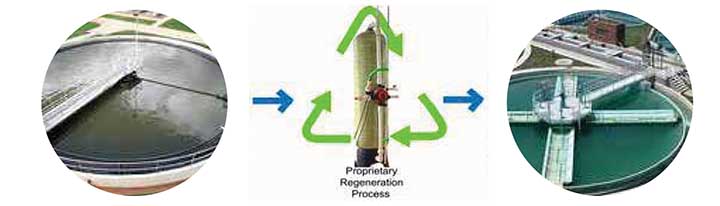
Exposome Pvt. Ltd. is a material chemistry provider – enabling various industries achieve their sustainability and Net Zero goals. With our cost-effective and energy-conserving filtration solutions we are enabling industries in re-using and recycling their wastewater effectively and/or meeting stringent discharge norms.
Our air filtration molecular filters enable a safe, healthy and breathable environment for the people working in the heavily polluted industrial areas.
Regenerable Molecular Filters
We manufacture regenerable, hence re-usable effluent treatment media for waste water and air. Based on the principle of absorption, adsorption, and redox, our filtration media for waste water efficiently removes COD, recalcitrant COD, BOD, colour, odour, hardness, etc.
We also have specialised filtration media which can selectively remove aluminium, heavy metals (such as zinc, chromium, iron, cadmium and copper), cyanide, silica and total ammonical nitrogen from waste water. Our molecular filters for air are very efficient in removing commonly seen air pollutants across various industries: SOX, NOX, VOC, H2S, odour, humidity etc.
Why are our filtration solutions more sustainable than the rest?
- Because our molecular filters are regenerable on-site, operating costs are significantly low.
- As it requires a simple flow-through mode, electricity consumption is nil or negligible.
- With 60-90% reduction in COD and other parameters, industries are able to reuse the water in their facilities hence enabling zero liquid discharge plants.
Our raw materials are natural in origin and biodegradable.
Email us at info@exposome.in or visit www.exposome.in.
Kelheim Fibres Unveils the Pivotal Role of Fibre Behavior in Tampons and Nonwovens
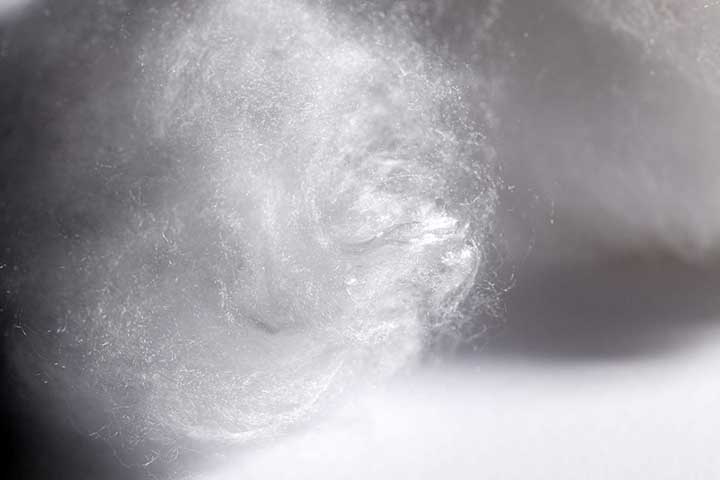
Kelheim Fibres, a leading manufacturer of specialty viscose fibres, recently unveiled their latest
findings at this year’s Cellulose Fibres Conference. Led by Dr. Ingo Bernt, Group Leader of Fibre & Appli-
cation Development at Kelheim Fibres, and in collaboration with Dr. Thomas Harter from Graz University of Technology, the study provided invaluable insights into the complex relationship between the geometric structure of viscose fibres and their liquid absorption capacity, particularly in the context of tampon applications.
For decades, Kelheim Fibres has been a trusted partner in the tampon industry, supplying specialty fibres pivotal for tampon performance. Modified fibre cross-sections often serve as the cornerstone for the distinctive functionalities of Kelheim’s specialty fibres. A prime illustration is the renowned trilobal Galaxy®, distinguished by its Y-shaped cross-section, boasting up to 30% higher absorption capacity than standard viscose fibres and serving as a flagship product in tampon manufacturing.
The latest research has shed light on the mechanisms governing liquid absorption and retention in tampons. The study compared the efficacy of two commonly used tampon viscose fibre types: round standard fibres and trilobal fibres. Tampons crafted from trilobal Galaxy® fibres demonstrate markedly superior absorption capacity compared to those made from round fibres, with trilobal fibres also providing higher water retention capacity. This could be attributed to the greater specific surface area of trilobal fibres, allowing liquid accumulation along the three legs of the Y-shaped cross-section, alongside their higher fibre porosity relative to round fibres. However, fibre swelling alone cannot entirely account for the augmented tampon absorption, as it contributes only about 11-13% to the total liquid uptake of tampons.
The research findings underscore the pivotal role of fibre behavior within tampons or nonwoven fabrics. Here, the trilobal Galaxy® fosters the formation and sustenance of a more voluminous and expansive network, ensuring a larger volume is accessible for liquid absorption, thereby enhancing the overall performance of the end product.
Dr. Ingo Bernt emphasizes the broader implications of the study results, extending beyond tampon applications. The remarkable absorption capacity of Galaxy® fibres transcends various absorbent products, offering novel solutions across diverse industries. Particularly amidst the increasing demand sustainable and environmentally friendly alternatives, this aspect this aspect is highly relevant. It underscores the potential of bio-based and biodegradable fibres to substitute numerous synthetic solutions without compromising performance.
NeenahPure™ – GESSNER’s Sustainable Solutions for Pocket Filters

Our world without pocket filters would be characterized by a sharp deterioration in air quality within industrial settings and surrounding areas. Without these filters, production facilities and industrial areas would be much more contaminated with harmful particles and pollutants, which would not only endanger the health of employees and residents but would also have a serious environmental impact.
In such a scenario, we could expect more frequent and more severe pollution, which would have a negative impact on ecosystems, soils, water bodies and air quality. This could lead to a rise in disasters affecting nature and health issues, as people and animals would be exposed to more toxic substances.
Pocket filters are not only a technological innovation but also a significant contribution to the preservation of our planet and sustainable practices.
With NeenahPure,™ you can make a positive impact on our environment. Our meltblown media for pleated and pocket filter applications are covering all efficiencies from ePM10 50% to ePM1 80% as per ISO 16890 standards, and M5-F9 according to EN779:2012. The combination of fine and coarse fibers ensures high separation efficiencies with low pressure drop and a good dust holding capacity.
Let’s continue to invest together in innovative technologies that help make our environment safer, cleaner & more healthier!
For more information visit NeenahPure™ Bag Filter Media – Enhance Indoor Air Quality at https://www.gessner-filtration.com.
Naia™ from Eastman: Where Fashion & Environmental Responsibility Meet
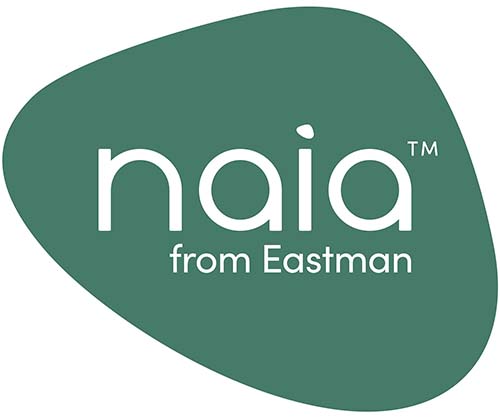
The textile industry has been increasingly focused on circular materials as a solution to combat the ongoing increase in waste pollution. In a world where fashion is still mostly looked at through the lens of speed, Eastman creates value from hard-to-recycle waste that would otherwise go into landfills, thus investing in sustainable innovation.
A perfect example of this is Naia™ Renew ES, a game changer for the industry: it’s a solution that blends fashion and environmental responsibility, made from 40% certified recycled waste material, 20% certified recycled cellulose and 40% sustainably sourced wood pulp. It is Eastman’s fiber with the most recycled content yet, first launched for a pilot project in collaboration with Patagonia in September 2022.
Early this year at Première Vision Paris, Naia™ announced the launch of Naia™ Renew ES at scale, as the perfect solution for brands that want to enhance their sustainable story. One valuable example is the renowned American brand Reformation, which has presented three gowns featuring Naia™ Renew ES in its latest bridal collection. This goes to show the versatility that this fiber can have in the fashion world, with applications that range from activewear to formal and bridal clothing. “Like silk but better” is the brand promise, which has chosen this yarn as a silk alternative due to its inherent properties – elegant drape, silky soft hand and luxurious luster – with all the benefits of circularity.
The high percentage of the recycled content in Naia™ Renew ES is possible through Eastman’s molecular recycling technology, which breaks down waste into its molecular building blocks. This process produces a fully traceable and biodegradable cellulosic fiber, proven by a series of certifications that highlight the fiber’s biodegradable and compostable nature (such as the TÜV Austria one).
Unlike other cellulose-based yarns and fibers, Naia™ Renew ES requires fewer virgin materials to make an eco-friendly alternative to natural or man-made fibers, ensuring elegance, comfort and high performance without compromising on sustainability. In the words of Carolina Sister Cohn, Global Marketing Leader for Eastman’s textiles division “…we’re proud to offer a 60% recycled content fiber at scale for the fashion market. With Naia™ Renew ES, we offer a sustainable and circular solution that meets the demands of both fashion and environmental responsibility, and we’re making significant strides in transforming the fashion industry and inspiring others to embrace sustainability as a design decision.”
Furthermore, Naia™ Renew ES received GRS certification in December 2023. This certifies the fiber’s recycled content, chain of custody, social and environmental practices, and chemical restrictions. Earned after an independent third-party audit, GRS certification provides increased traceability, environmental principles, social requirements, chemical content and labeling. The certification aids in building brand trustworthiness around the world, fostering relationships with more customers and collaborators around the world and strengthening Naia™’s expansion plans.
Eastman’s technologies are driving a revolution in materials – from a linear life cycle that results in waste to a circular life cycle that keeps materials in use, creates sustainable value, and enhances quality of life.
Learn more at www.eastman.com.
Plastic-Free Fibers Address Environmental Concerns for Feminine Care and Personal Hygiene Products

According to WWF1, on the current trajectory, by 2040 global plastic production will double, plastic leakage into oceans will triple, and the total volume of plastic pollution in oceans will quadruple. This surge in plastic production is going well beyond what any country can properly deal with, resulting in a plastic pollution crisis affecting the environment, especially the oceans.
Addressing plastic pollution demands systemic change, government regulations, and individual actions that can help the Earth. With consumers becoming more conscious of their choices, industries are adapting to offer more responsible options.
This shift is happening across industries but not fast enough. Using advancements in research and development, fibers are evolving to provide the consumer with alternative choices and address concerns about plastic waste. The balance is to do this without losing important characteristics of the fiber.
VEOCEL™, the flagship specialty nonwovens brand of Lenzing Group, has embraced these changes without compromising on quality or performance. Offering LENZING™ Lyocell Dry fibers to meet the growing need for non-plastic nonwoven products, VEOCEL™ adheres to EU SUPD2 regulations to deliver high-performance absorbency and comfort. This innovative approach makes it the optimum fiber choice for responsible absorbent personal care and hygiene products.
These fibers feature Lenzing’s unique Dry technology which is high-performing hydrophobicity and has liquid-controlling properties. The fiber retains its softness in both dry and wet environments, as tested by Lenzing.
LENZING™ Lyocell Dry is a cellulosic environment-friendly wood-based alternative to synthetic fibers. Derived from wood, the VEOCEL™ branded lyocell fibers with Dry technology are made using a closed-loop production process with low water consumption, while being biodegradable and compostable3 at end-of-life. The fibers bring the inherent advantages of cellulose to personal care and hygiene products: natural absorbency, liquid distribution, gentle on the skin, naturally smooth and soft, biodegradability, and versatility. Manufacturers have the opportunity to protect the planet without compromising on performance or comfort.
As an industry, it is our responsibility to provide more responsible options and contribute to a better future for the planet and future generations. Let’s come together to set higher standards for industry sustainability and comfort.
- https://wwf.panda.org/wwf_news/?8607466/WWF-ban-on-harmful-single-use-plastics-treaty.
- Directive (EU) 2019/904 of the European Parliament and of the Council of 5 June 2019 https://eur-lex.europa.eu/eli/dir/2019/904/oj.
- LENZING™ Lyocell Dry fiber has been certified as biodegradable in soil and compostable under industrial and home conditions.
XHL Technology for Extra High Loft Nonwovens
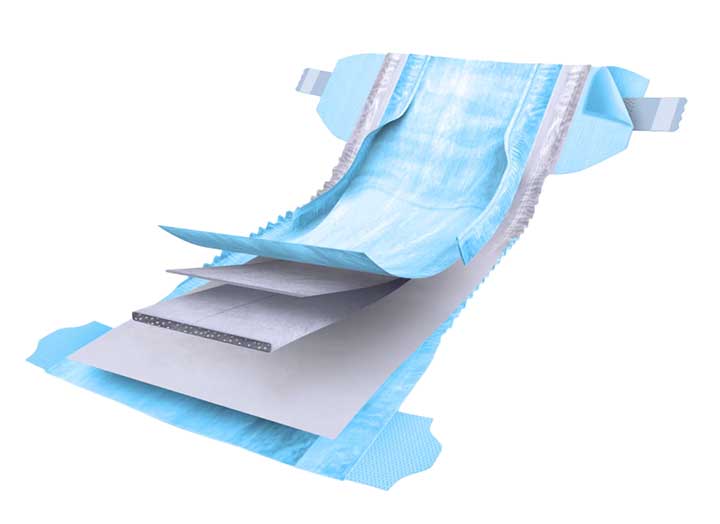
With the XHL (Extra High Loft) Technology Reifenhäuser Reicofil enables producers to easily combine superior softness with unseen drapability in nonwovens. The material is especially in demand among premium diaper manufacturers.
Manufacturers of baby diapers are looking for nonwovens that are particularly soft and adapt well to the baby’s body shape. Nonwovens producers, however, have only ever been able to satisfy one of these properties, and thus have not been able to make customers 100 percent happy. With Reicofil XHL technology, they can produce nonwovens that combine exceptional softness and super drapability in one material.
The Reicofil Technology Behind Extra High Loft Nonwovens
All that is needed to produce super-soft, drapable nonwovens is the proven Reicofil Bico spunbond process, which combines two polypropylene raw materials in one fiber. For Extra High Loft (XHL), Reicofil has developed a special recipe which – run as an eccentric core-sheath fiber – ensures optimum crimp with reduced fiber diameter.
Compared to common spunbond without crimped fibers, Extra High Loft technology enables 30 percent thicker material. At the same time, softness parameters such as drape and haptic are improved compared to processes that consolidate nonwovens using hot air. The result is a particularly soft feel combined with high abrasion resistance.
By using a state-of-the-art Reicofil 5 line the fiber size is reduced to almost one denier in XHL mode, thus lowering raw material consumption. Because bonding does not require hot air, the process also saves energy costs. In addition, XHL enables the processing of polypropylene raw materials only, which are ideally suited for inline recycling processes, thus reducing production costs and conserving resources.
Visit https://reifenhauser.com/en/lines-components/xhl-extra-high-loft
Thermore Introduces Freedom Stretch Insulation: Sustainable Performance for The Boldest of Movement
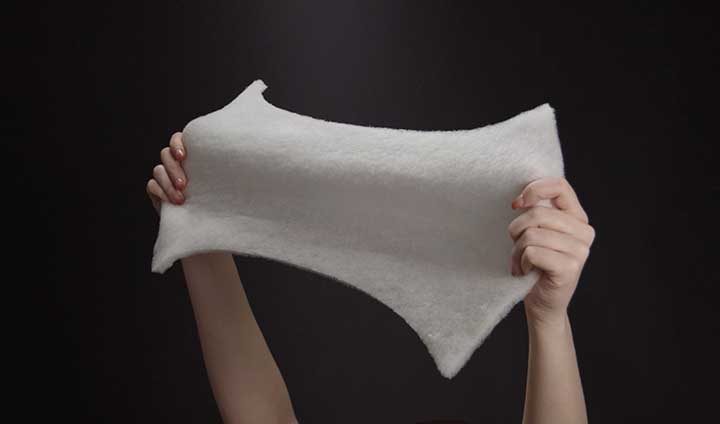
In March 20204, the Thermore group debuted its most dynamic stretch insulation in its five decades of innovation: Freedom. Made from 50% post-consumer recycled polyester, this unique and compelling insulation offers ground-breaking stretch while providing warmth across a multitude of uses including alpine sports, running, golf, commuter, fishing & hunting, cycling and a host of other active pursuits.
Dynamometer testing shows that the insulation – which comes in four levels of warmth, ranging from 60-150 grams per square meter – has incredible elasticity and recovers to 100% of itspre-stretch size time after time. The ability to provide warmth while also allowing for a dynamic range of motion is what impels performance brands to utilize Thermore.
The new Freedom insulation adds a higher level of comfort and functionality than what was previously attainable in the stretch category. It reaffirms Thermore’s place in the textile industry as a true innovator that is deeply rooted in performance and sustainability.
The Freedom insulation is GRS certified. It’s machine washable, can be dry cleaned and is easy-care for the consumer – and very design friendly for product developers with its high resistance to fiber migration. This represents another step forward in Thermore’s ongoing dedication to commit to a sustainable product line. Thermore pioneered the use of recycled fibers in the 1980’s and has mastered the technology ever since.