Mega-trends are ensuring the continued expansion of the filtration industry, which is estimated by the American Filtration Society (AFS) to have an annual value of around $80 billion globally. The demands for purer air and cleaner water are the biggest, and both are the subject of ever-more stringent legislation.
There are also requirements for finer degrees of separation in industrial processing – from food and beverages to hydraulic oils and semiconductor wash water. In addition, there is anticipation of many opportunities which will arise from the needs of growing new industries, such as biopharmaceuticals, mega data centers and electric vehicles.
Mergers
As a consequence, there have been some huge filtration industry mergers and acquisitions taking place in the past few years.
They include, for example, the $13.8 billion acquisition of Pall Corporation by life sciences giant Danaher in 2015, and more recently, the $4.3 billion buy-out of Clarcor by Parker-Hannifin in 2017.
These are just two examples of how the major companies of the filtration industry continue to grow via bolt-on acquisitions and profitability continues to rise in parallel to them being made.
In general, these companies are enjoying very high profit-to-turnover margins compared to other industries and this has now attracted the attention of major corporations in other fields, in addition to venture capitalists.
Most of the leading filtration companies are users of nonwoven filter media, often with their own proprietary filter media brands and backed up by in-house nonwoven developments, with or without the cooperation of third party suppliers.
Consumables
One factor, which is making the filtration industry attractive to investors, is the consumable nature of much of its business.
A considerable portion of the turnovers of some of the more profitable companies can be in aftersales – for a sustained period long after the initial sale of products and equipment has been made.
Nonwoven filter media are a key element of aftersales business, in many applications needing to be regularly replaced.
In the engine filtration sector, for example, the aftersales of Donaldson totaled over $1 billion of the company’s total sales of $2.4 billion in 2017, and this was up 14.2% in 2016.
The same is true of most other industry sectors where filtration is required, such as the pharmaceutical, food processing and medical industries.
Around 60% of the $2.8 billion sales of New York-headquartered Pall Corporation, for example, are generated by consumables. These consist principally of filters made with the company’s media, which include meltblown and wetlaid nonwovens, as well as membranes.
A key driver in the $16.8 billion acquisition of Pall Corporation for Danaher was to gain a leading position in technology
and filter media for the biopharmaceuticals industry.
Substantial orders
In industries such as power stations and steel and cement manufacturing where baghouse filtration is employed, a reorder for filters can be very substantial indeed.
As an example of the high volumes involved in supplying such industries, a single order for 30,000 filter bags to be used for flue gas cleaning was recently made by the Eesti Power Plant in Estonia – now the biggest oil shale fired power plant in the world.
Baghouse filters have in the past generally had a service life of between 1-3 years. However, even in China, stricter emission standards for flue gas and dust mean that finer – and more expensive – filter media are now being mandated. Not only are new filters being installed in both new and existing plants, but the new standards are requiring them to be replaced more frequently.
As far as indoor air filtration is concerned, in clean, controlled environments such as data centers, filters will be changed 3-4 times a year, based on a disciplined maintenance calendar.
For harsher environments such as outdoor enclosures, or for highly active systems such as those employed in the medical, military or telecoms sectors, the frequency of changing filters is much higher. In most cases, the need to replace filters for specialized equipment is dictated by maintenance sensors.
Transportation
Looking at individual sectors, there can be little doubt that the $2 trillion global automotive industry is on the verge of tremendous change.
There is currently frenzied activity and investment taking place in the bid to commercialize self-driving cars, involving both established car manufacturers and the technology giants of Silicon Valley.
In the even nearer term, electric vehicle and hydrogen fuel cell developments may start to threaten the dominance of the internal combustion engine.
Advanced filter media for conventional vehicles, however, continue to be improved.
Hybrid Structures
In response to tighter regulations on emissions from engines, along with less space for filters in engine compartments, nonwoven filter manufacturers are increasingly looking to hybrid structures.
Donaldson’s Synteq XP filter media, for example, contain a proprietary blend of polyester and glass fibers, which is thermally bonded in a proprietary process. The use of the polyester fibers establishes a stable framework, which supports the high filtration efficiency of the glass fibers. Synteq XP is employed in products such as Donaldson’s Blue filters, which provide premium protection for high- pressure fuel systems.
Similarly, at its new $35 million plant in Berlin, Johns Manville is now producing a thermally bonded bicomponent spunbond with a PET core layer and a melt polymer (other PET, PP or PE) sheath that bonds the PET fibers together at each crossing.
These PET spunbonds are in turn being combined with glass mats for the latest advanced filter media for automotive fuel and oil filtration applications.
It is imperative to evaluate the choice of filters being used in data centers, in terms of pressure drop and fan efficiency.
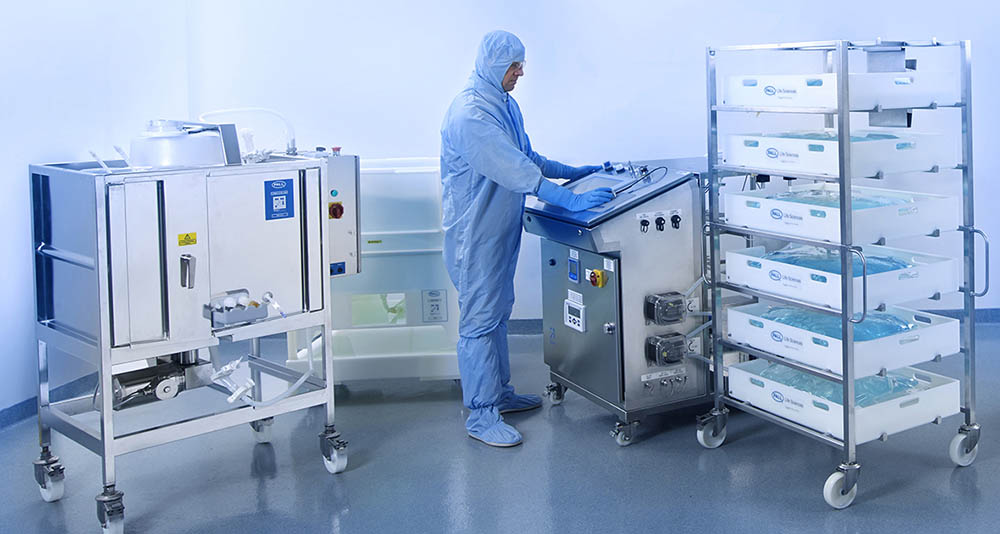
and filter media for the biopharmaceuticals industry.
Wet-Laid
Another interesting recent variant is Ahlstrom-Munksjö’s Captimax range of wet-laid media.
Aimed at the markets for fuel filters in passenger cars, as well as commercial heavy-duty vehicles and off-road machinery, the media are based on Eastman’s Cyphrex flat PET microfibers, which provide greater tear resistance, tensile strength and permeability without the usual challenges of processing synthetic fibers in wet-formed systems.
As a result, Captimax allows manufacturers to obtain optimum micron efficiency ratings and dust-holding capacity, and balance small-particle retention with the potential for longer product life. The media also lets fuel filtration system suppliers maintain existing capacity levels but decrease the product size, and in addition, can allow for increased efficiency with better options to filter fine particles to protect fuel injectors in vehicles and machines.
Pleating
Another important contributor to the efficiency of filter media in engine applications is in pleating, which effectively provides the largest possible filtration surface in the smallest space.
German filtration specialist Sandler, however, says that synthetic filter media, developed to compete with glass-fiber-based products, can often lack the contour precision and pleat stability required to ensure long-term performance.
The company’s Sawascreen Pleat media consists of two fine fiber meltblown nonwoven layers that are combined without the need for chemical binders and in which the fibers are highly aligned lengthwise.
The result is a product that can easily withstand the high mechanical pressure applied in the pleating process and guarantee accurately shaped and extremely stable pleats that provide the widest surface area possible throughout the filter’s lifetime.
HVAC
There are similar developments in the field of nonwoven filter media for heating, ventilation and air-conditioning (HVAC) applications.
Everist filtration media made by Berry Global is a nanofiber-coated spunmelt that offers enhanced mechanical efficiency, low pressure drop and high dirt-holding capacity, and is targeted especially at the HVAC markets for critical environments. Everist media provide a higher initial efficiency and the same mechanical efficiency as glass, while providing the same initial efficiency and higher discharge efficiency than other synthetics.
At the same time, they provide half the pressure drop of glass media and a comparative performance to electrostatically-charged synthetics. They also have similar dirt-holding capacity to glass and can be pleated on both rotary and blade units.
Gradient
The patented process that is employed by Kimberly-Clark to produce its Intrepid media results in a controlled gradient structure that has increasing fiber density from the upstream to the downstream sides.
This media construction, coupled with a proprietary electrostatic treating technology, allows filters made with Intrepid media to achieve high initial and sustainable filtration efficiencies with low pressure drop. Intrepid is made of thermally bonded continuous hydrophobic polyolefins, and its key features for HVAC applications include its ability to withstand moisture and to avoid fiber shedding.

Data Centers
Stockholm-headquartered Camfil manufactures specially-designed filter systems for data centers. It reports that its filter systems have in some cases resulted in savings in energy costs of up to 40%. The company adds that it is imperative to evaluate the choice of filters being used in data centers, in terms of pressure drop and fan efficiency.
Camfil’s Hi-Flo and Opakfil filters are certified by Eurovent and ISO-16890 to guarantee their energy efficiency and performance. They are based on a proprietary blend of fine fibers, which effect a mechanical particle capture principle, so do not require any electrical charge, extending their longevity and lowering the average pressure drop.
Depth Structure
New combinations of PET and glass fiber have also meanwhile been introduced for industrial air filtration in Ahlstrom-Munksjö’s Pleat2Save filters, which have a patent-pending depth structure consisting of a shaped mat glass core, enveloped within PET nonwovens and manufactured as a single web via the wetlaid process.
The key benefit of Pleat2Save is its robustness – it has a tensile strength around 2.5 times higher than microglass alternatives – allowing for excellent processing performance, especially during the pleating process.
The media are generally thermoformable and have another advantage in pleated form, in that the strips of glue that are generally spaced at 25mm apart to consolidate such structures can be widened to 50mm with no significant change in performance and no flow issues. This results in significant savings in adhesive.
Ultra-Web
There is a demand for higher levels of filtration in virtually all fields of application for nonwoven filter media and this is often being achieved with nanofibers.
A notable success to come from Donaldson’s internal research and development activities was Ultra-Web nanofiber-strengthened filter media.
Donaldson said it began research into the chemistry and production of fibers less than a micron in diameter before they were even called nanofibers. Its first commercial application for them came in 1981.
Ultra-Web technology is now backed by over 80 issued and pending patents, and has benefited numerous industries, including dust collection, transportation, construction, agriculture, mining, military and gas turbine.
Caterpillar, for example, uses Donaldson products in clean air filtration systems for its mining vehicles. According to reports published by the Mine Safety and Health Association trade group, these filter media offer a significant reduction in airborne contaminants in the cabin space, compared with cellulose-based filter media.
Nozzleless Spinning
The majority of leading filtration companies, as well as their nonwoven suppliers, now have nanofiber technologies and the technology for the production of nanofiber-based webs that are reinforced with standard fabrics has improved rapidly in the past decade or so.
The advent of so-called nozzleless electrospinning has emerged as a viable new technology, largely due to its mechanical simplicity.
The commercially-available Nanospider systems manufactured by Elmarco in the Czech Republic are characterized by significant improvements in this nozzleless technology.
There are now around 200 Elmarco Nanospider nanofiber nonwoven units in commercial operation.
Membranes
Nanofibers are seeing nonwovens getting ever closer to the performance of membranes and offering cost advantages.
DuPont Hybrid Membrane Technology (HMT), for example, is billed as filling the performance gap between meltblown nonwovens and microporous films.
HMT nanofiber sheets contain continuous polymeric filaments and are available on a commercial scale in the form of membrane-like sheet structures, which deliver an optimal balance of flux/barrier performance.
Another interesting patented nanofiber technology is Ahlstrom-Munksjö’s Disruptor, which filters by both charge and mechanical entrapment. The media employs submicron microglass support fibers as the platform for attaching nanoalumina fibers.
These can now be easily manufactured into a nonwoven web using wet-laid technology to produce a filter media that has a 2-micron average pore size.
A square meter of the filter media has greater than 42,000 square meters of nanofiber surface area available for adsorption.
Biopharmaceuticals
A further example of the potential of nanofibers in filtration is FibroSelect technology, which was acquired by GE during 2017.
Separating biopharmaceuticals is tricky. During affinity chromatography – the most expensive stage of separation – biological drugs diffuse through a coffee-table-sized column packed with tiny beads. Overall, it takes about eight hours for the products to find their way through millions of beads before they are safe for patient use.
FibroSelect is based on nanofibers and has the potential to eliminate beads and instead pump materials over webs of the new chromatography nanofibers in a process that takes just 10 minutes.
By speeding up production and reducing unit costs from currently up to $1,000 per gram, it has been calculated that drug companies can save anywhere up to $3.3 million per batch using the new nanofiber-based filter method.
The commercial opportunities here could be enormous.