In addition to Meridian’s expanded yarn dye capabilities, its new technology gives brands the option to buy yarn manufactured in a facility engineered to consume significantly less water, gas and electricity than most yarn dye operations around the globe.
Meridian Specialty Yarn Group’s new 116,000 square-foot facility in Valdese, North Carolina, is the first yarn and fiber dye operation built in the U.S. in over two decades. It offers:
- The only tow-dyeing capacity in the United States. Until this summer, all producer-dyed acrylic was manufactured outside the U.S.
- The ability to process every dyeable fiber in various forms, including yarn, tow and top and also chemically treat or dye all fiber substrates, from cellulosic and animal fibers, to polyester, nylon and dyable aramids.
- Faster and more efficient production in the U.S., and that means quicker, more efficient delivery to North American markets.
Meridian’s new technology gives brands the option to buy yarn manufactured in a facility engineered to consume significantly less water, gas and electricity than most yarn dye operations around the globe. Less water is needed for dyeing, and less water means fewer chemicals are used. Lower overall water consumption means less effluent and reduced power consumption. For example, MSYG’s new dyed yarn drying process is water-free, unlike the conventional process for drying dyed yarn. In addition, by using less water to dye and treat yarn, MSYG uses less gas to heat the liquor bath during processing.
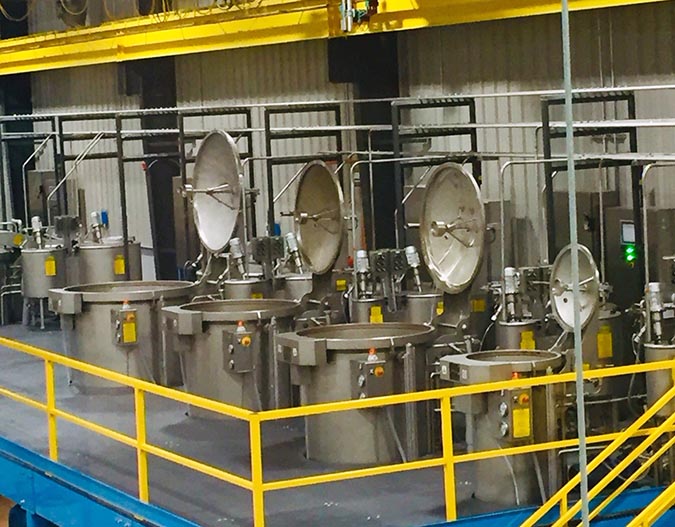
Meridian’s new plant includes dye equipment by Galvanin, S.p.A. of Vicenza, Italy; a patented automatic dosing system for dispensing chemicals and auxiliaries from Color Service Dosing Technologies of Dueville VI, Italy; new monitoring and control systems for all of the new dyeing equipment from Adaptive Controls of Huntersville, NC, U.S.; and a new Galvanin skein printing machine along with support equipment.
The package dye technology includes vertical, air pad, low-liquor ratio machines that replace all of MSYG’s existing fully flooded package dye equipment. The new acrylic tow dyeing capabilities will support the raw material needs at MSYG’s plant in Ranlo, NC, and are also available to outside customers. The skein-printed yarns will go into craft yarns, apparel products and some home furnishings. The top dyed wool capability will support worsted spinners supplying high-end apparel, hosiery and home furnishings.
Despite installing a new generation of robotics, the company has added positions and is in the process of retraining employees to work with the new technologies.
“We’ve met the initial employment targets of adding 25 jobs and are hiring and retraining,” said Tim Manson, president of MSYG. “We did not lose any positions due to new technology.” Meanwhile, the company’s Human Resources Manager, Debbie Sigmon, has begun working extensively in the community and with the local community colleges to develop programs to train a new generation of textile workers and attract new talent to the region.