In the dynamic and global textile fiber industry with its various manufacturing processes and end-uses, news and information is breaking on a daily basis. International Fiber Journal is tracking stories relevant to our industry from manmade to natural to bio-based fibers, innovations in nonwoven, woven, braided and technical textiles, technologies for additives, bonding, coatings and polymers, and applications from apparel to hygiene to transportation, and more. Here we will post news stories relevant to textile fibers and their downstream applications on an ongoing basis. Please check back for regular updates. If you have news that you feel should be added to this summary report, please email it to Ken Norberg at ken@ifj.com.
Most recent update: November 26, 2024
President Biden Announces Limited Trade Actions on Fine-Denier Polyester Staple Fiber in Section 201 Safeguard Case
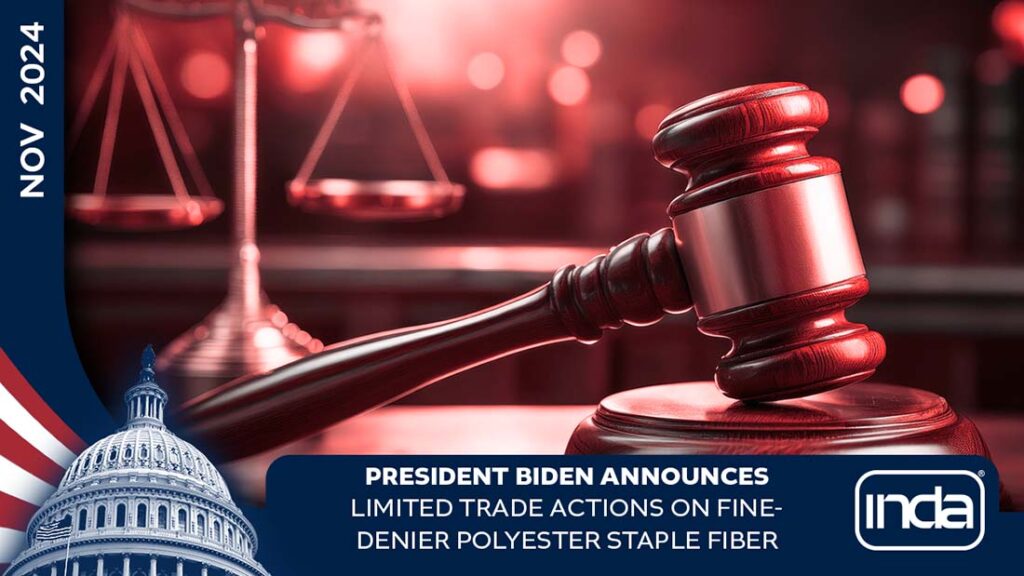
Last week, the White House announced that President Joe Biden would not implement a tariff rate quota on imports of fine-denier polyester staple fiber (PSF) in response to a section 201 safeguard case filed by U.S.-based fiber producers.
The President announced an import quota only on imports of fine-denier PSF under the temporary importation under bond (TIB) program, which is predominately used in woven textiles and apparel and is not expected to impact nonwovens.
President Biden opted not to implement a tariff rate quote or other measures that were recommended by the U.S. International Trade Commission citing that other industries, including nonwoven manufacturers, would be negatively impacted by such actions, President Biden’s proclamation stated that:
“While the USITC Commissioners recommended that I impose a tariff-rate quota on fine denier PSF imports, I have determined not to do so…[t]herefore, I have decided to tailor this safeguard remedy to TIB entries of fine denier PSF. Furthermore, I have determined not to impose a tariff-rate quota on imports of fine denier PSF in the interest of balancing the competing interests of domestic fine denier PSF manufacturers and the impact of the safeguard remedy on downstream United States producers, including manufacturers of textiles, defense products, and consumer products, that rely on fine denier PSF.”
This decision comes after several U.S.-based nonwovens producers commented to the White House Trade Policy Staff Committee and the USITC that the nonwovens industry would be harmed by actions that would raise the costs of fine-denier PSF. INDA submitted comments outlining the concerns of many nonwovens producers. Government affairs director Wes Fisher testified before the Trade Policy Staff Committee at the Office of the U.S. Trade Representative hearing on September 30th.
ALLIED Feather + Down’s ExpeDRY Insulation Now Powers Performance and Sustainability for Montane
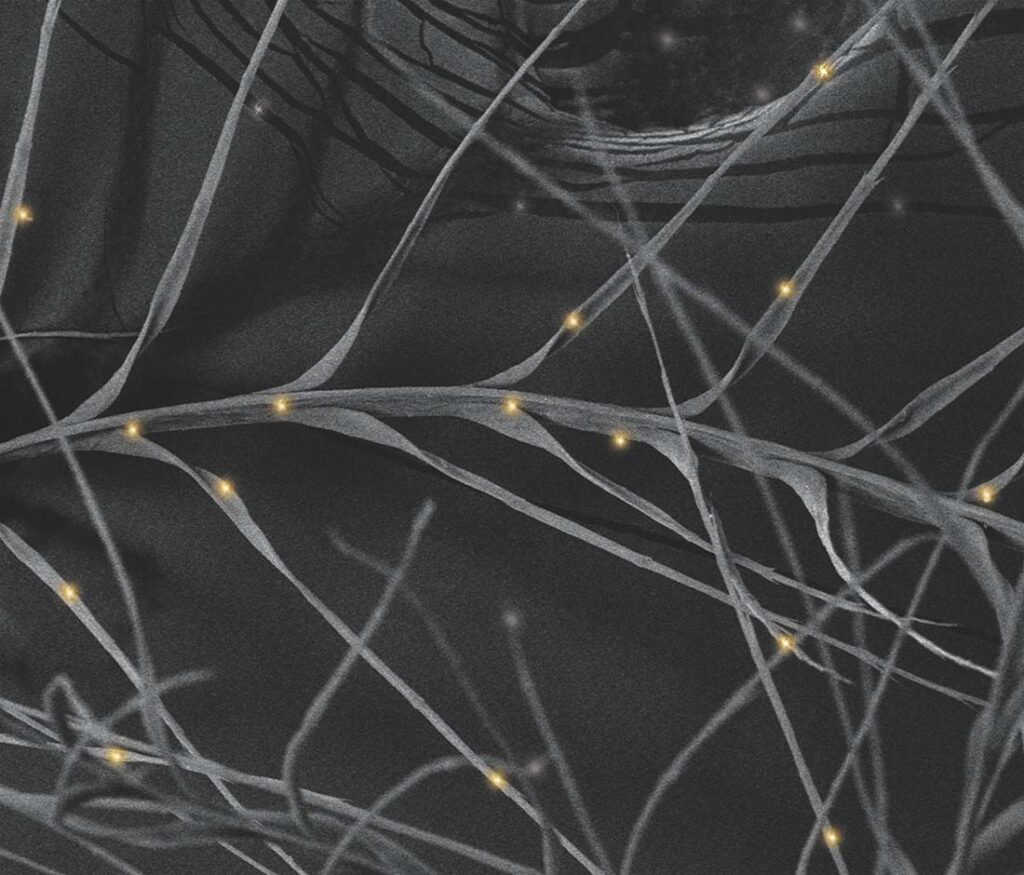
ALLIED Feather + Down (AF+D), global leaders in high performance, ethically sourced, and recycled down, will be supplying their high performance ExpeDRY ultra dry down to Montane for their fall 2025 down apparel line.
ExpeDRY represents the evolution of performance down for use in extreme situations, replacing chemical treatments with gold particles permanently bonded to down clusters. ExpeDRY keeps water vapor from condensing into droplets, providing better real-world performance than all other treatments. The ExpeDRY filled products will also dry significantly faster in-home laundry making care easier and utilizing much less energy through the life of the products.
Montane will offer ExpeDRY in 100% of their down jackets, being the first to adopt the technology over all down jackets.
Poised to render current, chemical-intensive treatments obsolete, ExpeDRY down insulation is cleaner and better performing than all current water-resistant down technologies. Created in partnership with FUZE Technologies and relying on gold particles permanently bonded to down plumes, ExpeDRY is permanent and since it is completely chemical free, there are no PFAS or other concerns. In all real-world simulations, ExpeDRY is far better at keeping insulated jackets dry and warm in any environment, and at a significantly lower impact than the WR treatment alternatives.
Absorbent Hygiene Professionals Advance Innovation and Sustainability at Hygienix™ in Nashville
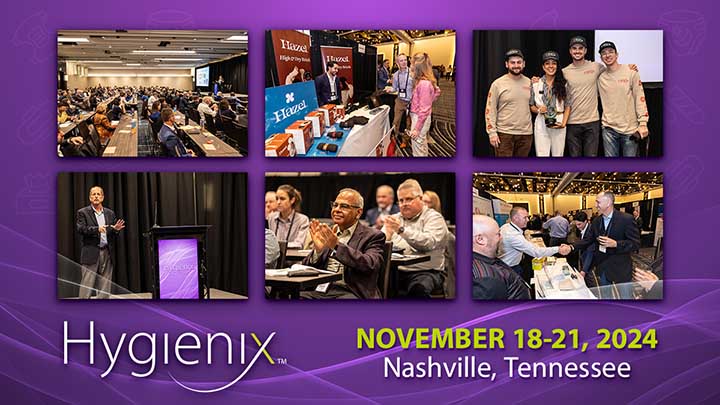
INDA brought together hundreds of industry leaders to explore advancements in the absorbent hygiene and personal care markets during the 10th annual Hygienix™ event, held Nov. 18-21 at the Renaissance Nashville Hotel.
Themed Driving Absorbent Hygiene Product Innovation: Consumer Desires, Market Dynamics & Sustainability Solutions, key sessions included pricing strategies, global trade impacts, FemTech, adult care, period poverty, emerging pet care and wound care markets, environmental regulations on plastics and PFAS, and the impact of aging societies.
An event highlight was the presentation of the 2024 Hygienix Innovation Award® to:
HIRO Technologies, Inc.’s World’s First MycoDigestable Diapers, diapers featuring plastic-eating mushrooms that combine excellent absorbency with natural materials.
The other notable finalists were:
Harper HYGIENICS S.A.’s Cleanic Naturals Hemp Sanitary Pads (Day & Night) and Pantyliners, an innovative femcare line made with regenerative hemp fibers from Bast Fibre Technologies.
Hello Hazel, Inc.’s High & Dry Briefs, the first and only disposable briefs for leaks designed to look, fit, and feel like real underwear.
Hygienix Highlights
Attendees gained insights and knowledge during three hands-on training sessions on Nov. 18, focused on fundamentals of absorption systems and opportunities in adult incontinence, innovations in menstrual care, and baby and infant care market dynamics.
Hygienix kicked off with a welcome reception that fostered networking. Attendees explored emerging trends and product innovations through Lightning Talks, connected with successful hygiene start-ups during Lunch Around sessions, and discovered the latest offerings at tabletop exhibits.
“Hygienix exemplifies INDA’s commitment to empowering companies in the absorbent hygiene and personal care markets to advance their businesses,” said INDA President Tony Fragnito. “The insights and connections made at this year’s event will drive growth and enable participants to meet evolving demands and market challenges.”
INDA announced Hygienix 2025 will be held Nov. 17-20 at Omni Amelia Island Resort, Fernandina Beach, Florida.
Green Theme Technologies and Golden Long John Integrate Clean Textile Dye and Finishing Technologies
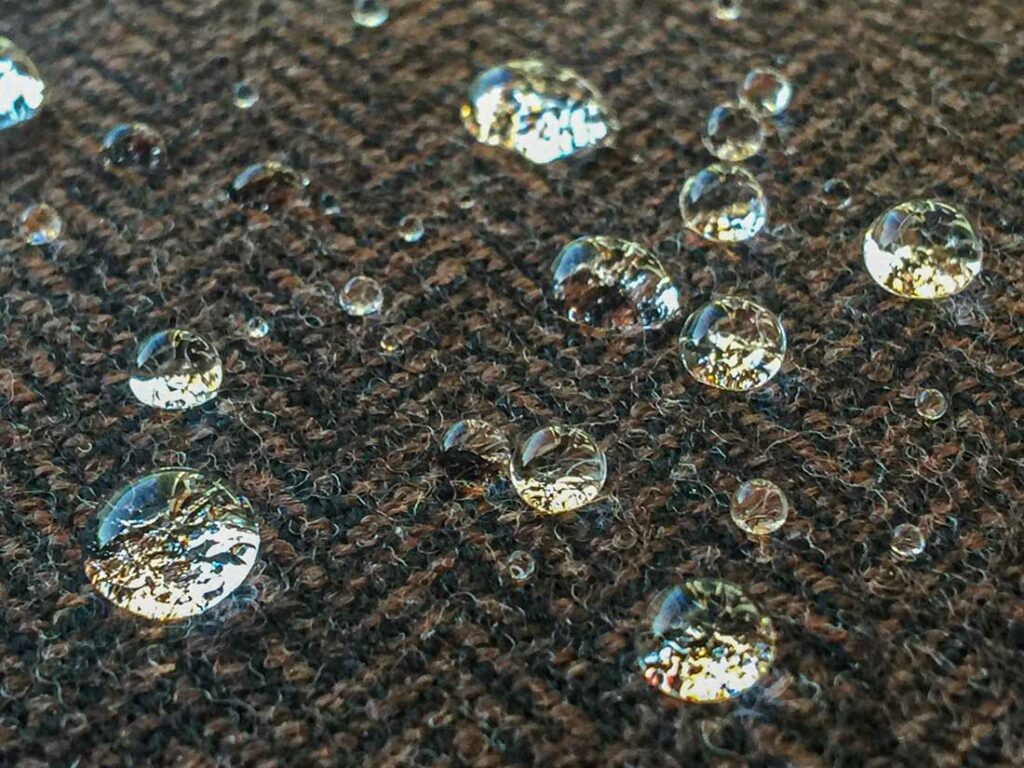
Green Theme Technologies (GTT), creators of the waterless and PFAS-free EMPEL® textile finishing platform, has teamed up with Golden Long John to promote the next generation of cleaner and more efficient fabric dye and finishing processes.
The textile manufacturing industry generates trillions of gallons of wastewater each year. Traditional textile dyeing and finishing rinses chemical dyes and water repellency onto fabrics. Post-production toxic water is then dumped into rivers and oceans.
Last year, Golden Long John, a major textile supplier of the global footwear industry, introduced GTT’s EMPEL® finishing platform in their Vietnam factories. Their partnership has led to the combination of their two industry leading technologies, the EMPEL® high-performance water-repellent finish and Golden Long John’s direct dye process.
“We believe, Cleaner IS Better and this is a big step forward for the fashion and textile industries,” said Martin Flora, President of GTT Business Development. “Similar to GTT’s EMPEL® application, Golden Long John applies dye chemistry directly onto fabrics. Better performance with much less pollution is our vision for the future.”
INDA and EDANA Release the Eighth Global Nonwoven Markets Report
INDA, the Association of the Nonwoven Fabrics Industry, and EDANA, the Voice of Nonwovens, announced the release of the Global Nonwoven Markets Report, A Comprehensive Survey and Outlook, 2023–2028, now available for purchase through both INDA’s and EDANA’s websites.
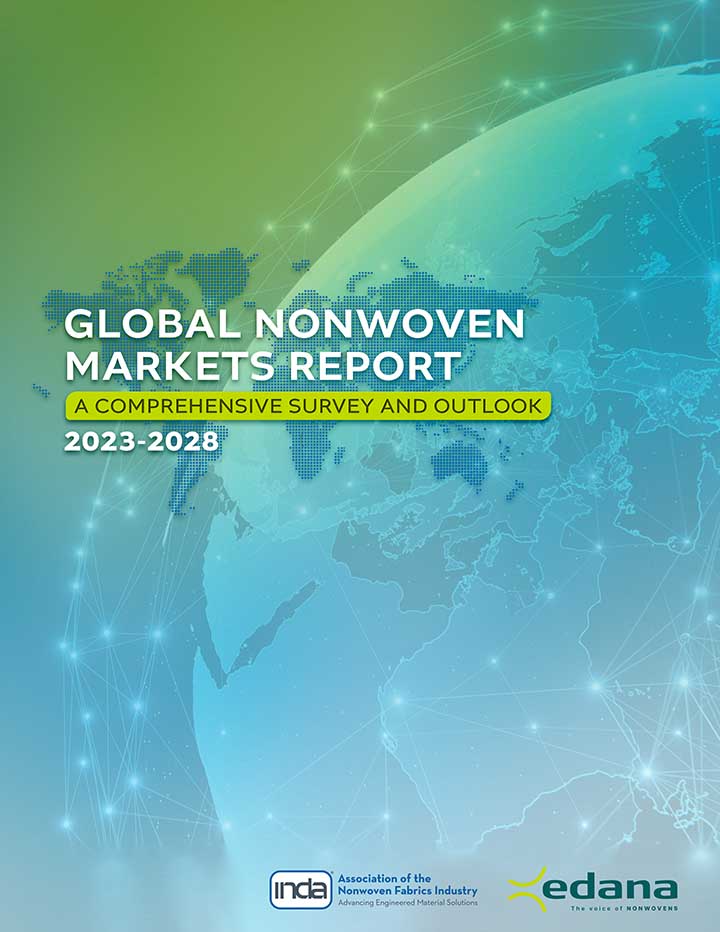
This latest edition offers a comprehensive analysis of global nonwoven macro drivers, supply and demand trends, and an expanded regional trade section. The report forecasts a steady growth in demand for nonwovens across key sectors over the next five years.
Key Insights from the Report Include:
- Production Growth: From 2013 to 2023, nonwoven production increased at an annual rate of 5.4%, with significant growth driven by the spunlaid and needlepunch processes.
- Regional Production: China led global production growth, contributing an additional 4.5 million tonnes from 2013 to 2023—a remarkable 9.4% annual growth rate.
- End-Use Expansion: Wipes, medical, and transportation segments experienced the fastest expansion among nonwoven end-use applications.
“The global nonwovens industry is changing in a positive way with moves toward innovation and sustainable products,” said the report’s co-authors Jacques Prigneaux, Market Analysis & Economic Affairs Director at EDANA and Mark Snider, Chief Market and Industry Analyst at INDA.
This report offers a detailed breakdown of regional demographics, production forecasts, technological advancements, and investment outlooks for North America, Greater Europe, Asia, and South America. Additionally, it includes an economic trade analysis, end-use segmentation, and insights into future industry trends.
“As strategic partners, INDA and EDANA are committed to sustained growth and innovation within the entire nonwovens supply chain. This report presents our collective best estimate on future demand, predicated on sound macro-economic analysis,” said INDA President Tony Fragnito. “This Global Nonwoven Markets Report is an essential planning resource for all those involved in strategic planning within the nonwovens supply chain.”
“The demand for reliable market information and forward-looking data is a vital ingredient for thriving a successful business. This new report, developed by our two leading nonwovens industry associations, draws on decades of experience, close observation, and direct data collection from hundreds of companies,” stated EDANA General Manager Murat Dogru. “Created by the industry for the industry, it stands as a unique, authoritative, and reliable resource on nonwovens data than any other report.”
Availability: The report will be available for purchase and download on November 21, 2024.
www.inda.org/global-nonwoven-markets-report
www.edana.org/trainings/publications/statistics-nonwovens-report2023-2028
Jones Family of Companies and ECO Fiber Inc. Enter Joint Venture
Jones Family of Companies, Inc. and ECO Fiber Inc. announced the formation of a joint venture to expand their offerings in the sustainable cold chain packaging market. This new venture combines the strengths of ECO Fiber’s expertise in packaging solutions with Jones Family of Companies’ nearly 90 years of experience in textiles and commitment to sustainability. Together, they are establishing a new company, EcoFiber Packaging, which will provide innovative, sustainable cold chain packaging solutions to meet the evolving needs of the industry.
Both companies recognized that a new corporate model would maximize their combined potential, prompting the creation of EcoFiber Packaging. As part of the venture, Jones Family of Companies has acquired the textile assets of ECO Fiber Inc., and a Joint Venture Agreement has been executed. EcoFiber Packaging will operate as a wholly new entity under its own brand, with the joint commitment of both companies to deliver high-quality, environmentally responsible packaging solutions.
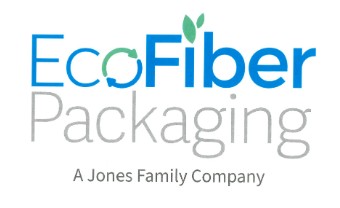
Jones Family of Companies is a pioneer in sustainable practices and a leader in the USDA BioPreferred Program. This federal program encourages the use of renewable agricultural resources in product manufacturing, reducing dependence on petroleum. Jones’ USDAcertified biobased insulation products, made from renewable materials like cotton and jute, meet rigorous standards for temperature-sensitive applications in industries such as frozen foods, pharmaceuticals, and medical supplies. This dedication to environmental responsibility is a natural alignment with ECO Fiber’s values of sustainability and product excellence, making this partnership a powerful combination of service, quality, and innovation.
With Jones’ manufacturing and warehousing facilities in Tennessee, New Hampshire, and Indiana joining EcoFiber Packaging locations in North Carolina and Texas, the new company now has expanded reach and capacity to serve customers nationwide with even greater reliability and efficiency. EcoFiber Packaging is committed to enhancing the service, quality, and product lineup that customers have come to trust from ECO Fiber, while advancing their commitment to sustainable practices.
4M Carbon Fiber Announces Launch of 50-Ton Plasma Oxidation Qualification Line
4M Carbon Fiber, a leader in innovative carbon fiber manufacturing, announced the commencement of its 50-ton per year plasma oxidation qualification line project. This strategic initiative marks a critical step in demonstrating 4M’s patented oxidation technology, which promises to revolutionize the carbon fiber industry by significantly improving efficiency, reducing costs, and enhancing material properties.
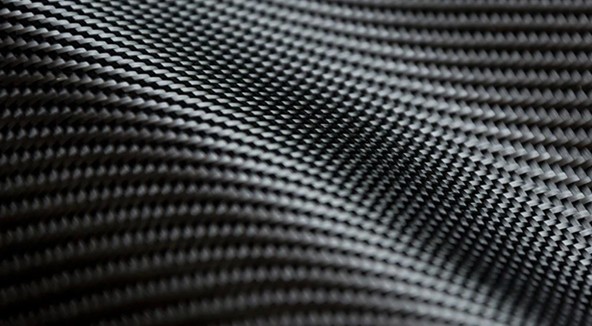
The $4.5 million project, which has already secured initial funding, will serve as a platform to showcase the scalability of 4M’s groundbreaking plasma oxidation process. With this line, 4M will be able to produce material for large-scale qualification projects, a key factor in securing licensing agreements and equipment sales. The technology is designed to triple throughput, cut oxidation energy consumption by 75%, and deliver up to 50% savings in capital costs and 30% in operating expenses compared to current industry standards.
The qualification line will also enable 4M to engage more closely with companies that are already showing strong interest in adopting the technology. Multiple major carbon fiber manufacturers and new market entrants have expressed readiness to proceed with qualification projects and licensing agreements once the technology is proven at this scale. Furthermore, the line will support ongoing development projects with domestic oil companies and other industry partners, who are looking to establish their own carbon fiber production capabilities using 4M’s patented process.
Lenzing Nonwovens Expands its LENZING™ Lyocell Dry Fiber Portfolio
Lenzing Nonwovens, a leading supplier of regenerated cellulose fibers, announced the expansion of its LENZING™ Lyocell Dry fiber portfolio with two new cellulosic fibers – a fine dry fiber that delivers strength and softness, and, a coarse dry fiber which provides enhanced liquid and air flow. These two innovative products enable customers to confidently broaden their use of LENZING™’s wood-based and biodegradable fibers into a wider range of applications while maintaining exceptional performance.
All LENZING™ Lyocell Dry fibers within the family (standard, fine, and coarse) have hydrophobic properties which ensure efficient liquid management suitable for extensive nonwoven applications.
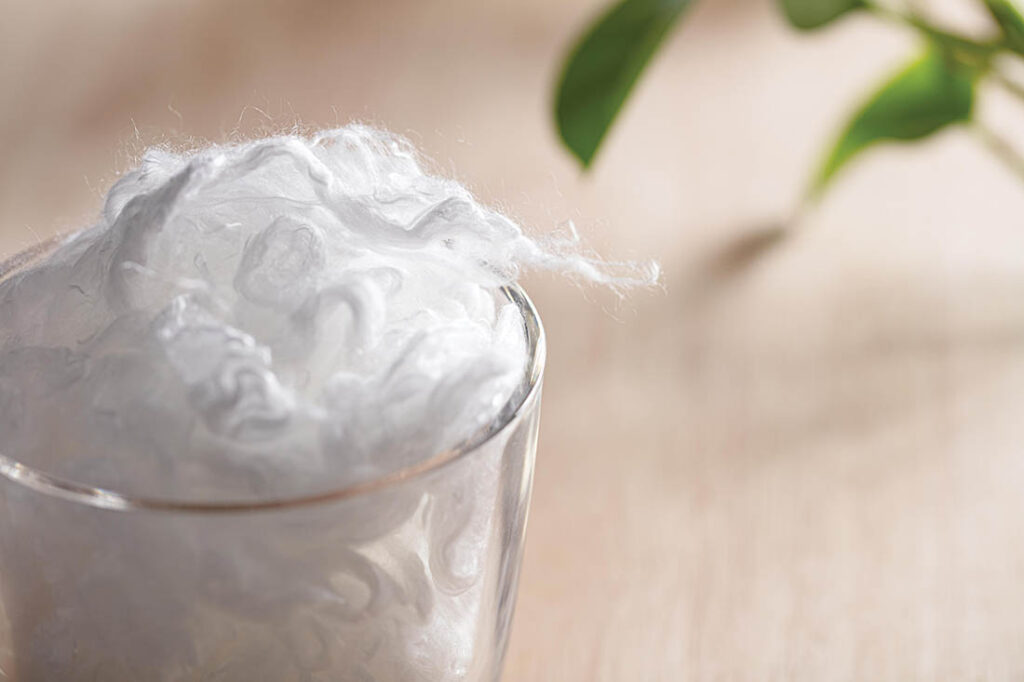
The new LENZING™ Lyocell Dry fine fiber can produce nonwoven fabrics with higher density compared to LENZING™ Lyocell Dry standard fiber. With up to 30% more cellulosic fibers in the same space, customers can create strong and soft nonwoven products. These fibers are suitable for use in hygiene applications such as diapers or sanitary pads.
The new LENZING™ Lyocell Dry coarse fiber creates fabrics that are more open due to its extended fiber diameter, and thus increasing the pore sizes between the fibers in the fabric. This allows for more air or liquid to flow through the material. It is particularly suitable for the acquisition and distribution layer in hygiene products and is also being explored for industrial filtration applications.
Monique Buch, Executive Vice President Nonwoven at Lenzing AG said, “By offering a diverse range of hydrophobic cellulosic fibers from fine to coarse, which are not plastic according to the EU’s Single-Use Plastics Directive (SUPD), our customers can use alternative fibers for a wider range of applications whilst delivering superior performance.”
Lenzing will showcase its innovative LENZING™ Lyocell Dry fiber family at tabletop 202 during the Hygienix Conference, November 18-21, 2024.
Vidalia Mills Introduces Innovative Digital Tracker for Cotton Products
American textile company Vidalia Mills based in Vidalia, Louisiana, has implemented a technologically advanced digital tracking system that asks the industry to reconsider how companies trace cotton products throughout the supply chain. This technology, unprecedented within textile manufacturing, guarantees full accountability for all products Vidalia Mills creates.
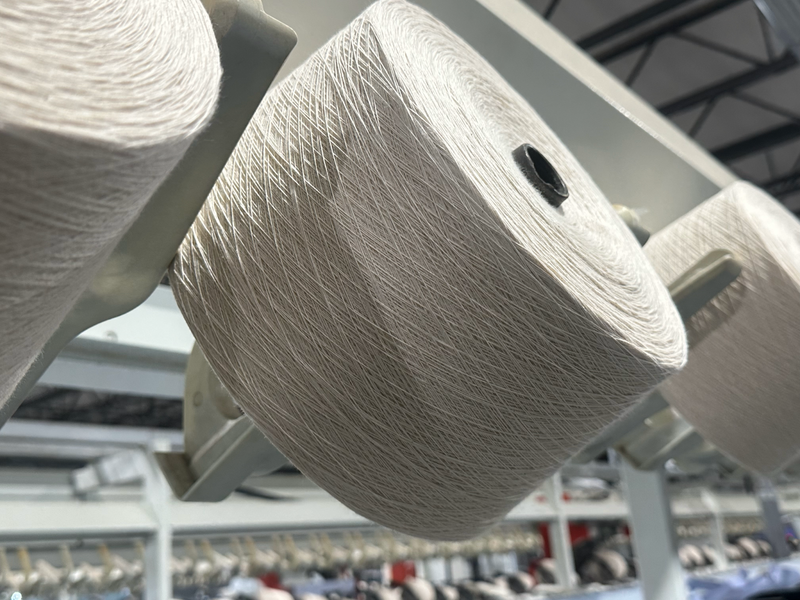
The digital tracker, embedded into the cotton fibers themselves, enables Vidalia Mills to monitor the journey of their products from the initial stages of cotton cultivation to the final finished goods.
By integrating this advanced tracking system, Vidalia Mills aims to provide its customers with complete assurance regarding their cotton products’ origin, quality, and sustainability. Vidalia Mills’ digital tracking system is now available for all its cotton products, including its signature artisanal canvas and denim fabrics. Customers can access detailed information about the origin and journey of their clothing by scanning a unique QR code on the garment’s label.
The digital tracking information will be readily available for each product, providing customers with a comprehensive understanding of the item’s journey from seed to shelf.
eVent Fabrics Hires Innovation Director Cathy Shao
eVent®️ Fabrics, a global leader in waterproof and breathable fabric technologies, is doubling down on their PFAS-free laminate offerings by hiring textile engineer and R&D leader Cathy Shao to the newly created Innovation Director role.
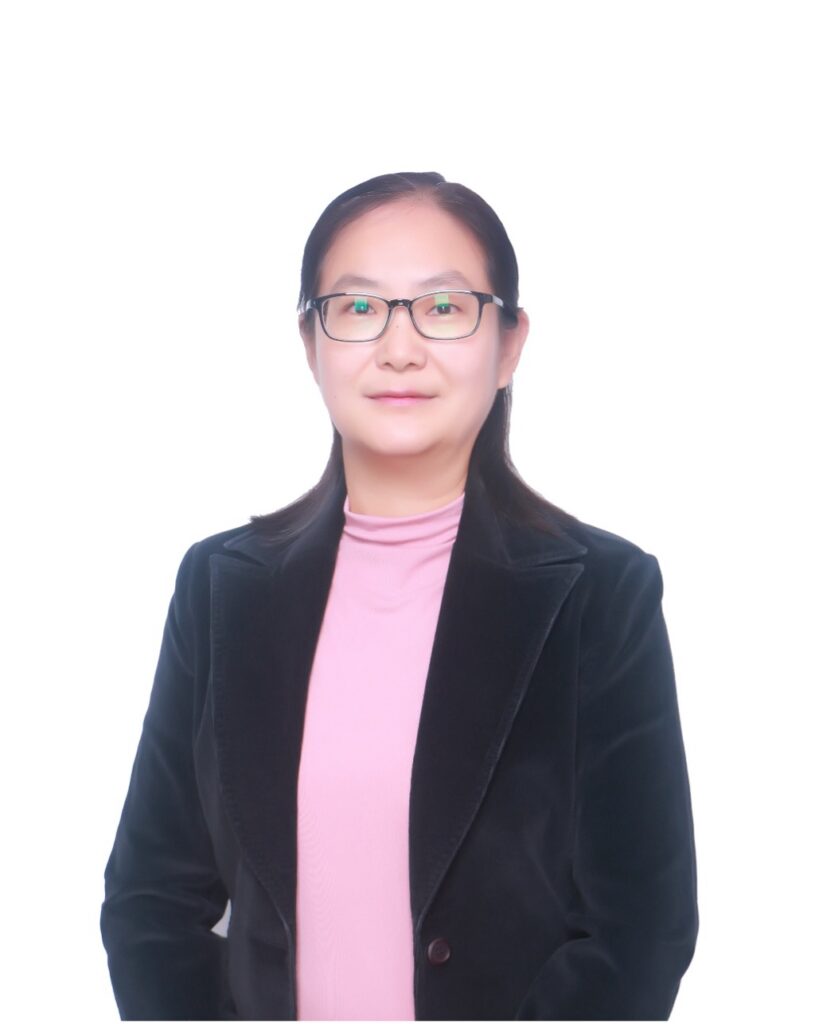
Shao will develop next generation fabric technologies and drive the innovation of cutting-edge, sustainable laminates, while also helping to expand and improve the eVent BIO and alpine ST collections. As global regulations and customer sentiment drive the demand for PFAS-free performance laminates, the timing is perfect for bringing new high-performance all-weather apparel, footwear, and accessory innovations for outdoor activities including run, bike, ski, hike, sail, hunt, fish, and golf to market.
In her previous roles, Cathy worked as a senior engineer and R&D leader in various industry-leading textile giants, including over 10 years with Dupont China. She has specialized in research and development of textile fibers and yarns based on different polymers, such as Bio-based polymers, Sorona®, PA56, and more. Her abundant experience in polymer material science, strong sense of new innovations, and well-established network will bring great value to eVent Fabrics. Cathy will continue the development and expansion of eVent BIO and alpineST as well as exploring new fabrics and membrane technologies. She holds a Master’s degree of Polymer Material Science in Donghua University.
Green Theme Technologies Closes $6 Million Series C Funding Round
New Mexico based Green Theme Technologies, Inc. (GTT), a leader in sustainable textile and materials science, announced the successful closing of a $6 million Series C funding round.
The funding will enable GTT to expand development, scale production, and meet rising demand for sustainable solutions in the apparel, footwear, and military sectors. Additionally, GTT plans to enhance its research and development efforts to refine its offerings and increase global impact.

Leading the round were Pangaea Ventures and Cottonwood Technology Ventures, two venture firms known for supporting innovations in advanced materials and sustainability.
GTT’s cutting-edge PFAS-free and water-free technologies provide sustainable alternatives to traditional textile treatments, eliminating harmful chemicals and drastically reducing water use. The Series C investment will enable GTT to expand its development capabilities, scale its technology, and meet the growing demand for sustainable solutions within the footwear, apparel, and military markets. The new funding will also drive continued RCD efforts to refine GTT’s product offerings and bolster the company’s global impact.
Rieter, ARISE IIP, Afreximbank Sign Framework Agreement for Africa Textile Renaissance Plan
ARISE IIP, the pan-African developer and operator of world-class industrial parks, has partnered with African Export-Import Bank (Afreximbank), and Rieter, the world’s leading supplier of systems for manufacturing yarn from staple fibres in spinning mills. The unprecedented partnership will spearhead the “Africa Textile Renaissance Plan” – a transformative initiative aimed at revitalizing the continent’s textile sector.
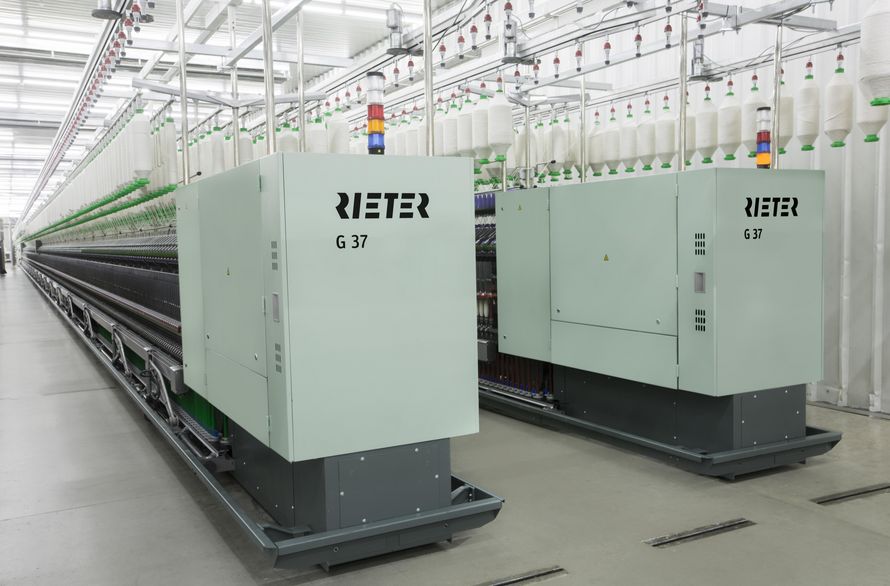
This ambitious project will leverage ARISE’s extensive network of industrial parks to support a new era of textile manufacturing in Africa.
In order to facilitate the implementation of the Africa Textile Renaissance Plan, Afreximbank, Arise IIP and Rieter AG signed a framework agreement in October 2024. The framework agreement outlines the collaboration to establish 500,000 metric tons of African cotton transformation capacity over the next three to five years, supported by USD 5 billion in financing. The Africa Textile Renaissance Plan aims to achieve the following key objectives:
- Establish 500,000 metric tons of African cotton transformation capacity over the next three to five years, with potential expansion of an additional 500,000 metric tons;
- Localise machine repair expertise in Africa
- Create up to 500,000 jobs
- Reduce Africa’s annual textile imports
- Boost exports to the US under the African Growth and Opportunity Act (AGOA), focusing on full value addition within the continent and to export to the rest of the world
- Develop a strong financing structure to support capacity building
Countries benefiting from the program will be selected based on criteria such as power and gas availability, and textile parks with standard infrastructure or equity contribution. Training centers will be established in selected countries to develop and improve skill levels.
Teijin Frontier Launches OCTAIRTM High-Performance Insulation Fiber
Teijin Frontier Co., Ltd., announced it has launched OCTAIR™, a new premium brand of insulation fiber for bedding and apparel. This innovative product utilizes a short-cut polyester fiber featuring a unique, hollow, 8-fin cross section with radiating protrusions. OCTAIR™ meets growing demand for alternatives to natural feathers, which is experiencing declining production volumes and rising costs.
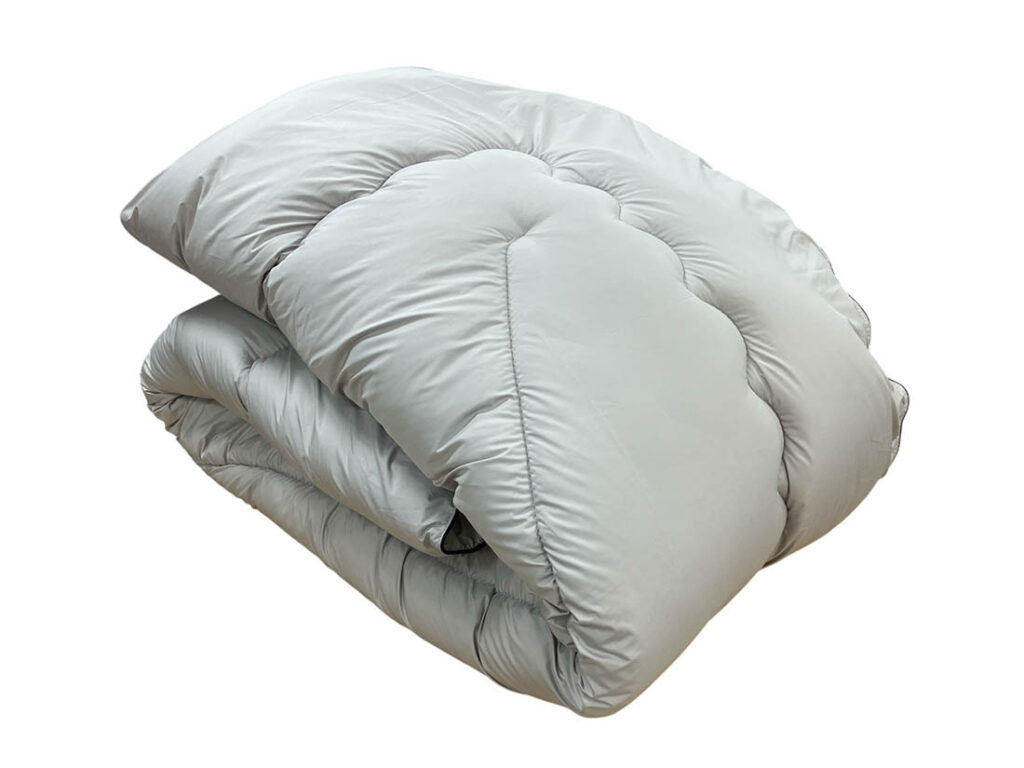
The company plans to expand its use across a wide range of materials. One of them is SOLOTEX™ OCTAIR™, an insulation material that incorporates polytrimethylene terephthalate (PTT) fibers along with OCTAIR™ fibers. Teijin Frontier has begun domestic and international sales of SOLOTEX™ OCTAIR™.
In SOLOTEX™ OCTAIR™ insulation, the OCTAIR™ fibers’ hollow structure with an 8-fin cross section creates air pockets that provide excellent warmth, loft and lightweight properties. As a result, SOLOTEX™ OCTAIR™ delivers insulation performance equivalent to the same weight of down (based on tests using 30cm square mini quilts).
To enhance the SOLOTEX™ OCTAIR™ fibers, the PTT fibers’ unique helical molecular structure offers a soft texture, elasticity and good shape retention. Additionally, the tips of the fibers are soft, do not spread out easily and reduce tangling, making the blowing process for filling comforters and clothing smoother than with conventional polyester insulation. This new insulation also offers sustainability benefits through the incorporation of plant-based raw materials.
Paradise Textiles Unveils First Garment with Kintra Bio-Synthetic Fiber
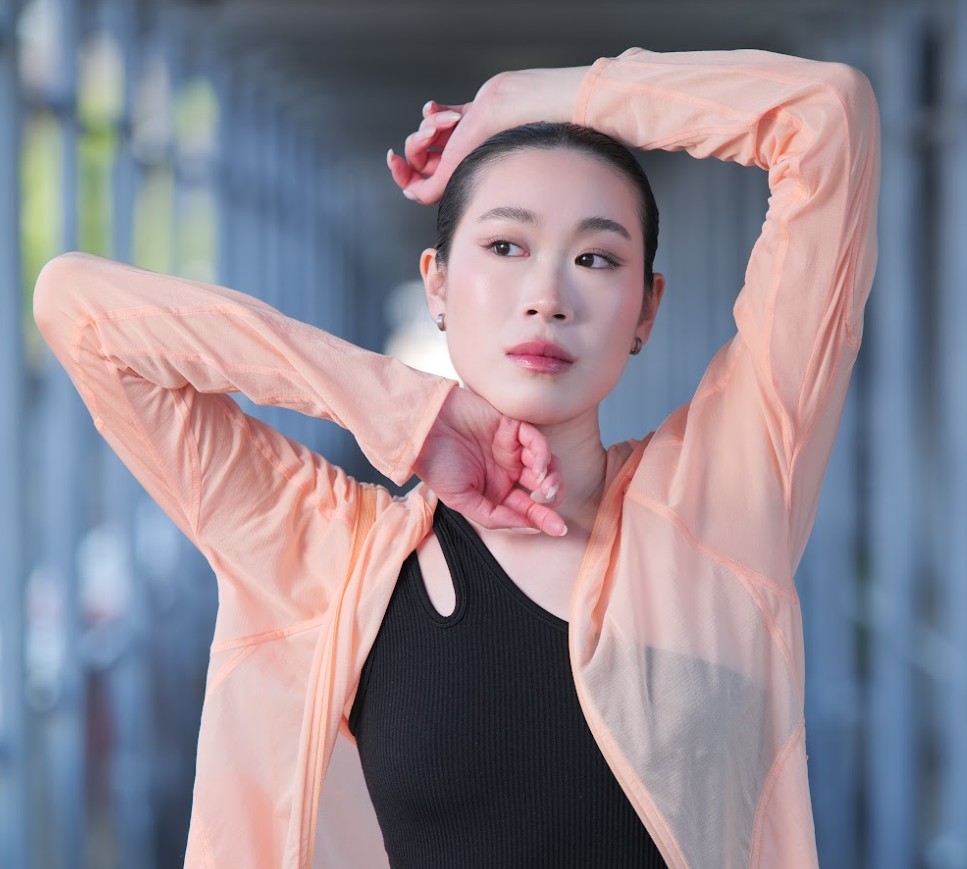
Paradise Textiles, the material science hub of Alpine Group, has partnered with Kintra Fibers, a leader in bio-based fiber innovation, to create the first garment using Kintra’s groundbreaking proprietary bio-synthetic material. This lightweight jacket serves as a proof-of-concept, representing a crucial milestone in Kintra’s journey toward commercial viability as a sustainable alternative to traditional fossil-based polyester.
The development follows a successful pilot project in 2023, during which Kintra and Paradise Textiles collaborated to create and rigorously test textiles made from Kintra’s yarns.
Kintra’s proprietary bio-synthetic material provides a sustainable alternative to polyester. Made on the same equipment as conventional polyester, Kintra’s resin is estimated to reduce emissions by 95%, water usage by 30%, and energy consumption by 20%. These advancements are achieved with the use of bio-based inputs, lower processing temperatures, and efficient production methods. Upon the completion of a full life cycle assessment, the company expects to see continued energy savings and reduced Scope 3 emissions in downstream processes, including yarn spinning, dyeing, and finishing.
In terms of performance, testing conducted by Paradise Textiles has shown that Kintra yarns are on par with polyester with regard to strength, yet are 4x softer, and have twice the stretch, resulting in a unique fabric profile. Fabric testing demonstrated that Kintra knits and wovens are on par with, or surpass, the polyester benchmark in strength and durability tests including tensile strength, seam slippage, tear strength, and abrasion and pilling resistance.
Although the properties of Kintra fabrics are versatile enough for various applications, Paradise Textiles chose to debut a jacket made from Kintra due to its outstanding abrasion and pilling resistance, which enhances garment longevity and minimizes microfiber shedding, two key properties for outerwear. Additionally, this jacket highlights Kintra’s compatibility with existing textile production machinery and dyeing processes, making it an ideal choice for brands seeking to transition to sustainable materials seamlessly.