In the dynamic and global textile fiber industry with its various manufacturing processes and end-uses, news and information is breaking on a daily basis. International Fiber Journal is tracking stories relevant to our industry from manmade to natural to bio-based fibers, innovations in nonwoven, woven, braided and technical textiles, technologies for additives, bonding, coatings and polymers, and applications from apparel to hygiene to transportation, and more. Here we will post news stories relevant to textile fibers and their downstream applications on an ongoing basis. Please check back for regular updates. If you have news that you feel should be added to this summary report, please email it to Matt Migliore at mmigliore@inda.media.
Most recent update: February 26, 2021
ProAmpac partners with Clemson University to support smart packaging R&D
ProAmpac, a flexible packaging leader, has partnered with the Clemson University Department of Food, Nutrition and Packaging Sciences to support the company’s commitment to leading the industry in developing smart food packaging.
“ProAmpac is committed to leading the industry in developing smart packaging technologies,” said Hesam Tabatabaei, vice president of product development and innovation. “Smart packaging is a fast-growing packaging innovation, which can promote both food safety and food shelf life; and, within the food segment, seeks to protect food from harmful bacteria and virus contamination to prolong product freshness.”
With the partnership announced today, ProAmpac is working with Clemson’s Kay Cooksey, professor and Cryovac Endowed Chair of the Food, Nutrition and Packaging Sciences Department within the College of Agriculture, Forestry and Life Sciences. Recognized as an expert in the fields of food safety, shelf life and active packaging, her lab will provide testing capabilities critical to the smart-packaging mission of extending shelf-life and promoting food safety. “I am very excited about this partnership. I have worked in the field of active and Intelligent Packaging for over 25 years and it is a pleasure to work with a company so committed to advancing this field,” said Professor Cooksey.
This University support is being integrated with ProAmpac’s Product Development and Innovation teams. ProAmpac is expanding research, adding personnel, purchasing equipment, and building a new Collaboration & Innovation Center that will serve as the company’s international hub for packaging design and development.
Clemson’s food science and packaging expertise complements polymer-science and application development engineering capabilities provided by the Polytechnique Montréal. Last year ProAmpac announced a five-year extension of its R&D alliance partnership with Polytechnique Montréal for its Sustainable, Safe and Smart Polymer Flexible Packaging program operated by the university’s Department of Chemical Engineering, chaired by Prof. Abdellah Ajji.
Source: proampac.com
Sustainable textile fiber producer Spinnova and wood pulp producer Suzano to open commercial-scale factory in 2022
Material innovation company Spinnova and the world’s largest wood pulp producer Suzano will make an estimated 22 million euro investment to build the first commercial-scale Spinnova
production facility in Finland. The total investment, including all needed infrastructure such as real estate, is estimated to be some 50 million euros. Spinnova’s sustainable fiber, created out of wood and waste without the use of harmful chemicals, will be available for global textile brands in 2022.
The new, industrial-scale production unit will be located in Jyväskylä, Finland, home of Spinnova’s R&D hub and pilot facility. Production will be managed and operated by a new joint venture company owned 50/50 by Spinnova and their partner and investor, Suzano.
The joint venture investment is estimated to be 22 million euros in size. According to Spinnova, the total investment, encompassing all needed infrastructure such as real estate, is some 50 million euros. The real estate will be built and rented for the joint venture by the Jyväskylä real estate development company Jykia.
“Every leading textile brand is looking for ways to minimize their emissions and ecological footprint, and build a circular material foundation for their products,” said Spinnova’s CEO and co-founder Janne Poranen. “We feel humble and proud that soon we will be able to provide brands our new, disruptively sustainable fiber and fabrics.”
Suzano is a world leader in the production of eucalyptus pulp and has expanded its operations to create sustainable and innovative solutions derived from trees to the challenges faced by society. In the joint venture, Spinnova will be the exclusive technology provider, while Suzano will ensure the supply of sustainably produced micro-fibrillated cellulose obtained from eucalyptus planted by Suzano in Brazil. The fiber produced will be sold under the Spinnova trademark.
“Suzano uses only planted trees in its production processes. This renewable raw material is being combined with Spinnova’s technology for producing fibers that are more sustainable than the options currently available in the textile industry, which is aligned with the demands of contemporary society”, says Fernando Bertolucci, Chief Technology and Innovation Officer of Suzano. With a process that uses no harmful chemicals and 99% less water than the cotton value chain, the Spinnova fiber can be considered the most sustainable textile fiber there is. Fiber produced this way creates minimal CO2 emissions, is quickly biodegradable and contains no microplastics. The fact that these fibers can be recycled into a new fiber again and again makes the Spinnova fiber disruptively circular. The Spinnova technology enables textile fiber production out of wood but also from textile waste or agricultural waste such wheat or barley straw.
Source: spinnova.com
German Institutes of Textile and Fiber Research Denkedorf celebrate 100-year anniversary
The German Institutes of Textile and Fiber Research Denkendorf (DITF) look back on 100 years of successful textile research. In 1921, the cornerstone was laid in Reutlingen with the foundation of the German Research Institute for the Textile Industry. Today, the DITF form the largest textile research center in Europe.
The new institution quickly met its goal of supporting the domestic industry with independent research. With the technical center as a teaching institute, the testing office as a service provider and the research institute as a source of ideas, the Reutlingen institute made a significant contribution to the economic success of the German textile industry in the following decades. Over the years, further locations are established in Stuttgart and Denkendorf, which are merged in Denkendorf in 1979 to become the German Institutes of Textile and Fiber Research.
Today, the DITF conduct research on the entire textile value chain, including corporate processes and business models. The DITF work on an interdisciplinary basis: chemists, biologists, mechanical engineers, process engineers, cyberneticists, computer scientists and economists collaborate in researching all textile topics of the future. They are involved in regional, national and international networks.
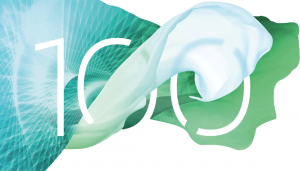
“Today, the DITF are the innovation engine of the German economy, especially for technical textiles and medical textiles. We open up new ways of bringing textile ideas and technologies quickly and efficiently to industry and society,” said CEO Professor Götz T. Gresser.
With its innovations, the DITF primarily support small and medium-sized enterprises that do not have their own research department. Specialized events, often in cooperation with other institutes, ensure knowledge transfer to various industries. Service offerings such as a wide range of textile testing services, prototype construction and a pilot factory complement the DITF’s range of services. In 2001, the subsidiary ITV Denkendorf Produktservice GmbH (ITVP) is founded, which successfully manufactures medical precursors for industrial partners.
For research on an industrial scale, the DITF is continuously expanding its pilot plants. In 2014, for example, the High-Performance Fiber Center (HPFC), one of the world’s most modern facilities for the development of high-performance fibers, an important unique selling point of the DITF is built with the support of the state.
“This year, however, the DITF are celebrating especially the people who have accompanied 100 years of successful research” said Professor Gresser. “These are, of course, first and foremost our dedicated employees who are passionate about their work every day. They include the industrial partners who work with the scientists to drive forward future-oriented projects and implement numerous research results on the market. And last but not least, we would like to thank the politicians and the administration for their reliable support and their trust in 100 years of textile future,” said Gresser.
Source: ditf.de/100-years
Integrated Fiber Solutions announces $30M expansion in Rome, Ga.
Integrated Fiber Solutions (IFS), a manufacturer of synthetic bulked continuous filament (BCF) yarns for the carpet, rug, and automotive industries, will invest $30 million in expanding its operations in Rome, Ga., to meet growing demand. This expansion will bring approximately 40 additional jobs to Floyd County.
“It’s always gratifying to see family-owned Georgia businesses continue to expand and create opportunities in their home state,” said Governor Brian P. Kemp. “I’m grateful to Integrated Fiber Solutions for continuing to invest in northwest Georgia and creating great manufacturing jobs for hardworking Georgians in Floyd County and throughout the region.”
Integrated Fiber Solutions was established in 1986 to serve the man-made yarn needs of multiple carpet and rug industries in Georgia. With locations in Rome, Dalton, and Lafayette, the company employs approximately 600 people in northwest Georgia.
“We are very pleased to announce the expansion of Integrated Fiber Solutions Rome manufacturing facility. IFS is adding additional capacity to continue to meet the demand of our customers in multiple market segments. The Rome-Floyd community has supported our efforts for many years, and now we have the opportunity to add jobs and opportunities for workers to grow as our business grows,” said IFS COO Mark Cook. “IFS will be investing over $30 million for an expansion of multiple phases spanning the next five years, with the addition of approximately 40 new jobs over the course of the project.”
Integrated Fiber Solutions will construct a new facility adjacent to their current plant, which is located at 19 Westside Industrial Boulevard in Rome. New job opportunities include management, operator, and mechanic positions. Individuals interested in careers with Integrated Fiber Solutions are encouraged to email cbaez@intfibers.com for additional information.
Source: gov.georgia.gov
RadiciGroup and Avient ColorWorks team up to create carpet samples based on the new ColorForward 2022 Palette
Despite added challenges imposed by the Covid-19 pandemic, Avient ColorWorks and RadiciGroup once again worked together to create carpet samples that are part of Avient’s ColorForward 2022 trend-analysis and color-forecasting guide for the polymer industry. The 16th edition of the annual kit, announced in December, includes four societal trends and twenty related colors that can be expected to resonate with consumers consciously or unconsciously in the next few years. The colors are rendered in several different forms, including traditional color chips, sample cards, various molded forms and fiber pom poms.
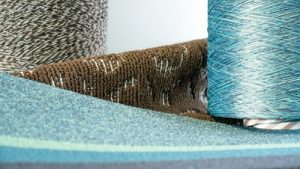
RadiciGroup produced carpet samples aimed at contract and automotive applications. For the first time, RadiciGroup used its proprietary sustainable Renycle BCF yarn for the creation of the samples. Made from recycled nylon 6, Renycle is a highly valued material because of its excellent resistance and versatility.
“This is the 5th year of collaboration between our companies,” says Heike Schmidt, Marketing & Carpet Application Manager at RadiciGroup Advanced Textile Solutions. “Avient ColorWorks is synonymous with reliability and innovation in the color sector. By working with them on the creation of the Renycle® carpets included in ColorForward 2022, RadiciGroup can create and propose new, inspirational and sustainable samples and yarns to its customers.”
Source: radicigroup.com
EDANA opens registration for OUTLOOK 2021
Registrations are now open for the 2021 edition EDANA’s OUTLOOK event, to be held 21- 23 April in a virtual format. Every year, hundreds of professionals attend OUTLOOK to network, do business and share knowledge around the topics of personal care, hygiene, and wipes. And, although distanced by current circumstances, EDANA’s ambition remains to offer participants a unique journey and gathering.
“For the second time running EDANA will host OUTLOOK online, with a promise to ensure participants a fully interactive and practical experience featuring all that which makes OUTLOOK an enduring success: expert insights, knowledge sharing, and networking,” said Pierre Wiertz, General Manager of EDANA.
The online OUTLOOK conference will bring three days of inspiration and insights featuring over 30 speakers and a diverse range of panel discussions and topical presentations. The conference will examine new product developments, evolving global drivers, market trends and key industry sustainability initiatives over three days. “After a year where medical and infection prevention nonwoven-based product have more than ever demonstrated their essential character, it is quite natural that, again in this edition of OUTLOOK, ample coverage be devoted to these, with opportunities of hearing from expert speakers how long-lasting the related market changes are likely to be in Europe and beyond,” said Wiertz.
EDANA has invested in a new platform to host the event, ensuring further options for productive engagement. Through the platform, participants will be able to connect with all other attendees, discuss in depth with speakers, see who is attending a specific session, discover the products and offers of the participating companies, attend live company meetings, participate in live panel discussions and last but not least network and exchange in one-on-one video meetings. New features have been implemented for companies that wish to get extra exposure and organize meetings, mirroring the typical routines of live editions of OUTLOOK. The presentations will remain available 3 weeks after the conference.
For more details about the event and to view the conference program: edana.org/events/outlook/outlook-2021.
Source: edana.org
Eastex Products moves to new, larger headquarters to accommodate growth from PPE demand
Eastex Products, Inc., specializing in textile components, custom solutions and PPE, announced it has moved to a new, larger headquarters in Plymouth, Massachusetts. The move stems from the company’s accelerated growth in 2020. Following the increased demand for PPE and other nonwoven medical textiles, Eastex outgrew its previous facility and sought to expand its warehouse size.

The newly acquired building, nearly three times larger than the previous location, will provide the much-needed room to accommodate increased inventory for its customers. The additional space also provides for the company’s growing workforce, with multiple conference rooms and stations where teams can collaborate on better solutions for their customers, colleagues, and partners. This is a significant milestone for the fast-growing company, whose owners are committed to sourcing its PPE from U.S. suppliers.
Source: eastexproducts.com
Lightweighting technologies boosted by sustainability and circular economy initiatives
At the annual meeting of the VDMA Hybrid Lightweight Technologies working group, which took place on 12 February, 2021, it became clear that the industry is intensively addressing holistic concepts of lightweight construction, offering its customers worldwide customized solutions for CO2 reduction. In the automotive sector in particular, there is growing pressure from supply chains to live up to the guiding principle of climate-neutral manufacturing and to be able to prove this with data. In the context of taxation based on CO2 intensity, monetary benefits can also be generated through CO2 savings.
In addition to sustainable production, the recyclability of plastics products is becoming increasingly important against the background of resource conservation and the goal of a functioning circular economy. It is still a challenge for materials and process technology to combine the benefits of use of new lightweight material composites with good ecological product design in terms of recyclability. Industry and research are working together on new methods for the material recycling of hybrid lightweight components, which improve the eco-balance and, at the same time, offer economic advantages. In the development of new lightweight components, design for recycling must have the same priority as functionality and production efficiency.
Consideration of the carbon footprint is becoming increasingly important for mechanical engineers. The chairman of the VDMA working group, Marc Kirchhoff, TRUMPF, states: “In addition to the own production location, it is the degree of energy and resource efficiency of the machines that we deliver to our customers. But we can also score points with the positive CO2 balance of the lightweight products manufactured on these machines. The focus on circular economy and CO2 footprint opens up new fields of application for hybrid lightweight construction and drives development – not least the digitalization of production processes!”
Achieving the climate targets and a more sustainable use of raw materials is guiding policies and legislation worldwide when it comes to implementing new regulations for sustainable business. The European Union is aiming for climate neutrality by 2050 as part of the Green Deal. To achieve this goal, the EU is planning concrete measures for this year. These include, for example, the planned CO2 pricing or quotas for the use of recycled materials in order to promote the circular economy for plastics.
But sustainability goals do not only play a role in Europe. CO2 regulations per climate protection and the expansion of renewable energies are also on the agenda of the upcoming five-year plan of the Communist Party in China — one of the most important sales markets with growth potential for lightweight construction technologies.
Source: vdma.org
Oerlikon Manmade Fibers announces webinar series focused on home textiles
Oerlikon Manmade Fibers has scheduled a series of webinars on the topic of home textiles. Traditionally, the company’s event calendar begins with the DOMOTEX trade fair and the supplementary BCF Symposium. Due to the COVID-19 pandemic, Oerlikon has an alternative event for its customers this year. Those interested can register to take part in the webinars via the Oerlikon Manmade Fibers Division corporate website.
Manufacturing carpet yarn with the BCF S8 – ‘Experience-based Innovation’
March 3, 2021: 2-2.45 CET
The series of webinars launches in March 3, 2021 with a presentation on the BCF S8 system. Nis Lehmann-Matthaei, Sales Director BCF at Oerlikon Neumag, introduces the latest development steps in the monocolor variant. Under the ‘Experience-based Innovation’ motto, this system technology sets new standards with never-seen-before spinning speeds, up to 700 filaments and fine titers of up to 2.5 dpf.
BCF S8 Tricolor – a massive step forward for your carpet yarn production
March 10, 2021: 2-2.45 CET
In his webinar, BCF Sales Director Michael Rübenhagen focuses on tricolor yarn production. Thanks to the patent-pending CPC-T unit (Color Pop Compacting), the BCF S8 is capable of manufacturing in excess of 200,000 different shades – from mélange through to strongly-separated.
Heavy-denier applications – WINGS HD and eAFK Big V complete your home textiles portfolio
March 17, 2021: 2-2.45 CET
The carpet yarn portfolio is complemented by a POY-DTY solution for heavy-denier applications: using the WINGS HD and the eAFK Big V, carpet yarn manufacturers can efficiently and economically cater to increasing demand for heavy-denier DTY yarns. The technology is presented by Area Sales Director Oliver Lemke.
Compact spinning system for heavy-denier POY and DTY – what the VarioFil can do for you
March 24, 2021: 2-2.45 CET
In a fourth webinar, Product Manager Ralf Morgenroth unveils the VarioFil R+ compact spinning system for recycled filament yarn, developed and built by subsidiary BBE. The system is available for producing POY.
Source: oerlikon.com
Textile sensor patch, made with conductive yarns, could detect pressure points for amputees
A soft, flexible sensor system created with electrically conductive yarns could help map problematic pressure points in the socket of an amputee’s prosthetic limb, researchers from North Carolina State University report in a new study.
In IEEE Sensors Journal, researchers from North Carolina State University reported on the lightweight, soft textile-based sensor prototype patch. The device incorporates a lattice of conductive yarns and is connected to a tiny computer. They tested the system on a prosthetic limb and in walking experiments with two human volunteers, finding the system could reliably track pressure changes in real time.
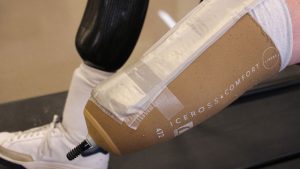
“What people commonly use to measure pressure within prosthetics are rigid sensors,” said the study’s first author Jordan Tabor, a graduate student in the NC State Wilson College of Textiles. “They’re hard, they’re bulky; they can be heavy. These are not things that amputees can use on a daily basis because rigid sensors negatively affect the fit of amputees’ prosthetics. Rigid sensors can also cause discomfort. We designed sensors that can be integrated into textiles in a way that doesn’t cause any additional discomfort for the user, and could be worn on a more regular basis.”
In one experiment, the researchers tested whether the patch could detect changes in pressure when they placed it on an artificial limb, turned at different angles. Then they used it to test pressure changes when an able-bodied person wore the sensor patch while walking with a bent-knee adaptor and while shifting their weight between legs.
In their last experiment, a volunteer with an amputated lower leg wore the patch on the liner of their prosthetic limb in areas where the prosthetic limb typically applies higher pressure. They tested the sensor patch while the volunteer shifted weight and walked on a treadmill, finding the system was durable and could reliably monitor pressure changes in the socket.
“This approach that we thought of a few years ago does work, and it’s a readily manufacturable technology,” said Tushar Ghosh, the study’s co-corresponding author. “You cannot put materials next to the skin that are uncomfortable and may not be safe. So we are putting things that are used around us all the time, and are soft and flexible.” Ghosh is the William A. Klopman Distinguished Professor of Textile Engineering, Chemistry & Science in NC State’s Wilson College of Textiles.
Read the full story: https://news.ncsu.edu/2021/02/textile-sensor-patch-could-detect-pressure-points-for-amputees/
Source: ncsu.edu
Berry Global makes $70M investment to expand disinfecting wipes capacity in the US
Berry Global Group, Inc., a leading global nonwovens manufacturer, announced its investment of over $70 million in its United States wipe substrate capabilities. The investment includes a new line, producing additional capacity, and enabling the Company to better serve its global customers as well as support the continuing growth of its business. Berry provides many of the world’s leading brands with wipe materials for infection prevention. Prior to the demand surge of 2020, the impregnated wet wipes segment, specific for home cleaning and disinfecting, was growing at six percent in the 2014 to 2019 time frame. Amplified by COVID-19 prevention, the demand for disinfectant wipes is expected to have permanently shifted to its current, increased use.
Berry will add to its broad scope and scale by installing the line in the United States. This investment is complementary to Berry’s existing portfolio and features the Company’s proprietary Spinlace® technology. The U.S. investment has a targeted commercialization date of the March quarter 2023.
“This investment reflects the commitment we have in support of our customers’ growth plans and it is a clear signal of our intent to provide the best products in the disinfectant wiping space worldwide,” said Mark Siebert, EVP and General Manager, U.S. and Canada, Healthcare and Specialties at Berry.
Source: berryglobal.com
Techtextil North America now accepting abstracts for 2021 Symposium and education programs
The 2021 edition of Techtextil North America is now accepting abstracts for its Symposium program and additional educational features including Tech Talks, The Lab, and its Student Research Poster Program. Techtextil North America 2021 will be held August 23 – 25, 2021 at the Raleigh Convention Center in Raleigh, North Carolina.
The Techtextil North America Symposium will provide the latest research and technology across verticals – with insights into textile industry trends, challenges brought on by emerging technology and how to keep stride in an ever-changing, global business landscape. It will explore advancements throughout the supply chain and address the industry’s response to the COVID-19 pandemic.
The Symposium will feature seven paid sessions featuring presentations and discussions with academia and industry experts on the following topics:
- Reinventing the Supply Chain
- Digital Transformation
- Sustainability in Laundering and Textile Care
- Circular Economy
- Fabric and Materials ID
- Government Laws and Regulations
- Nonwovens and Personal Protective Equipment (PPE)
Submissions to present in the Techtextil North America Symposium must be sent to ali.rosenberger@usa.messefrankfurt.com by April 2, 2021.
Also returning to Techtextil North America are Tech Talks and The Lab – complimentary mini-sessions on the show floor, for which abstracts are now being solicited in (but not limited to) research, design, engineering, and innovation in the following areas:
- New Fiber Technologies
- Testing and Standards
- Raw Materials & Sustainability
- Medical/Healthcare/PPE
- Durable Nonwovens
- High Performance Materials
- Nanotechnology
- Military Textile Applications
- Smart Textiles
- Automotive & Aerospace
- Manufacturing Technology
- Textile Care
Submissions to present in the Techtextil North America Symposium must be sent to ali.rosenberger@usa.messefrankfurt.com by May 1, 2021.
Student Research Poster Program
For students with research in technical textiles, nonwovens or a related field, the Student Research Poster Program is also now open for applications. Techtextil North America invites students perusing their undergraduate, graduate, or Ph.D. degrees to submit unpublished, technical research to be considered for this opportunity to present their findings on the show floor among industry professionals. Subject areas include but are not limited to:
Technical Textiles
- Aerospace
- Automotive
- Coated Fabrics
- Composites
- Geosynthetics
- High Performance
- Medical & Healthcare
- Military, Safety & Protective
- Nanotechnology
- Smart Textiles
Nonwovens
- Automotive
- Fibers
- Filtration
- Functionalization
- Geosynthetics
- Medical & Hygiene
- Nanofibers
- Polymers
- Wipes
Student applications must be sent to peyton.rowe@usa.messefrankfurt.com by May 21, 2021.
7H aims to set the bar in sustainable dyeing with imogo Dye-Max spray line
Swedish commission dyeing company 7H Färgeri is looking to propel itself to the forefront of sustainable fabric production with the installation of the first industrial scale imogo Dye-Max spray dyeing line. With the potential to slash the use of fresh water, wastewater, energy and chemicals by as much as 90% compared to conventional jet dyeing systems, the DyeMax has gained considerable attention since the concept was outlined and a prototype machine constructed in 2019.
7H Färgeri was founded in 1935 and has established itself as the Nordic region’s most complete dyeing and processing plant, specializing in technical and functional textiles for the automotive and soft furnishings sectors, as well as functional and protective clothing.
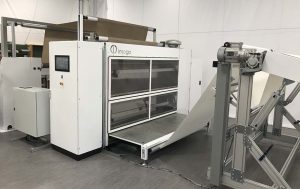
Currently under construction, the line will be delivered in the first week of March to the 7H plant close to the Swedish city of Borås. It will have a full working width of 1.8 meters with an operating speed of up to 50 meters for the reactive dyeing of cellulosic fiber-based fabrics. In addition, it will be capable of carrying out the application of a wide range of fabric pre-treatments and finishing processes, providing the company with unbeatable flexibility in production.
A proven Mini-Max laboratory unit for pre-determining application volumes and color matching will also be delivered as part of the contract.
Pilot scale trials have subsequently been carried out with many well-known international textile companies and their brand partners.
The application unit of the Dye-Max consists of a closed chamber containing a series of spray cassettes with precision nozzles for accurate and consistent coverage, in combination with the patented imogo Pro Speed valve that controls the volume to be applied.
Source: imogotech.com
Glatfelter reports strong fourth quarter earnings; with 2020 EBIDTA growth of 12%
Glatfelter Corporation, a leading global supplier of engineered materials, reported its results for the fourth quarter of 2020. On an adjusted basis, earnings from continuing operations for the three months ended December 31, 2020 and 2019, were $9.6 million, or $0.22 per share, compared with $7.7 million, or $0.17 per share, respectively. Adjusted earnings is a non-GAAP financial measure for which a reconciliation to the nearest GAAP-based measure is provided within this release. Consolidated net sales for the three months ended December 31, 2020 totaled $235.3 million compared with $231.0 million during the same period in 2019. On a constant currency basis, Composite Fibers’ and Airlaid Materials’ net sales decreased by 1.4% and 5.2%, respectively.
“Glatfelter delivered robust earnings in the fourth quarter, further contributing to a strong year amid unforeseen global economic challenges resulting from the pandemic,” said Dante C. Parrini, Chairman and Chief Executive Officer. “As businesses across the globe faced unprecedented volatility, Glatfelter continued to make progress by focusing on employee health and safety and overall operational excellence while ensuring uninterrupted supply of critical products to our customers, thereby achieving full-year adjusted EBITDA growth of 12%. We continued to realize operational and strategic benefits of our transformation that included an optimized portfolio comprised of over 85% essential consumer staples, and an improved cost structure from a flatter and more agile operating model. Also, we generated significant cash flow that translated into meaningful debt reduction, resulting in a very healthy balance sheet.”
Mr. Parrini continued, “In Composite Fibers, strong demand across nearly all product categories drove an increase in total shipments during the quarter compared to prior year. This volume increase and improved mix, combined with elevated production, enabled the segment to deliver an operating profit margin of nearly 11% for the fourth quarter. In Airlaid Materials, shipments during the quarter were above the prior year in all product categories except tabletop, which was negatively affected by the pandemic. As a result, we took more downtime in our Airlaid facilities to manage tabletop inventory, which impacted profitability. For the year, the Airlaid segment delivered an operating profit margin of approximately 12%, exceeding our guidance range.”
“As we start the new year, we remain focused on managing through the ongoing pandemic by keeping our employees safe and facilities operational. Equally important will be accelerating growth through diligent commercial execution and strategic investments such as our recently announced acquisition of Georgia-Pacific’s U.S. nonwovens operations. We believe this business is an excellent fit for Glatfelter and, given our strong balance sheet and stable cash flows, we are financially well positioned to invest in a variety of opportunities that further enhance the enterprise and align with our long-term growth strategy,” concluded Mr. Parrini.
Source: glatfelter.com
EDANA welcomes EU, UK Trade & Cooperation Agreement
EDANA, a global association serving the nonwovens and related industries, issued a statement welcoming the Trade & Cooperation Agreement (TCA) signed in December 2020 between the European Union and the United Kingdom and, in particular, its specific rules of origin for nonwovens.
The most recent available figures cover 2019, when the UK exported nonwoven roll goods worth €96 million to the EU, while export traffic in the other direction reached a value of €280 million. The UK remains the second biggest trade partner for EU local manufacturers after the United States.
Jacques Prigneaux, EDANA’s director of Market Analysis and Economic Affairs, said, “This trade agreement not only guarantees that nonwoven roll goods will be able to continue to travel between EU member states and UK without customs duties, but also recognizes that a nonwoven process is sufficient to confer the origin on the product.
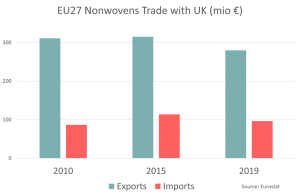
“In order to qualify for the zero preferential tariff under the EU-UK Trade and Cooperation Agreement, products classified in HS 5603 must originate in the EU or the United Kingdom. According to the specific rule for nonwovens, devised and promoted by EDANA, and included in the TCA, any nonwovens produced locally will be considered as originating in the EU or United Kingdom, even if it has been produced using non-originating materials.”
Pierre Wiertz, General Manager of EDANA said “In this news, I see two key achievements and subjects of satisfaction for nonwoven producers whom we value as the core of EDANA’s membership. On one hand, the ability for all of them to keep doing ‘business as usual’, or even expand trade opportunities, whether they trade from the EU or the UK, and on the other hand, the official recognition, hopefully once and for all, of the fact that manufacturing nonwoven roll goods is a substantial enough operation to confer origin status of the country where the resulting goods are obtained. This latter event marks another step in the independence of the nonwovens industry from the traditional textile customs rules which too often unnecessarily constrained its development.”
Source: edana.org
Gaston College announces plan to build state-of-the-art Fiber Innovation Center
The Gaston County Board of Commissioners and Gaston College are working in partnership to transfer $5.3 million in funding to the college for the addition of a new Fiber Innovation Center on the College’s Kimbrell Campus in Belmont.
The new Fiber Innovation Center (FIC) will be a facility expansion of the Kimbrell Campus and be a resource of the Manufacturing & Textile Innovation Network, a partnership between Gaston College’s Textile Technology Center and Catawba Valley Community College’s Manufacturing Solutions Center. The MTIN partnership, announced on December 15, 2020, was formed to develop a regional workforce focused on advanced materials and textile testing development. The collaboration also affords better support to each Center’s clients in the textile and manufacturing industries, expand services to other related industries, and provides opportunities for research and development.
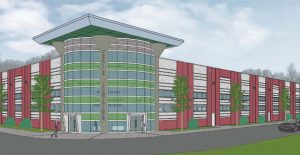
Gaston College President John Hauser has been working closely with County Commissioners and has moved forward with selecting an architect for the Fiber Innovation Center. Speaking before Commissioners on Tuesday, January 26, he showed two optional preliminary floor plans of 40,000 square feet and 22,000 square feet. Also, an exterior site plan showing the location of the new building on the Kimbrell Campus and an exterior concept design.
The Fiber Innovation Center will provide a state-of-the-art facility to develop and test advanced fibers for the advanced materials industry for products such as crucial personal protective equipment, smart textiles for the defense sector, and many other proprietary products developed by national and international clients of the MTIN.
Read the full story: https://www.gaston.edu/blog/2021/01/28/gaston-college-is-developing-a-world-class-fiber-innovation-center/
Source: gaston.edu
Price Hanna market report shows China is now largest volume market for absorbent hygiene products
Price Hanna Consultants has published a report on the global outlook for absorbent hygiene products and the key raw materials of nonwovens, fluff pulp, airlaid cores, superabsorbents and hygiene films.
The report’s analysis shows global consumption of absorbent hygiene products (disposable diapers, child pants, feminine hygiene and adult incontinence products) grew to about 691 billion units in 2020. Due to rapid market penetration and growth over the past decade, China is now the largest volume market for hygiene absorbent products. Volume in the emerging markets, collectively, is substantially larger than the combined markets for these products in North America, Western Europe and Japan. Growth rates for the next five years in the undeveloped and developing markets of Asia and Africa will continue to exceed the global average growth of this industry. These regions provide significant market penetration and volume growth opportunities for absorbent product market participants and their suppliers.
The study details the five-year market outlooks in each major country market and each geographic region. Demographic factors, such as declining birth rates and increases in elderly populations, are assessed in the projections of the potential market sizes for absorbent hygiene products. This edition also considers the impacts of COVID-19 along with a host of other recent developments relevant to the hygiene industry. It includes a fresh look at consumer market trends and developments in an expanded section about brand and product marketing strategies in the three main categories of absorbent hygiene products (baby diapers, feminine hygiene, adult incontinence).
Since 1993, managing partner Pricie Hanna has prepared 15 in-depth reports analyzing the markets for absorbent products in key countries/regions throughout the world and the important materials used in them. The last global hygiene report was released in February 2019. This updated study details the prospects for absorbent products in the key global markets of North America, Western Europe, the Pacific Rim, Central and South America, the Middle East, Central and Eastern Europe, China, India, Africa and the rest of Central Asia. The report contains unit volume market estimates for 2019 and 2020 and projections for 2025 for 46 individual countries and all geographic regions. The 2019 global and regional market share positions and volumes of the leading absorbent products competitors are estimated. The study includes 2019 and 2020 estimates and 2025 forecasts of the consumption of key raw materials used in absorbent products (cover stock, superabsorbents, fluff pulp, airlaid cores and hygiene film) by product category and region.
This 316-page report is immediately available. To obtain a detailed prospectus and report order form for this study, contact Michele Scannapieco at +1 610.793.1500 or mscannapieco@pricehanna.com.
Source: pricehanna.com
Henkel recognizes CFF cellulose fiber technology as part of its annual supplier awards program
For the 14th time, Henkel recognized its top suppliers for industry-leading performance in 2020. The event took place on January 25 – for the first time in an all-virtual setting – with more than 300 registered participants. The partners were awarded in five categories: Sustainability – Beauty Care, Sustainability – Laundry & Home Care, Innovation – Beauty Care, Innovation – Laundry & Home Care, Supply Performance.
At the award ceremony, Rik Strubel, chief marketing officer for Henkel Beauty Care, talked about the recent trend of solid beauty products in hair and body care. In the category of Best Innovation Contributor Beauty Care, Henkel awarded a second prize to CFF for its cellulose fiber technology for a fiber spray with excellent texturing performance.
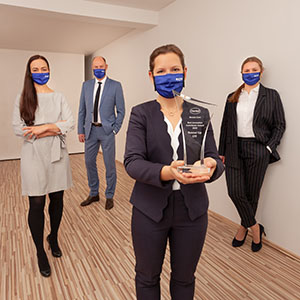
Bertrand Conquéret, president of Global Supply Chain and senior vice president of Purchasing at Henkel thanked all suppliers for their tremendous commitment and support in extraordinary times. He shared Henkel’s new 100% responsible sourcing agenda and encouraged the partners to help develop and grow Henkel’s leadership in sustainability ambitions: “Sustainability is at the core of our purposeful growth agenda. It is a leadership call and requires the commitment of all of us to take the responsibility and to deliver real progress in 2021. Leadership in sustainability – this is our joint agenda.”
In accepting its award, CFF said: “We haven been rewarded due to our successful collaboration with Henkel in developing innovative hair styling products with our bamboo fibers SENSOCEL bc 20. It was a great pleasure to be involved in the development of a market novelty. This successful project clearly shows that the functionality of cellulose fibers has an unimagined diversity and pushes the creation of new ideas.”
Source: henkel.com, cff.de
INDA announces webinar program addressing facemask standards, single-use plastics legislation & COVID-19 capacity issues
INDA, the Association of the Nonwovens Fabrics Industry, is taking the lead to inform the nonwovens/engineered materials industry with three one-hour webinars on what it sees as the toughest issues facing the North American nonwovens industry. These critical issues include facemask performance standards, single-use plastics (SUP) legislative policy issues, and industry impacts from recent capacity announcements in Spunbond/Spunmelt/”Spunlace” caused by COVID-19 demand for wipes, medical gowns and facemask materials.
The one-hour webinars will be held at 11 am EDT on March 16th, 25th, and April 6th, and include subject matter experts in facemask standards, plastics legislation, and nonwoven supply/demand analysis. Topics include:
The New ASTM Performance Standard for General Public Facemasks and Resultant Design/Product Opportunities
Tuesday, March 16th, 11 am EDT
Presenters: Dave Rousse, President, INDA, and Jeff Stull, President, International Personnel Protection, Inc.
Plastics Concerns and the Nonwovens Industry
Thursday, March 25th, 11 am EDT
Presenters: Dave Rousse, President, INDA, Jessica Franken, Director of Government Affairs, INDA, and Tom Carlyle, Nonwovens Commercial Manager-Americas, Lenzing AG
Spunbond/Spunmelt/”Spunlace” Capacity/Demand Scenarios Prompted by COVID-19
Tuesday, April 6th, 11 am EDT
Presenters: Brad Kalil, Director of Market Intelligence and Economic Insights, INDA, and Dave Rousse, President, INDA
For more information: inda.org/inda-webinars.
Source: inda.org
Techtextil North America to return to Raleigh, North Carolina, with a theme of ‘Accelerating Technology’
Techtextil North America will return to Raleigh, North Carolina, August 23-25, 2021. The show’s theme this year is “Accelerating Technology” and aims to highlight the textile industry’s high level of innovation and contribution to the global supply chain through advanced technology. North Carolina State University’s Wilson College of Textiles – internationally renowned as a leader in the field of textile education and innovation – will again serve as the Official Academic Partner, with several members of the college’s faculty also seated on the show’s Advisory Council.
Selected for their industry knowledge and expertise, the Advisory Council acts as a support to the management team in the planning and execution of the Techtextil North America Symposium and other educational content and show features, which, in line with the show’s theme, will heavily focus on advanced technology in textile design, development and end-to-end manufacturing.
This year’s advisory council will include:
Frank Henderson: President, Henderson Sewing
Dr. Karen Leonas: Professor of Textile Sciences, Department of Textile and Apparel, Technology and Management, Wilson College of Textiles, North Carolina State University
Dr. Bryan Ormond: Professor of Polymer and Color Chemistry, Department of Textile Engineering, Chemistry and Science and the Textile Protection and Comfort Center, Wilson College of Textiles, North Carolina State University
Dr. Behnam Pourdeyhimi: Associate Dean for Industry Research and Extension, William A. Klopman Distinguished Professor of Materials, Professor of Chemical and Biomolecular Engineering and Biomedical Engineering, Executive Director, The Nonwovens Institute, Wilson College of Textiles, North Carolina State University
Melissa Sharp: Associate Director, Zeis Textiles Extension, Wilson College of Textiles, North Carolina State University
The Techtextil North America Symposium will provide the latest research and technology across verticals – with insights into textile industry trends, challenges brought on by emerging technology and how to keep stride in an ever-changing, global business landscape. The Symposium will include six paid educational sessions over the course of the three day event, which will be complimented by mini-sessions on the show floor.
This year, the event will include the first-ever Texprocess Americas pavilion, supported by SPESA – featuring machinery, equipment, and technology suppliers for the sewn products industry – designed to foster new business opportunities and strategic partnerships between exhibitors and attendees.
In addition to the pavilion, SPESA will once again co-locate its Advancements in Manufacturing Technologies Conference with Techtextil North America in 2021. The conference features presentations and panel discussions from SPESA members about the products they make as well as the challenges they face as they aim to improve efficiency, speed, and accuracy in sewn products manufacturing.
Source: techtextilna.com
AATCC launches Digital Labs online training program
The American Association of Textile Chemists and Colorists (AATCC) has launched its Digital Labs program, offering online trainings, lectures, and informational discussions for textile-related topics, hosted by top industry and academic experts. The upcoming program schedule includes:
February 10
Efficacy Testing of Antimicrobial Personal Protective Equipment (PPE) presented by Matthew Hardwick, PhD, ResInnova Laboratories
Explore the technical definition of ‘antimicrobial’, current standard test methods, and how the testing field can evolve to meet future needs. The AATCC PPE Series is free for members.
February 18
Overview of Color and Colorants for Textiles presented by Tova N. Williams, PhD, TCI America
Learn about the application of color to various fiber types, dye/pigment-fiber interactions, color production, and more!
March 4
Introduction to 4D Textiles presented by Chris Pastore, PhD, Thomas Jefferson University
This session will discuss 4D textile fundamentals and offer a live Q&A for participants.
March 24
Rebuilding the Textile Talent Pipeline presented by Jasmine Cox, Textile Technology Center at Gaston College
Examine the textile talent gap and learn how to cultivate the next generation of leaders – from recruiting and developing young professionals to finding resources for talent sourcing and management.
Registration fees for live or archived – single session access:
- AATCC Individual Member OR Corporate Member Employee: $99
- Non-members: $169
- Group Rate: $2,250 (Recommended for large groups of 23pp+. Available for AATCC corporate members only.)
For more info: aatcc.org/events/digital-labs/
Oerlikon Barmag Huitong Engineering commissions its first PBS system
A polybutylene succinate (PBS) polycondensation system was commissioned at Yingkou Kanghui Petrochemical Co. Ltd. in Dalian in the Chinese Liaoning Province in January 2021. The PBS system, for which Oerlikon Barmag Huitong Engineering supplied both equipment and engineering, has a daily production capacity of 100 tons.
It is used to manufacture high-viscosity chips for biodegradable films. Consequently, Yingkou Kanghui, a subsidiary of the Hengli Group, is catering to rising demand for biodegradable polymer products, a demand that is increasing not just in China, but across the globe.
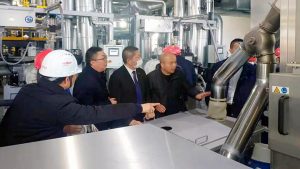
Yingkou Kanghui Petrochemical Co., Ltd., founded in 2011, predominantly produces polyester chips and films. By expanding its portfolio to include the manufacture of PBS products, the enterprise is positioning itself as a pioneer of biopolymer production.
The new plant at Yingkou Kanghui Petrochemical Co, Ltd. was production-ready with the support of Oerlikon Barmag Huitong Engineering within less than 14 months following contract signing.
Source: oerlikon.com
BASF increases price of additives for plastic applications
BASF announced a price increase for products in its additives portfolio for plastic applications globally by up to 10 percent.
The price adjustment is in response to higher costs for raw materials and logistics, according to the company.
BASF is a supplier, manufacturer and innovation partner of plastic additives. Its comprehensive and innovative product portfolio includes stabilizers which provide ease in processing, heat and light resistance to a variety of polymers and applications including molded articles, films, fibers, sheets and extruded profiles.
Source: plasticadditives.basf.com
Paper Converting Machine Co. names Andy Piotter as business development manager for its Packaging Systems unit
Paper Converting Machine Company (PCMC) in Green Bay, Wisconsin—a division of Barry-Wehmiller and a supplier of high-performance converting machinery for the tissue, nonwovens, package-printing and bag-converting industries worldwide—announced that Andy Piotter has accepted the position of Business Development Manager, Packaging Systems.
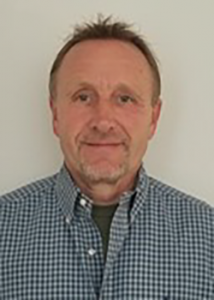
Piotter brings more than 35 years of experience in developing complete packaging systems for a variety of industries. He joins PCMC after being extensively involved in engineering, sales, and business management and development.
Source: pcmc.com