In the dynamic and global textile fiber industry with its various manufacturing processes and end-uses, news and information is breaking on a daily basis. International Fiber Journal is tracking stories relevant to our industry from manmade to natural to bio-based fibers, innovations in nonwoven, woven, braided and technical textiles, technologies for additives, bonding, coatings and polymers, and applications from apparel to hygiene to transportation, and more. Here we will post news stories relevant to textile fibers and their downstream applications on an ongoing basis. Please check back for regular updates. If you have news that you feel should be added to this summary report, please email it to Matt Migliore at mmigliore@inda.media.
Most recent update: December 31, 2020
Industry veteran Ben Talbert launches search firm to service textiles, industrial sector
Ben Talbert, with more than 17 years of experience both working in and recruiting for the industrial sectors, including the textile industry, announced that his industrial recruiting firm, Better Than Found (BTF), will launch on January 1. Specializing in professional and executive recruitment across manufacturing, engineering and construction, Better Than Found was formed on the mission to leave companies, careers and lives better than we found them.
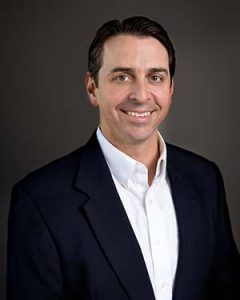
BTF does nationwide recruitment for companies in the Upstate of South Carolina and throughout the Southeast. Better Than Found is a full-service industrial consultant and talent resource, capable of sourcing vital and specialized professionals and executives. With diverse industry knowledge and experience, its team has served clients, in textiles, HVAC/R, consumer products, OEM industrial equipment and aftermarket parts supply, capital equipment design/engineering/automation/integration, plastics and packaging, automotive, aerospace, power generation, warehousing/distribution/logistics, chemicals and food and beverage.
With 10 years of direct industry experience along with seven years of recruiting across industrial sectors, Talbert holds a Textile Engineering degree from the (now) Wilson College of Textiles at the North Carolina State University. Talbert spent the first eight years of his career at Milliken, followed by two years at O’Neal, Inc. He has served on the Board of Directors for the Upstate Chapter of the Institute of Industrial & Systems Engineers for over six years. He also is a member of the Southern Textile Association (STA).
Source: btfsearch.com
EURATEX: Despite positive Q3 trends, recovery of European apparel and textile business remains uncertain
EURATEX data for the third quarter of 2020 showed a partial recovery compared to the second quarter. Nevertheless, production is still negative, and signs of a full recovery are yet to be seen, according to the association, which represents European apparel and textile organizations.
After an unprecedented T&C activity plunge in the second quarter of 2020, the third quarter showed clear improvements, notes EURATEX. During the third quarter of 2020, the EU turnover partially recovered as compared to the previous quarter, and “retail sales of textiles, clothing, footwear and leather goods in specialized stores” increased +62% compared to the second quarter. The EU27 production experienced also a rebound compared to the previous quarter with +25% in textiles and +33% in clothing.
However, the EU output reported a negative quarterly growth as compared with the same period of the previous year. The decline in the clothing industry was -15%, while for the textile, it was -7%. Spain and Italy recorded the worst performances in textiles, with production drops reaching -16.5% on average during the third quarter, while Romania and Austria were severely hit in the clothing sector with respectively -25% and -31%.
Such data tells that the signs of recovery, noticed since May, are now slowing down, due most probably to the reintroduction of stricter measures in European countries. Faced with such forecasts, EURATEX is calling upon the European Union to work on four critical areas:
- Turn sustainability and circularity into an opportunity for business.
- Invest in upskilling the T&C labor market, developing new curricula which meet today’s needs around digital production or technical textiles.
- Promote access to external markets and ensure level playing field on the EU Internal market.
- Invest in innovation, to digitalize production chains and techniques and develop new sustainable materials.
Source: euratex.eu
Glen Raven Custom Fabrics executing multi-phase global expansion plan
Glen Raven Custom Fabrics announced the latest milestones in a multi-phase global expansion plan.
The first phase, initiated at the end of 2019, includes new and upgraded equipment to support the continuing growth of Sunbrella fabrics and other Glen Raven textile products in the company’s U.S. and Asia facilities. This highly customized equipment has begun to come online and will continue in stages through the first half of 2021. It will not only increase output, but also reduce energy and water usage, according to the company. The company is also implementing system enhancements that will better address the supply chain challenges created by the pandemic and the spike in demand for Sunbrella fabrics. The improvements will enable Glen Raven to serve and communicate with customers even more efficiently.
This next phase of the expansion plan is marked by the purchase of a new production facility in Valenciennes, France, an industrial hub with ready access to major transportation routes across Europe. Once converted to meet Glen Raven’s requirements, this facility is expected to be operational by the second half of 2021. The site also allows for future production and distribution expansion.
The projects mark an investment of more than $65 million in expanded production capacity to support its customers and the increased demand for Sunbrella, Dickson and other Glen Raven fabrics. Future phases of the program include additional production and distribution capacity for the U.S. and Asia markets.
Source: glenraven.com
Techtextil and Texprocess North America to present webinars on Industry 4.0 for textile printing and sustainability
Techtextil and Texprocess North America announced two new virtual symposium sessions for the month of January 2021. The online programs include:
INDUSTRY 4.0 & THE EVOLUTION OF PRINTING | January 13, 2020 | 2:30 PM EST
This session will feature providers of fabric printing who use both analog and digital printing technologies. Attendees will learn how the latest developments in printers, inks and materials have removed the quality gap between analog and digital processes – and in some cases, even offer improved quality. Gain an understanding of when and why digital printing can and should be used in lieu of analog technologies, as well as some of the challenges the industry still faces in its analog-to-digital transformation journey.
HOW TO IMPLEMENT YOUR ROADMAP TO SUSTAINABILITY | January 14, 2020 | 11:30 AM EST
As the textile industry moves towards more sustainable business practices, many companies are left trying to figure out HOW to take steps forward towards their goals. In this panel-style discussion, industry professionals representing various pieces in the supply chain will discuss how to benchmark sustainability and how to set practical sustainability goals for the next month, the next year, and the next 10 years.
The session will explore the machinery, materials, programs, and processes companies can implement to accomplish these goals.
- Reduce waste and emissions
- Source sustainable raw materials, including fibers, dyes, chemicals, and coatings
- More efficiently use and recycle resources like energy and water
- Sustainably apply and use chemicals, dyes and coatings
Sessions are being offered with a 25% discount using promo code TREAT25VS through January 15th, 2021.
Register for symposium sessions: http://bit.ly/techtextilNAsymposium_012021
Source: https://techtextil-north-america.us.messefrankfurt.com/us/en.html
Callaly Tampliner receives U.S. FDA 510(k) clearance
Callaly, manufacturer of feminine hygiene products, received 510(k) clearance from the U.S. Food and Drug Administration (FDA) for its Callaly Tampliner. The tampliner is a brand new period product that combines an organic cotton tampon with a soft mini-liner for extra protection against leaks. It’s convenient, mess-free and hypoallergenic.
The Tampliner, which is designed and manufactured in the UK and launched in February 2020, was invented by Dr Alex Hooi, a senior British gynaecologist and Fellow of the Royal College of Obstetricians and Gynaecologists and developed by garment technologist Ewa Radziwon, who trained at London College of Fashion. The product is protected by four granted patent families covering 80% of the $34bn global market. It is now being exported across Europe to Sweden, the Netherlands and Ireland.
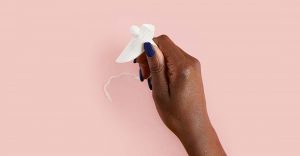
Callaly’s multiple-award winning Tampliner was recently recognized as a “next-gen tampon” in TIME’s 100 Best Inventions of 2020 — its annual list of inventions that are making the world better, smarter and even a bit more fun.
Callaly’s founder and CEO, Thang Vo-Ta said: “We are excited that Callaly was able to receive 510K clearance from the U.S. Food and Drug Administration, opening up the important U.S. market for our Tampliner, now earmarked for launch in Summer 2021. We are committed to delivering innovative period care products that truly meet the needs of people with periods, through dedicated innovations that are highly differentiated and adhere to the highest possible standards.”
Source: calla.ly
The Jones Family of Companies announces several appointments in support of its nonwovens businesses
The Jones Family of Companies, provider of engineered nonwoven products spanning multiple markets such as sleep, furniture, cold chain and protective packaging, acoustics, and floor care, has made several new appointments in quality control, operations and human resources. Pranil Vora joins Jones as manager of Quality Engineering and Performance Improvement in Morristown, Tennessee; Alex Webster joins as plant operations manager in Humboldt, Tennessee; and Kassey Cruz joins as HR generalist and operations recruiter in Charlotte, North Carolina.
Vora earned his bachelor’s degree at the D.K.T.E Textile and Engineering Institute in India, where he participated in three separate internships and received a number of achievements and certifications from institutions around the world, as well as having articles published in several notable textile publications. In May of 2020, Vora earned his M.S. in Textile Engineering from North Carolina State University in Raleigh. Professionally, Vora has worked in the Research & Development departments at Mann+Hummel’s filters division and most recently at The Nonwovens Institute, becoming proficient in several aspects of the nonwovens industry.
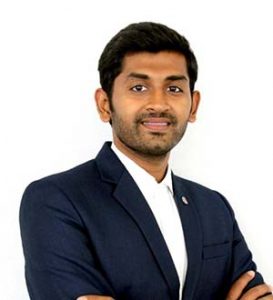
Since earning his bachelor’s degree from The Citadel, The Military College of South Carolina in 2016, Alex Webster has built a strong and diverse career in the textile industry. Immediately after graduation, he began working in management for Parkdale Mills, overseeing the Carding department and assisting in upgrades to the Thomasville, NC production plant. In 2019, he began working for Frontier Yarns, moving between supervisor and management roles at three separate facilities across the southeast U.S.
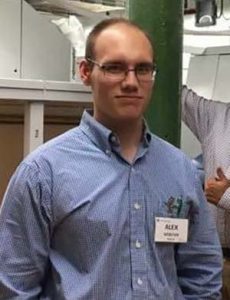
Operations Manager, The Jones Family of Companies
Kassey Cruz joins the Jones business office located in Charlotte, North Carolina. Cruz earned her bachelor’s degree in Psychology from Montclair State University in New Jersey, achieving a certification in Human Resources Management in 2020. During her undergraduate, Cruz participated in an HR internship at Urban CoalHouse, gaining valuable experience in managing the infrastructure of a workplace. After graduation, she joined Sumitomo Mitsui Trust Bank in New York City as an HR Generalist, further developing her skill set in HR management and recruitment.
With Jones, Cruz will provide direct recruitment efforts for manufacturing associates across all five of the company’s nonwovens plants.
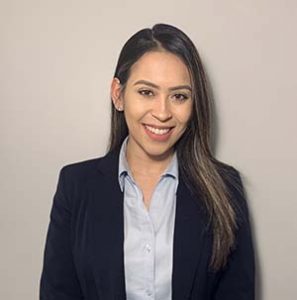
Source: jonesfamilyco.com
MMI Textiles to open 30,000 sq.ft. production facility in North Carolina
MMI Textiles Inc., a global supplier of industrial and custom fabrics and textile components, has announced an expansion of its operations, including the opening of a 30,000-square-foot production facility in Lenoir, North Carolina.
The new facility in Lenoir, NC is scheduled to open in the first quarter of 2021, and it will focus on manufacturing and printing narrow fabrics, including a full line of mil-spec webbing and binding tape products. The main driver behind the new operation is MMI’s CTEdge Printed Narrow Fabrics that use patented technology to give the border of webbing and binding tape a more concealed edge, because it is woven with different color threads that allow it to blend into the materials behind it. This product line has seen strong growth over the last few years with sales on a global scale and multiple international distributors.
As part of its expansion, MMI will hire new staff and acquire new equipment in Lenoir to ensure better control of the manufacturing process for this line. The new facility will house both MMI Textiles’ new manufacturing facility and Mikan’s print facility under one roof.
The new MMI Textiles manufacturing and print facility will be integrated under one roof to ensure efficiencies and consistencies. All sales and customer service transactions will continue to be handled through existing channels.
Source: mmitextiles.com
International Conference on Cellulose Fibres announces Innovation Award nominees
The 2nd International Conference on Cellulose Fibres (CCF), to be presented virtually February 2-3, 2021, will mark the debut of the “Cellulose Fibre Innovation of the Year” recognizing important developments in new technologies and applications.
Out of 12 nominees submitted for consideration through the program, six have been nominated as finalist for the Innovation Award. The selection was made by a jury consisting of nova‑Institute, the conference’s sponsoring organization, and the conference’s advisory board. Conference attendees will elect the three winners. The award finalists are:
Bast Fibre Tech (Canada): Compostable fiber products from agricultural hemp and flax waste
BFTi produces compostable fiber products out of agricultural waste from hemp and flax processing. Using biogenic waste from the production of fast-growing crops instead of using wood or fossil resources is environmentally and economically more sustainable. Applications for the obtained fiber with moisture absorbing properties are for example toilet paper and recyclable, thus flushable cleaning wipes.
Empa – Laboratories for Materials Science and Technology (Switzerland): Cellulose nanofiber assisted biomimetic aerogels for EMI shielding
Empa researchers combined cellulose-based aerogels with silver nanowires. The flexible composite blocks high-frequency electromagnetic radiation, which is traditionally achieved by using inflexible metal sheets or metallized foils. This ultra-light electromagnetic shielding material can be used to protect electronic components or the transmission of signals from electromagnetic fields caused by neighboring electronic devices or motors.
www.empa.ch/web/s604/cellulose-emi-shielding
Kelheim Fibres (Germany): Plastic-free absorbent hygiene products
Kelheim Fibres developed plant-based fiber solutions for absorbent hygiene products. These comprise of speciality fibers for the single layers of AHP with different functionalities: a hydrophobized fiber for the top sheet, a trilobal fiber for the acquisition/distribution layer and a hollow fiber for the absorbent core. These biodegradable and sustainably manufactured fibers enable the replacement of plastic fibers without a loss of performance. The material has the potential to be used also for the production of textiles, such as reusable menstrual underwear.
Metsä Spring (Finland): Textile fiber based on paper‑grade pulp
The Metsä Group is developing a more energy-efficient process based on a new solvent family to produce Man-Made Cellulosic Fiber (MMCF). Using ionic liquids, the MMCF can be produced from paper-grade pulp, avoiding the use of energy-intensive dissolving pulp.
www.metsaspring.com/project/textile-fibre-from-paper-grade-pulp/
OrganicDisposables (Poland): FibriTech – a porous and light material from cellulose for soilless farming
FibriTech is a new process for the production of porous and light material from cellulose and lignocellulose. A mixture of fibers can be used, including waste and recycled fibers. This extends the possible feedstock for usable materials and reduces waste. Desired properties are derived by the application of bio-additives.
Stora Enso (Sweden): Cellulose-based Foam by Stora Enso – a lightweight cellulose-based foam for packaging
“Cellulose-based Foam by Stora Enso” is a lightweight foam material made from cellulose. It is designed as an eco-friendly alternative for fossil-based packaging and cushioning materials such as expanded polystyrene or polyethylene. The foam has comparable shock-absorbing and insulating properties whilst being bio-based, biodegradable, compostable and recyclable in ordinary paper recycling.
www.cellutech.se/cellulose-based-foam.html
The International Conference on Cellulose Fibres will cover the entire value chain from lignocellulosic feedstock, dissolving pulp, cellulose fibers – such as rayon, viscose, Modal, lyocell, etc. – to a wide range of applications, woven textiles (clothing) and nonwovens (wipes and technical applications).
View the full conference program: www.cellulose-fibres.eu/programme/
To register: www.cellulose-fibres.eu/registration/
Source: cellulose-fibres.eu
Freudenberg Performance Materials, Ratti develop process to reuse silk textiles for thermal insulation
Freudenberg Performance Materials (Freudenberg) and Ratti, the Italian fashion textile company, have developed a process for reusing silk textiles and using them for the manufacturing of high-performance thermal insulation, which Ratti is currently launching onto the market. As a production partner in this project, Freudenberg is contributing to the sustainable development of the clothing and textile industry.
The practice of using recycled materials from other industries, such as post-consumer PET bottles, has been common practice in the textile industry for years. Freudenberg and Ratti are now re-using silk textiles from their own industry, the clothing industry, in a jointly developed process. Ratti re-uses silk textiles (outer fabrics/clothing) and Freudenberg uses this to produce thermal insulation made from 70% re-used silk, which Ratti then markets.
Freudenberg’s airlaid technology plays a key role in the re-use of silk textiles, enabling Freudenberg to produce waddings with a three-dimensional structure from this material. This leads to the formation of countless tiny air chambers, which give the padding excellent thermal insulation properties combined with exceptional breathability. Its high dimensional stability and wash resistance and durability make this wadding made from 70% re-used silk textiles a good fit for environmentally conscious outdoor enthusiasts, according to Freudenberg.
Source: freudenberg-pm.com
Lynda Kelly named Senior VP, Americas at Suominen
Lynda Kelly has been appointed Senior Vice President, Americas business area for Suominen, effective Jan. 1, 2021. Lynda has a long experience in different management positions at Suominen. She will continue to report to Suominen President and CEO, Petri Helsky.
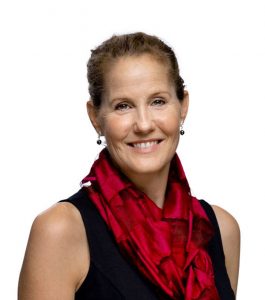
“I am happy that we were able to appoint an excellent internal candidate to this position utilizing her experience and versatile expertise in nonwovens business. Lynda is energetic and efficient and she knows the company very well, as she has worked for Suominen since 2014,” says Petri Helsky, President and CEO of Suominen.
Source: suominen.fi/en/
Gerald Vogt to succeed Rolf Strebel as CEO of Stäubli
Stäubli, a provider of industrial and mechatronic solutions, is starting the new year with a new Chief Executive Officer. Gerald Vogt, previously responsible for the global business of the company’s Robotics Division, will take over as CEO from retiring Rolf Strebel, effective Jan. 1, 2021.
With Vogt, an experienced manager from within the company’s own ranks will take over the management of the company. The 50-year-old Franco-German engineer and business economist has been responsible for the global Robotics business as Group Division Manager since mid-2016.
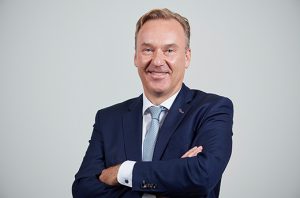
When he joined Stäubli almost 20 years ago, Gerald Vogt initially moved from the development and production site in Faverges, France, to the U.S. for several years. As Division Manager he significantly expanded business for Stäubli Robotics North America. Afterwards he returned to Faverges as Head of Development before taking over responsibility for the German business as Head of Stäubli Robotics in Bayreuth.
Christophe Coulongeat will assume the global responsibility for the Robotics Division on Jan. 1, 2021. The French manager has been Deputy Division Manager since 2018 and previously gathered extensive experience in the packaging and automation industry in France, Austria, the United Arab Emirates and Switzerland.
Source: staubli.com
KARL MAYER integrates North American Stoll office; invests in Greensboro, North Carolina facility
Textile machinery company KARL MAYER acquired flat-knit technology specialist STOLL earlier in 2020. As a next step in the integration of the North American operations, STOLL America’s operation in New York City will close and resources and activities will be integrated into KARL MAYER’s Greensboro, North Carolina location. This process started in October and will be completed at the end of the year.
The STOLL core team in its new location will include business and technical management, textile design and product development, STOLL machine programming, and customer service. Some team members will relocate from New York and others will be new.
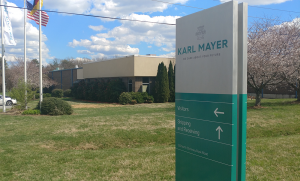
The team’s focus will be twofold, serving the needs of the STOLL machine market with innovative machines, spare parts and technical service. And equally important, innovation support services to customers, brands, incubators, startups and educational institutions. These support services include textile product design and development, sample, prototype and small collection production and training.
For these new activities, KARL MAYER is making a major investment in the Greensboro building, adding a state-of-the-art textile development and visitor center. This center will have customer collaboration and training areas with end-product samples, STOLL machines for demonstration, training and production purposes, and a prototype finishing and assembly operation. The new center will offer similar collaboration opportunities for industry partners working with other KARL MAYER technologies. It is planned to be completed in March 2021.
In related news, KARL MAYER China will showcase new solutions of the STOLL brand for flat knitting during an in-house presentation, Dec. 17–19, in Changzhou.
KARL MAYER acquired STOLL in February 2020, and shortly afterwards moved its Shanghai plant to KARL MAYER’s Changzhou site as one of the first integration projects.
Highlights of the face-to-face, in-house event include a brand new flat knitting machine for the volume market, demonstrating its skills in the automated and fully digitized production of an individualized fashion article, innovative software solutions for flat knitting and design inspiration for the creative process. There will also be a presentation of an innovative technology for the production of everyday masks; during the knitting process, the nose bridge for the face covering is inserted automatically. Representing warp knitting technology, a weft knitting machine will demonstrate how chic home textiles and garments can be efficiently produced.
For more information on the exhibits and the in-house show program: https://www.karlmayer.com/en/news-and-media/events/stoll-product-show-china-2020/.
Source: karlmayer.com
Kimberly-Clark to invest $140M to expand Corinth, Mississippi, nonwovens manufacturing facility
Kimberly-Clark has approved a significant investment in its Corinth, Mississippi, manufacturing facility, the second major investment in the past 12 months. The investment further expands capacity and brings nonwovens capability in support of Kimberly-Clark’s continued growth in North America, according to an announcement by the Mississippi Economic Development Council.
With an estimated investment of more than $140 million, the project is the company’s largest ever investment in its global nonwovens capabilities. It will expand the Corinth facility by more than 150,000 square feet and install innovative new technology to manufacture nonwovens components primarily for Huggies, Pull-Ups, Poise and Depend products.
The investment is expected to deliver increased capacity, enhanced product performance and greater manufacturing efficiency. The company will add at least 33 new full-time jobs to its current employee base. Hiring for these roles is expected to begin later this year.
The Mississippi Development Authority is providing assistance for building construction. Alcorn County is negotiating a fee-in-lieu agreement in support of the project. The Tennessee Valley Authority also is assisting with the project.
Kimberly-Clark employs more than 300 workers in Corinth between its nonwovens and K-C Professional* facilities. The shared site produces nonwovens components for the company’s Huggies, Pull-Ups, Poise, Depend, WypAll* and Block-it* brand names, as well as industrial wipers under the WypAll* brand name.
Source: medc.ms
Protective apparel manufacturer Kappler hosts leaders to discuss workforce development
Kappler hosted a group of state officials to discuss the critical and changing needs of workforce development programs. The group was led by Alabama Lt. Governor Will Ainsworth and included other elected officials plus education leaders from K-12, the community college system and the governor’s office.
The event was organized by Lt. Gov. Ainsworth, based on the suggestion of Kappler President and CEO Laura Kappler-Roberts, who had conveyed a common theme heard from industry leaders today: “I just need people to show up for work!”
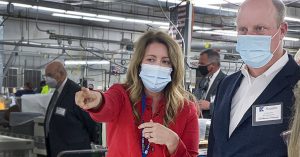
In addition to her role at the helm of Kappler, Kappler-Roberts serves as a board member for the local K-12 school system, The Schools of Guntersville. She is a long-time proponent of STEM (Science, Technical, Engineering, Mathematics) education initiatives, and as a manufacturer she is especially concerned with workforce development.
She explained to the group how small and large businesses alike are experiencing a tremendous challenge with retaining a productive workforce and this has implications of stunting industry growth.
In Kappler’s case, the local workforce limitations have forced the company to look outside of its Marshall County, Alabama, employee base for both domestic and offshore contractors to provide production capacity to meet customer demand.
Source: kappler.com
Hamle leverages Monforts Thermex textile dyeing range for continuous improvement
Leading Turkish textile printing company Hamle has installed a new Monforts Thermex dyeing range as part of its ongoing strategy of continuous investment.
Hamle’s plant in Çorlu already houses a Monforts 10-chamber Montex stenter and two Monforts sanforizing ranges on which the company carries out an extensive range of finishing processes.
The new Thermex range further integrates a number of processes on technology all from a single supplier.
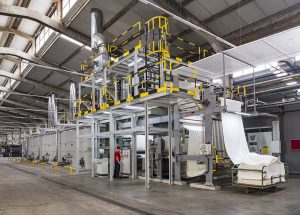
The Thermex universal hotflue for continuous dyeing, condensing and thermosoling achieves unrivalled reliability even at maximum fabric speeds, for exceptional cost-effectiveness when dyeing both large and small batches of woven fabrics.
The new range installed for Hamle benefits from the Econtrol process for reactive dyestuffs.
This is quick and economical one-pass pad-dry and wash off process, with drying in the hot flue at 120-130 C and controlled humidity (25-30% by volume) to obtain fixation in 2-3 minutes.
Econtrol ensures excellent reproducibility of all colors, improved dye penetration on difficult fabrics and no risk of the browning of cotton or other cellulose fibers due to the low fixation temperature.
“Investment in new technology and capacity expansions are very important to us, in order to stay ahead in terms of sustainable, high quality production,” says Hamle general manager Gürkan Uzuner. “We carefully assess the benefits of each advanced new technology in order to thrive in a sector that is constantly changing.”
Source: monforts.de
Eurofins expands testing capabilities with CNAS accreditation in China
Eurofins Softlines & Leather is pleased to announce that new accreditations have been awarded by the China National Accreditation Service (CNAS) to two Eurofins laboratories in Hangzhou and Shanghai, China.
The laboratory in Hangzhou has received over 200 new accreditations from CNAS, which relate mostly to analysis of textile and leather products with popular mechanical testing standards, such as GB/T 22853-2019 for knitted sportswear, GB/T 32614-2016 for water-resistant outdoor garments, FZ/T 73043-2012 for knitted shirts, and QB/T 2858-2007 for schoolbags.
With accreditation secured, the laboratory also develops new China GB testing standards for overseas and domestic customers, such as GB/T 22583-2009 for radiation-resistant knitwear, GB/T 22845-2009 for anti-electrostatic gloves, and FZ/T 73039-2010 for rubberized vibration-proof gloves.
The new accreditations secured by the laboratory in Shanghai also cover common chemical testing items, such as EN 17132:2019 determination of PAH, EN 17131:2019 determination of DMF, EN 17130:2019 determination of DMFu, and EN ISO 17226-1:2019 determination of formaldehyde, offering a wider test selection to our customers.
Source: eurofins.com
Lenzing earns spot on CDP’s ‘A List’ for tackling climate change and the protection of forests
The Lenzing Group has been recognized by the global environmental non-profit CDP, securing a place on the ‘A List’ for tackling climate change, as well as acting to protect forests – two of the three environmental themes covered by CDP.
CDP’s annual environmental disclosure and scoring process is widely recognized for corporate environmental transparency. This year, more than 5,800 companies were scored based on data submitted through CDP’s questionnaires.
“We are particularly proud to be the only first-time discloser who has achieved an ‘A’ score for tackling climate change and acting to protect forests. The double ‘A’ score reconfirms our long-term sustainability strategy and is an exciting acknowledgement of our efforts on transparency as well as sustainable raw material sourcing”, says Stefan Doboczky, CEO of the Lenzing Group.
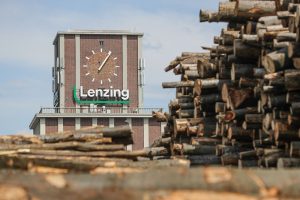
In 2020, over 515 investors with over US$106 trillion in assets and 150+ major purchasers with US$4 trillion in procurement spend requested companies to disclose data on environmental impacts, risks and opportunities through CDP’s platform. Over 9,600 responded – the highest ever.
A detailed and independent methodology is used by CDP to assess these companies, allocating a score of A to D- based on the comprehensiveness of disclosure, awareness and management of environmental risks and demonstration of best practices associated with environmental leadership, such as setting ambitious and meaningful targets. Those that don’t disclose or provided insufficient information are marked with an F.
Already in the year 2019, Lenzing became the world’s first producer of wood-based cellulosic fibers making a strategic commitment to dramatically reducing its carbon footprint and cutting its emissions per ton of product by 50 percent by 2030. This target has been scientifically verified and approved by the Science Based Targets initiative. Furthermore, by the year 2050, Lenzing aims for Net-Zero emissions.
Sustainable fiber innovations such as the introduction of the first TENCEL™ branded CarbonNeutral® fibers and a blockchain-enabled traceability platform are an integral part of Lenzing’s sustainability strategy since they help to combat climate change and trigger a new level of transparency along the entire value chain. In addition to that, pioneering technologies like REFIBRA™ and “Eco Cycle” contribute to a circular economy by combining the environmentally responsible lyocell fiber production with the upcycling of cotton waste materials.
Lenzing is proud of its decades-long clean record of sustainable wood sourcing, evidenced by its long-standing credible commitment to wood certifications. The company’s commercial wood sources are 100 percent either certified by FSC®1 or PEFC™2, or controlled in line with FSC® standards. The combination of a stringent wood sourcing policy and the dedicated commitment to the CanopyStyle Initiative confirms that the production of Lenzing’s wood-based cellulosic fibers does not contribute to deforestation.
Source: lenzing.com
Texpertise Network touts accomplishments, announces further measures to implement Sustainable Development Goals
Since 2019, the Messe Frankfurt Texpertise Network has been working with the Conscious Fashion Campaign and the United Nations Office for Partnerships to bring the Sustainable Development Goals to all 58 textile events in the network worldwide. Numerous measures have already been implemented. Others are imminent.
Shortly before the start of the COVID-19 crisis, the UN Secretary-General Antonio Gutérrez hailed the start of the Decade of Action. As of 2020, the international community now has just 10 years to achieve the 17 Sustainable Development Goals (SDGs) to which the UN Member States committed themselves in the 2030 Agenda. As part of the collaboration with the Conscious Fashion Campaign and the United Nations Office for Partnerships, the Messe Frankfurt Texpertise Network will put the SDGs on the agenda of additional events in December, thus further supporting their implementation in the fashion and textile industry.
Ever since the expanded collaboration between the Messe Frankfurt Texpertise Network, the Conscious Fashion Campaign and the United Nations Office for Partnerships was announced at the UN headquarters in New York in December 2019, the international Messe Frankfurt textile events have implemented numerous measures to support the SDGs.
At the Messe Frankfurt textile events in Germany alone, a number of things came to fruition: the most recent physical and digital editions of Heimtextil, the leading trade fair for home and contract textiles and Neonyt, global hub for fashion, sustainability and innovation, offered panel discussions, press conferences and video messages, including with the Conscious Fashion Campaign and United Nations Office for Partnerships. An SDG Lounge in the Green Village at Heimtextil and selfie walls with the SDGs inspired exhibitors, visitors and influencers alike to engage with the 17 goals and share them on their social network channels. Podcasts were produced that can still be listened to on the Neonyt and Heimtextil channels and Neonyt also hosted, for example, the influencer challenge ‘Let’s wear the goals!’.
A great deal has also already been achieved internationally: in March 2019, Neonyt organised a showcase with selected Neonyt brands to mark the foundation of the ‘UN Alliance for Sustainable Fashion’ in Nairobi. Techtextil India launched Techtextil NEXT at its 2019 edition, India’s first hackathon for technical textiles and sustainability. Among those who attended were Shrikar Dhole, founder and CEO of the SDG Foundation and Niharika Gautam, who campaigns for the achievement of the SDGs in the fashion industry and co-leads the fashion section of the All Ladies League Delhi. The Heimtextil Russia 2020 Digital Edition was able to attract a prominent figure to give a message of greeting, namely Vladimir Kuznetsov, head of the UN Information Centre (UNIC) in Moscow. The digital edition of Texworld USA (now Texworld New York City) and Apparel Sourcing USA in summer 2020 offered a talk by the Conscious Fashion Campaign and supported the production of a podcast with Claire Kells from the UN Global Compact.
With its SDG actions to date, Messe Frankfurt Texpertise Network is estimated to have reached around 146,000 visitors, 170,000 followers on social media channels and 65,000 subscribers to newsletters about participating events at home and abroad. Added to this is also the approx. 2.5 million followers of the influencers involved in the actions.
Source: messefrankfurt.com
Polygiene, Body Doctor partner on antibacterial fabrics for eye compresses and facemasks
Polygiene and Body Doctor have partnered to bring antibacterial fabric to eye-care, eyelid hygiene and facemasks.
Under terms of the deal, Body Doctor will offer its AB+ face masks with Polygiene ViralOff antimicrobial technology with an anticipated launch date of December.
Polygiene Biostatic technology is also incorporated in all the Eye Doctor Sterileyes eye compresses, a unique feature that has become a core component of the company’s overall product offering and performance. With an exclusivity agreement and very strong sales momentum in 2020 – order value of approximately 1 million sek, Polygiene expects to see even higher numbers in 2021.
Source: polygiene.com
PFNonwovens to add two new spunmelt production lines, expanding North American Center of Excellence
PFNonwovens, a global producer of nonwoven fabrics with operations in Europe, the U.S. and Africa, is investing to expand its Hazleton site in Pennsylvania. This expansion at its North America Center of Excellence will significantly increase manufacturing capacity and allow PFN to grow its medical and hygiene markets, according to the company.
The investment, in two phases, will enhance both global and regional innovation to meet the growing market needs for high levels of softness, comfort and sustainability.
Phase 1, which is now underway, will see an initial outlay of more than $70m for an expansion of the manufacturing facilities at the Hazleton site to include the latest Reicofil R5 technology. This exciting plan allows PFN to commercialize innovation that combines two proprietary technologies in order to produce revolutionary, cottony-soft hygiene products for the North American market. Completion of phase 1 is planned for mid-2021.
“We are the first to invest in the latest R5 machinery in the US. This commitment, in combination with our unique proprietary technology, allows us to produce consumer-preferred ultra-high loft, soft and textured nonwoven fabrics. This solidifies PFN’s position as a global leader in the production of innovative spunmelt nonwoven fabrics.” said Shane Vincent, Chief Commercial Officer & Global Head of Business Development.
A Phase 2 site expansion will see PFN invest in the building of a second production line presently scheduled for completion in 2022.
This latest development at the Hazleton site is expected to result in more than 60 new job opportunities at PFN over the course of the next two to three years.
Source: pfnonwovens.com
Jacob Holm to expand spunlace capacity in Candler, North Carolina
Jacob Holm’s board of directors approved a capability expansion of an existing line at the company’s Candler, North Carolina, facility. This comes in addition to the significant Project Boost capacity investment announced in June 2020, which is on track to be completed as scheduled, with waves of equipment installations currently progressing as planned at all sites.
The new equipment in Candler is expected to launch by December 2021 and will target further expansion of sustainable products, including more efficiency in running natural and innovative fibers.
This investment specifically increases spunlace (hydroentangle) capacity.
Says CEO Martin Mikkelsen, “We so appreciate the hard work of our team members who have been critical in making this happen, as well as local officials in Buncombe County, North Carolina, for their unwavering support of local businesses.”
Source: jacob-holm.com
NCTO issues recommendations to incoming US Biden administration
National Council of Textile Organizations (NCTO) President and CEO Kim Glas issued a statement outlining immediate steps President-elect Joe Biden’s administration and a new Congress can take to bolster the U.S. manufacturing sector. As President-elect Biden has named several key members of his economic team in recent days, the U.S. textile industry stands ready to work with this critical team, according to the statement. NCTO is also eager to work with the new Congress on advancing these bipartisan priorities.
The U.S. textile industry looks forward to working with President-elect Joe Biden’s transition team and his administration to provide input on key policies outlined in the campaign to prioritize investing in American manufacturing and its workforce, onshoring critical supply chains, and cracking down on the predatory trade practices that have harmed the manufacturing sector and U.S. jobs. Glas says NCTO agrees with the President-elect that the U.S. must not revert to status quo trade policies that have undermined our nation’s resilience and exacerbated income inequality by impacting the manufacturing sector and promoting a race to the bottom that have especially hurt the nearly two-thirds of the American workforce without college degrees.
According to Glas, there are four immediate steps the Biden administration can take in the first months in office to help boost investment in the U.S. textile industry and onshore critical PPE supply chains:
- Expand investment in American-Made PPE
- Appoint a high-level COVID-19 coordinating supply chain team
- Continue to support tariffs and strong trade enforcement
- Provide targeted stimulus to U.S. manufacturers and workers
Source: ncto.org
ANDRITZ to acquire Laroche
ANDRITZ will take over all Laroche entities and its business worldwide. Closing of the transaction, which is subject to approval by the ANDRITZ Supervisory Board, is expected at the beginning of 2021.
Laroche is a leading supplier of fiber processing technologies such as opening, blending and dosing, airlay web forming, textile waste recycling and decortication of bast fibers. The product portfolio further complements the ANDRITZ Nonwoven product range. ANDRITZ is now able to offer the complete supply and value chain, from the raw material, to opening and blending, web forming, bonding, finishing, drying, and converting. Laroche’s high-performance technologies for opening and blending enhance the ANDRITZ scope of supply for spunlace, needlepunch and wetlaid production lines. Moreover, both companies have agreed to further strengthen the development of their existing technologies for high-speed and high-capacity applications and also to continue pursuing the development of textile recycling processes in order to stay ahead of the changes the industry is facing.
Laroche SA has been developing fiber processing technologies for more than 100 years. With integrated manufacturing, the company supplies lines for a wide range of industries/products: spinning, bedding and furniture, automotive, acoustic and thermal insulation, geotextiles, filtration, wipes, and many more.
Source: andritz.com
INDA publishes North American Nonwovens Industry Outlook, 2019-2024
INDA’s North American Nonwovens Industry Outlook, 2019-2024 is organization’s 11th analysis of the nonwoven/engineered materials market since its first overview of the industry in 1995. INDA’s exclusive content provides analysis across all of the nonwoven end-use markets, including 133 disposable and 129 durable categories, to provide the most comprehensive and accurate view available of the total North American nonwovens industry. Detailed supply (capacity, production, and trade flows) and demand data are presented for the North American industry for 2014, 2019, and a forecast for 2024.
INDA designed this report to support strategic business planning and decision-making using INDA’s proprietary demand model of 262 nonwoven categories. The projections in the report were made by analyzing current market trends and driving forces to highlight the market potential in terms of dollar value, units, and volume in both square meters and tonnage.
Dave Rousse, INDA President, said, “This report provides the most actionable insights available on demand prospects in the most important disposable and durable market segments. No other report has the primary data that INDA gathers, making this the most reliable and definitive view of the industry through 2024. Anyone who must assess, understand, and manage the assets of an organization would benefit from this essential business planning tool.”
The report features:
- Insight into the overall impacts of Covid-19 through to 2024;
- Overall markets based on an in-depth combination of primary and secondary research;
- Baseline economic and demographic trends and forecasts, as they are significant drivers of demand within the North American nonwovens industry;
- Industry consumption figures by sales, units, square meters, and tonnage for nonwoven materials in 11 main end use markets and their numerous subcategories for 2014 and 2019, and provide a forecast for 2024;
- Industry trends and drivers within each of the end use markets;
- End use market segmentation and production processes to provide greater precision in categorizing the industry
For more details: https://www.inda.org/north-american-nonwovens-industry-outlook-report-2019-2024/
Source: inda.org
Despite impacts from COVID-19, study shows composites industry remains optimistic about the future
The ongoing epidemic of COVID-19 that has been affecting the world’s economy since last winter has had a tremendous impact on many major industries, including aerospace and automotive, at the heart of the composites industry. Although the outlooks seem uncertain for the latter, the composites industry has remained resilient and shows strong adaptability during this crisis, according to a new report by JEC Group. The survey on which the report is based targeted 1,500 international respondents in May and October 2020 to evaluate the impact of COVID-19 on their company. Results found many industrials are looking forward to the future with much optimism.
- 1 Out of 2 company remains optimistic about the future
On a global scale, the composites industry has resisted much the impact of COVID 19.
- 64% of companies are operating at 76%-99% of their capacity showing a positive sign of recovery post-COVID 19.
- Half of the respondents have shown concerns over business opportunities. The crisis has pushed them to reinvent themselves shortly to support production capacities and avoid downturns.
- Only 25% express concerns regarding innovation and R&D. Their main objective is to turn to more investment in R&D to innovate in the future.
The survey also revealed that 50% of the respondents changed materials suppliers to cope with supply chain issues. Many have changed their foreign providers to turn to local ones to avoid supply chain delays, and 70 % plan to remain on the same path in the future.
Also, 25% of the companies have switched their production to manufacture healthcare production in May, 30% of them will continue in the long run showing a growing interest in this sector.
Future perspectives and problematics:
- 1 out of two companies are optimistic about the evolution of the situation within the next 18 months; this is consistent across regions, companies’ types, and sizes
- 50% of respondents considered entering a new activity sector. Sustainability and renewable energies being main ones.
- Renewable energy, Sports and health sector, Marine, Building, Railway, and Defense are considered to be in the top new sectors to enter in the future.
- 50% consider that innovation is critical to enter new markets and new manufacturing processes. Innovation sources via universities and startups will remain stable whatever the region.
- The top 3 innovation drivers are reducing cost, competition concerns, and new customers’ needs.
Source: jeccomposites.com
ANDRITZ, Infinited Fiber extend agreement to develop regenerated fiber technology
International technology group ANDRITZ and biotechnology group Infinited Fiber Company have signed a cooperation agreement to develop the process and equipment solutions for Infinited Fiber Company’s textile fiber regeneration technology. The technology can turn any cellulose-rich raw material, including discarded textiles, used cardboard or rice or wheat straw, into cellulose
carbamate fibers – unique, high-quality textile fibers with the look and feel of cotton. ANDRITZ is the process equipment supplier for the technology. The two companies have worked together to carry out trials since the end of 2019.
Under the newly signed cooperation agreement, the two companies will work together to develop the factory process and equipment solutions, aiming to perfect every step in preparation for the technology to be scaled up to commercial scale production. Infinited Fiber Company currently operates two pilot facilities in Finland. The operations
have a nominal combined capacity of 150 metric tons/annum.
Under the new agreement, ANDRITZ and Infinited Fiber Company will spend the next six months collaborating on the development, testing and validation of the process and equipment solutions,
with ANDRITZ providing equipment for both the mechanical and chemical pre-treatment processes as well as for the carbamation process. This will be followed by factory deliveries, with Infinited
Fiber Company expecting to secure a commercial deal or deals during 2021.
Source: andritz.com
Klopman production facility in Indonesia achieves Oeko-Tex STeP certification
KAI (Klopman Argo International) – Klopman’s joint venture with Argo Manunggal Textile, which was conceived to serve the Asian market with dedicated production at a new Jakarta plant – has reached an important milestone. Replicating the success of the Frosinone plant, the Indonesian production site has now obtained the highest level (Level 3) of STeP certification by Oeko-Tex®; a system specifically dedicated to the textile supply chain to ensure the use of eco-friendly technologies and products, an efficient use of resources and the adoption of working conditions in line with the highest international standards.
The STeP certification, an acronym for Sustainable Textile & Leather Production, is further proof of Klopman’s ongoing commitment to sustainability that allows the company to offer its customers all over the world the same standards in terms of quality and social responsibility, communicated in a transparent and effective way.
“This is an important milestone that highlights how much sustainability is now part of Klopman’s DNA regardless of the geographical area in which the company operates,” says Amaury Sartorius, Managing Director of Klopman. “We are very satisfied with the results achieved since the beginning of our adventure in Asia with KAI, and we will continue to pursue our mission to offer customers in the Asian area the same technical and quality standards offered in Europe, with particular attention to social and environmental commitment.”
Source: klopman.com/it
Italy-Pakistan Textile Technology Center inaugurated
Italian Ambassador to Pakistan H. E. Andreas Ferrarese and the CEO, of Crescent Bahuman Limited, MR. Rizwan Shafi inaugurated the “Italy-Pakistan Textile Technology Center” (IPTTC) established at National Textile University (NTU), in Faisalabad last month.
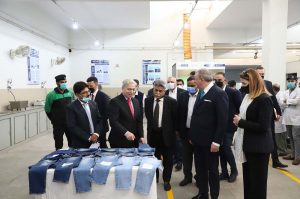
The inauguration ceremony was chaired by Professor Dr. Tanveer Hussain, Rector of NTU. Ambassador of Pakistan to Italy H. E. Jahuar Saleem, Italian Trade Commissioner to UAE, Pakistan, Oman Mr. Amedeo Scarpa and Dr. Alex Zucchi, President of ACIMIT (Association of Italian Textile Machinery Manufacturers) participated in (at) the ceremony through video link. The technology Centre would strengthen ties between the two countries and would help the denim industry to improve the quality of garments through research and innovation.
Source: ntu.edu.pk
ProAmpac acquires Rosenbloom Groupe Inc., Hymopack Ltd. and Dyne-A-Pak
ProAmpac, a provider of flexible packaging solutions, announced that it has acquired Rosenbloom Groupe Inc., Hymopack Ltd. and Dyne-A-Pak, private businesses based in Canada that manufacture packaging products. Terms of the transaction were not disclosed.
Rosenbloom Groupe, Hymopack Ltd. and Dyne-A-Pak are suppliers to North American retailers, grocery chains and quick service restaurants (QSR), as well as wholesale distribution companies, specializing in the manufacturing of paper bags, plastic bags and can liners, and foam packaging trays. With this acquisition, ProAmpac expands its manufacturing capabilities and broadens the product offering it provides to retail, grocery and QSR customers.
Greg Tucker, CEO of ProAmpac, said, “All of us at ProAmpac have deep respect for the legacy and long history of excellence of the Rosenbloom Group of companies. We are pleased to add this strong business to our platforms, which enhances our presence in Canada and allows us to broaden our product offering in the United States. With the Rosenbloom, Dyne-A-Pak and Hymopack brands as part of the ProAmpac family, we will deliver even greater value and services to our customers.”
Cincinnati-based ProAmpac is owned by Pritzker Private Capital along with management and other co-investors. With the addition of the Rosenbloom Groupe, ProAmpac has 35 sites globally, with nearly 4,600 employees supplying more than 5,000 customers in 90 countries. ProAmpac manufactures flexible packaging for various consumer, healthcare, e-commerce, retail and industrial goods markets. Rosenbloom Groupe’s brands will continue in Canada and will maintain operations at its manufacturing facilities.
Source: proampac.com