In the dynamic and global textile fiber industry with its various manufacturing processes and end-uses, news and information is breaking on a daily basis. International Fiber Journal is tracking stories relevant to our industry from manmade to natural to bio-based fibers, innovations in nonwoven, woven, braided and technical textiles, technologies for additives, bonding, coatings and polymers, and applications from apparel to hygiene to transportation, and more. Here we will post news stories relevant to textile fibers and their downstream applications on an ongoing basis. Please check back for regular updates. If you have news that you feel should be added to this summary report, please email it to Matt Migliore at mmigliore@inda.media.
Most recent update: August 31, 2020
Rieter wins patent dispute in China
Rieter protects its innovations by means of patents and registered designs. The company takes action against companies that infringe Rieter patents or designs and copy products or machines. In 2018, Rieter registered design infringements by Shenyang Hongda Textile Machinery Co., Ltd. in relation to double-head draw frames, and decided to file a lawsuit against the Chinese company.
In mid-July 2020, the Shanghai Intellectual Property Court of the People’s Republic of China determined that the double-head draw frames JWF1316 and JWF1316T of Shenyang Hongda Textile Machinery Co., Ltd. are similar to and fall within the scope of protection of the design patent concerned. The defendant Shenyang Hongda Textile Machinery Co., Ltd. was sentenced to compensate the plaintiff Rieter Ingolstadt GmbH for financial losses and expenses.
Source: rieter.com
Royal DSM’s Dyneema fiber employed for protective jerseys in 2020 Tour de France
Royal DSM announced its Dyneema fiber is driving the performance of Team Sunweb’s protective cycling jerseys in the 2020 Tour de France. Together with its partners, Team Sunweb and Craft Sportswear, DSM has helped to deliver a jersey that, when combined with a protective baselayer, offers cyclists effective abrasion protection at speeds up to 60km/h, while also reducing the severity of open wounds at even higher speeds. In this way, DSM underlines its commitment to protect people and the environment they live in.
“Being 15 times stronger than steel on a weight for weight basis, Dyneema fiber offers an excellent solution to increasing the abrasion resistance of a fabric, reducing the severity of road rash in case of a crash, without compromising the rider weight or comfort,” states Piet Rooijakkers, Head of R&D Team Sunweb “What’s more, the new jersey can form part of a modular protection solution, where riders can easily take off or put on layers according to race and weather conditions. In this way, the new jersey will support our riders significantly in the Tour de France and beyond.”
To address these needs and enable a safer riding experience, DSM has teamed up with Craft Sportswear and Team Sunweb to develop a cycling jersey that offers much-needed increases in abrasion resistance without compromising the comfort or low weight that cyclists demand. The new jersey is the latest protective cycling apparel solution, following the launch of the protective bib shorts (2015) and the protective baselayer (2019). The jersey will be worn for the first time by Team Sunweb in this year’s Tour de France. When combined with the protective baselayer, the new jersey offers complete protection against abrasions up to 60km/h, a speed below which professional cyclists spend 95% of race time in a typical stage.
Source: https://www.dsm.com/
Textile tech groups collaborated to develop antimicrobial garment
2A-NYGUARD, Coats, HeiQ, SITIP and Vagotex collaborated to create JUST5, a viroblocked jacked that provides protection for the wearer. JUST5 is treated with HeiQ’s Viroblock Swiss antimicrobial fabric technology, originally developed to treat face masks registered by Swiss Medic as a medical device. This treatment will protect each component from spoilage by contaminating microorganisms.
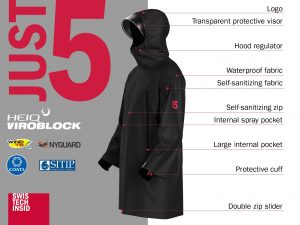
JUST5 has 2A-NYGUARD NYSHIELD zippers and ProtectV sewing thread from Coats. The zippers are self-sanitizing and restore usability 5 minutes after every touch, while the sewing thread from Coats provides anti-microbial and anti-viral properties. SITIP’s warp-knitted fabric allows for extendable cuffs on the JUST5 jacket to shield hands when touching potentially contaminated surfaces. Windtex Vagotex’s fabric creates a water-repellent and wind-resistant finish to the commercialized garment. The components are individually available for any apparel or home textile brands.
Source: heiq.com
Fitesa to acquire Tredegar Personal Care Films business
Fitesa has entered into a sale & purchase agreement to acquire Tredegar Corporation’s Personal Care Films business. The Personal Care Film business has approximately 400 employees worldwide and includes manufacturing sites located in Terre Haute, Indiana; Kerkrade, The Netherlands; Rétság, Hungary; Diadema, Brazil; and Pune,
India.
The acquisition strengthens Fitesa’s films, elastics and laminates business. “We are happy to announce this investment which reinforces our commitment to innovation and growth. We are
continuously looking for opportunities to improve the value we create for our customers, employees, communities and shareholders. Fitesa is a strategic player that focuses on
investments with a view to hold them for the long term. We believe this new acquisition, which was accomplished amidst a global crisis, is yet another demonstration of that,” said Silverio
Baranzano, Fitesa’s CEO.
Closing of the transaction, which is contingent upon the satisfaction of customary conditions, is expected to occur during the fourth quarter of 2020.
Source: fitesa.com
Dornbirn GFC Webinar Week — Sept. 17 program announced
PPE (Personal Protective Equipment) Production – a Challenge for the Industry in Europe?
Speakers & topics include:
Thomas Menitz
Chief Operating Officer & VP – Lohmann und Rauscher
“Key factors for a successful PPE business”
Stephan Trubrich
Managing Director – Hygiene Austria, VP Lenzing Group
“Lessons learned from setting up a PPE business in Europe”
Ingo Mählmann
Senior Manager Nonwovens – Oerlikon
“Leading Meltblown Technology for the production of Face-Mask Filter Media”
Henk Vanhoutte
Secretary General – European Safety Federation
“PPE in times of the COVID-19 health crisis”
Intro by EDANA & Panel Discussion
Thomas Menitz, Stephan Trubrich, Ingo Mählmann and Henk Vanhoutte
Chaired by Pierre Wiertz – General Manager, EDANA
Register at: https://www.dornbirn-gfc.com/en/programme/webinar-week-2020
Source: https://www.dornbirn-gfc.com/en/
Gerber to present virtual conference for the fashion, home furnishing and automotive industries
Gerber Technology is hosting its first virtual conference on Wednesday, November 4 and Thursday, November 5. The conference will feature announcements about AccuMark, YuniquePLM and the latest technologies in the fashion, home furnishing and automotive industries.
The conference will provide opportunities to network with industry experts, discover trends and challenges shaping the future of manufacturing and will have dedicated tracks for the fashion, furniture, transportation and PPE industries.
Source: gerbertechnology.com
INDA’s Hygienix event goes virtual with a focus on the pandemic’s impact on absorbent hygiene and personal care markets
INDA announced the sixth edition of the annual Hygienix event will be held in a new virtual format Nov. 17-19. Its focus will be the impact of the global health pandemic on the absorbent hygiene and personal care markets.
Originally scheduled as an in-person conference in New Orleans, the fully virtual format offers the opportunity to participate from any location while providing vital program content on market and technical developments, scheduled networking, virtual exhibits and product innovation awards.
The virtual Hygienix event schedule includes:
- Virtual Hygienix Conference Presentations – Nov. 17-19
- 2020 Hygienix Innovation Award Virtual Presentations – Nov. 18
- Virtual Hygienix Tabletop Displays – Nov. 17-18
- Virtual 2020 Hygienix Innovation Award Announcement – Nov. 19
Industry experts will present supply-side and demand-side developments in both the North American nonwovens markets and the absorbent hygiene markets, market intelligence, economic insights, challenges and disruptions brought on by the coronavirus. Featured presentations include Global Market for Absorbent Hygiene: Disruption, Innovation, Path to Future Growth with Svetlana Uduslivaia from Euromonitor International; U.S. Economic Outlook presented by Lindsey Piegza from Stifel Financial Corporation; Challenges for 2021 and Beyond: Post-Covid-19 Supply Chain Resiliency and Sustainability for Absorbent Hygiene Products with Colin Hanna from Price Hanna Consultants LLC; and many more.
Registration is now open for Hygienix. Registrants will receive a personal URL to access the event and all speaker presentations will be recorded and available near real-time and on-demand for 12 months.
Registration: hygienix.com
Source: inda.org
VDMA continues technology webtalks on energy efficiency in textile dyeing and finishing
Energy efficiency will be the topic of VDMA’s next edition of Textile Machinery Webtalks on August 27, from 2pm-4pm CEST.
Efficient energy management is of increasing importance in textile dyeing and finishing. Innovative machine designs with minimal water and energy consumption as well as the recovery and use of the heat energy produced in the processes represent valuable potential savings for any modern company.
The presenters include Ludger Sommer of Thies, speaking on how to manage heat energy in wet processing, and Benjamin Schnabel from Brückner Textilmaschinen, who will demonstrate how to make one of the most energy consuming processes in textile manufacturing more sustainable, eco-friendly and cost effective. Fabian Buckenmayer from PLEVA Sensors and Controls will speak on the specific opportunities for an energy-efficient textile production via measuring and controlling process parameters.
The experts will be available after the presentation to answer participant questions.
Registration link: register.gotowebinar.com
Source: vdma.org
Retech expands facilities for logistics, development and testing of heat treatment systems for synthetic fibers
Retech, a provider of technology and components for the heat treatment of synthetic fibers, opened a logistics and testing center at its headquarters in Meisterschwanden, Switzerland.
Construction work on the new logistics center, at Retech’s headquarters in Meisterschwanden, started at the end of February, shortly before the coronavirus pandemic outbreak. The building was officially opened in mid-July, allowing optimization of production workflows, assembly and quality assurance.
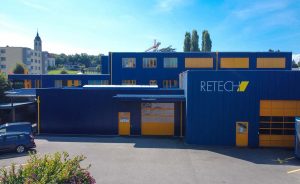
The expansion also included complete renewal of the technical center and test laboratory, extending the capability for long-term trials of new developments in area of heated godets, high-temperature applications, temperature regulation and temperature transmission systems. This is a key aspect of Retech’s innovation policy, which has already seen various successful trials and tests on these systems in recent months.
Further investments for the product group have already been made in the winding department for the manufacture of induction heaters. Newest-available technologies are also now in place to ensure optimized and safe production in high-temperature applications.
The combination of significant investment and comprehensive optimization of facilities is evidence of Retech’s commitment to long-term growth and ongoing global eminence in synthetic fiber technologies, according to the company.
Source: http://www.retech-godet-rolls.ch/
Kettelhack replaces sanforizing line with new Monfortex Qualitex 800 system
Kettelhack GmbH – a German leader in the dyeing and finishing of monochrome fabrics for high-quality and durable workwear and bed linen – has retired its existing Monforts sanforizing line after 35 years of daily service, replacing it with a new one.
Kettlehack’s new two-meters-wide Monfortex line benefits from the latest Qualitex 800 control system, which allows all parameters to be easily automated via the 24-inch color touchscreen, including production speed, control of all fabric feed devices, rotation spray or steaming cylinder options, the width of the stretching field and the rubber belt pressure. The integrated Compactomat system allows a continuous indication and control of the shrinkage values and the temperatures of the shrinking cylinder and felt calender. Up to 10,000 separate process parameter records can be generated and stored by the data manager.
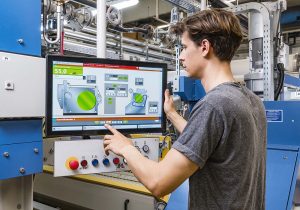
Full line management can be optimized via the batch-specific calculation of all process material consumption and water and electricity use, with any standstill times analysed and immediately corrected for the future.
Commissioning of the new Monfortex line at Kettelhack commenced in January and it was fully operational in a relatively short time.
Key features of the Monfortex line are the proven fabric preparation, weft straightening and spreading units, prior to the compressive shrinkage machine with a 750mm shrinking cylinder, and a felt calender equipped with 2,000mm diameter drying cylinder. The line also features an integrated automatic grinding unit.
Kettelhack is processing primarily cotton and polyester woven fabrics, with lyocell becoming increasingly popular in workwear for its softness and comfort.
As part of its customer service, the company stocks more than a million metres of grey fabric and at least 1.2 million metres of finished and rolled standard fabric in its warehouse at any one time, with a further 750,000 metres permanently in production.
Source: https://www.monforts.de/ & https://kettelhack.de/
Color & specialty chemicals provider Archroma earns EcoVadis ‘Gold’ rating for sustainability
Archroma, a leader in color and specialty chemicals towards sustainable solutions, has been awarded the EcoVadis “Gold” rating in corporate social responsibility (CSR) 2020, placing the company within the top 5% of the best-rated companies in its industry.
Archroma was evaluated by EcoVadis, an organization specialized in assessing the CSR performance of companies on a global basis. The assessment focuses on 21 criteria which are grouped into 4 themes: Environment, Labor & Human Rights, Ethics, and Sustainable Procurement.
“For Archroma, sustainability is a process of bringing continued improvement to our societal, environmental and economic performance, and that of our customers” comments Heike van de Kerkhof, CEO at Archroma. “We are extremely proud of this first Gold rating by EcoVadis, which is a strong encouragement that we are heading to the right direction in the way we run our own operations, because it’s our nature!”
Source: https://www.archroma.com/
Michelman appoints Technology Director and Marketing Manager for fiber business
James Chantler, Ph.D., joins Michelman as its new Global Technology Director for Fibers & Composites. Dr. Chantler, a glass fiber industry veteran, has held several positions, including Business Manager, Global Research Manager, and Material Development Engineer for PPG Industries, Reichhold, and GAF. He was the Research & Development Director for Nippon Electric Glass (NEG-US), where he led the strategy for new product development, intellectual property, and global product transfer & integration. His industry knowledge and technical expertise will allow Michelman to broaden its fiber sizing and surface technology portfolio and help the composite industry achieve increased performance, and accelerate the adoption of new and novel concepts.
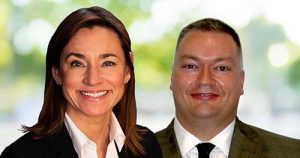
Ms. Lauren Hickey joins Michelman as its Global Marketing Manager for Fibers & Composites. She has spent over 20 years in senior marketing positions such as Business Manager, Senior Global Marketing Manager, and Global Director of Marketing & Product Management for companies such as Invacare Corporation, PolyOne, and Americhem Inc. She will use her plastics and polymer material product portfolio management experience to direct efforts with reinforced plastic composites.
Source: https://www.michelman.com/
Spinnova bolsters its team with leadership, R&D & lab appointments
In preparing to scale its sustainable fiber production, Spinnova recently added two niche textile experts to help commercialize its sustainable wood-based fiber. It also appointed four additional team members.
Shahriare Mahmood was named Spinnova’s Sustainability Director. Mahmood joined Spinnova from the renown Finnish children’s wear brand Reima. Mahmood has both an academic and a technical textile industry background. He earned his chemical engineering degree in Bangladesh, a master’s degree in engineering in Finland, and a Ph.D. in sustainability management. He has worked in textile mills in Asia and Europe.
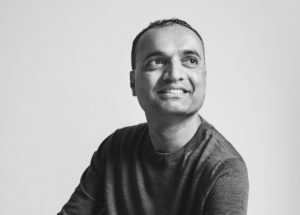
Sustainability Director
Spinnova
With Spinnova, Mahmood will focus on supporting sustainability efforts of partnering brands and related pre-commercial and commercial-phase supply chains.
Spinnova’s other textile expert appointment is Eun (Enja) Young Kim, who started as Senior Fibre Application Specialist in Spinnova’s R&D team. Engineer by background, Kim previously worked for fiber technology company Lenzing in Austria, where she worked in technical customer service of technical applications. She will be focusing on developing the Spinnova fiber’s quality and finishings.

Senior Fibre Application Specialist
Spinnova
Other appointments were focused on Spinnova’s R&D and laboratory teams: Matias Nissinen as Development Engineer, Tomi Nieminen and Toni Hiltunen as Process Technicians, and Riikka Happonen as Laboratory Technician.
Source: https://spinnova.com/
Organic Cotton sees second largest harvest on record
Textile Exchange’s 2020 Organic Cotton Market Report reveals data collected for the 2018/19 harvest year. The report shows an increase of 31 percent in organic cotton production over the previous year, making it the second-largest harvest on record after 2009/10. In addition to data per region, the report is sprinkled with insights from industry professionals about their current projects, challenges, successes, goals, and visions for the organic cotton sector, with a particular focus this year on impacts of, and responses to, the dual threat of COVID-19 and climate change.
In summary, the results show that 222,134 farmers grew 239,787 metric tons of organic cotton in 19 countries on 418,935 hectares. In addition, 55,833 hectares of cotton-growing land was in-conversion to organic, helping to meet the increasing demand.
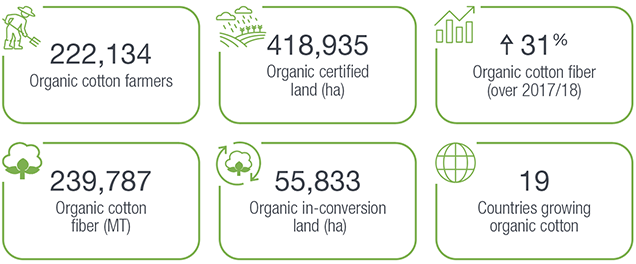
Download the full report at: https://store.textileexchange.org/product/2020-organic-cotton-market-report/
Source: https://textileexchange.org/
Researchers develop self-healing, reprogrammable polymer
Nature’s blueprint for the human limb is a carefully layered structure with stiff bone wrapped in layers of different soft tissue, like muscle and skin, all bound to each other perfectly. Achieving this kind of sophistication using synthetic materials to build biologically inspired robotic parts or multicomponent, complex machines has been an engineering challenge.
By tweaking the chemistry of a single polymer, researchers at Texas A&M University and the U.S. Army Combat Capabilities Development Command Army Research Laboratory have created a whole family of synthetic materials that range in texture from ultra-soft to extremely rigid. The researchers said their materials are 3D printable, self-healing, recyclable and they naturally adhere to each other in air or underwater.
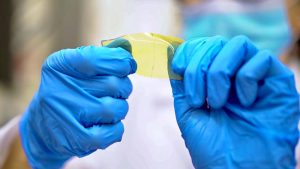
“We have made an exciting group of materials whose properties can be fine-tuned to get either the softness of rubber or the strength of load-bearing plastics,” said Dr. Svetlana Sukhishvili, professor in the Department of Materials Science and Engineering and a corresponding author on the study. “Their other desirable characteristics, like 3D printability and the ability to self-heal within seconds, make them suited for not just more realistic prosthetics and soft robotics, but also ideal for broad military applications such as agile platforms for air vehicles and futuristic self-healing aircraft wings.”
Read the full story: https://engineering.tamu.edu/news/2020/08/versatile-new-material-family-could-build-realistic-prosthetics-futuristic-army-platforms.html
This research is also featured in the May issue of the journal Advanced Functional Materials.
Source: https://engineering.tamu.edu/
USTER reveals quality data on a range of fiber and yarn performance characteristics
Uster Technologies offers spinners valuable new insights into yarn quality optimization, thanks to its unique combination of expert monitoring of market trends and comprehensive statistical analysis. For example, there is evidence that fiber elongation depends more on the type of cotton than on fiber length. And not all neps are the same: there are significant gains to be made from differentiating between seed coat and fiber neps.
Both of these facts offer spinners potential for competitive advantages, arising from new data categories in USTER STATISTICS 2018. This global benchmarking tool now includes revealing information about fiber elongation, as well as seed coat and fiber neps, and Uster explains how these can be exploited to improve yarn quality consistency.
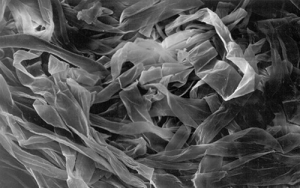
In conjunction with fiber tenacity, fiber elongation influences yarn elongation and the processing behavior of the yarn, since higher values will typically perform better in the weaving mill. For this reason, it was obviously beneficial to include fiber elongation in the latest USTER STATISTICS.
Analysis of Uster databases show that the correlation between fiber elongation and yarn elongation of a combed cotton ring yarn is at a level of 85%. Although the twist multiplier and yarn production speed have a huge impact on yarn elongation, the basis for high yarn elongation actually comes from the fiber. The elongation of cotton fiber conclusively depends more on the type of cotton than the fiber length.
When engineering laydowns for yarn production, experts know which yarn parameters are influenced by certain fiber properties. It is possible to offset small deficiencies in one fiber property with an improvement in another. If a low fiber length might negatively affect yarn elongation and twist level, a slightly higher elongation in fiber could help.
Established in 1957, USTER STATISTICS are a vital source of quality data for the textile industry and are now newly available as an app. The combination of textile knowhow, current statistical data and advanced technology is the basis for consistent yarn quality, despite changing conditions and new trends. “We could consider the laydown mixes used in yarn spinning as a ‘recipe’ and fiber quality parameters as the ‘ingredients.'” said David McAlister, product manager for Uster Technologies’ Fiber Lab. “We would then aim to adjust the ingredients to keep consistency in the recipe. With USTER STATISTICS 2018, we can determine the relationship of fiber properties to yarn properties and from that we can learn how to adjust the ingredients of the recipe for optimal performance. This is important for cotton, as it is not always possible to obtain the same or similar fiber qualities year-in and year-out.”
Source: uster.com
Glatfelter reports Q2 earnings, Composite Fibers & Airlaid Materials see decreases
On an adjusted basis, earnings from continuing operations for the three months ended June 30, 2020 and 2019, were $9.9 million, or $0.22 per share, compared with $8.5 million, or $0.19 per share, respectively. Adjusted earnings is a non-GAAP financial measure for which a reconciliation to the nearest GAAP-based measure is provided within this release. Consolidated net sales totaled $216.2 million and $235.1 million for the three months ended June 30, 2020 and 2019, respectively. On a constant currency basis, Composite Fibers’ and Airlaid Materials’ net sales decreased by 6.3% and 7.2%, respectively.
“Glatfelter’s solid second quarter results, in the midst of a global pandemic, demonstrate the resiliency of our new business model and continued demand for our portfolio of engineered materials that are essential for producing a variety of consumer staples,” said Dante C. Parrini, Chairman and Chief Executive Officer. “Composite Fibers outperformed expectations for the quarter, due in part to strong shipments in the food and beverage category and better than expected demand for wallcover products. Profitability for this segment relative to guidance was also better than expected, driven by lower downtime and continued cost control.”
In Airlaid Materials, Glatfelter saw exceptional growth in home care and health and hygiene products, although overall shipments for the segment were hampered by the pandemic’s impact on tabletop demand as restaurants around the globe were either closed or operating at dramatically reduced capacity. Despite this headwind on volumes, Airlaid Materials achieved record quarterly EBITDA with margin of 19%.
Composite Fibers’ net sales decreased $10.4 million or 7.9%, compared to the year-ago quarter driven by lower shipments of wallcover products, which were down 49%, as well as unfavorable foreign currency translation of $2.0 million.
Composite Fibers’ operating income of $11.5 million was $1.5 million lower, or approximately 12% unfavorable, compared to the second quarter of 2019. Lower shipping volumes impacted results by $2.1 million driven predominantly by lower wallcover demand.
Airlaid Materials’ net sales decreased $8.4 million in the year-over-year comparison. Shipments were lower by 2.2% due to weak demand for tabletop products as restaurants globally were closed or operated at dramatically limited capacity. This shortfall in demand was mostly offset by strong orders for home care and health and hygiene products. Selling prices were $4.6 million lower due to contractual cost pass-through arrangements, while currency translation was unfavorable by $1.1 million.
Airlaid Materials’ second quarter 2020 operating income of $12.3 million was $1.9 million favorable, or approximately 19% higher, when compared to the second quarter of 2019. Improved sales mix favorably impacted results by $0.6 million, while price declines due to contractual raw material pass-through provisions were more than offset by lower raw material and energy prices, adding net $0.5 million of profit. Efficient operations complemented by disciplined cost control favorably impacted results by $0.9 million, driven by higher demand for essential product categories and improved performance in both North American facilities compared to the year-ago quarter.
Source: glatfelter.com
DuPont Sorona launches Common Thread Certification Program to provide fiber traceability
The DuPont Sorona brand team is launching a new brand architecture and hangtag program designed to bring simplicity of choice and fabric confidence to designers and apparel brands. New fabric collections offered by mills are tested and certified through the DuPont Sorona Fabric Common Thread Certification Program to assure the fabrics have the unique molecular footprint of partially plant-based Sorona polymer, as well as meet key fabric performance attributes. Apparel brands and designers will be able to request that mills provide their DuPont Sorona Fabric Common Thread Certificate to show their Sorona fabrics truly have the unique fabric performance and feeling that Sorona fibers provide.
“Fiber producers are able to create many unique constructions from Sorona polymer enabling a wide variety of textiles exhibiting diverse performance properties from wrinkle-resistant outerwear fabrics to lightweight breathable insulation products, permanent stretch and recovery, and newly launched Sorona faux fur,” said Renee Henze, DuPont biomaterials global marketing director “We are committed to ensuring that mills, designers and brands have clarity on our offering and that they can trust the source of the materials when they’re choosing fabrics using Sorona.”
Source: sorona.com
Sateri achieves EU-BAT sustainability compliance at two additional mills in China
Two more Sateri mills in China, Sateri Jiujiang and Sateri Jiangxi, have received verification of compliance to the emissions limits set out in the European Union Best Available Techniques Reference Document (EU-BAT BREF) on Polymers. This brings the total number of EU-BAT compliant mills to three of five, accounting for over 60 per cent of Sateri’s overall fiber production capacity. In April this year, Sateri Fujian was the company’s first mill to be verified as being EU-BAT compliant.
Verified by independent consultant Sustainable Textile Solutions (STS), a division of BluWin Limited (UK), the parameters of the EU-BAT BREF assessed included resource utility efficiency, wastewater discharge and air emission. As a highlight, STS’ assessment concluded that the energy intensity and air emission of Sateri Jiujiang and Sateri Jiangxi were well under EU-BAT norms for viscose production. Considering the EU-BAT energy requirements limit of 30GJ/MTf, the mills were each saving about 1,100 kg CO2/MT of fiber production. The mills also followed local requirements for controlling ecological impact for viscose production, and there were no gaps identified against EU-BAT.
Sateri Jiangxi is a 16-year-old mill and the company’s first and oldest, while Sateri Jiujiang was acquired and expanded in 2015. Said Allen Zhang, President of Sateri, “For three of our five mills to meet the EU-BAT emissions limits in such a short span of time is a testament to our continued investment in best-in-class technologies. This applies to all our mills – regardless of whether they are existing, acquired, or newly constructed ones – as we aim to achieve a high level of sustainability performance across all our operations.”
The company is well on track for its remaining two mills, Sateri Jiangsu and Sateri China which were acquired and newly-built in 2019 respectively, to comply with EU-BAT’s recommended emission levels by 2023.
Source: sateri.com
Reference: Sateri EU-BAT Assessment Reports
Geosynthetics Materials Association announces 2021-2023 Koerner Awardee and Lecturer
The Geosynthetics Materials Association announced the 2021–2023 Koerner Awardee and Lecturer, Jie Han, Ph.D., PE, F.ASCE. Dr. Han is the Glenn L. Parker Professor of Geotechnical Engineering at The University of Kansas in Lawrence, Kansas, and has been an active member of the geosynthetics community for many years.
He becomes the third recipient of the award named in honor of Robert M. Koerner, Ph.D. “I am very honored to be selected for the 2021–2023 Koerner Awardee and Lecturer. I am humbled to accept this award. Prof. Bob Koerner is one of my most respected educators, researchers and engineers in our field. He has been my role model to follow for many years,” Dr. Han said in his acceptance.
Dr. Han will follow the 2017 inaugural winner, Dr. Koerner, and the second awardee Barry Christopher, Ph.D., in 2019. As the award winner, Dr. Han will present the keynote lecture at Geosynthetics Conference 2021, taking place Feb. 21–24, 2021 in Kansas City, Missouri, and will repeat the lecture at three additional geosynthetic conferences during 2021–2023.
Source: geosynthetics.ifai.com
W+D names Marc Wolpers VP of Sales, Hygiene
Marc Wolpers is taking over the position of Vice President Sales Hygiene at Winkler+Dünnebier GmbH (W+D).
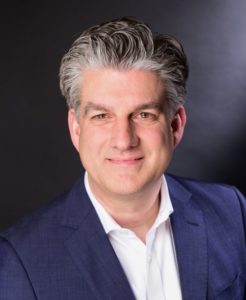
In his new role, Wolpers will manage the entire sales department of the W+D Hygiene Solutions division and thus manage both the W+D sales team and sales for BICMA Hygiene Technology in Mayen. Before that, he was Sales Director at Trützschler Nonwovens and has extensive professional knowledge of the hygiene industry.
Ulrich Wald, Wolpers predecessor in this position, will remain active for the company and will concentrate on dealing with key accounts directly.
Source: w-d.de
Mahlo celebrates its 75th anniversary
Dr. Heinz Mahlo founded a company based on measurement and control systems for the textile industry in 1945 after the end of World War II. His work resulted in the patent for the first automatic weft straightener and established Mahlo’s position as the world market leader in the industry.

01/29/1912 – 05/10/1979
Photo: Mahlo
Today, as Mahlo celebrates its 75th anniversary, the company’s thread straighteners and systems for process control for textile finishing can be found in all important markets. Countless products from many large and well-known brands have gone through a “Mahlo” during their manufacture.
In the mid-1990s, Mahlo engineers developed the Qualiscan QMS quality control system. The system enables the nonwovens, plastics and paper industries to measure and control critical process parameters such as moisture, surface weight or layer thickness.
A forward-looking decision. These markets are becoming more and more important. How strongly has it been shown in this special year, in which the nonwovens industry is growing, while the textile industry is being shaken by the crisis. It is all the more important for a company not to stand on just one pillar.
“Our 75th anniversary marks an important milestone in the company’s history,” said Rainer Mestermann, managing director of Mahlo GmbH + Co. KG. “We see this as confirmation of the continuous development of the company and at the same time as an incentive to further increase the competitiveness of our customers with technologically leading products and tailor-made services.”
Source: mahlo.com
ANEX-SINCE 2021 dates announced
Asia Nonwovens Exhibition and Conference (ANEX) and Shanghai International Nonwovens Exhibition (SINCE) will be co-located 22nd-24th Jul, 2021 at the Shanghai World Expo Exhibition and Convention Centre (SWEECC), Shanghai, China.
ANEX-SINCE will cover nonwovens raw materials, nonwovens production machinery & accessories, nonwovens roll goods, testing and inspection machinery and converted goods. Industries served include hygiene, filtration, fabrics & apparels, medical, automotive, wiping, home furnishings & upholstery, etc.
ANEX-SINCE 2021 is expected to attract more than 600 exhibitors and 30,000 professional visitors, with 35,000 square-meters display area.
Source: en.since-expo.com
Chargeurs names Christy Raedeke Chief Marketing Officer
Chargeurs*PCC Fashion Technologies has appointed Christy Raedeke as the company’s first Chief Marketing Officer, effective August 10. An expert in bringing advancements in apparel technology to market, Raedeke will lead all marketing efforts in support of Chargeurs’ global growth strategy, reporting directly to Angela Chan, Global President of Chargeurs*PCC Fashion Technologies.
“We’re extremely pleased to have Christy join us to lead marketing efforts in support of Chargeurs’ global growth, including the growth of our new US-based Lainiere Health & Wellness division,” said Angela Chan. “We’re confident that her leadership experience, industry expertise and marketing vision will enable us to effectively execute our expansion and innovation strategies at this critical time.”
Raedeke joins the company with more than 30 years of experience in marketing, PR and business development across the high-tech, biotech and textile technology sectors.
Source: chargeurs.com
United Sewing Automation opens automated manufacturing facility to bolster US facemask supply
United Sewing Automation, Inc. (USA) announced the official opening of its new automated manufacturing facility in Mount Airy, NC to produce disposable PPE facemasks. Prompted by the PPE supply shortages experienced in the U.S. during the coronavirus pandemic, USA took the initiative to invest in automated equipment to manufacture American-made medical grade masks.
USA’s facemasks feature a three-ply design with a built-in adjustable nose bridge and ear loop straps made of nylon and elastic cord to provide a better fit than traditional disposable masks. USA’s medical grade facemasks are tested for protection against bacterial and other airborne particulates, liquid barrier protection, breathability, and are rated as Class 1 for flammability. USA’s FDA-registered manufacturing facility is located in Mt. Airy, North Carolina.
“Due to the significant shortage of personal protective equipment caused by the COVID-19 pandemic, we decided to do our part to help fill this void by manufacturing medical grade facemasks at our facility in Mount Airy,” said Ben Webb, USA’s CEO. “We’ve installed new high-tech automated production equipment that now produces large amounts of facemasks quickly and efficiently.”
USA’s ownership team has many years of experience in the textile and apparel industry and had the vision in 2017 to bring apparel manufacturing back to Mount Airy, NC through automation. USA recently installed high-tech ultrasonic welding machines and automated production equipment capable of producing more than one million facemasks per week.
Source: madeinusafacemask.org
STOLL breaks ground on new customer center in Germany
STOLL, a new business unit of the KARL MAYER Group with expertise in the area of flat knitting and technical textiles, is in the process of moving from Stollweg in Reutlingen, Germany, to the Reutlingen-Betzingen industrial estate, where it will continue its activities under the new owner, as planned. During two project stages, a development center is first being built, and later a customer center will follow.
Official start of the construction for the development center began in July 2019. The building, with bright and modern offices and meeting rooms for roughly 70 employees, is expected to be completed by autumn 2020.
July 2020 saw the opening of the second project stage, with the aim to erect the customer center by autumn 2021. A symbolic groundbreaking ceremony was attended by Daniel Hebisch, Shareholder and Member of the Executive Board of isin+co GmbH & Co. KG, and Cemal Isin, Managing Partner of isin+co GmbH & Co. KG, Uli Kälber, Managing Director of Rommel SF-Bau GmbH & Co. KG, as well as the following gentlemen from KARL MAYER Textilmaschinenfabrik GmbH: Andreas Schellhammer, President of the STOLL Business Unit, Erhard Vöhringer, Senior Sales/Service Manager, Jörg Wilhelm, Senior Operations Manager, and Frank Wittel, Vice Chairman of the Works Council.
The project is carried out by Rommel SF-Bau GmbH & Co. KG as general contractor. The architects come from ISIN + Co. GmbH & Co. KG. They designed a functional building complex, which will be housing the reception, offices for a workforce of about 100 persons and conference rooms. An associated industrial building will provide enough space for showrooms, machine floor areas, project rooms and for the company’s own training center. The usable floor space covers approx. 5,350 m².
Source: stoll.com
Marina Crnoja-Cosic named head of new business development at Kelheim Fibres
Marina Crnoja-Cosic, Ph.D., has been appointed head of new business development for Kelheim Fibres. She will also serve as a member of Kelheim’s management board. A chemist with a doctorate degree, Dr. Crnoja-Cosic brings with her significant experience in fiber and application development, as well as in business development.
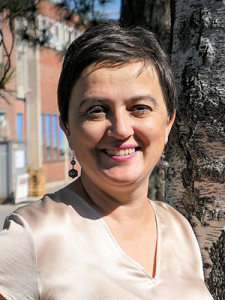
“Dr. Crnoja-Cosic is highly competent. She has an enormous wealth of experience, as well as a comprehensive network. At the same time, she has repeatedly proven that she is not afraid to tread new paths – a perfect match with our philosophy! Together with Dr. Crnoja-Cosic we will intensify our focus on innovation even more. We are very pleased to have her on board!”, said Craig Barker, CEO at Kelheim Fibres.
Source: kelheim-fibres.com
Garrett Forde appointed CEO of SPGPrints
The Supervisory Board of SPGPrints has appointed Garrett Forde as a member of its Management Board and the CEO of the SPGPrints Group, effective on October 1st, 2020.
Dick Joustra is going to retire this year. Joustra started his career at SPGPrints (then Stork) in 1983, becoming a managing director in 1999 and was appointed CEO of the SPGPrints Group in 2003. Joustra will transfer his responsibilities to Forde and has agreed to assume a senior advisory role to the SPGPrints Group and to remain as a member of the Supervisory Board after this transition.
Forde joins SPGPrints from his most recent position as CEO of Hitec Power Protection B.V. in The Netherlands, a provider of continuous power solutions. Prior to his position at Hitec Power Protection, Forde had a distinguished career in the technology manufacturing industry in the U.S. and Europe, where he held various positions with Philips, Intelligent Energy and Panalytical.
Source: spgprints.com