Predictive Fulfilment is the Goal as AI Moves In
For a number of decades now, the supply chains of many high-tech industries have been highly structured and strictly managed top-down by the OEMs (original equipment manufacturers) they ultimately serve, to ensure both maximized efficiency and just-in-time sequencing.
The automotive industry is a good example of this, explains Jason Kent, CEO of the British Textile Machinery Association (BTMA).
“Control from the top over a fully visible supply chain extends not just to suppliers of individual components such as, for example, carpets, but even to the suppliers of the machinery on which these carpets are made,” he explains. “As a result, companies making machines on which automotive carpets are to be produced must not only be ISO 9001 certified, but also meet many other stipulations in areas such as power consumption and wastage.”
Restructuring
Such a top-down structure could now be very rapidly established across the highly complex and fragmented textiles and fashion apparel supply chain Kent believes, in response to a raft of new legislative measures that are poised to be introduced, initially in both the European Union and parts of the USA.
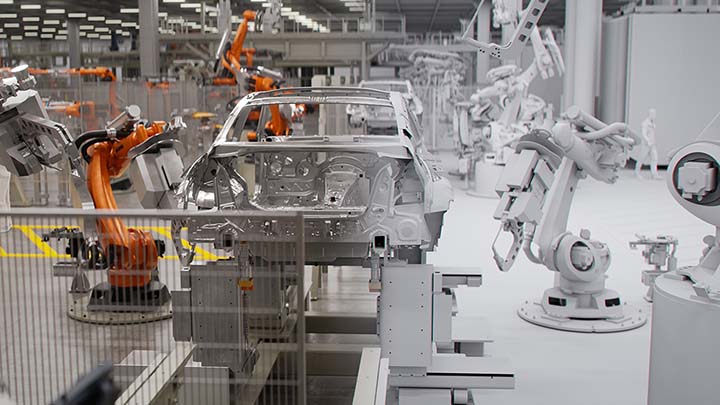
This major restructuring will be enabled by ever-improving AI tools providing greater transparency, digitization and automation.
“Having committed to ambitious sustainability goals by 2030, the majority of major apparel brands, as well as the corporations extensively using nonwovens and technical textiles in their products, are taking a much greater interest than ever before in their supply chains,” Kent emphasizes. “They are now examining each link in the complex succession of processes that result in their final products, in order to more fully understand how they are being made and exactly what they are made from. This new level of cooperation and transparency – stretching right back to the chemical and fiber producers – is to be welcomed and can only lead to more sustainable practices across many areas, and not least in designing for circularity in the first place.”
The term ‘predictive fulfilment,’ he adds, encapsulates everything AI – from generative design tools for enhancing creativity and streamlining initial process steps to quality and wastage control in manufacturing, assisted by predictive maintenance and machine learning.
Complex Patterns
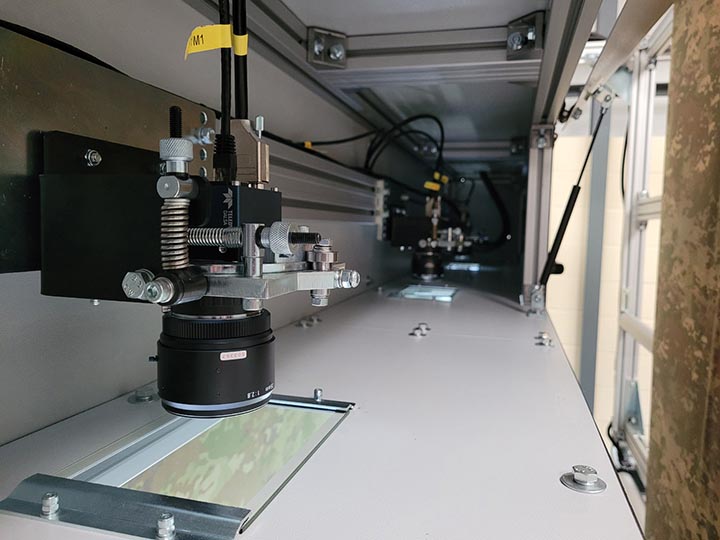
In respect of the latter, one BTMA member company which has seen its business soar in 2023, is Shelton Vision.
Having successfully demonstrated its WebSpector automated fabric inspection system detecting faults on camouflage fabrics at speeds of up to 100 meters a minute during the ITMA 2023 in Milan last June, Shelton Vision has secured an unprecedented number of new orders in many fields of the textile industry.
Building on its established vision system for plain, single-color textiles, Shelton’s patent-pending image processing techniques recognize and adapt to complex patterns – even those on fabric with significant distortion and deformation. Fabrics are not rigid and can be sheared or stretched while also being subject to local distortion, but the WebSpector system successfully deals with such anomalies in real time to provide a reliable inspection process at the same levels of plain fabric. Advanced software techniques ensure a totally clean image, allowing the full detection of faults on fabrics running at high speeds.
Eliminating False Positives
“Using machine learning, our vision system automatically trains new styles, and our AI platform is continuously updating to achieve high accuracy of real time defect naming and grading,” explains Shelton MD Mark Shelton. “This eliminates false positives and provides consistently accurate data for both roll cutting optimization and yield increase, as well as for optimizing fabric utilization in panel cutting processes.”
The automotive interiors and one-piece woven airbag sectors remain the major destinations for this advanced technology, but further finished fabric WebSpector systems are now being supplied to manufacturers of performance wear and high-end fashion, denim, outdoor upholstery, sunscreen, mattress ticking, window dressings and even carbon fiber composites. In addition to finished fabric inspection, there is also a growing demand for fabric forming/grey cloth inspection to streamline mending of both plain and patterned fabric.
“We are being greatly assisted by the increased quality expectations across value chains and the realization by brands and larger corporations of what our technology can do – and on a more fundamental level, that a reliable fabric inspection system technology actually exists, after disappointments with previous technologies,” Shelton says. “These brands and corporations are now actively promoting the adoption of our system to their fabric suppliers.”
CEMATEX
The BTMA is one of nine national associations who comprise CEMATEX – the blanket organization behind the hugely successful ITMA exhibitions – and all are agreed on the driving force of AI. They include Belgium’s Symatex and Sweden’s TMAS, who both underline the importance of good data.
“Digitalization is both driving the development of new technologies and also leading to an environment of continuous improvement for machine builders,” says Stijn Pauwels, manager of Symatex. “A key strength of companies such as Picanol is in having both R&D and manufacturing at the same locations, because as machines become increasingly customized in mills around the world, it becomes harder to build them in series without access to all production data.”
At the site of the customer, digitally enabled smart factory production machines can talk to each other and make a lot of new features possible, including real-time monitoring, correcting based on historic data and instantaneously adapting in real time. With the latest Belgian weaving machines operating at the highest speeds attainable to date, real time is very much a necessity. More than anything, digitalization is about increasing the optimal flow of the entire plant, and increasingly, networks of plants operating in sync around the world.
Intuition
Weaving, however, is never just a matter of numbers, parameters and settings, but also relies on the intuition, experience and the gut feeling of the expert weaver, who is able to feel when something isn’t right or a machine is off sync, and sense when settings need to be fine-tuned.
It is this very intuition, however, that Picanol has now digitalized with its latest PicConnect platform, which provides a wide range of features, from industrial IoT to service-related applications, as well as brand-new functionalities, such as applications for energy and production monitoring, digitalized gripper stroke setting and gripper tape monitoring, climate control and shed angle measurement.
PicConnect enables the creation of a library of machine settings which when machines are connected can easily be sent to and from the platform. Ensuring machines all use the optimal settings is extremely convenient and the settings can be easily visualized for an intuitive overview, and then edited, to further fine-tune performance.
An additional feature is the ability to compare the settings of two different machines or compare the actual settings of a machine with a reference file. This highlights the differences between the two machines, and settings can be copied from one file to another. After settings have been changed or copied, all machines in a weaving mill can then be optimized with just a couple of clicks.
Materials Handling
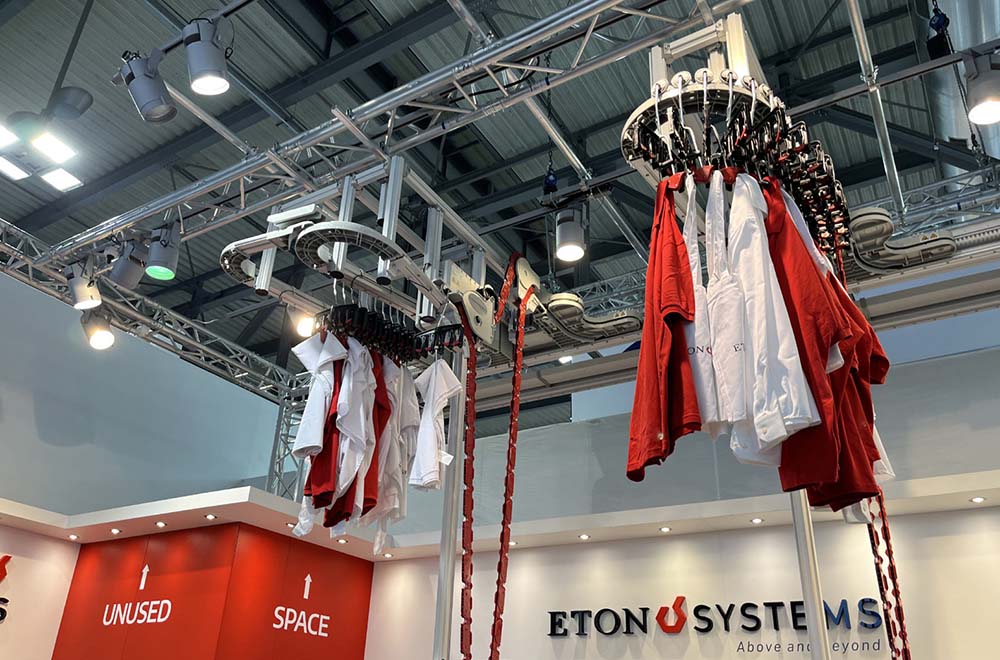
Fully integrated technologies with up-to-the-minute automated features for the end-to-end production of fully-finished garments and home textiles have also been developed by members of TMAS, such as the automated material handling installations of Eton Systems and ACG Kinna’s robotic pillow filling system.
Eton provides modular, individually addressable carriers designed to eliminate manual transportation and minimize handling within product assembly and finishing plants.
The ETONingenious software platform gathers, processes and presents powerful, value-adding product information to operators, supervisors, quality control personnel and management. The system has a web-based user interface and runs on any browser – laptops, PCs, tablets and even mobile phones – without any client installation requirements. It is also easy to integrate with any existing ERP system and is industry 4.0 compatible. Dashboards provide a clear and easy overview of production.
Robotics
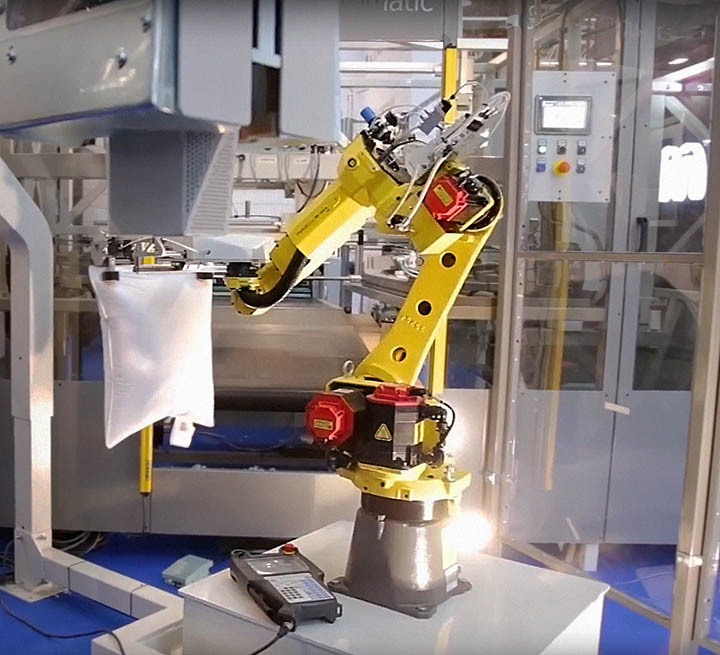
With the ability to fill and finish some 3,840 pillows per eight-hour shift, ACG Kinna’s automated units meanwhile cover the entire process – from the opening and weighing of the fiber to the filling of the product and on to the sewing and packing processes.
The technology is based on two robotic arms which have been specially modified by ACG Kinna with advanced gripping tools and seaming and labelling devices. The system further includes an integrated marking solution which allows QR codes, batch numbers and dates to be individually printed on the labels of each garment, as well as unique software for automatically detecting faults in production.
“The use of robotics is now standard across many industries dealing in solid goods, but the handling of soft materials such as textiles is a little more complex,” says ACG Kinna CEO Christian Moore. “Nevertheless, our robotic system is now fully operational in a number of plants around the world.”
Data Coordination
“AI and advanced automation really have the potential to revolutionize the textile industry, improving production efficiency, quality control and design processes,” adds TMAS secretary general Therese Premler-Andersson. “AI-powered systems can, for example, help detect defects in fabrics and garments during manufacturing processes and by using computer vision in the machinery, different defects such as stains, holes and uneven stitching can be rapidly identified and corrected at an early stage.
“Predictive maintenance is another benefit. AI is being used to monitor machines and predict when they are likely to need maintenance. This can help prevent breakdowns and reduce downtime, improving overall efficiency. AI is also proving valuable in R&D for TMAS companies, enabling data from different sources to be coordinated in order to optimize product design and reduce time and costs via the sensor-controlled optimization of a host of different parameters.”