Automation is pervasive in November’s mammoth textile machinery show in Milan
The 17th ITMA textile machinery show, which took place in Milan, Italy, from November 12-18, broke all previous records, attracting almost 123,000 visitors from 147 countries and with 1,691 exhibitors from 46 countries participating.
“We registered a 20 per cent jump in visitor numbers compared to the last event in 2011 and more importantly, from feedback, we can confidently say that our message on sustainability has resonated greatly with buyers,” said Charles Beauduin, president of show owner CEMATEX, the European Committee of Textile Machinery Manufacturers.
Coming of age
Without a doubt, ITMA 2015 will be remembered as an event at which digital printing came of age, with a number of single-pass systems demonstrated producing beautifully-patterned fabrics at speeds of up to 1,000 square meters an hour. To put this in context, when the first digital textile printing systems were launched around 15-20 years ago, the achievable speed was around ten meters an hour – and at the time this was still considered an extraordinary achievement.
In the production of synthetic fibers and yarns, meanwhile, as well as in weaving, knitting and dyeing and finishing technology, it is the continued advance of sophisticated automation and control systems which is responsible for the lion’s share of improved efficiencies and ease of operation.
World leader
At the ITMA Asia + CITME 2014 exhibition in Shanghai, Hi-Tech Group Corporation (CHTC) had the largest hall virtually to itself, staking its claim – following a succession of major acquisitions – to being the undisputed leader in the textile machinery industry in 2015.
It is also a key manufacturer of synthetic fibers and the technology for manufacturing them, and Chairman Zhang Jie said the group was currently building capacities in all of the advanced raw materials which are currently in much demand globally, including carbon, UHMWPE, lyocell and PLA fibers.
“The application of these new types of fiber will effectively improve the structure of textile materials and the structure of the global textile industry,” he said.
At ITMA 2015 – with many of its brands having their own stands dotted around the halls – CHTC’s presence was understandably more modest than in Shanghai.
Nevertheless, CHTC is the only major textile machinery manufacturer in China under the control of the country’s state-owned Assets Supervision and Administration Commission and it had total assets of RMB 60 billion in 2014, with 200 subsidiary and branch companies, in total employing 54,000 people.
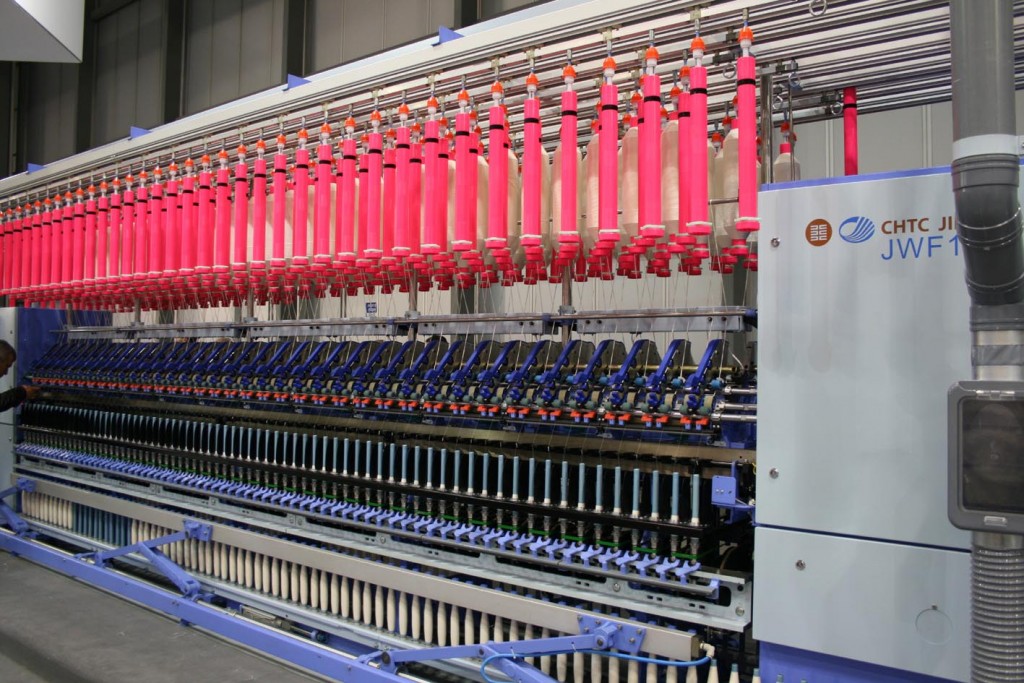
Mergers and acquisitions
Founded in 1998 and headquartered in Beijing, CHTC was built on the merger of many Chinese textile machinery companies and organizations previously run by the country’s national Ministry of Textiles.
In 2011, it took over the huge Hong Kong-headquartered Fong’s Group, which itself had been grown through the acquisition of a number of European machine builders, including:
- Switzerland’s Xorella, a manufacturer of steam setting and conditioning equipment for yarns and fabrics.
- German dyeing machinery maker Then.
- Goller, the Swiss manufacturer of wet finishing ranges.
Following the amalgamation of Fong’s into CHTC, further purchases of European companies have been made.
During 2011, CHTC acquired the former companies of Oerlikon’s Carding Division to form the Autefa Solutions Group, and in 2012 German finishing technology leader Monforts was acquired, as well as the Swiss dryer technology specialist Strahm, which has subsequently been merged with Autefa.
At CHTC’s ITMA 2015 press conference, Zhang Jie said that as far as textile machinery operations are concerned, the company’s current focus is understandably on synchronization of all of its operations and restructuring, in addition to extending levels of service.
He added that the company has recently installed its first intelligent spinning factory in China, which can be fully controlled by mobile phone from anywhere in the world.
“Increased automation and digital control will be accelerated across all of our machine ranges and this is only the first step,” he said. “We anticipate the further full integration with both suppliers and customers, because completely integrated supply chains are the future.”
Cloud control
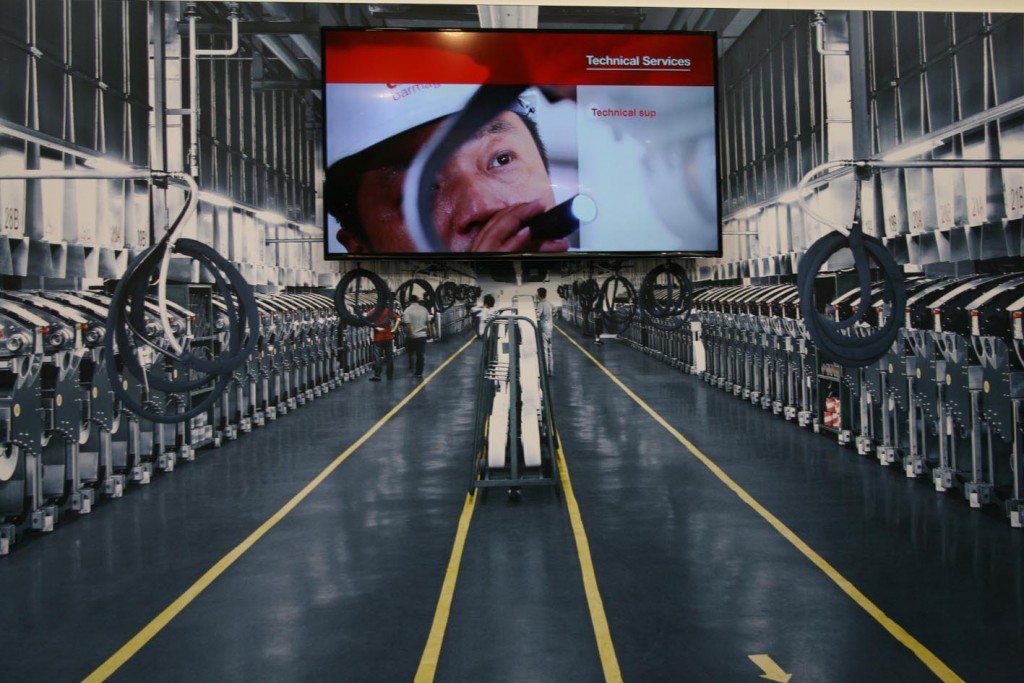
Manmade fibers leader Oerlikon reinforced this theme, presenting the next development stage of its modular Plant Operation Center (POC). This extended process and production control system can now capture and digitize all the steps of filament yarn production and processing, including plant technology from third party suppliers.
The networking of several plants via cloud computing is also possible. Manufacturing technology is linked via computer and Internet to make production and machine data available in real time as well as over the entire value chain, around the clock and anywhere.
Oerlikon reported that it secured a very significant new order at the show – and when we’re talking technology that has the capability to produce up to 3,000 tonnes of synthetic staple fibers a day, significant really does mean just that.
Oerlikon Neumag has an extensive plant portfolio for the production of synthetic staple fibers with the following options:
- Daily production of between five to 3,000 tonnes.
- One or two-step technologies.
- Polypropylene, polyester, recycled polyester, polyamide or alternative fibre systems for commodity or special applications.
Specifically designed for the economic production of staple fibers in smaller batch sizes of up to 15 tons per day, the compact Staple Force S 1000 on show in Milan requires low initial investment and is also very compactly constructed.
By replacing the conventional steam and water baths with a dry drawing process over godets, energy costs can be considerably reduced.
The technology combines the spinning and subsequent drawing in one process, making it is possible to produce up to 80 tons of staple fibers each day. The process is ideally suited to recycled polyester, whether chip or flake.
A major competitive advantage of the 300-tons per day staple fibre plant for commodity fibers, however, is the considerably higher profitability per ton compared to smaller plants, as a result of their energy efficiency.
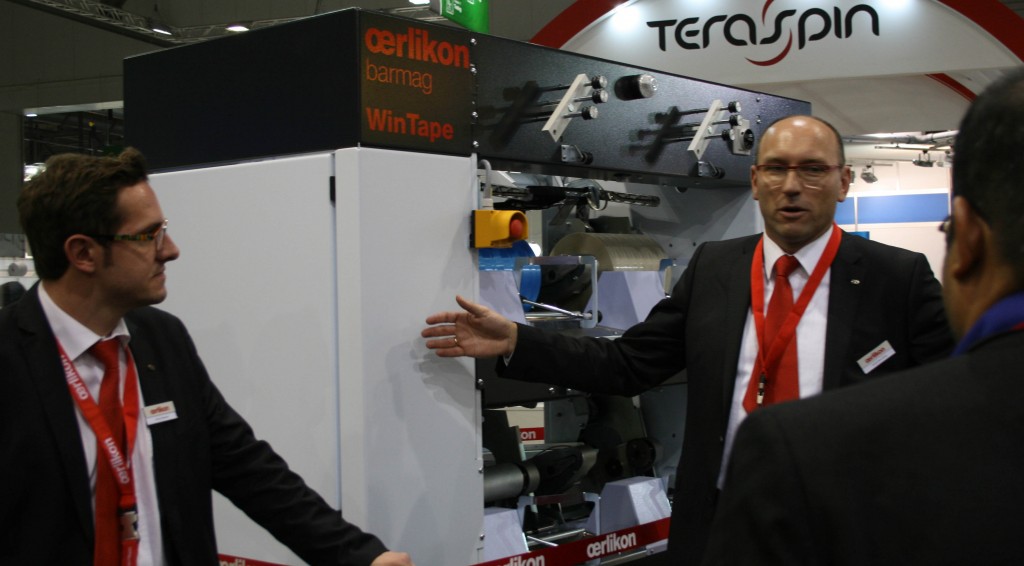
In the field of spun-dyed filament yarns, Oerlikon Barmag is meanwhile providing solutions for the efficient production of spun-dyed polyester POY and FDY microfibre yarns using its EvoQuench radial quenching systems.
A key here, are the long, stable duration of use for the sieves installed in the EvoQuench. This ensures a highly consistent yarn quality over long production periods and makes a considerable contribution to reducing downtimes and consumption costs.
Spunbond
Oerlikon Neumag also highlighted its technology for the production of spunbonded nonwovens for technical applications, which can reduce energy consumption by 20-30%.
Today, almost 50% of all nonwoven fabrics are produced directly from polymer chips, and this share is growing. While the majority is used in hygienic, medical and wipe products, spunbond and meltblown materials are frequently replacing carded nonwovens in technical applications as a result of their technical and economic advantages. In home construction, their share is already over 80% and for filter nonwovens over 50%. Geotextile applications are also growing.
“As a result, polyester is becoming increasingly significant as a raw material for technical spunbonds,” said André Wissenberg vice-president and head of marketing, corporate communications and public affairs. “One reason is that the world market price for polypropylene, which has been the fiber of choice to date, is now consistently higher than the price for PET. Another reason is that sustainability, thermal protection, energy consumption and insulation are playing an increasing role for important users such as the construction industry and polyester nonwovens often satisfy requirements with the lowest use of material and without additives. They protect against cooling, only absorb minimum moisture, can be easily used as insulating material, are good for insulation and recyclable, and thus present an alternative to plastic foams, glass wool or mineral wool.”
For such technical applications, the filaments need to have a very high tensile strength and often also allow a high elongation. These properties must be achieved with the lowest possible web-weight and optimized raw material usage, since the cost of raw material for spunbond production amounts to around 75-85% of production costs.
Benchmark comparisons with current products in Europe have proved that with the spunbond technology of Oerlikon Neumag, it is possible to achieve higher web strengths at a comparable web-weight. At the same time, the required stabilities can also be achieved with reduced web-weights.
Carbon recycling
In other news from the nonwovens technology sector, DiloGroup has installed a compact line for recycling carbon fibre at the Institute of Technical Textiles (ITA) in Augsburg, Germany.
At ITMA 2015 the group demonstrated not just one, but two full needlepunching lines over an area of 1,232 square meters consisting of fibre preparation units from DiloTemafa, cards and card feeding systems from DiloSpinnbau and crosslappers and needlelooms developed by DiloMachines.
The 3.2-metre-wide staple fibre needling line on show is highly suited to the production of technical textiles, and especially geotextiles.
Dilo’s latest VectorQuadro card (VQC) incorporates a modular transfer group between its breast and main section allowing it to be quickly switched to different carding configurations.
A major breakthrough is the new Super-DLSC 200 crosslapper.
“This allows web infeed speeds of up to 200 m/min to be achieved, depending on the fibre specification, in a bid to eliminate what can be a bottleneck point in a complete line,” said general manager Johann Philipp Dilo.
The CV1A web regulation system ensures improved evenness with a great potential for fibre savings. The very high web infeed speed has been made possible by a further increase of the drive power within the three-apron-layering system.
The layering width is seven meters and the new Di-Loom AB needleloom at the end of the line is said to have a very favorable price-performance ratio.
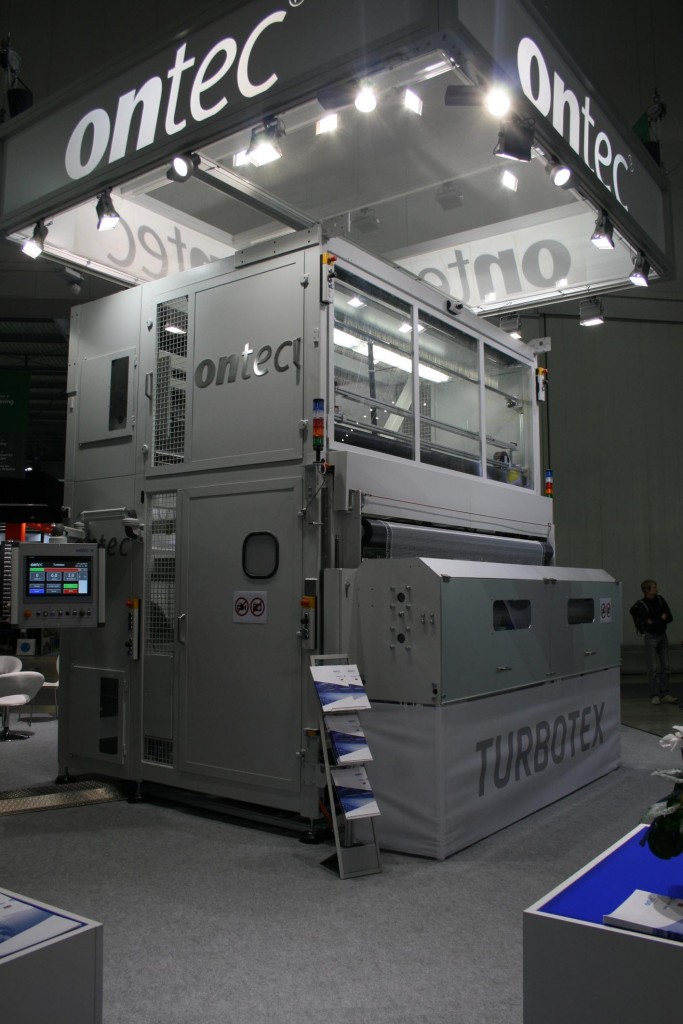
A second, more compact line displayed is for the production of high quality felts used in the medical sector and for those made from fibers such as carbon with a working width of 1.1 meters and a layering width of 2.2 meters.
Spunlace launch
Autefa Solutions announced that it would launch a new spunlace system characterized by a new energy-efficient jet design.
“Until now, Autefa has concentrated on cards, crosslappers, needlepunching systems and thermobonding technology,” said Vice-President Marco Fano, pictured with head of marketing Jutta Soell at the company’s carding machine displayed in Milan. “Following intensive R&D work, however, we believe our new jet design will allow manufacturers to achieve a 30% saving in energy compared to competing systems.”
Autefa Solutions unites the brands Autefa, Fehrer, F.O.R., Octir and Strahm and as mentioned earlier, is now part of China Hi-Tech Group Corporation.
Autefa’s latest card is designed for high production speeds and has been designed to allow easy access to cut down cleaning and maintenance times. The company’s Topliner CL 4004 SL crosslapper has already received the VDMA Blue Competence Award. With an infeed speed of up to 150 m/min and a precise weight distribution, the lapping of the web layers is continuously monitored to minimize rejects and save material.
Turbotex
Finally, an interesting new technology introduced in Milan is the Turbotex system, developed by Ontec Automation, based in Naila, Germany.
It makes scrims direct from either creels or beams and in a single pass can laminate them to either nonwovens or films. As such, the resulting materials are ideally suited for technical applications in construction, packaging, geotextiles, insulation and floorcoverings and the advantages of the process are considerable, explains Managing Director Volker Rossner.
“Our system uses just six per cent of the energy required to make such scrims by weaving, and additional finishing of these products is eliminated,” he says. “The personnel requirement is reduced and a thirty per cent thinner end product also saves material.”
Stepless adjustment of both the grid size in the weft direction and the overall fabric width is also possible, to significantly save on converting. The system is highly suited to high performance fibers such as glass, aramids and carbon, in addition to more widely used polyester, with a maximum weft speed of 4,000 insertions a minute for production of up to12 meters a minute. The extremely quiet system operates on 6 bars of pressurized air and a current of 400 volts.