By C. Burgstaller and B.M. Lekube, Transfercenter für Kunststofftechnik, Wels, Austria, and S. Riepler and W. Hermann, IFG Asota, Linz, Austria
In this work, we investigated the suitability of a bio-based elastomer to modify polylactic acid (PLA) towards more elasticity, in combination with a reactive coupling agent.
We found that this is possible in general, but the processing of the materials has to be carried out with care so as not to locally cross-link the materials, which would result in a reduction of properties.
The challenge
Today, the availability of resources and the end-of-life options of materials used in every application have to be considered. Public awareness about environmental pollution in general and plastics in the environment specifically are forcing producers to rethink their choice of materials.
While recycling plastics to reduce the consumption of crude oil and energy is a viable option for many applications, there are some end-uses in which recycling is not possible, owing to the contamination acquired by the material in its use.
Examples include plastics used in medical applications, where contamination presents an infection risk or prescription drugs can even leak into the environment, or in agricultural applications, where the plastics cannot be separated from the environment.
For these cases, bio-based and biodegradable plastics are an alternative, as these have lower carbon dioxide footprints when incinerated, as in the case of medical waste, and can degrade and more importantly be resorbed by the environment with much lower impact than conventional plastics.
When looking at the possibilities of bio-based and biodegradable plastics, there are only a few options that are promising in terms of availability and also material costs, the most prominent of them being PLA.
PLA is a thermoplastic material that can biodegrade under proper conditions. This is important as any residues can be resorbed by the environment. For example, the residues of PLA fibers from washing machines will have less environmental impact compared with regular polyester fibers.
One of the main drawbacks of PLA, however, is its brittleness, which is also exhibited as limited elongation and elasticity when fibers are produced.
The aim of this work is to modify PLA with a biodegradable elastomer component in reactive extrusion so that these fibers exhibit better elasticity and can therefore be used in textile applications.
Materials and methods
The materials used in this study were PLA (grade 2003D from NatureWorks, melt flow rate of 6 g/10 min at 210°C and 2.16 kg) and polybutylene succinate (PBS – Bionolle 1001 from Showa Denko, melt flow rate of 2.4 g/10 min at 190°C and 2.16 kg) as the biodegradable elastomer component.
To couple these two polymers, a multifunctional epoxy (Joncryl ADR 4360 from BASF) was used in a concentration of 0.1 wt percent in some formulations in the compounding step prior to fiber spinning.
The different compounds were produced on a co-rotating 24-mm twin-screw extruder (ThermoPrism TSE 24MC) equipped with a gravimetric dosing system. The melt strands were chopped after cooling in a water bath by a strand cutter.
Using these granules, fiber spinning was carried out on a laboratory fiber spinneret to produce fibers at a draw ratio of about 1:2 and approximately 20 dtex and without any crimp.
From pre-trials, we identified a formulation of 60 wt percent PLA and 40 wt percent PBS as a mixture that showed promising results.
These fibers were tested for their mechanical properties, in particular their elastic recovery by means of a universal test machine (500 N load cell, Zwick Roell Z0.5), where the pre-strain was applied by small clip-on weights.
The fibers were elongated to a set strain (e.g., 20 percent), and after reaching that the strain was released to record the recovery of the fibers, i.e. how much of the strain was permanent.
The test speed was 20 mm/min at an initial clamping length of 20 mm, and at least five fibers were tested per strain level.
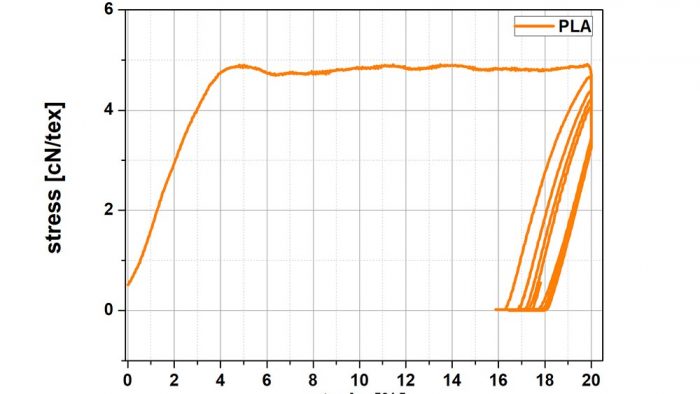
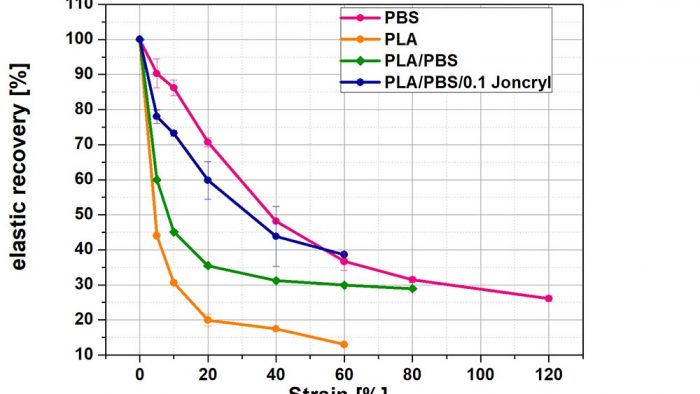
Study results
The elastic recovery behavior of 100 percent PLA is shown in Figure 1. A strain of up to 20 percent was applied to the fibers; the machine then reduced the strain and recorded the load.
Here it can be seen that the permanent deformation is about 16-18 percent of strain, and only 2 percent are recovering. This effect gets more serious at higher strains, which shows that PLA needs to be modified to improve its elastic recovery.
The elastic recovery behavior of different fibers is plotted in Figure 2. As mentioned above, PLA fibers show a low elastic recovery, even at low strains, and can be applied with a strain of up to 60 percent to exhibit some recovery.
PBS, on the other hand, shows much better elastic recovery, and recovers about 30% of the strain when elongated to 100 percent.
Together with its biodegradable properties this makes it a good blend partner for PLA. When using a blend with 40 wt% of PBS for fiber spinning, these fibers show an increased elastic recovery behavior compared with 100 percent PLA. For example, at 40 percent elongation the blended fibers recover 30 percent of the strain, while PLA recovers only around 18 percent, but the effect is limited.
To further improve this effect, a multifunctional epoxy (Joncryl) was added as a coupling agent, to increase the interaction between the different polymer chains and yield a material with elastic domains.
As shown in Figure 2, the elastic recovery behavior was further improved, reaching results close to 100 percent PBS, which shows that the coupling works.
The repeatability of this approach needs some further work, however. As we discovered, the scattering between different blends used for fiber spinning with the same formulation is relatively high – sometimes the improvement was negligible.
A closer inspection of the fibers revealed that these had thinner or thicker regions; we suspect that this is the result of gel particles heavily cross-linking the material, which can then no longer melt.
Such regions in the fibers will negatively influence the fiber properties, and therefore also the elastic recovery.
A possible way to reduce this is an improved processing setup, where the additive is dosing more uniformly into the melt to avoid gel particle formation.
Summary and conclusions
This research shows that PLA fibers, which show nearly no elastic recovery, can be modified with biodegradable elastomers such as PBS to improve elastic behavior.
Adding a coupling agent can improve that behavior further, although care must be taken in processing not to locally cross-link the material, which results in gel particles, as these have a negative influence on the fiber properties.
Nevertheless, the approach presented here should be investigated further, as the modification of PLA can change the properties to be more suitable for different fiber applications, which can help to substitute crude oil-based materials in applications where biodegradability is necessary.
Acknowledgements
The authors acknowledge the support from the Austrian research promotion agency for the BioModFiber project in the Produktion der Zukunft scheme.
For further information contact: Dr. Christoph Burgstaller Transfercenter für Kunststofftechnik GmbH Tel: +43 7242 2088 1017 Email: christoph.burgstaller@tckt.at Website: www.tckt.at