The complexity of absorbent hygiene products (AHPs) – baby diapers, femcare products and those for coping with adult incontinence – is not immediately apparent to consumers who never-
theless greatly value their comfort and convenience.
A typical open diaper – one that is fastened around the baby rather than the growing option of fully-formed pant styles – can consist of up to 20 separate functional components, all of which have to be assembled from running rolls of materials at speed in order to cost effectively produce what are extremely highly engineered systems for single-use, disposable products.
Key Components
GDM, a leading manufacturer of turnkey lines for the manufacture of AHPs headquartered in Offanengo, Italy, lists the components of a typical open diaper as: an elastic waist band; refastening tape;
a stretching rear wing; a front rigid wing; frontal tape; the topsheet; skin care lotion; the absorbent core; the acquisition and distribution layer; a standing leak guard; leg elastic, and the backsheet, along with a wetness indicator. Many of these components can in addition, be composed of combination layers of nonwovens, plastic films and superabsorbent polymer (SAP), and they also need to be stacked and bagged at extremely high speeds.
GDM’s premium line, the B12-W Red, is capable of the running assembly of up to 1,200 open baby diapers a minute and over the years, the company’s lines have been constantly improved in terms of configurability, in order to maximize lead times and cost efficiency.
To make them as modular as possible in order to accommodate individual customer requirements, GDM lines – which can be well over 100 feet long – are made up of 40 to 60 base modules, with approximately 10,000 parts.

Naturally, this allows much scope for constant evolution, especially given the increasing possibilities of digitalization. As part of the Coesia Group, GDM benefits from the internal synergies of a global organization with expertise in the construction of industrial machinery and plants for everything from tobacco and food to precision engineering and cosmetics.
“To fulfil the evolving needs of the market and satisfy such diverse expectations, the entire manufacturing industry is going through an Industry 4.0 strategy encompassing hardware, software and services, where concepts such as smart manufacturing, data analysis and Internet of Things become central,” said GDM’s head of sales and marketing Maurizio Cantoni. “This is not just a restyling. On the contrary, it is a through-and-through rethinking of manufacturing’s business model, head to toe, with far reaching implications for its value chain. This is a key focus for GDM in 2022.”
Culling
Notable GDM innovations in recent years have included a single culling system for high-speed AHP production lines. These lines are typically equipped with vision systems looking at each product to detect defects and when detected will remove three from the line – the actual defective diaper and the ones before and after it – in order to completely guarantee the fault has been removed.
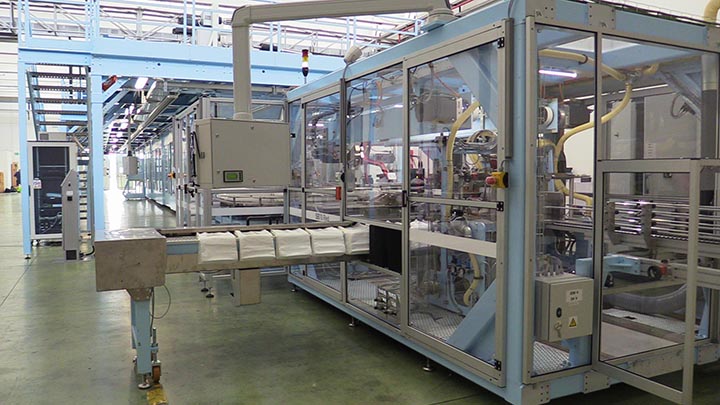
GDM’s single culling system ensures that only the defective product is rejected, to make considerable savings when machines are running at up to 1,200 pieces a minute. The system consists of a vision system to detect the product defects, a high-speed servo drive waste gate and a signal handling unit.
Crucial to its operation is the algorithm that handles the signals from vision system to machine PLC and activates the waste gate ensuring that the right product is always ejected. GDM’s single culling system is available for both new machines as well as a retrofit kit for existing machines and is vision system brand-independent, so it is potentially adaptable to all of the approximately 1,200 diaper machines
already on the market.
Zero Waste
Meanwhile, the GDM rear wing zero waste system significantly reduces downtime when changing the size of products on high-speed diaper converting lines.
Flexibility is supplied by the company’s patented Linear Motion and E-cam technologies to optimize processes, minimizing the necessary times required for product recipe, material and size setting activities. Within the rear wings application unit, the double shifter is equipped with linear motors, allowing the cross-machine repositioning of the wings. Thanks to synchronization between this technology and the dynamic shaping unit, it is possible to produce up to four open baby diaper product sizes without having to replace any mechanical components. Electronic cams, installed on the final accelerator of the rear wings unit, manage multiple sizes and product lengths without changes.
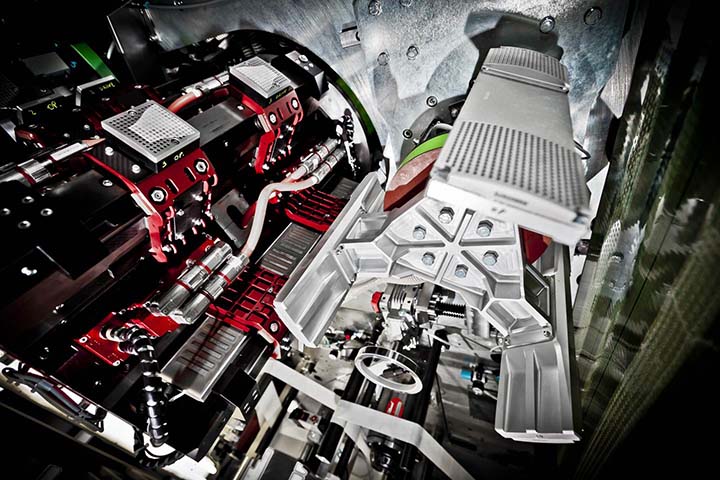
GDM recently claimed an INDEX™20 Innovation Award at the nonwovens show in Geneva which was eventually held in October 2021, for the development of an expandable welding wheel which generates a side seam welding in both baby and adult pant-type products. This technology enables the production of an extended number of sizes with the same unit and side-seam bonding and performance are guaranteed for a wide range of raw materials. The unit is composed of welding stations mounted onto a wheel-like system, allowing high-speed operation and requiring zero size-change time.
Absorbent Cores
Material developments can also have a significant impact on the production of AHPs and one of the biggest changes has been the move to thinner absorbent cores through increasingly substituting the fluff pulp component with more SAP.
The products of market leaders, including Procter & Gamble, increasingly moved in this direction, but ten years ago, Drylock Technologies, headquartered in Zele, Belgium, introduced the first entirely adhesive and fluff pulp-free absorbent cores in diapers, significantly reducing the products to just a few millimeters in thickness, compared to an average of 8mm for existing products.
In addition to reducing materials, the patented design of the Drylock diapers also enabled every truck to move 30% more stock than was previously possible. In addition, the thinner products reduced the shelf space requirement in stores while meeting consumer needs for more discretion and improved comfort.
Having tested the waters in Germany and other markets in Europe, the diapers quickly found favor on the wider markets and Lidl was the first to introduce its Toujours diaper range featuring DryLock technology into many more markets.
Since then, Drylock’s progress has been meteoric and the company has expanded across Europe. In 2017, Drylock also moved into the USA with the acquisition of Presto Absorbent Products Incorporated (PAPI) in Eau Claire, Wisconsin.
Further innovation also followed with the introduction of Magical Tubes for baby diapers – a technology for improved fit and air flow, along with enhanced leakage protection which piqued the interest of Procter & Gamble – and most recently, the first paper packaging for diapers.
In parallel to Drylock’s first success, GDM developed its own technology for reducing the amount of fluff pulp in absorbent cores based entirely on exploiting advanced CFD (computational fluid dynamic) simulations allowing customers to anticipate the final results through mathematic models of the raw materials. This is now standard on new production lines and also available as a retrofit kit on existing installations.
Expanding Wrap
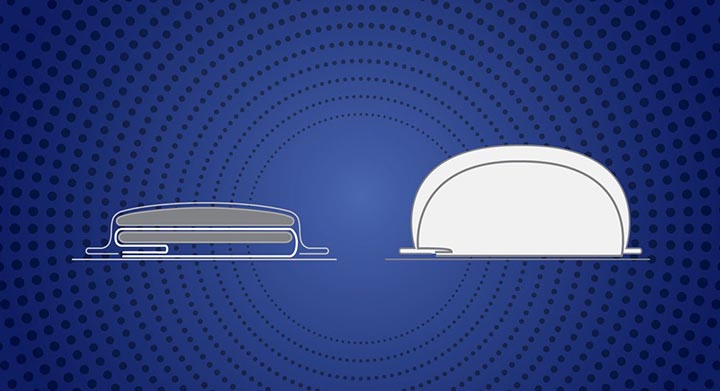
Another major manufacturer of lines for AHPs production, Curt G. Joa, of Sheboygan Falls, WI, has further developed the absorbent core with a patent-pending design which allows it to expand within the containment wrap, regardless of the blended fluff pulp and SAP ratio.
Essentially, the core grows as the product is insulted. The expandable wrap allows cores to be designed with higher amounts of SAP, resulting in thinner products that have higher absorbency.
“As designs evolve, products now contain higher quantities of SAP and these new designs absorb more fluid than ever before,” explained Chris Nelson, business development manager and co-inventor of the product. “The performance of the core depends on allowing the SAP to work and there was therefore a need for accommodating the core swell and expansion of SAP as fluid transfers through the product. Joa machines ensure core integrity by keeping the core materials contained, reducing the risk of leakage which decreases skin irritation and improves skin health.”
Further design features include a core edge definition that rivals die cut, balanced SAP distribution with more consistent core weights, and single or dual dusting layer capability with a homogenous blend of fluff and SAP.
Infinity
Also new from Curt G. Joa is the patented Infinity Roll, designed to ensure the complete control of nonwoven materials throughout the entire production process, regardless of material shape or size.
“The trend towards using lower grammage per square meter materials will accelerate, and these materials can become difficult to control at high production speeds,” explained Kevin Zeinemann, Joa’s corporate director of engineering.
“Furthermore, newer materials that incorporate sensory features, such as softness for example, may result in slippage during the converting process. The patented Infinity Roll corrects the process deviations that may otherwise result, reducing machine downtime and product quality defects.”
Another recently patented development is an automatic cuff defect correction system, which identifies, prevents and corrects defects in the cuff section of the diaper, including cuff folding and elastics, enabling correction without stopping the machine. In addition, it can individually reject spliced materials before they are combined to form an end product, correct acquisition and distribution layer (ADL) inversions and automatically rethread stretch materials.
Automation
When it comes to patents, Fameccanica, headquartered in Sambuceto di San Giovanni Teatino, Italy, filed 85 with the European Patent Office in 2021, pushing it to the top of the league of Italian companies as it seeks to increasingly diversify from its core business of AHP lines into a specialist in general smart factory automation and robotics.
The total number of Fameccanica patents has now risen to more than 750, covering many different sectors and technologies and in May this year, the company announced a collaboration with the Massachusetts Institute of Technology (MIT) on robotics and automation solutions.
Fameccanica is implementing a six-year action plan with the goal of developing synergies between MIT’s applied research programs and Fameccanica projects in the areas of robotics, industrial automation and sustainable manufacturing. Given the complexity of AHP manufacturing lines and the high degree of digitalization they already exploit, Fameccanica’s evolution is a perfectly logical progression.
Also in 2022, Angelini Industries – an Italian multi-business industrial group operating in 26 countries with 5,700 employees – has acquired 100% ownership of Fameccanica following its purchase of the 50% share Procter & Gamble has held in the company since 1992.
Angelini views the transaction as the first step towards the creation of an ecosystem of companies dedicated to the design and development of technologies, products and services aimed at improving production and industrial processes.