Hot-air nonwoven is three-dimensional porous fabric with fusible fiber as the main material. With these features, it is widely used in medical care and hygiene (e.g. sanitary towel, tampons, etc.), filtration (e.g., mask, air filter) and heat insulation. It is regarded as the most economical and practical porous fiber material.
The production principle of hot-air nonwoven involves hot air penetrating a loose fiber batt (normally ranges between 20 – 200 g/m2), melting the thermoplastic fiber on the surface of the batt, achieving binding at fiber crossovers, and thus producing nonwoven fabric with certain thickness and stable structure. The thermoplastic fiber is generally of low melting point (PE, PP, PET, etc.) and/or bi-component fiber. In a nutshell, the fabric is produced with the binder of fiber melts and bonds at the effect of temperature and hot air flow. Thus, without any additives of chemical binder, it is regarded as an environmentally friendly production process.
This article examines the production parameters of air-through bonding to find out the effect of different temperatures and heating time on the quality of air-through bonded nonwoven, with the aim of optimizing the production parameters and improving quality.
The experiment
Raw material and production process
Raw material: two different (PE/PP) bi-component fibers are used in this experiment, one is 2.22 dtex*38mm and the other is 1.67 dtex*38mm. They are both sheath-core bi-component fiber, the sheath of which is PE with the melting point at 125-130 C and core of which is PP with the melting point at 165-170 C.
The production line is designed and manufactured as a whole, from material feeding to oven and winding, by Zhengzhou Textile Machinery Engineering and Technology Co., Ltd., which ensures the fiber web of CV value within 5% on both cross and machine direction and the oven temperature is consistent in every corner. The two materials are mixed by 1:1 and go to the carding machine to form loose fiber batt. Then the web is delivered to a flat-belt air-through bonding machine (oven). The oven temperature and belt speed can be adjusted to make the fiber sheath (PE) melt and form molten droplet throughout the fabric cross-section, thus producing through-air bonded fabric.
Structure and property testing
For this article we conducted a series of testings and experiments to explore the effect of different production parameters to the fabric quality.
Grammage and thickness: This testing was intended to examine the precise weight per square meters of the fabric and the thickness.
Mechanical property: The breaking elongation of the fabric and the tensile strength were tested on both the machine direction and cross direction. The fabric sample was cut into pieces of 50mm*100mm. The testing machine stretching speed is 100mm/min.
Liquid Permeability: This test was designed to find out the time required for liquid to penetrate the fabric and the quantity of liquid that back-flows to the surface. The liquid is urine simulated 0.9% physiological saline. The fabric was also put under a weight of 4 kg (100mm*100mm) to find out the quantity of water that backflows to the surface.
Results and analysis
Thickness
Fig. 1.1 shows that as the fabric grammage increases from 18.20 g/m2 to 25.7 g/m2, the thickness also increases from 0.44mm to 0.65mm.
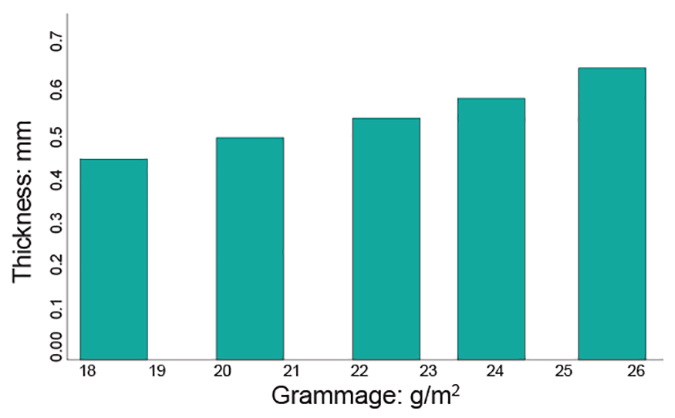
Fig. 1.2 shows the relation of fabric thickness to hot-air temperature. It can be seen that as hot-air temperature rises from 123.4 C to 137 C, the fabric thickness shows a trend of reduction. As the hot-air temperature rises above the melting pointing of the sheath of fiber, the sheath melts, and as the temperature rises higher, the melting and bonding increases, which, after ensuing pressing and drafting, become more condensed.

Mechanical property
For hot-air nonwoven fabric, grammage and and hot-air temperature are two important factors that affect the fabric tensile strength.
When the hot-air temperature is at 131 C and the time lasts for 84.3 seconds, the fabric tensile strength changes along with the change of fabric grammage, as shown in Fig. 2. From Fig. 2, we can conclude that with higher grammage of the fabric, the tensile strength of the fabric on both longitude and traverse direction increases accordingly. Comparing Fig. 2.1 and Fig. 2.2, it can be seen that the fabric tensile strength on longitude direction surpasses that on traverse direction. This difference enabled by the parallel production process, in which most of the fiber are paralleled on longitude direction.

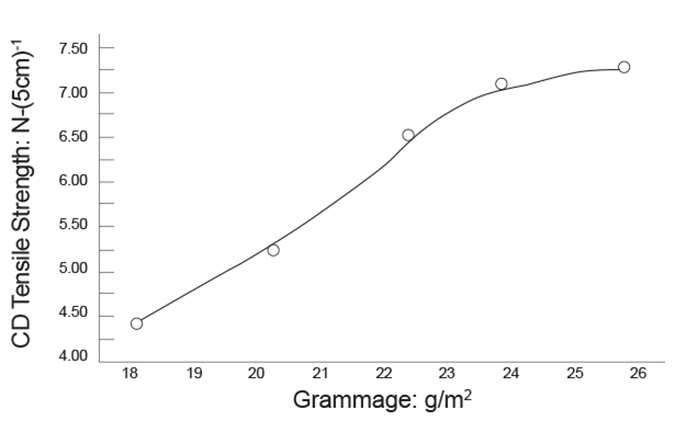
For fabric of 16.02g/m2 for 84.3 seconds, the curve in Fig. 3 shows the correlation of the tensile strength at different hot air temperatures. It shows that when the temperature rises from 123.4 C to 139.00 C, the tensile strength increases from 9.81N/(5cm) to 18.01N/(5cm) at longitude direction and from 3.01N/(5cm) to 6.66N/(5cm), indicating that hot-air temperature has significant influences on the tensile strength on both longitude and traverse direction. It should be noted that when temperature rises from 123.40 C to 127.20 C, the tensile strength rises at a higher rate than it does from 127.20 C to 139.00 C. This is because the melting point of the sheath of bi-component fiber (PE) is at 125 C-130 C, and when the temperature reached to this sweet zone of the melting point, the tensile strength rises at a higher rate.

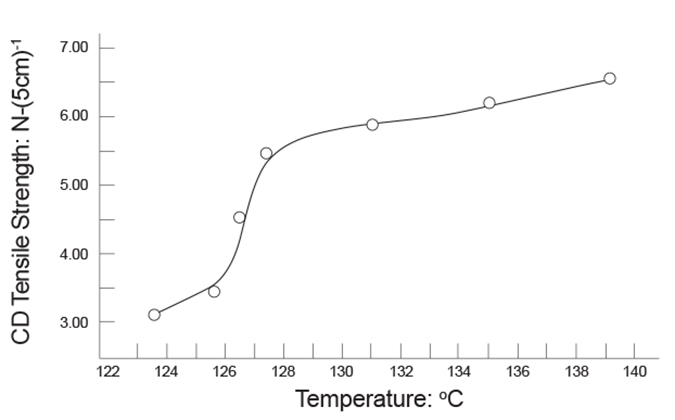
Liquid permeability
Hot-air nonwoven features being fluffy and porous which provides it with advantage for liquid penetrating. Fig. 4.1 shows the time that liquid passes through the fabric and the backflow quantity at different grammages.

From Fig. 4.1, it can be seen that the time for liquid to pass through increase with the increase of grammage of the fabric, for the fact that with higher grammage, the fabric becomes thicker and with more porosity, which elongates the time for liquid to go through all the porosity. Meanwhile, for a same sample of fabric with same grammage, the time of passing through is t1<t2<t3 (t1, t2 and t3 refer to the time for liquid to pass through at the first time, second time and third time respectively).
Fig. 4.2 shows that with higher grammage, the liquid back quantity increases accordingly. This is because with high grammage and thickness, more liquid remains in the fabric and causes more backflow.

As production process remains the same, the thickness of fabric increases along with the increase of grammage. When the fabric grammage remains the same, higher temperature would cause less thickness of fabric.
Fabric grammage has a huge influence on fabric tensile strength. As other production parameters remain the same, the rise of temperature would enhance the tensile strength of the fabric on both longitude and traverse direction. And as the temperature rising from 123.40 C to 127.20 C, the tensile strength increases at a higher rate.
Fabric grammage is an important factor that affects the liquid permeability and backflow amount. With the increase of grammage, the time of liquid passing through and liquid back flow amount increases accordingly. Thus, to reduce the grammage of the fabric is one of the solutions to enhance the comfort of the absorbency of hot-air nonwoven products.