High-modulus, high-tenacity fibers have played a key role in the development of many performance textiles
Performance fabrics – one of the fastest growing sectors of the industry – are textiles that provide additional functionalities, such as repellency, resistance or protection from, for example, liquids, extreme temperature or ultraviolet (UV) light, and include fabrics that resist wrinkles, soiling or odors, and/or protect from a specific environmental condition.
Performance textiles were initially introduced into the activewear and outdoor markets for such activities as aerobics, running, cycling, hiking, swimming and skiing, but they have now crossed over into the fashion and home furnishings sectors.
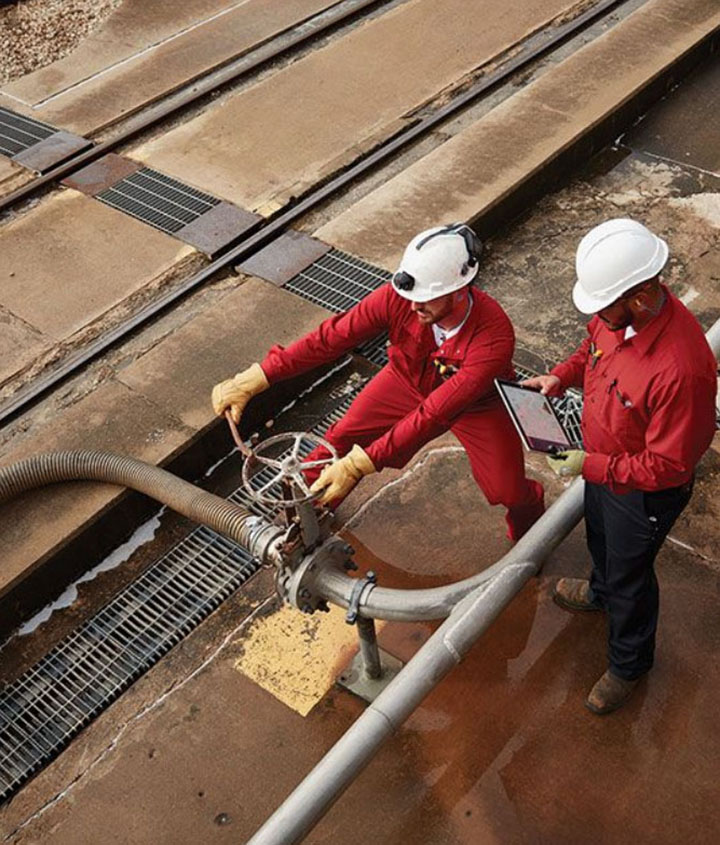
Classification
In some respects, all but the cheapest commodity fibers, as well as natural fibers such as cotton, wool and silk that are mainly used for fashion products like apparel, furnishings and floor coverings, can be classed as high-performance fibers.
The large-scale introduction of manmade fibers from the first half of the 20th century created the category of technical textiles that are principally used in engineering or industrial applications.
The next generation of manmade fibers – high-performance fibers or high-modulus, high-tenacity fibers – have shown a step change in strength and stiffness, according to the late Professor John Hearle in his introduction to High-Performance Fibers (2001, Woodhead Publishing).
High-performance fibers, which have largely been developed and commercialized over the past 50 years or so, are fibers that are engineered for specific uses that require exceptional strength, stiffness, heat resistance or chemical resistance. These fibers are increasingly being used for a wide range of applications, including geotextiles and geomembranes and for construction and civil engineering projects, as well as in composite materials.
High-modulus, high-tenacity fibers can be divided into three groups: polymer fibers such as aramids and polyethylene fibers; carbon fibers; and inorganic fibers based on glass and ceramic fibers. This article focuses on the first category.
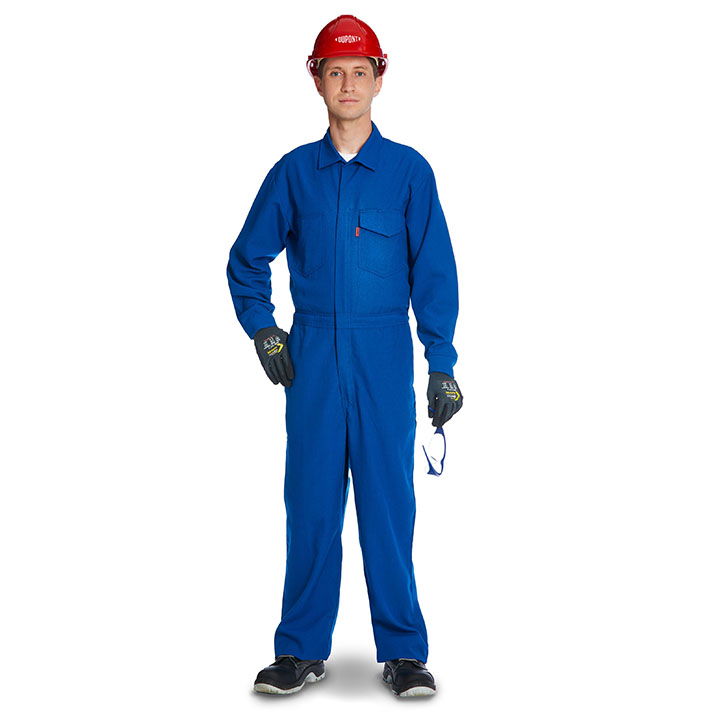
Aramid fibers
Aromatic polyamide (aramid) fibers, particularly meta-aramid fibers, exhibit high temperature resistance and stability. Materials based on them have been developed for specific industrial heat-resistant applications.
Advanced composites reinforced with aramid fibers have also found application in areas where the strength-to-weight and stiffness-to-weight ratios of such materials make them attractive for use over conventional materials like aluminum and steel, such as in the manufacture of structural aircraft components.
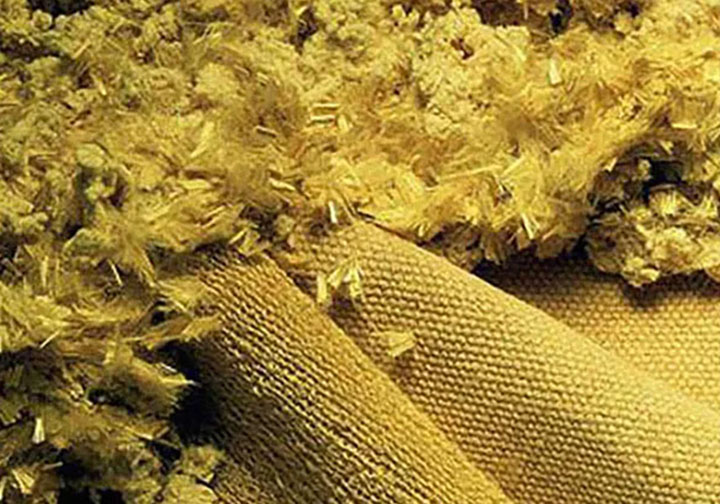
Meta-aramid fibers
Originally called HT-1, Nomex – poly(m-phenylene isophthalamide) – was the first commercially available aramid fiber. Developed in the 1960s and commercialized in 1967 by DuPont, it was initially used as fabric for racing car driver suits.
Nomex has excellent heat and flame resistance and can withstand temperatures of up to 370°C. It also has high chemical resistance, low thermal shrinkage, self-extinguishing flame-retardant properties and a soft hand that yields good textile properties. It also has high chemical resistance, low thermal shrinkage, self-extinguishing flame-retardant properties and a soft hand that yields good textile properties.
Compared with the para-aramid fiber Kevlar, Nomex has a lower tensile strength and modulus, but is flexible and higher in elongation, making it an ideal yarn for fabrics.
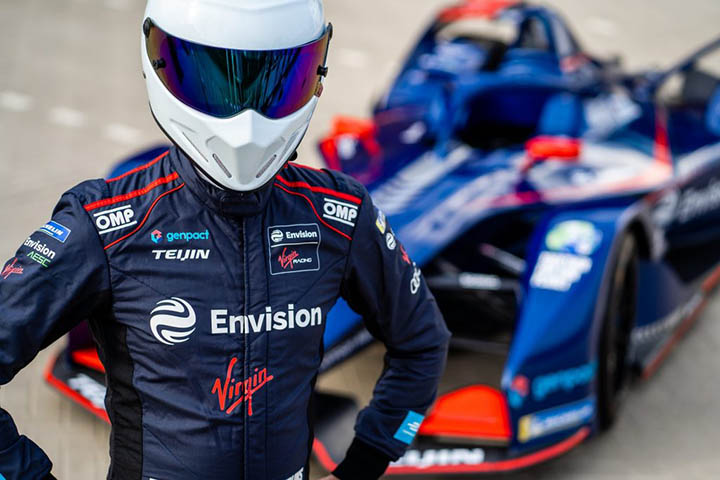
Teijin’s meta-aramid fiber is Teijinconex, which also offers excellent resistance to heat, flame and chemicals, making it suitable for use in the manufacture of protective textiles and other industrial applications, including hoses, filters and copy cleaners.
Teijinconex can be supplied in different fiber lengths and linear densities. It is available not only in raw white, but also in a range of dope-dyed colors, allowing for color matching in combination with para-aramid fibers. Further, the Teijinconex neo variant can be easily dyed in any color, allowing for the production of protective workwear in company colors.
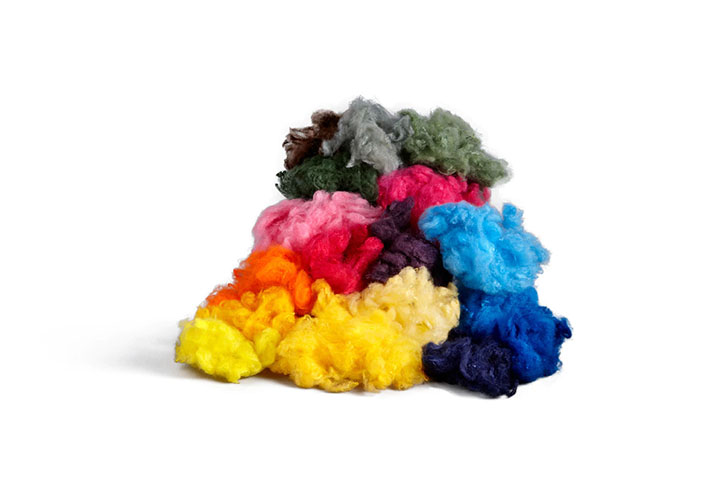
Para-aramid fibers
Perhaps the most successful para-aramid fiber is Kevlar – poly(p-phenylene terephthalamide) (PPTA). It was first developed by DuPont chemist Stephanie Kwolek in the 1930s, but not used commercially until the 1970s as a replacement for steel in racing car tires.
Kevlar offers a high strength-to-weight ratio, low elongation to break, good heat and flame resistance, good chemical resistance, high cut resistance and excellent ballistic properties.
First made commercially available in 1987, Technora is Teijin Aramid’s high-end, high-performance, PPTA-based para-aramid yarn that is eight times stronger than steel and has a high modulus, as well as excellent heat and chemical resistance.
Technora’s characteristics originate from the unique molecular and crystalline structure of the aramid, with molecular chains preferentially oriented along the filament axis. It is produced by condensation polymerization of different copolymers, yielding a high-modulus, low-creep and thermally stable fiber.
Applications are rubber reinforcement in automotive hoses, power-transmission belts for automotive, industrial and agricultural applications, as well as umbilical hose reinforcement in the oil and gas industry.
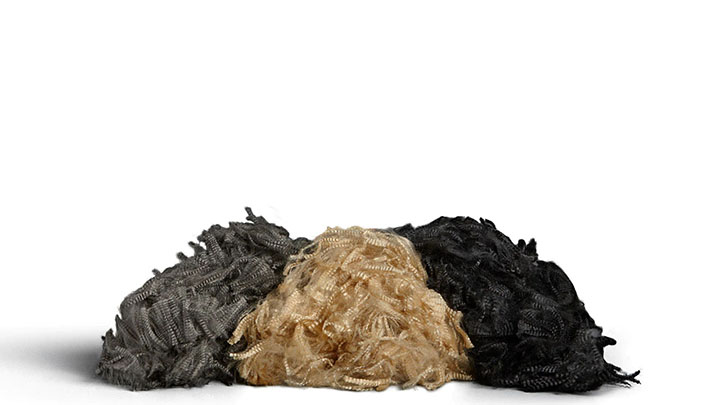
Technora is also used for tape reinforcement in flexible pipes, in ropes for high-temperature and dynamic-loading applications, in heat-resistant fabrics and cut-protection products, and in composite reinforcements for increased durability.
Another Teijin flagship brand – Twaron – is a para-aramid, high-performance yarn that offers well-balanced performance in terms of mechanical properties, chemical resistance and thermal stability that makes it suitable for use across a wide range of challenging applications and industries, from ballistic protection to heat and cut protection, and from oil and gas to the automotive and telecommunications industries.
The unique characteristics of Twaron are the result of its 100% para-crystalline structure with molecular chains preferentially oriented along the yarn filament axis.
Polyarylate fibers
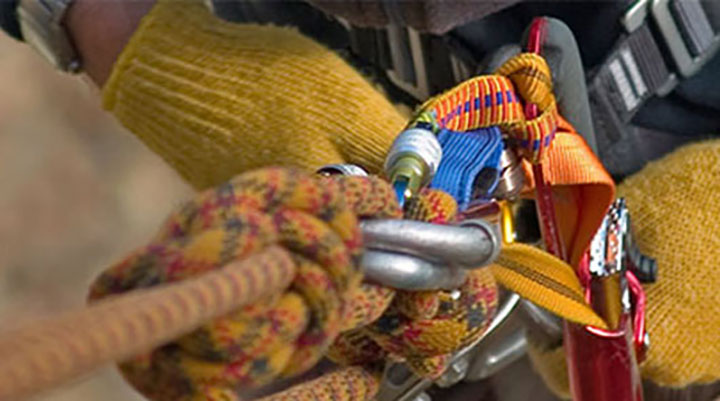
Polyarylate fibers are high-performance multifilament yarns spun from liquid crystal polymers (LCP). Research into LCPs began in the 1970s, resulting in a wholly aromatic polyester fiber called Vectran, which, because of its relatively high cost, remains a niche product.
First produced in 1990, Vectran is the only commercially available melt-spun LCP fiber, spun from Vectra LCP. It was originally created by Celanese and is now manufactured by Kuraray. (Chemically, it is an aromatic polyester produced by the polycondensation of 4-hydroxybenzoic acid and 6-hydroxynaphthalene-2-carboxylic acid.)
Vectran is produced in a melt-extrusion process, which orients the molecules along the fiber axis, resulting in a high-tenacity fiber that is five times stronger than steel and 10 times stronger than aluminum on a weight-for-weight basis. It also has high chemical-resistance and flex fatigue properties.
Further, Vectran exhibits good abrasion resistance, good high-temperature resistance and high tenacity and modulus. Besides ensuring minimal moisture absorption and outstanding vibration damping characteristics, it is stable under static loads, showing negligible creep, but is sensitive to UV light.
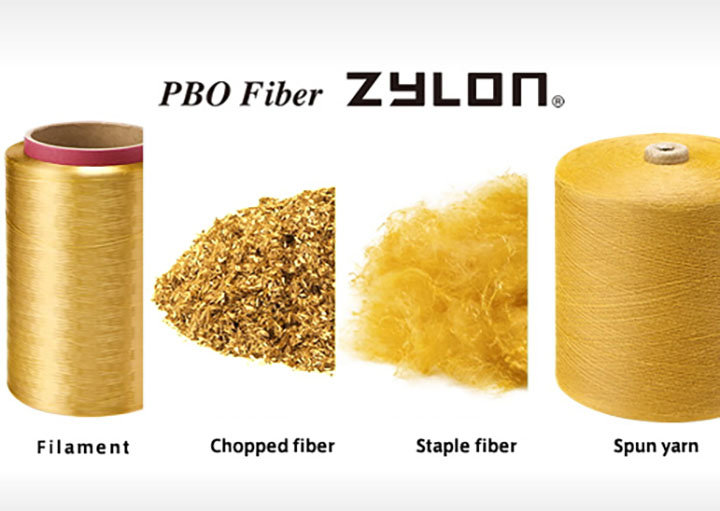
Vectran is principally used in the building, textile and coating industry. Major applications include cut-resistant gloves and clothing, sailcloth, fishing line, tow cables, inflatable structures, heavy-lifting lines, puncture-resistant bicycle tires and cordage. Vectran fiber has been chosen for NASA space systems owing to its outstanding performance properties.
According to Netherlands-based Fibr-XL Performance, there are several key differences between Vectran fiber and two other high-performance fibers – aramid and ultra-high molecular weight polyethylene (UHMWPE). Vectran fiber is thermotropic; it is melt-spun and melts at a high temperature. Aramid fiber is lyotropic; it is solvent-spun and does not melt at high temperature. UHMWPE fiber is gel-spun and melts at a low temperature.
High-strength polyethylene
Ultra-high molecular weight polyethylene (UHMWPE) was first polymerized in the 1950s, and the first UHMWPE fibers were commercialized in the late 1970s.
UHMWPE is a type of polyolefin composed of long chains of polyethylene with a very high percentage of parallel orientation and high level of crystallinity. The long polymer chains enable load transfer by strengthening intermolecular interactions.
UHMWPE fibers are manufactured in a gel-spinning process. They exhibit an excellent strength-to-weight ratio, high abrasion resistance, low specific gravity, stability to UV radiation, and they are chemically inert (except for strong oxidizing acids) and resistant to fatigue and internal friction.
UHMWPE fibers include Spectra from Honeywell and Dyneema from DSM. (Netherlands-based DSM recently announced the sale of its protective materials business, including the Dyneema brand, to the U.S. manufacturer of specialized polymer materials Avient for nearly US$1.5B.)
Applications for UHMWPE fibers include armor, cut-resistant gloves, bow strings, climbing equipment, automotive winching, fishing line, spear lines for spearguns, high-performance sails, suspension lines on sport parachutes and paragliders, rigging in yachting, kites, and kite lines for kite sports.
High-performance polyethylene
The properties of high-performance polyethylene (HPPE) fibers can be utilized in ballistic applications and also in cut-resistant gloves, fencing suits and chainsaw protective clothing.
For cut resistance, optimum protection can often be achieved by combining high-performance fibers with stainless steel or glass fibers, while such fibers as polyamide, polyester and cotton can be added to improve wearer comfort.
In non-ballistic composites, HPPE fibers are mainly used to improve the impact resistance and energy absorption of glass or carbon fiber-reinforced products. They can also provide weight savings, such as in motorsport helmets and in combination with wood laminates for boat hulls.
The low weight and high strength of HPPE fibers make it possible to produce heavy-duty ropes that can float on water, are flexible and have a low elongation, making them easy to handle as well as exhibiting good abrasion and fatigue resistance.
Oblix is an ultra-strong high-modulus polyethylene fiber produced by DSM that is impregnated at the filament level with a high-performance thermoplastic resin. This composite material offers high strength combined with a high level of abrasion and UV resistance.
In addition, Oblix offers superior performance in dynamic bend-over-sheave applications. The product has been engineered for critical applications where extreme strength and durability are paramount, says supplier FibrXL.
PBI fibers
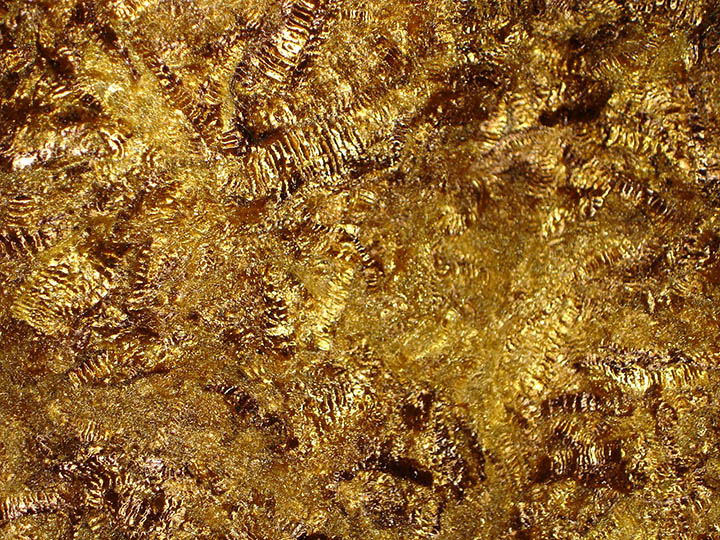
Polybenzimidazole (PBI) fibers are a class of extremely heat-resistant synthetic fibers, formed from completely aromatic polyamides. They are fibers in which the fiber-forming substance is a long-chain aromatic polymer having recurring imidazole groups as one of the main structural repeat units in the polymer backbone.
PBI is prepared from an aromatic tetraamine and an aromatic dicarboxylic acid or a derivative of it. The resin is then spun into fibers via a dry-spinning process using dimethyl acetamide as a solvent.
The only commercial PBI fiber is poly (2,2’-m-phenylene-5,5’-bibenzimidazole). Hoechst Celanese was the first to produce PBI products under the Celazole (U-series) tradename, which was quickly followed by PBI-Polyaryleneketone blends (T-series).
PBI fiber was originally developed by Celanese for the NASA Apollo space program because of its inherent flame-resistance properties and chemical stability. Today, the only producer of PBI fibers is PBI Performance Products, a subsidiary of the InterTech Group, which acquired the PBI business from Celanese in 2005.
The development of fibers, from utilitarian, pre-industrial fibers to man-made fibers for technical applications and now extended to high-performance end-uses, shows no signs of stopping any time soon.
PBO fibers
Polybenzoxazole (PBO) is a high-performance, heat-resistant fiber with a benzene-fused oxazole ring structure. The fiber is almost twice as strong as aramid fibers such as Kevlar and Nomex and about 10 times stronger than steel, making it the world’s strongest manmade organic fiber. It also has a 100°C higher decomposition temperature than aramid and exhibits very little creep under stress, which makes it suitable for high continuous loads.
The only manufacturer of PBO fibers is Toyobo which sells the fibers under the Zylon tradename. It offers two types: AS (as spun) and HM (high modulus). The HM fiber has a higher modulus and lower elongation at break.
Zylon PBO is a rigid-rod isotropic crystal polymer that is spun by a dry-jet wet-spinning process. The fiber is difficult to manufacture and rather expensive.
PBO fibers are used for demanding applications, including bulletproof vests, heat-resistant garments (safety gloves and firefighter uniforms), high-performance sporting goods (bicycle spokes, yacht ropes, rackets, snowboards and rider suits) and various civil engineering materials.
Polyimide fibers

Polyimide (PI) fibers are a class of heat-resistant and fairly strong synthetic fibers with an orange to yellow color. They are prepared by a two-step process from aromatic diamines and aromatic tetracarboxylic dianhydrides.
PI fibers are often chosen for demanding applications where high temperature, corrosion, wear and creep resistance are required. The high-performance properties are maintained during continuous use to temperatures up to 260°C and to short-term exposure of 550°C.
PI fibers can be produced by a dry-spinning process from a polyamic acid solution. The precursor fibers are then transformed into PI fibers by a subsequent heat-treatment process.
While expensive and difficult to manufacture, PI fibers have a much higher glass transition temperature (about 400°C) and a much higher melting point than other fibers, such as polyester and acrylic. And owing to the aromatic structure, PI fibers have a low flammability and excellent chemical resistance to most chemicals; they are also lightweight.
PI fibers are used for high-performance flexible cables in the electronics industry, as a filter material for hot gases in the chemicals industry and for heat-protective clothing. They are also used in multi-layer insulation of spacecraft and astronauts’ spacesuits.
The base material for P84 PI fibers, manufactured by Evonik, is composed of aromatic backbone units only. It is derived from aromatic dianhydrides and aromatic diisocyanates and exhibits a high degree of thermal stability. Despite the non-melting, aromatic, halogen-free structure it is classified as non-flammable with a limiting oxygen index (LOI) of 38%.
Owing to their chemical and physical properties, P84 fibers are used for a variety of applications, ranging from filter media for high-temperature filtration, protective clothing and sealing materials for spacecraft to various high-temperature applications, such as heat insulation.
Next-generation fibers
The development of fibers, from utilitarian, pre-industrial fibers to man-made fibers for technical applications and now extended to high-performance end-uses, shows no signs of stopping any time soon.
The next generation of fibers – so-called smart fibers that can react to an external stimulus, such as temperature or light, or can record, store and transmit data – is already here.