In light of the ongoing coronavirus (COVID-19) pandemic and the supply chain challenges this global emergency has presented for the manufacture of critical nonwoven-intensive products, such as personal protective equipment (masks, gowns, hair covers, shoe covers, etc.) and wipes of various kinds, IFJ reached out to leading nonwoven industry associations in China, Europe and North America with the aim of providing a global view.
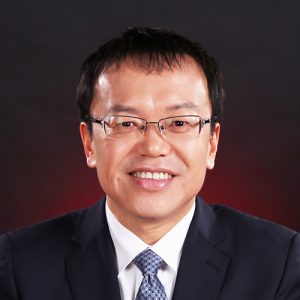

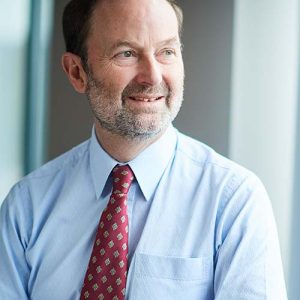
The nonwovens industry’s response to the pandemic, while commendable, presents challenges, opportunities for improvement and ultimately lessons to be learned as we consider the way forward in a world where global pandemics may be a more common reality. To this end, we asked our subject matter experts, what do you see as the nonwoven industry’s:
primary challenges in responding to COVID-19 and similar pandemics we may face in the future?
Li Lingshen: Since the outbreak of the coronavirus, personal protective equipment (PPE) and wipes have become very important products in the fight against COVID-19. The production and supply of these products were a high concern for the government, the public and the media.
China ’s Ministry of Industry and Information Technology, the National Development and Reform Commission are responsible for the production and supply, the National Administration for Market Regulation is responsible for the quality supervision. China Nonwovens and Industrial Textiles Association (CNITA), as a national industry organization in this field, has provided a lot of support for the work of these government departments. In responding to COVID-19, China’s nonwovens industry faces the following challenges:
- First, industrial information is insufficient. China is the largest producer of masks in the world, but masks account for a very low proportion in China’s nonwovens industry. Before the outbreak, the daily production capacity was about 20 million. Mostly small and medium-sized enterprises are engaged in mask production, and they are scattered in different fields, such as textile, medicine, health, etc. Obtaining comprehensive information of these enterprises in the early stage of the outbreak and accurately assessing the supply capacity have become the most important issues
The supply of raw materials, such as meltblown, spunbond, spunlace, hot air nonwovens has become the biggest bottleneck in the entire supply chain, and the price of these materials has risen sharply.
- Second, supply chain collaboration was not sufficient during the early stage of the outbreak. The outbreak occurred at the Spring Festival, the most important festival in China. Enterprises in the entire industrial chain had stopped production, and workers returned to their hometowns for the holiday. Therefore, gradually restarting the industrial chain on the premise of COVID-19 prevention was the primary task in the initial stages of the pandemic. As the pandemic worsened, a large number of enterprises purchased mask machines, and clothing and home textile companies began to convert to medical protective clothing. By the end of April, the daily production capacity of masks exceeded 500 million, and the daily production capacity of medical protective clothing exceeded 1.5 million. The supply of raw materials, such as meltblown, spunbond, spunlace, hot air nonwovens has become the biggest bottleneck in the entire supply chain, and the price of these materials has risen sharply.
- Third, the standards and regulations for masks and protective clothing are not uniform. A large number of China’s companies adopt the EU and U.S. standards to produce protective clothing for exports. In the early stage of the outbreak, although not adopting Chinese standards, the products of these companies were urgently permitted by China Regulatory Authority to be used for prevention and control of COVID-19. This measure effectively alleviated the contradiction of production capacity. In April, with the spread of the coronavirus around the world, the export of Chinese masks and protective clothing once again faced inconsistencies in the standards and supervision of various countries, which caused great problems to the production and supervision.
Dave Rousse: The COVID-19-driven need for personal protective equipment and for disinfectant wipes, and other wet wipes in light of the toilet paper shortage, has required the full engagement of the nonwovens industry.
Prior to 2020 (i.e., pre-COVID-19), over 80% of the U.S. demand for medical and surgical facemasks (N95 Respirators, N95 Masks, ASTM Level 1,2,3 Masks) was supplied by China and Taiwan. Many of the Level 3 and Level 4 Surgical Gowns were cut-and-sewn in Asian countries, even if the nonwoven fabric was made and coated/laminated in the U.S.
When the COVID-19 situation took hold, many of these supply chains were disrupted as countries withdrew exports of these items to supply their own national demands. These developments exposed the risks related to long supply chains subject to local mandates, low inventories (because supply chains had been working well), and single-source suppliers (as back-ups add cost and time), and risk-avoidance was secondary.
When the COVID-19 situation took hold, many of these supply chains were disrupted as countries withdrew exports of these items to supply their own national demands.
For wipes, the issue was the shear volume of demand, which continues today, as more people are using more wipes for the surface and skin cleaning associated with Centers for Disease Control guidance.
Addressing these structural issues in a competitive market economy may require some policy changes by the federal government to maintain a level playing field in the private sector, and to eliminate the “bidding war” each state went through in trying to secure their own hospital supplies during the early stages of the COVID-19 pandemic.
Pierre Wiertz: The primary challenge presented by the COVID-19 pandemic was, of course, surprise and an unprecedented need for nonwoven products. Our industry is used to stable, long-term demand. Now nonwovens and related industries are proving to be an essential partner in the fight against the coronavirus pandemic, and facemasks, personal protective equipment, medical supplies and wipes are among the nonwoven-intensive technologies particularly relevant to the COVID-19 response effort. The availability of disposable hygiene and medical products is an essential element in the fight against COVID-19.
Another challenge has been the “knowledge gap” about the crucial role of nonwovens. Industry in general and trade associations, such as our own, have an important role in relaying information on supply chain issues, production capacity and lead times so that authorities can plan accordingly.
Early on during this crisis we sent a letter to the European Commission, requesting its support in working with Member States to ensure that all production facilities where these products are manufactured are kept fully operational in the interest of public health. And we continue to work closely with the services of the European Commission to find solutions to the continued provision of the essential medical and protective equipment and to any bottleneck in the supply chain.
But we are still dealing with the unknown and unexpected. Before now meltblown has not been a strategic commodity, and predicting prices and ensuring steady supply will not be easy.
But we are still dealing with the unknown and unexpected. Before now meltblown has not been a strategic commodity, and predicting prices and ensuring steady supply will not be easy. And meeting demand is not simply a raw material issue either; to install an assembly line of meltblown can take many months.
Facing numerous requests from start-ups and new ventures with little or no experience in our sector has forced us to open the eyes of their initiators about the aforementioned realities.
primary opportunities for improvement and/or new technology development to better position for similar pandemics in the future?
Dave Rousse: Out of every crisis comes opportunity, and we have seen some new material developments in facemask media to address the shortage of meltblown for N95-quality facemasks. We have also seen a nimbleness and adaptability of some producers of meltblown for the sorbents industry quickly pivot some equipment to the lighter-weight meltblown required for N95-quality facemasks. And we have collaborated with other trade associations serving the textile sector to enable woven fabrics to satisfy the demand for Level 1 and Level 2 isolation gowns. Some equipment makers for converting nonwovens quickly came up with facemask converting machines to supply the overnight demand for more facemask manufacturing.
Out of every crisis comes opportunity, and we have seen some new material developments in facemask media to address the shortage of meltblown for N95-quality facemasks.
All of these developments indicate an adaptability and flexibility so much needed to deal with the next pandemic.
Pierre Wiertz: Industry is already pushing capacity limits to meet the exponential rise in demand, and along with this we need continued coordinated and collective action from the EU and member states to maintain open trade and efficient supply chains, both within the EU and with the EU’s trading partners. Already the European Commission has created a strategic common European reserve of medical equipment such as ventilators, personal protective equipment, reusable masks, vaccines and therapeutics and laboratory supplies.
On the technical side, I expect we will see a lot of movement as companies look for efficient alternatives to meltblown and the lead times to supply a production line is already shrinking.
On the technical side, I expect we will see a lot of movement as companies look for efficient alternatives to meltblown and the lead times to supply a production line is already shrinking.
With the support of the European Commission, EDANA is setting up a new working group, one the missions of which will be to promote the sustainable development of an independent and self-sufficient supply chain for medical facemasks and personal protective masks in the EU.
Li Lingshen: China’s nonwovens and related industries have provided a very sufficient guarantee of products and technical capacity to combat the pandemic. China has achieved the localization of spunbond, meltblown nonwovens and polypropylene. In 2019, the output of polypropylene spunbond nonwovens in China reached 1.989 million tons, and the output of meltblown nonwovens was 66,000 tons. During the pandemic, enterprises and research institutes cooperated to install and debug new production lines and transform SMS lines.
Meltblown nonwovens for masks increased from the usual daily production of 200 tons to 1,000 tons.
In response to possible outbreaks in the future, China’s nonwovens industry will strengthen the research and development of PPE and raw materials …
The outbreak of COVID-19 is not only a test, but also an opportunity for China’s nonwovens industry. In response to possible outbreaks in the future, China’s nonwovens industry will strengthen the research and development of PPE and raw materials, especially high filtration efficiency meltblown nonwovens, electrospinning, high-protection grade fabrics and washable reusable fabrics to protect the safety of medical staff.
In response to the needs of ordinary people for pandemic prevention, we have developed civilian masks with different levels of protection to achieve a balance of protection and cost. We will formulate and improve the standards, evaluation and certification systems of masks and protective clothing for different groups of people and application scenarios, and regulate the order of production and go-to-market practices.
primary lessons learned as we consider COVID-19’s impact on the nonwoven industry’s supply chain for critical products such as PPE and wipes?
Pierre Wiertz: As I touched upon earlier, self-sufficiency will be key, and we are seeing support to encourage European production and ensure future production capacity and supplies. In Germany a new subsidy scheme is being developed in which the government will cover 30% of the cost of a meltblown production line.
In Germany a new subsidy scheme is being developed in which the government will cover 30% of the cost of a meltblown production line.
We estimate that Europe is set to triple its output of meltblown between March and the end of the year, from about 500 tons a month to 1,500 tons.
Li Lingshen: CNITA took the initiative in the PPE and wipes supplies, and actively cooperated with the government to facilitate information collection, enterprise resumption of production, coordination of efficient operation of the supply chain, regulation of industry operation, and standardization of products. Good results have been achieved. There are some experiences to share:
- First, for severe natural disasters and large-scale public health incidents, we need to establish an integral database of production enterprises of raw materials, equipment and products, establish whitelists of key enterprises, and reserve emergency supplies of technology and production capacity to facilitate the mobilization of the nonwovens industry’s plunge into supplies in a short time.
It is necessary to strengthen communication and coordination with other countries’ associations, effectively allocate resources on a global scale, and collaborate with various countries.
- Second, it is necessary to strengthen communication and coordination with other countries’ associations, effectively allocate resources on a global scale, and collaborate with various countries.
- Third, countries all over the world should strengthen the unification of standards and certification of anti-pandemic products, and mutual recognition in emergency, reduce non-tariff barriers to trade, and facilitate the cross-border transaction of these products.
Dave Rousse: There are many lessons to be learned from this experience, some at the federal policy-making level and some at company operating levels. From a federal policy-making level, we have exposed the risks of having supply chains extending to Asia on products critical to the safety of our citizens. While this is the likely outcome of the free-market system and the need to drive costs down on key products, there are some products where the risk premium in price is worth it.
We need to relearn that when it comes to facemasks and medical gowns, paying a little more for assuredness of supply (and quality) may need to be mandated to get above the private sector profit motives. This was done for military apparel with the Berry Amendment mandating U.S. sourcing of the material, thread, and manufacture of U.S. military apparel. Something like that may be needed for essential medical/surgical PPE. Incenting investment in the PPE precursors may also be needed.
Monolithic meltblown capacity (i.e., not the “M” in SMS) in the U.S. could be incented through the Defense Production Act, and demand steadied by a National Stockpile with rotating stock. These, among other options, will likely be looked at.
We need to relearn that when it comes to facemasks and medical gowns, paying a little more for assuredness of supply (and quality) may need to be mandated to get above the private sector profit motives.
Regarding private sector practices, cost reduction strategies have reduced the maintenance of second sourcing of some key materials. Again, a “premium” may be worth paying to assure supply when one key supplier gets disrupted, as the Taiwanese N95 respirator/facemask supply chain has been.
We do hope that there will be valuable learnings and reassessments coming out of the COVID-19 pandemic.