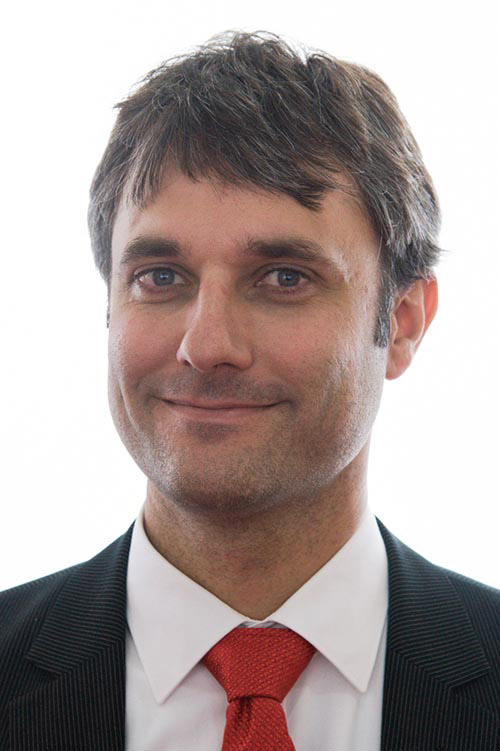
Applications, fiber quality and stabilization determine the quality of nonwovens. The Oerlikon Manmade Fibers segment, a proven expert in polymer processing, spinning and texturing, also beneficially deploys its many years of expertise for its nonwovens (airlaid, meltblown and spunbond) and staple fiber technology.
The group’s Neumünster, Germany-based nonwoven business unit is therefore able to offer solutions for processes and systems for manufacturing high-end spunbond and fibers for carded nonwovens.
International Fiber Journal had the opportunity to talk to Dr. Ingo Mählmann, Vice President Sales and Marketing for the nonwoven business unit at the Oerlikon Manmade Fibers segment.
Dr. Mählmann, the demand for nonwovens has been rising since 2002. What is the reason for this ongoing growth?
Huge infrastructure programs, particularly in China and India as well as in other emerging countries, are being implemented, for which large volumes of geotextiles are required. This has led to a 6% annual growth with regards to the use of nonwovens in geotextiles.
Besides that, many manufacturers are continually developing new and innovative applications, in which nonwovens such as geotextiles are often replacing classical materials.
Why are classical materials being replaced by nonwovens and where can they be used?
Classical materials are being replaced by nonwovens because they are much more versatile. Nonwovens can be combined with other structures such as bubble films, geomembranes and geogrids to create so-called geosynthetics. These can be used as composites, fulfilling several functions at the same time.
Nonwovens are already being used to provide various functions in penetration protection, drainage, reinforcement and separation.
Once installed they are used to help secure dams and disposal sites, but also increase the load-bearing capacity of the substrate in road, path and railroad construction, without even being visible.
Geo-nonwovens provide various functions, but what is the special property of these diverse textile fabrics?
One special property is that geo-nonwovens are voluminous and can very easily absorb tension. This, for example, can considerably reduce the required mineral substructure in road construction.
The tenacity of nonwovens is one of the most important things in such industrial applications. They need to be very extensible and also extremely tear-resistant.
Nonwovens should behave isotropically, meaning that they show similar characteristics in the longitudinal and transversal direction.
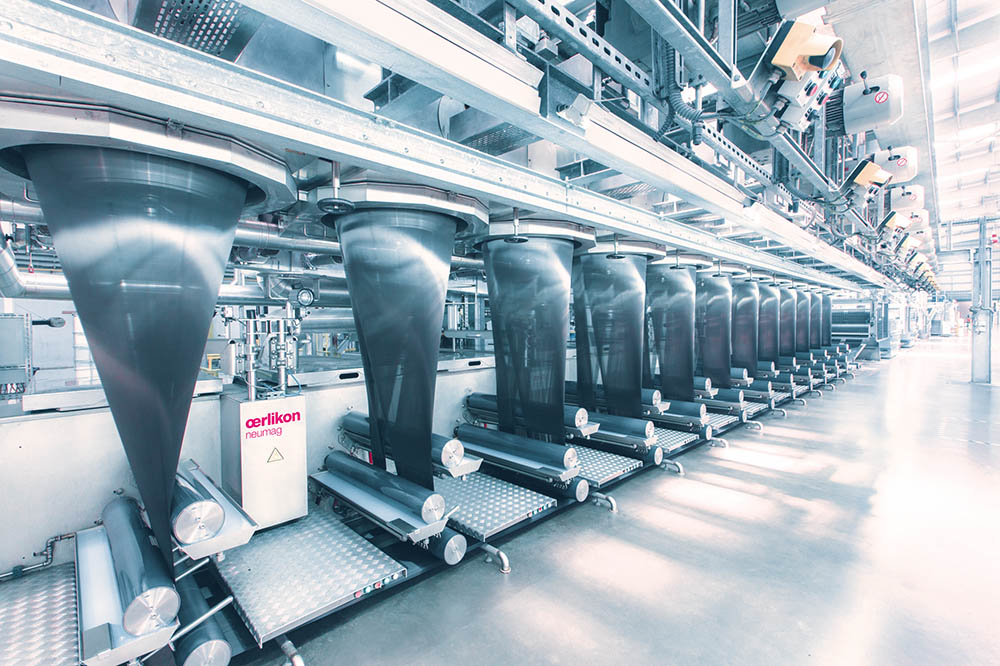
How do you achieve the greatest possible product and which materials are used to produce this?
The polymer raw materials we use to achieve the greatest possible mechanical robustness and durability are either polypropylene (PP) or polyester. As PP is long-lasting and its chemical resistance and hydrolysis are more advantageous than those of polyester, it is used for products that remain in the ground for more than 50 years while still being able to provide a load-bearing function.
On the contrary, polyester is cheaper and more suitable for solutions requiring shorter lifetime tenacity in the ground. It is used if the geo-nonwovens are installed closer to the ground surface and are exposed to solar ultraviolet (UV) radiation over long periods of time since its UV resistance is superior to that of PP.
Where does the Oerlikon Manmade Fibers segment come into play regarding nonwovens?
A decisive determinant of the quality of nonwovens is the targeted transformation of the polymers into fibers and filaments with the application-appropriate properties – and we have decades of experience with these systems.
Today more than 4.3 million tons of fibers per year are manufactured across the globe using systems from our company. And we are growing this figure!
Is it possible for you to use your expertise in another field?
Our spinning expertise has successfully been transferred to spunbond technology. For this purpose we have progressive technologies both for the manufacture of geotextile spunbonds and to produce fibers for geotextile carded nonwovens.
What is special about the carded nonwovens solution of Oerlikon?
Carded nonwovens are made from staple fibers, whereby the card web is generally doubled and flattened using a crosslapper before it is needled.
Geo-nonwovens are composed of staple fibers that can be manufactured on single-stage staple fiber systems, where the spinning and subsequent drawing of the staple fibers are carried out in an in-line process; these systems can produce 40–80 tons a day.
Although our extruder technology permits fibers that are spun-dyed and/or include additives such as a UV stabilizer to cater to the corresponding target applications, most fibers are manufactured in white.
Our solution provides the highest quality along with total reliability, and offer superlative flexibility in terms of raw materials such as PP, polyester, recycled polyester and polycaprolactam. Fiber quality requirements are very high, which is why the flexibility of our systems is essential.

comparison and product setting opportunities
Critical fiber characteristics for geotextiles include high tenacities with simultaneously high elongation in terms of controllable nonwoven quality, carding and needling machines. What needs to be taken into consideration regarding further processing?
To ensure reliable further processing of geotextiles, an excellent, even spin-finish application and the crimping of the fibers is required. The opening of the fibers in the carding system is faster and more even the better the crimping and the spin-finish application are.
The production of geo-nonwovens generally involves the use of fibers with a so-called two-dimensional crimp in which the shape of the crimp is in two directions. As our Oerlikon Neumag Baltic Crimper ensures homogenous crimping and enables good opening of the fibers, it is well suited to this task.
Spunbonds and geotextile applications are on the rise in many industrial nonwovens applications. What benefits do they have compared with classical carded nonwovens?
The market is increasingly demanding more efficient processes and products, which means the product requirements are often the same or greater, but with a lower raw material input. Spunbonds are progressively replacing classical carded nonwovens due to their technical and commercial benefits.
Particularly in the case of polyester, the current generation of our spunbond systems has been able to achieve excellent nonwoven tenacities with low raw material input. Moreover, the energy consumption has been reduced by 20–30% compared with the predecessor generation.
Higher nonwoven tenacities can be achieved at comparable base weights, as shown by general benchmark comparisons with standard products in Europe. On the contrary, the required tenacities can be achieved with the reduction of base weights and therefore with lower raw material input, which alone allows raw material savings of more than 5%.
Why is Oerlikon’s business unit nonwoven the ideal partner for manufacturers?
Oerlikon offers the entire process for manufacturing needled spunbonds for geotextiles, starting with the polymer granulate all the way through to the rolled product.
Efficiency and productivity are combined in the single-phase spunbond technology. This offers a potential reduction of production costs of up to 20% with low wastage and maximum nonwoven quality compared with conventional spunbond processes. Depending on the product type and nonwoven weight, the production capacities can range from 800–1,500 kg/h.
Our unique spunbond technology enables high spinning speeds, which are essential when producing high-tenacity filaments. Polyester filaments that have very low shrinkage and are extremely strong can be manufactured on an Oerlikon machine. The spunbonds are traversal-drawn directly in-line following the needling to set the isotropy.
An outstanding price-performance ratio and excellent properties distinguish end-products from our solutions such as geo-nonwovens.
Thank you very much.