From Robotics to Sensors to AI – and even into Space – Industry 4.0 is Positioned for a New Era
Manufacturing is in a period of hyperautomation whereby smart technologies that range from artificial intelligence (AI) to machine learning (ML), robotic process automation (RPA) and low-code/no-code (LCNC) platforms are being brought together to automate as many processes as possible on multiple levels. The global hyperautomation market size was valued at $1.39 billion USD in 2021 with this expected to expand at a compound annual growth rate (CAGR) of 16.5% from 2022 to 2030 according to a report by Grand View Research. In this feature we consider what this can offer the textile industry, asking what it means for environmental impacts, for workers, and concluding with a look to the next generation of manufacturing that is scheduled to take place in space.
Sewing Up Efficiency
Hyperautomation offers the possibility for a fully integrated manufacturing process that includes a wide range of technologies such as RPA, AI, ML and LCNC, that have the potential to deliver efficiencies in time and production. This is already leading to changes in business and working practices with 56% of organizations already implementing at least four hyperautomation initiatives according to Gartner research. The textile and textile product industries are recognizing the advantages that it can offer.
Sewing has often proved a bottleneck in the automation process because of the need for manual steps operated by people. Automatex have now developed a sewing and assembly system that looks to eliminate many of the manual aspects reducing the stop-start between the human and machine that cost time during manufacture. In the production of consumer bags for example, the Automatex system allows the cutting, hemming, handle attachment, labelling, gusset, and bag forming to be automated producing around 540 bags per hour. Eton Systems specializes in material handling systems across a broad range of needs including dashboards for the automotive industry, upholstery, apparel and home textiles that use quilting machinery. The Swedish chair manufacturer, Flokk use the Eton System to achieve time and cost efficiencies bringing together the seat assembly, with sewing and assembly taking place in one factory rather than two. This has resulted in a productivity increase of 25%, with order to delivery time down from four days to three. Work injuries and related ailments caused by repetitive movement have also been significantly reduced with Flokk estimating that their return on investment (ROI) to be around 18 months.
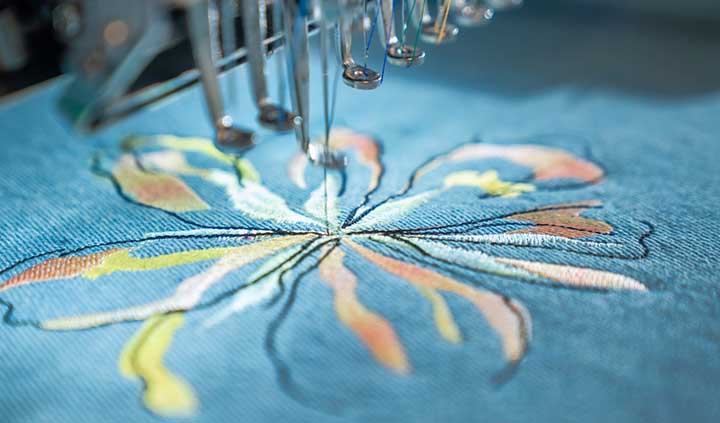
Real-Time Quality Control
While the first wave of the Industrial Internet of Things (IIoT), Industry 4.0, concentrated on the manufacturing and assembly processes, the focus is now extending to include areas such as Real-Time Quality Management (RTQM). The benefit of including quality control during rather than post-production is multiple as it extends from reducing spoiled stock and waste to reputational damage and loss of customers.
Advanced sensing technology is a contributing factor to new developments such the Instrumar Fiber System that uses electromagnetic sensors capable of detecting a wide range of fiber defects such as node count, spin finish fluctuations, variable denier, filament migrations, and fluffs or “slubs.” Importantly the software can suggest underlying causes of a problem in real time allowing workers to resolve the issue in a timely way. Instrumar report a customer claims reduction of 95% by manufacturers using their system, in some cases it has led to a 5-10% increase the company’s top-grade fiber.
Yarn and Energy
Yarn production accounts for as much as 8% of the fashion industry’s global greenhouse gas emissions according to a McKinsey’s “Fashion on Climate” report (2020). The fiber and yarn spinning manufacturer Rieter estimates that spinning machines consume 60-80% of the energy needed for yarn production. This has brought them to focus on energy efficiencies in the development of new machine technologies such as ring spinning and compact-spinning machines for producing fine quality yarn, also air-jet spinning machines that require the use of both electrical and compressed air energy, with the rotor spinning machine being the most energy efficient.
Rieter is measuring their progress in this respect, with the air-jet spinning process seeing an energy reduction of 69% since 2008, while ring spinning of viscose yarn is showing a decrease in energy needs of 37% since 2000, and rotor spinning 54% for the same yarn and time period.
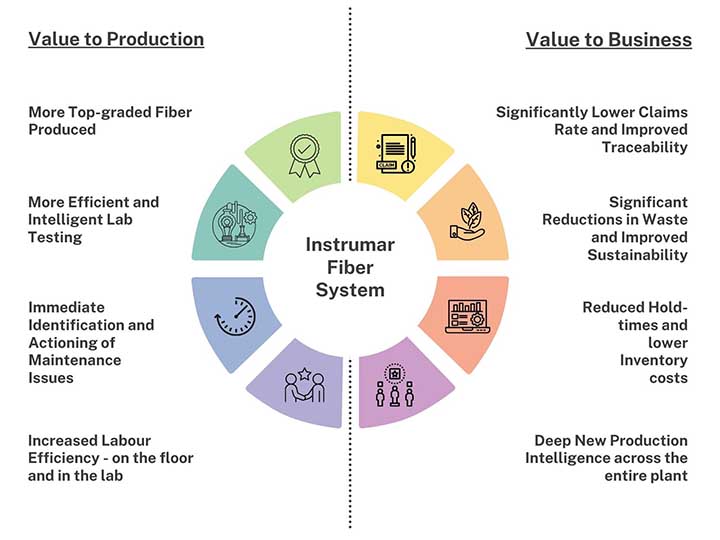
Real-Time Quality Control
Robotics have long been valued for the productivity, speed and efficiencies that they bring. The natural extension of this is to help manufacturers reduce their environmental impact. Based in the Czech Republic, Compo Tech PLUS, spol. sr.o are specialists in manufacturing technology for the fiber composite industry, producing advances such as fiber winding and filament placement machines. They have developed an Integrated Loop Technology (ILT), for automated fiber placement, such as “Pitch” and PAN fibers, that eliminates the need for drilling and fixings.
The accuracy of the fiber placement for a typical carbon fiber epoxy beam is estimated to be 10-15% higher stiffness in the axial direction and offers as much as 50% improved bending strength compared with traditional filament winding. The company’s winding machines include an integrated FANUC M-20iA/20M-R-30iB 6-axis robot arm and remote controller unit as well as software developed in-house for fiber placement and winding. The accuracy achieved minimizes waste fiber achieving both an environmental and economic benefit.
Controlling Thread Waste
Coloreel addresses the issue of waste embroidery thread as well as dye in their innovative technology that colors the polyester thread as it stitches using a CMYK ink system. The technology reduces wastewater by 97% and also utilizes recycled thread. The Swedish company has advanced their technology to allow it to be used on multi-thread embroidery machines that makes more complex designs a possibility. The latest software enhancements make it possible to use special effects such as frosted, metallic and neon colors, these were previously quite limited.
It is also possible to combine Coloreel thread with other threads. This “mix and match” facility make it possible for users to use less expensive thread, such as for block color areas of the design. The company has joined forces with fashion brand H&M to bring customized manufacturing to the consumer at high street prices. The pilot scheme has been introduced in the H&M Alexa store in Berlin, where customers can select from a library of designs. In the initial phase it can be used on store-purchased products, with the intention of extending this to customer’s own garments eventually.
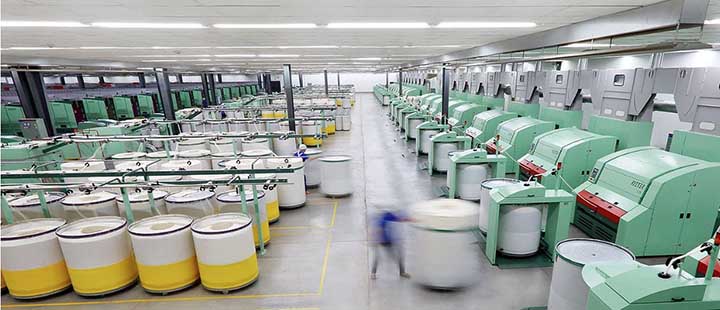
Workforce Integration
The North American market dominated the global hyperautomation industry, with 34.2% of the market share in 2021 according to Grand View Research. In theory this is a positive for highly skilled jobs, the sort that attracts and retains a strong workforce. However, looking at the future of work, the World Economic Forum (WEF) accuse schools and universities globally of failing to evolve to meet the skills demand needed for these jobs.
The WEF point to U.S. states with tax credits for apprenticeships as being where the apprenticeship uptake is highest, but the global view is not positive with 47% of workers receiving no workplace training in the past five years despite the pace of digital acceleration. This matters for many reasons including talent attraction and retention as research from McKinsey reports a staggering 41% of workers worldwide that cite lack of opportunity for advancement as the primary reason for leaving their jobs.
The Harvard Business School and the Burning Glass Institute have undertaken a study on “Managing the future of work.” Amongst their findings, they point to the significant role of individual companies in determining whether low-income workers can escape poverty through enabling opportunity and mobility in their corporate practices. Their employee survey of Fortune 500 workers reported 84% of employees stating that they would be more likely to remain with their current company if they felt that they had opportunity for advancement.
Human-Machine Collaboration
The composites industry recognizes that human and machine working together can offer the advantages and efficiencies of both. In Europe, the EU Horizon 2020-funded DrapeBot with partners from Italy, Germany, Denmark and Austria combines a high level of automation with a skilled workforce in the manufacture of Carbon Fiber Reinforced Polymer (CFRP) composites for aerospace. The issue found with full automation was the high investment needed and reduced flexibility.
DrapeBot looks to address the need for automation efficiencies with the desire to nurture a highly-skilled workforce, both essential for the future of the industry. Drape is needed for around 30% of carbon fiber laid into molds. Accuracy in fiber placement and orientation, as well as avoiding wrinkles are key challenges. In the DrapeBot project, the robot’s role is focused on the transportation of large pieces of the carbon fiber material and draping it into the low curvature areas of the mold using a gripper system, low-level control structures with AI-driven human perception and task planning. The human concentrates on the areas of high curvature in the mold. The project has undergone a complete draping process showing all interaction possibilities from robot-only to fully collaborative draping and is now due for completion in December 2024.
Final Frontier
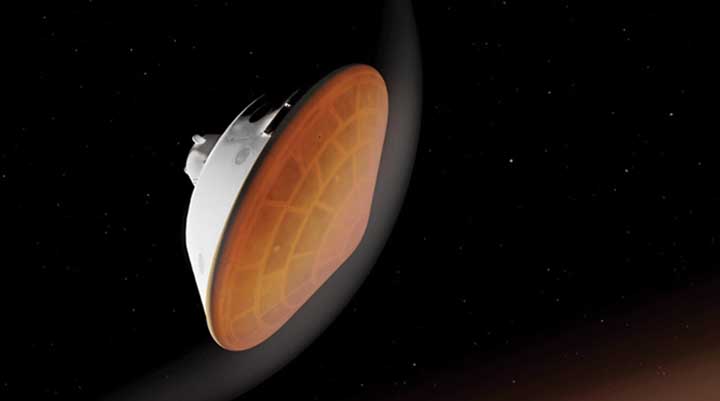
Space is destined to be the next frontier for manufacturing with the in-space manufacturing market predicted to the worth around $4.6 billion by 2030, going on to reach $62.8 billion by 2040 at a CAGR of 29.7% during the forecast period according to a report from Markets and Markets. Enabling technologies include 3D printing, bioprinting, space robotics directed at automation and assembly. The focus is on miniaturization of hardware as well as low resource manufacturing.
Deloitte Insights’ “Riding the exponential growth in space” (2023) point to six significant areas for disruptive growth in space: space data-as-a-service, in-space manufacturing, additive manufacturing, robotics, sustainability, and national security. The report points to manufacturing for in-space applications as well as terrestrial.
The microgravity offers challenges but its unique environment eliminating the forces of sedimentation, convection and vibration can also allow for the study of processes that cannot be manufactured on Earth.
In January 2024, the United States Space Force (USSF) in partnership with the Air Force Research Laboratory selected two institutions under the Space Strategy Technology Institute (SSTI 2) to facilitate applied research to include in-Space Operations, that includes space access, mobility and logistics (SAML).
The University of Cincinnati and Texas A&M University (TAMU) form the lead institutions and receive combined funding of $49.9 million. Focus areas will include research into robotic servicing and associated modelling and simulation, developing testbeds, also CubeSat berthing and refuelling technologies and large-scale in space assembly. In-space manufacturing was included as a recommendation in the U.S. Government’s National Strategy for Advanced Manufacturing under Goal 1aimed at the developing and implementing advanced manufacturing tech:
- 1.4.4. In-Space Manufacturing: Develop new additive manufacturing processes in microgravity environments to create replacement parts and space infrastructure. Enable integration of robotics with in -space additive manufacturing processes for deep space exploration. Prioritize biomanufacturing investments in microgravity to enable extended space presence including sustainable food production, processing, and recycling, and the deactivation of hazardous materials.
Advanced Manufacturing Strategy
The initiative will involve industry partners such as Aegis Aerospace Inc., who anticipate supporting the institute and TAMU in a number of ways including technology development projects, student internships and in-space technology testing using its Space Testing as a Service (STaaS)* platforms located on the International Space Station and lunar surface.
Orbital Composites have received a Direct-to-Phase-II SBIR contract from the United States Air Force (USAF) to develop a carbon-carbon (C/C) composite manufacturing. The technology uses Orbital’s 3D printing process to significantly reduce cycle times so that C/C parts could be ready in weeks versus months conventionally. Applications are anticipated in defense, aerospace, aviation and energy in applications where temperature extremes can demand novel solutions that would be more expensive to produce on earth.
“Orbital is building a factory that is redefining the possibilities of the future of aerospace and energy,” according to CTO and founder Cole Nielson, “Our work on C/C and other ceramic matrix composites will enable global scale hypersonic transportation of cargo and people.” The process is expected to allow for very complex and exotic shapes, optimizing thermal management, fluid dynamics and other high-performance characteristics to be produced that would not be possible, or be prohibitively expensive using conventional manufacturing techniques.
The common factor in the current wave of manufacturing developments is the move to ensure benefits to manufacturing, environment and workers, proving that these can, and indeed should always be inclusive.
*StaaS is discussed in more detail in Space & Sportswear, IFJ, January-February, pp. 28 or at https://www.fiberjournal.com/space-sportswear.