Many segments of the textile industry rely on adhesives and binders that securely hold a product together, in one way or another. From automotive, medical, hygiene and more, this seemingly invisible technology contributes to the critical success of products that are used by consumers daily. Adhesive and binding solutions are undergoing their own epiphany in the research and development to support the advancement of the products that utilize them, and industry wrestles with sustainability, durability and circularity.
IFJ highlights several companies who share their most recent news in our first edition of the IFJ Adhesives and Binding Roundup.
Diaper closures, which some consider as the humblest of diaper components, play a critical role in the design of disposable diapers and incontinence products. From newborn infants to adults, the closure system enables the liquid and solid management wizardry of a modern absorbent product to stay where it belongs and do what it is intended to do. To explore what the future “holds” for the diaper closure system, it is necessary to first consider the interesting co-evolution of the fastener with the diaper design itself.
As a starting point for this historical review, let us consider the classic cloth diaper. Properly folded and applied, a length of cotton material was secured using what was most commonly available, (i.e., simple shawl and coat pins). As clothing pins were not necessarily designed for such hygiene-inspired applications, there was the ever-present risk of an inadvertent pin stick or for the pin itself to disengage during use. The advent of “safety” pins in the mid to late 1840s, such as the specific diaper pin of Thomas Woodward in 1842 (notably, seven years before the Hunt and Rowley safety pins that we are familiar with today) was one of the first to improve the user experience while affording a unique performance advantage in fitting diapers. The advantage in performance came in allowing the diaper to be adjusted to the anatomical variances of the user by the simple placement of the safety pins. This approach to diaper closures was accepted practice for both the “Baby Boomer” and much of the “Gen X” generations.
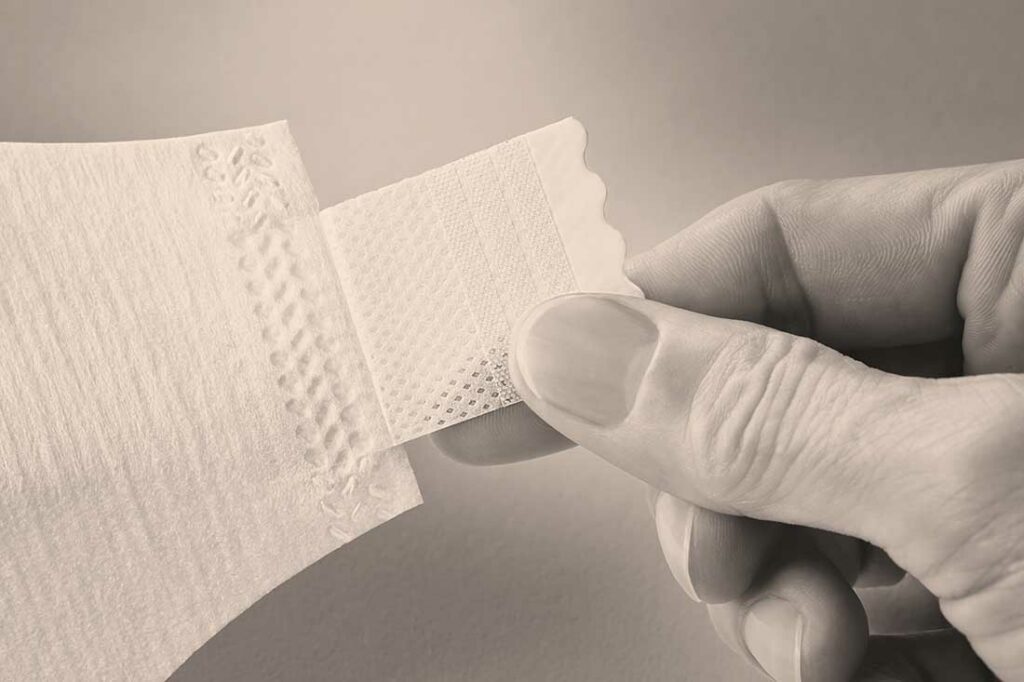
The next historical landmark was the market migration to early reusable diaper hygiene chassis with disposable absorbent components of the late 1930s, followed by the antecedents of modern disposable diapers in the 1950s. Here, we see the market acceptance for integrated closure systems becoming more prevalent. Whether the closure system was defined as tying together lengths of fabric, such as that of the Wilson patent from 1939, or the use of specialized macro-scale fasteners as described by Horowitz and Laser, we see a new trend occurring: defined horizontal closure placement on the belt line (across the waist) of the diaper.
Two notable advancements in belt line closures of that time remain with us today – the use of adhesive-tape fasteners (e.g., Miller) and hook-and-loop fasteners (e.g., Brooks et al.). Both types of fasteners allowed for easier integration of closures in the waist band while also supporting consumer interest in aesthetic appeal. These types of fasteners also introduced the need for dedicated counterparts (or landing zones) to achieve reliable closure and resistance to inadvertent opening. Hook-type structures require a durable loop fabric counterpart whereas adhesive tapes use a counterpart contact patch that is typically smooth and essentially fiber-free.
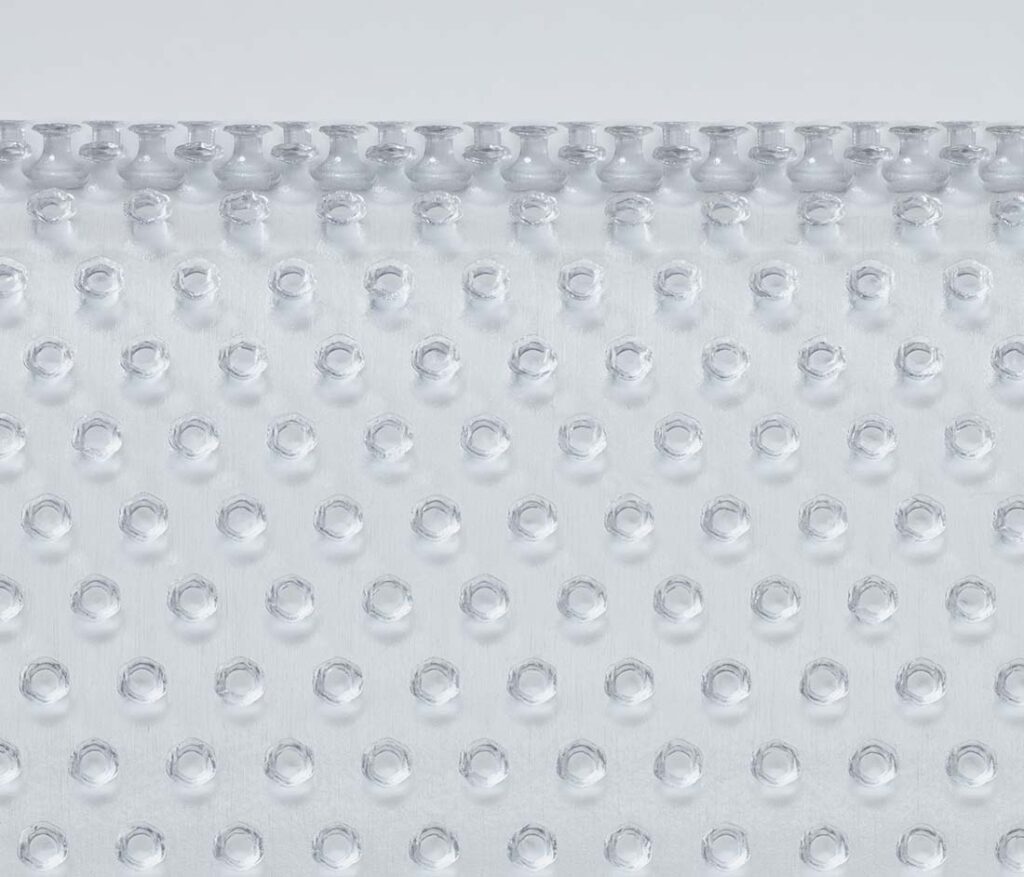
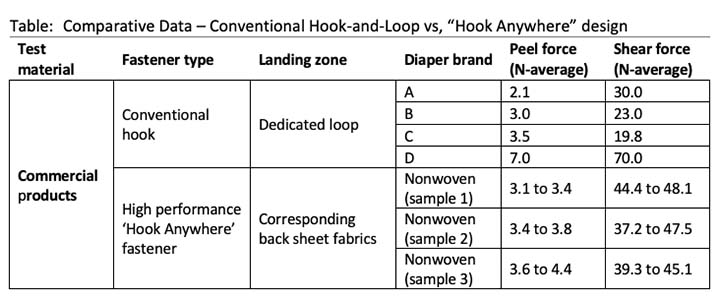
With the introduction of integrated closures in the disposable diaper, the issues of convenience in fastening improved, although another issue arose: how to achieve good fit and function of the diaper. This is a classic example of diaper closures affecting diaper function. With the belt line now taken care of and different diaper sizes becoming available to best manage different waist dimensions, the next issue to consider was the variance in the thigh dimensions of target users. Early approaches for improved fitment around the thigh involved manual adjustment of the “leg hole” by application of secondary fasteners, such as those found in the patent of Schaar. Whereas such adjustments improved the fit of the disposable diaper, it did require initial manual adjustment as well as proper retention of that adjustment during the use of the diaper. Alternative technologies came to the forefront that overcame such manual fitting steps, specifically though inclusion of elasticated fabrics, bands and filaments creating defined “leg cuff” structures. Looking at patents such as those of Buell and other related efforts of that time, we see a rapid adoption of, and improvement upon, the functionality of the leg cuff.
It is interesting to note that across the patents cited in this article, phrases such as “comfortable fit,” “easy adjustment” and “inexpensive construction” remain just as relevant today as they were at the time. To innovate in new directions, we can look to the past in view of the current status quo and focus on a compelling question: “Can the industry produce a product/closure fixture that ensures flexibility and enhanced fit while reducing the environmental impact and conserving resources?”
Our industry can benefit from a “back-to-basics” approach with an eye towards challenging our preconceptions of performance in the modern baby diaper. Landing zone structures require more manufacturing steps, logistical management, levels of resource consumption (both in fabrication and shipping) and waste/quality control requirements. Why is a landing zone still required in the modern baby diaper closure system? Incontinence management manufacturers have explored ways of using a “hook on backsheet” approach to enhance the fit on an adult.

Whereas incontinence products are intentionally produced using far more robust fabrics to account for stresses resulting from an active user, baby diapers have not developed in a comparable way. Baby diapers show the side effects of applied downgauging/lighter weight materials, particularly in the nonwoven fabric layers of the diaper, as part of continuous cost reduction. For example, we now have back sheet structures that have spunbond facing layers of 15 gsm or less. With such low basis weights, the diaper chassis has limited structure for a fastener to engage and still achieve reliable closure performance.
To address the above scenario, Gottlieb Binder has combined new perspectives with fresh knowledge to introduce a new solution to a historical challenge in diaper performance. Drawing on years of conventional hook and loop experience in hygiene applications, together with knowledge of how to specifically alter the performance of micro-scale structures, a series of new hook-type fasteners are now available in both conventional and bio-sourced/biodegradable technologies. This series of fasteners incorporates uniquely formed engagement elements that embody the attributes of flexibility and durability to allow enhanced “grab and hold” behavior with typical spun-melt fabrics. Continuing the evolution of these “Hook Anywhere” designs allow for high shear force performance to keep the closure closed under load, yet provides an opening/repositioning force without creating undo stresses on the back sheet’s fibre/filaments. As the adjoining table shows, peel and shear strengths are achieved without the need for a defined landing zone, simplifying diaper designs and production.
The “Hook Anywhere” fastener from Binder offers a new direction in diaper closures. Achieving fit and functional performance – which is and always has been a challenge and core focus of diaper designers throughout the years – is now possible using a fixture system that engages anywhere on the diaper. The product’s flexibility and its optional bio-based content will be a catalyst for each link of the supply chain. Such an evolution of the humble closure should be just one contribution towards products that are truly “ready for the future.”
Visit Gottlieb Binder at https://www.binder.de.