Driving Forces of Flexible Hybrid Electronics
The global smart textile market estimated to be worth $2.82 billion in 2022 and projected to rise to $17.94 billion by 2031, showing a growth rate of 22.8% CAGR over the forecast period according to a report by Straits Research. Fibers in this field have two related but distinct forms. The first are fibers that act as a substrate for printed electronics, the second are e-fibers and yarns, where the fiber is itself or as part of a hybrid yarn conductive or sensing. In this column we concentrate on the first group [returning to e-fibers in a later column], and specifically examining the role of fibers in Flexible Hybrid Electronics (FHE) for the transport market.
The term Flexible Hybrid Electronics is used to refer to materials that are hybrid in nature, with the characteristics of having electronic capabilities while being flexible and/or conformable and/or stretchable. Discussions for this column with key figures from the FHE and printed electronics industry, points to strong potential for fiber producers. Barriers to market development for the transport sector center on cost and reliability. Reliability not a reflection on fibers themselves, but in doing something new in electronics. Much of the performance evaluation needed to being FHEs to market is use-case dependent because of the emerging and the unique nature of many of the applications in the transport market. This in turn requires specially designed tests and protocols all of which comes at a cost. In terms of market opportunity, the FHE market size was estimated at $128 million in 2021 and expected to reach $342 million by 2030 with a CAGR of 11.54% according to Precedence Research.
Until now much of the substrates for printed electronics have been plastic. However, market trends, transport in particular, is starting to see a shift in focus to fiber as an alternative substrate. One reason for this is the increasing use of composites in transport with weight and energy proving important considerations for cost, environmental and consumer reasons. Polyester is common in composites, with carbon fiber also used for its good strength to weight ratio. However natural fibers such as flax and hemp are starting to be used in applications where a lower level of strength is needed such as glove compartment doors. For FHE it is the carbon fiber or alternatively, a polyester reinforced composite that is of most interest at present. Strength and durability are one reason, but the smooth fiber surface is another factor. FHE applications in the vehicle center on the communication of data and information so that lighting or displays are often needed.
While synthetics are most commonly used at present, it is technically possible to use natural fibers as the basis for a material substrate for flexible printed electronics.
PolyIC GmbH & Co KG have been bringing composites, including carbon fiber, together with printed electronics adding sensors, lighting and decorative elements. These are suited for use as Human Machine Interface (HMI) interface panels in the transport sector. The HMI instrument panel comes with an integrated LCD Touch Screen and PolyTC sensors to create a smart panel with a durable surface and backlighting to allow for day-night visuals. Decorative elements ware applied to a carbon fiber prepeg that doubles as a substrate for the printed electronics using the company’s In-Mould Decoration process. The sensors for the multi-touch panel are added using an In-Mold Labelling process, all taking place in a single step. The proximity sensors in the instrument panel have been laminated in place. The sensors for the light and color-regulating touch controls are integrated with a Functional Foil Bonding (FFB) process.
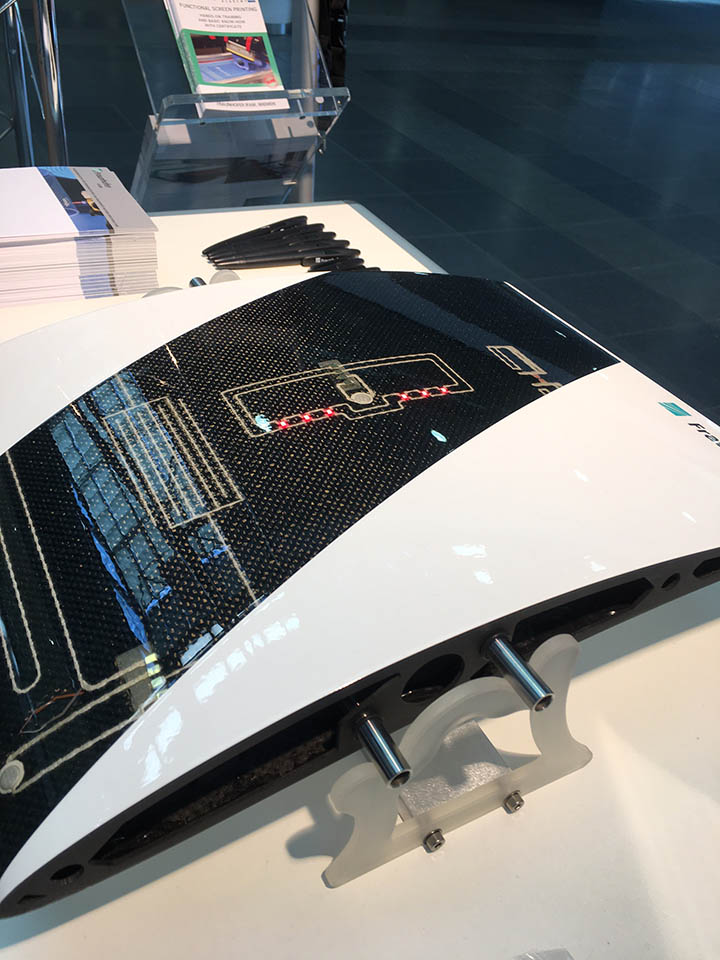
The driver or pilot are not always seated in the same area as the sensing technology. At LOPEC 2023, the annual printed electronics conference and trade show in Munich, Fraunhofer IFAM showcased a smart aircraft FHE composite. The core material is a functionally integrated carbon fiber reinforced plastic (FRP). Printed onto the surface are an array of temperature and capacitive sensors with heating, UHF antenna and LEDs integrated onto the fabric layer structure. The electronics need to be protected so that a layer of insulation is placed between the carbon fiber, the ink and the LEDs, these are then covered with a protective resin before the structure is then formed in its 3D mould. The result is a complex and sophisticated composite that marries sensing capability with the physical performance requirements of the aircraft wing.
In terms of fiber use, while synthetics are most commonly used at present, it is technically possible to use natural fibers as the basis for a material substrate for flexible printed electronics. The structure of textiles gives them flexibility, stretch and formability the degree depending on the fiber selection. Fibers, because of their porous nature, can be challenging to work for FHE. New manufacturing technologies such as mass component transfer using laser or stamping techniques, as well as 3D printing are set to usher in a new era of stretchable electronics, while the utilisation of platforms such as hydrogels will enable flexible, formable and stretchable devices not previously possible. The growth in electric cars, as well as the market for land and airborne autonomous vehicles will all contribute to the demand for FHE, driving innovation and growth. The predicted FHE market value of $342 million by 2030 may prove to be conservative.