Textiles Ensure Safety, Performance, Comfort and Reliability in Transportation
Transportation, which includes the automotive, aerospace, railways and marine sectors, represents one of the largest markets for technical textiles, with fibers used in significant volumes for a wide range of end uses.
Fabrics for transport are subjected to a range of environmental conditions, including abrasion and fluctuating temperatures, while developments have been geared towards improving durability, weather resistance and safety.
Automotive Applications
In the automotive industry, textiles are used in such applications as seat upholstery, headliners, floorcoverings, seatbelts, airbags, tire cord, headliners, insulation and filtration. Modern passenger vehicles currently use an average of 30-35 kg of yarn in various applications that are especially focused on comfort and safety.
Most forecasters estimate the global automotive textiles market to be worth in excess of US$40 billion by 2030 with a compound annual growth rate of 4%.
Many producers are now designing automotive interior materials that meet the 2030 end-of-life vehicle requirements and the ambitions of original equipment manufacturers (OEMs) with regard to
circular economy targets.
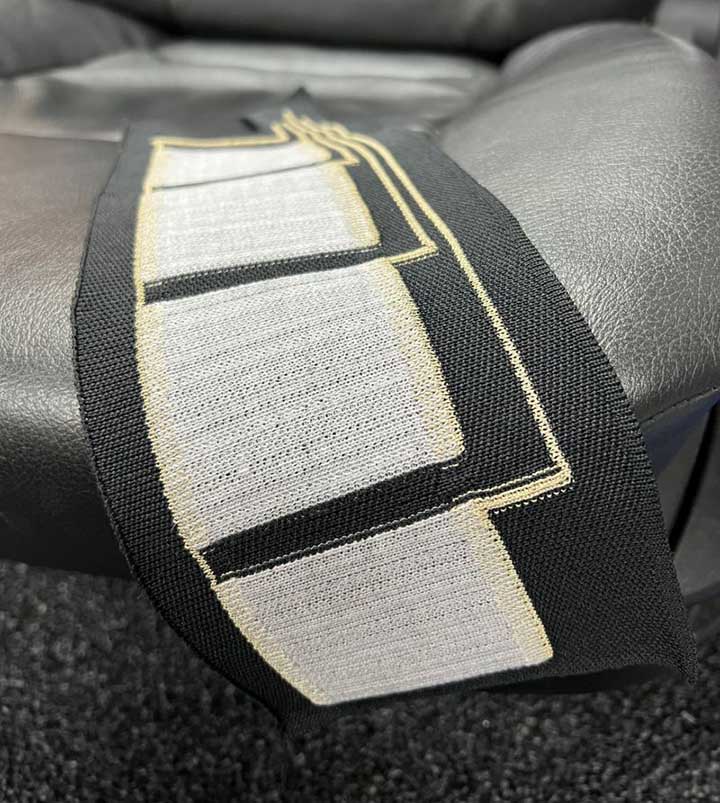
Most carmakers are now emphasizing the integration of “eco-friendly” materials in their latest models, where recycled fabrics and sustainably treated leather are increasingly featuring in seat upholstery, interior trim, and door panels.
Customization and Personalization
At the same time, consumer demand for customized and personalized vehicle interiors continues to grow, driven by preferences for individualization and self-expression. Fabric manufacturers are beginning to offer customizable fabric options in a range of colors, textures, patterns and finishes, catering to diverse consumer tastes and preferences.
According to a recent report from market research company The Brainy Insights, integrating smart technologies into vehicle interiors presents an opportunity for automotive fabric manufacturers, where fabrics embedded with sensors, heating elements, lighting systems and interactive displays can offer enhanced functionality, comfort, and convenience for passengers.
In addition, the incorporation of temperature regulation, moisture management and antimicrobial properties into automotive fabrics can be used to enhance passenger comfort and well-being during travel.
At the same time, momentum is growing amongst automotive OEMs and Tier 1 suppliers for the development of products that, from the initial design phase, consider eco-design, for example, by constructing mono-polymer carpets and flooring that are 100% recyclable at end of life.
For example, Autoneum has introduced an automotive tufted carpet made of 100% polyester that is fully recyclable. The floorcovering also has a high content of recycled polyethylene terephthalate (PET), according to the Switzerland-based producer of acoustic and thermal insulation systems. The company’s zero-waste and latex-free manufacturing process is claimed to significantly reduce carbon dioxide (CO2) emissions as well as water and energy consumption.
Belgium-based BIG Yarns, part of Beaulieu International Group, expects the automotive carpet market to grow strongly in the coming decade with the increased demand for vehicle customization and personalization driven by owners looking to upgrade and enhance interiors, including the flooring area.
The company notes that a growing awareness around hygiene is also boosting the market as consumers become more conscious of maintaining cleanliness in their vehicles, including the floors. “Automotive carpets provide an effective solution by trapping dirt and preventing it from spreading to other areas,” said BIG Yarns.
Mono-Material Approach
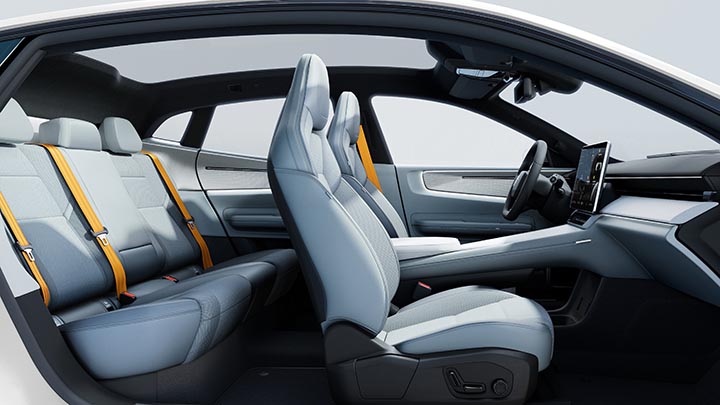
Polestar’s second all-electric model, the Polestar 4, features interior materials that focus on sustainability through a mono-material approach for effective recycling. These include a tailored knitted textile made of 100% recycled PET; bio-attributed MicroTech vinyl, which was introduced in the Polestar 3 and replaces crude oil with pine oil and features a recycled textile backing; and traced leather sourced from Bridge of Weir Leather.
The new Polestar vehicle also features inlay carpets in the interior made from recycled PET, floor carpets made from Econyl that incorporate polyamide fiber from reclaimed fishing nets, and door trim panels made from a natural fiber/polypropylene composite that results in up to 50% less virgin plastic and a weight saving of up to 40%, says the Swedish automotive manufacturer, owned by Volvo.
Airbag Cushions
Yarns used in airbags are mainly made of polyamide, although polyester is increasing in usage. In an effort to reduce the greenhouse (CHG) gas footprint of airbags, Sweden-based automotive safety systems provider Autoliv recently introduced airbag cushions made of 100% recycled polyester.
Tests show that the new material used in these airbag cushions provides equal safety functionality to a standard polyester airbag while reducing GHG emissions by approximately 50% at the polymer level.
Airline Identity
In the aviation industry, textile furnishings for aircraft include seat covers, seatbelts, lifejackets, curtain fabrics, carpets and floorcoverings, wallcoverings, blankets and headrest covers – elements of an aircraft interior that enable an airline to develop and reinforce its corporate identity and offer much greater scope for customization than most other interior products.
According to interior designers, passengers register an airline’s identity within the cabin environment through the stimuli of a number of factors in which textiles have the greatest part to play.
Importantly, all textiles used in aircraft cabins must be flame retardant in air with a normal concentration of oxygen. They should also be wear-resistant, stain-resistant, non-toxic, and as light as possible – the lighter the aircraft, the lower the airline’s fuel consumption and therefore its CO2 emissions.
Seat upholstery must also be comfortable against the skin. Seat covers for aircraft can be made of a wide range of materials, from blended fabrics containing wool, viscose, and synthetic fibers, as well as leather.
A blend of wool and polyamide is an industry standard for seat covers, with wool fibers often accounting for 90-95% of the fabric, which also helps to make the fabric flame retardant. The use of polyester in seat upholstery, meanwhile, is dependent on being combined with fire-blocking materials.
Real leather has a high-quality look, and with ultrathin coatings it is still a popular material for aircraft seat covers. However, recent developments have focused on vegan, fully recyclable leather substitutes made from a wide range of plant-based materials, as well as products such as Alcantara, a luxury microfiber fabric that offers light weight, durability, softness and high-performance properties.
Recyclable Aircraft Dress Cover
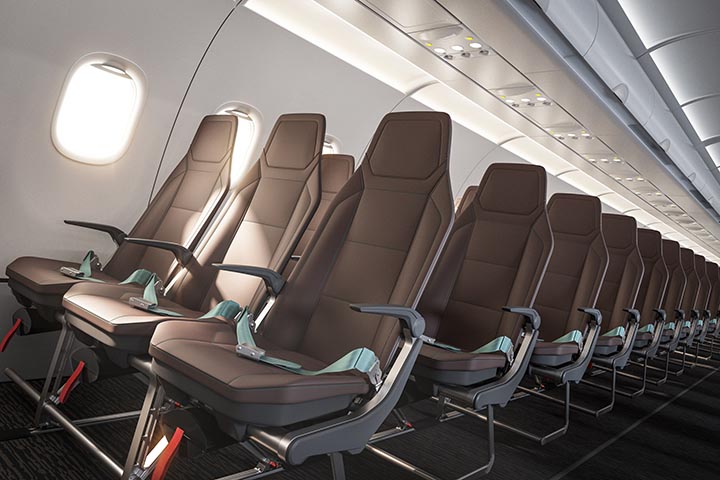
UK-based Generation Phoenix, in partnership with Sabeti Wain Aerospace and Doy Design, has launched what is claimed to be the aviation industry’s first fully recyclable aircraft dress cover.
This is said to represent a closed-loop solution that allows airlines to recycle 100% of their end-of-life seat covers into new seat cover material with the same quality, durability, and certification
requirements.
This fully circular cover is upholstered in Helios, a new material developed by Gen Phoenix, made using recycled end-of-life waste in a closed-loop process, which can be recycled continuously.
According to Gen Phoenix (formerly ELeather), which uses leather offcuts destined for landfill and regenerates them into a premium recycled leather material, current seat covers are traditionally made from a mix of non-recyclable materials that are hard to separate and end up in landfill or incinerated after their typical service life.
Carpets and Seatbelts
For aircraft carpets, European airlines almost always favor products with a high wool content, while U.S. airlines are just as adamant about using polyamide. Meanwhile, seatbelts in aircraft must, of course, have high tensile strength, but must also be resistant to light and acids, have flame-retardant properties and keep their shape.
Outside the Earth’s atmosphere, aerospace textiles include fiber-containing articles for specific functional requirements to work in space suits, space shuttles and spacecraft, such as for future lunar and Mars missions.
Additional Functions
Thomas Stegmaier, sustainability officer and research director for technical textiles at the German Institutes of Textile and Fiber Research (DITF) Denkendorf, Germany, expects further development of textiles for aircraft applications.
“What is going to be really interesting are smart textiles with additional functions,” he said, citing the work currently being done on self-illuminating textiles, which incorporate metal fibers that emit light when electrified. “Upholstering the aircraft cabin ceiling with this kind of fabric would mark a significant reduction in weight. Ultimately, that is what all developments in textile technology are trying to achieve.”
Public Transport
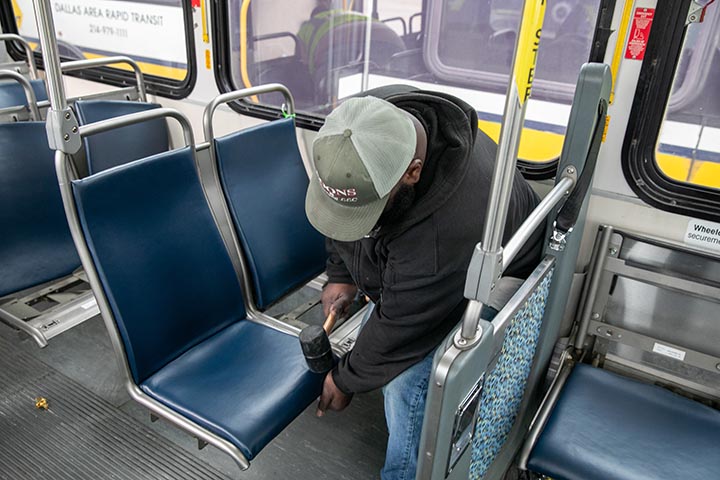
Interior textiles for the railways include tufted carpets, entrance mats and fabrics for seat covers, curtains, wallcoverings, and headrests, while textiles for buses include woven and tufted carpets, entrance mats and fabrics for seat covers, curtains and headrests. Many public transport operators still use durable wool-rich moquette for seat upholstery, including cushions, headrests and armrests, particularly in long-distance vehicles where seat comfort is a key requirement.
However, in the mass transit sector there are an increasing number of metro and subway systems, as well as buses, which are replacing fabric upholstered seats with alternative materials, principally to provide a cleaner and more comfortable environment for passengers.
Recent examples include the Seoul Metro in the South Korean capital, which is replacing its all-fabric upholstered seats with reinforced plastic chairs, and the Dallas Area Rapid Transit (DART) in Dallas, Texas, USA, which is replacing 34,000 fabric seat cushions with new vinyl ones across its bus fleet.
Marine Demands

In the marine sector, textiles are used as fabric for inflatable boats and lifejackets, as well as carpets and fabrics for the complete interior furnishing of cruise liners and yachts, including woven and tufted carpets, hand-tufted and hand-woven carpets as well as stitched carpets.
In this market, the demands placed on textiles are not only high in terms of fire protection, but also with regards to light resistance and durability. This is particularly true for textiles used in outdoor marine applications, which must be extremely robust as they are exposed to moisture and sunlight.
Natural Fibers
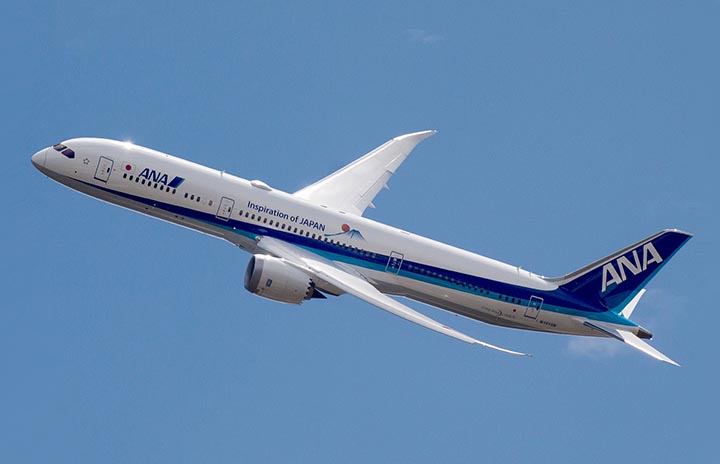
While most textiles and nonwovens used in the transportation sector are made from synthetics such as polyester, polyamide and polypropylene, sustainability and climate change issues have promoted the use of, and interest in, biodegradable and compostable materials.
Biodegradable bast fibers, particularly flax and hemp, are now being used as the reinforcement material to produce sustainable, lightweight biocomposites that help make vehicles, such as cars, trucks and buses, more durable and safer as they will not splinter in a collision. They are increasingly being used in place of petrochemical-based carbon fibers and glass fibers in both structural and non-structural applications such as car bumpers, door linings, package trays, dashboards and trunk parts, where different materials are combined to enhance mechanical strength and durability as well as other important properties, such as impact resistance and scratch resistance, to produce natural fiber composites that are lightweight, renewable and low cost.
These properties are especially important in aviation where, for example, the Boeing 787-9 Dreamliner aircraft – the world’s first major commercial airliner to use composite materials as the primary material in its airframe – uses around 80% carbon fiber reinforced composites and other composites by volume (50% by weight). Owing to their light weight and strength attributes, the use of composites in the primary structure, including the fuselage and wing, has helped to make the Dreamliner 20% more fuel efficient than the comparable aircraft it has replaced. The newer Airbus equivalent aircraft, the A350, also uses carbon fiber composites extensively.
Flax-Based Composites
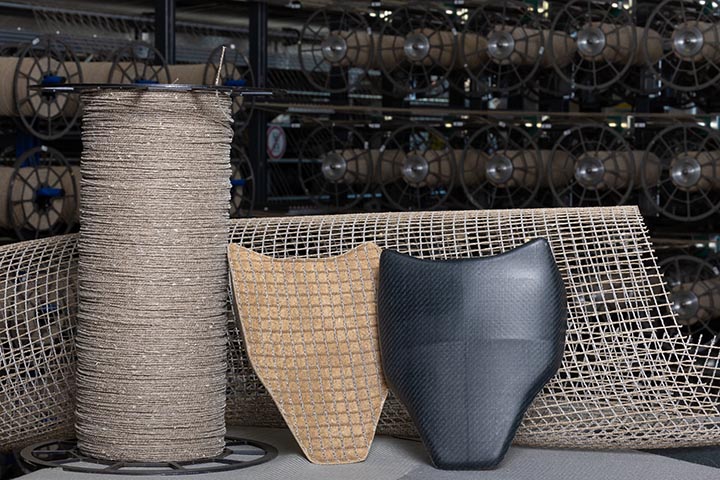
In the automotive industry, the intrinsic properties of flax fibers allow carmakers to combine excellent performance with more sustainable production methods, according to the Paris, France based Alliance for European Flax-Linen & Hemp.
Flax-based composites have similar or sometimes even superior properties compared with traditional composites. Its excellent shock absorption capacities and resistance to breakage make this natural fiber composite a promising element in automotive safety. On the other hand, as flax has a low density it can be used to make lightweight composites, which is crucial in reducing the weight of vehicle batteries.
In the marine industry, the adoption of composite parts based on flax fibers in particular continues to grow, with major OEMs as well as smaller shipyards now aiming to take advantage of the reduced carbon impact and mechanical properties they can provide.
Hydrophilic Properties
However, the main disadvantage for using natural fibers is that they are hydrophilic materials, which when exposed to humidity and moisture over a number of years could lead to swelling and loss of its shape and can also lead to a loss of strength. Current research is looking to develop treatments that make natural materials more compatible with plastics in terms of safety by maintaining the mechanical strength required while minimizing the risk of moisture absorption.
Another issue is the consistency and reliability of natural fibers compared with that of, say, carbon fibers in terms of such attributes as diameter, strength and density.
Overall, textiles are transitioning to carbon-reducing materials however they make the most sense for their value. More and more, transportation segments will be under scrutiny for their sustainability efforts as fallout from regulators expands beyond the focus of EVs. Most are working towards solutions before that happens.