In September this year, imat-uve, a development and engineering company based in Mönchengladbach, Germany, intends to apply for Cradle to Cradle (C2C) certification for an automotive interior fabric made entirely from mixed fiber post-consumer clothing waste.
If successful, this will be a very major achievement, because not only are the automotive industry’s own quality standards extremely high, but C2C is perhaps the most stringent of all sustainable certification schemes a fabric can be put through.
Surprisingly, the fabric is being produced by a mechanical recycling process, without any chemical treatment, and simply relies on blended fibers being shredded very finely and then processed into a particularly soft, uniform card sliver by new spinning preparation technologies. Also surprising, the product will partly contain oil-based synthetic fibers, which are generally anathema to the C2C philosophy.
The fabric has been developed within the Dutch-German Intereg project, which has been ongoing since 2013, by a consortium comprising:
- imat-uve.
- Texperium, an open innovation center for textile recycling in the Netherlands.
- Dutch textile production consultancy FBBasic.
- Trützschler, a leading textile machine manufacturer which is also based in Mönchengladbach.
- Cradle to Cradle’s ExpoLAB, which specialises in the practical application of C2C principles.
Used workwear
Speaking during one of the series of webinars organized recently by the textile machinery branch of Germany’s VDMA, Michael Wolf, imat-uve design and development engineer said that the yarns for the fabric have been produced from used workwear consisting of 60% polyester and 40% cotton, as well as a portion of old clothes of unknown fiber blends and a percentage of raw polyester.
“Even yarns made entirely of the recycled fibers have been woven industrially without complications, with no thread breaks and little abrasion during subsequent weaving,” Wolf said. “Standard tests for the automotive industry have been passed in terms of durability and comfort, including Martindale tests for abrasion behavior, internal and external pilling and hot-light ageing.”
Yarns have subsequently been developed that are suitable for both the warp and weft of the woven fabrics.
“Mixed fiber recycling can also result in sophisticated designs, with the natural mixing of materials resulting in attractive coloration effects,” Wolf said. “We are not re-dyeing the fabrics but achieving the attractive appearance entirely through this [process], and samples are now ready for assessment.”
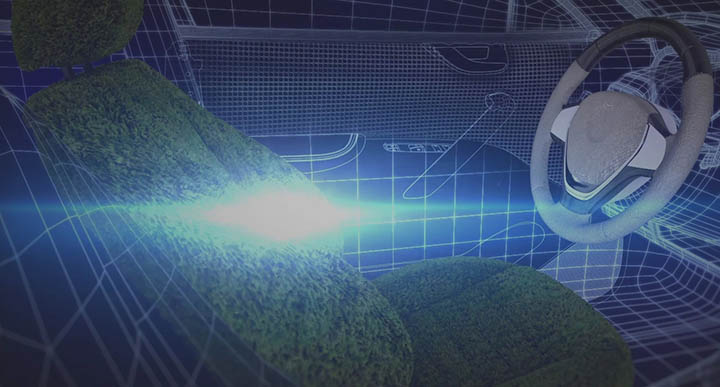
Continuous improvement
The C2C Certified Product Standard, which was first introduced in 2005, guides designers and manufacturers through a continuous improvement process, aiming to achieve a circular economy approach. It examines a product through five quality categories:
- Material health
- Material reutilization
- Renewable energy and carbon management
- Water stewardship
- Social fairness
A product receives an achievement level in each category – Basic, Bronze, Silver, Gold or Platinum – with the lowest achievement level representing the product’s overall mark.
The criteria at each level builds towards the expectation of eliminating all toxic and unidentified chemicals, and becoming nutrients for a safe, continuous cycle.
So far, the C2C Certified Product Registry lists just 612 separate products – across all industrial categories – with 59 being Gold standard and just one having achieved Platinum. It’s that demanding.
Material health
Cradle to Cradle operates the separate Material Health Certificate Registry for the simpler registration of the individual components of products, and listed under its basic materials are NatureWorks Ingeo PLA, seven separate Lycra elastane yarns, two Roica elastanes from Asahi Kasei and Enka’s viscose. All of these are certified Gold standard.
Only Naturalis, a natural wool yarn produced by Italy’s Botto Giuseppe has a Material Health Platinum rating in textiles-related basics, so to date, there is not a huge toolbox of raw materials already C2C approved for textile and garment designers to turn to for inspiration.
Denim pioneers
The biggest sector of the textile industry to have embraced C2C principles by far, however, is the denim industry – where differentiation is always key in a very competitive market – and the major denim producers that are based in the Karachi region of Pakistan have undoubtedly been the pioneers.
Karachi denim companies to have achieved C2C Gold for specific fabric brands are:
- Artistic Fabric and Garment Industries, for Earthmatics and Redfine
- Artistic Milliners, for Dylan
- Rajby Industries, for Greenmystery and Blue Magic fabrics
- Soorty, for Pure D and Smart Loop
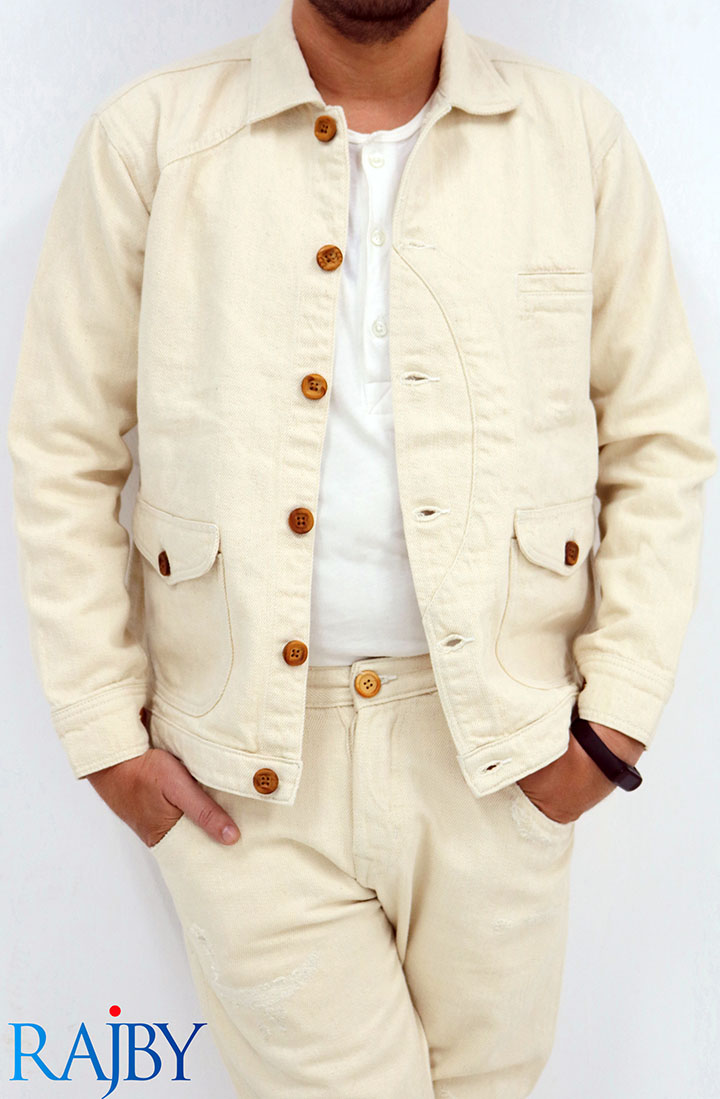
Platinum first
During 2020, however, Rajby Industries went a stage further and became not only the first denim fabric, but the first product – of any kind – to achieve the Platinum Cradle to Cradle (C2C) Certified Product Standard.
Rajby’s Beluga denim fabrics for retailer C&A gained the ultimate sustainability score in all five categories covered.
The fabric is based on 100% GOTS certified organic cotton and employs no hazardous chemicals in its production. At the same time, it is both recyclable and biodegradable, with 100% of the energy used in its production off-set by green energy and involving a closed loop system with no wastewater generated and no material wastage.
As such, Beluga denim fabrics, which range from 4oz to 13oz in weights in different woven constructions, represent a new zenith in circular denim production.
To meet the active cycling requirement, Rajby has committed to using Beluga denim fabric exclusively in apparel products sold by retailers who already have programs for taking back fabrics in place, such as C&A.
C&A led the research and quantification for the initial certification of Beluga fabric through its We Take it Back program and will track the active cycling rates through it.
Rigid requirements
Achieving C2C certification for a fabric is one thing, however, but achieving it for a finished pair of denim jeans is quite another, as C&A has discovered in other ambitious projects.
This is where the C2C standard is rather rigid, in applying the same five high standards to both a comparatively simple product such as a fabric, and to a product like a finished pair of jeans, involving numerous components and a wide range of supply chain partners.
With approximately 1,400 branches in 18 European countries and more than 31,000 employees, C&A, headquartered in Vilvoorde, Belgium, is one of Europe’s leading fashion retailers.
It is the world’s largest buyer of organic cotton and currently 67% of all of the cotton it uses is either certified organic cotton or sourced as Better Cotton, with a target set for shortly achieving 100%.
Back in 2017, C&A introduced the C2C Gold-certified Bio Cotton t-shirt, but due to the stringency of the system, a portion of the Bio Cotton t-shirts that reached C&A stores had to be labelled C2C Silver, due to the unavoidable use of certain inks.
Undeterred, the retailer then pushed on with having a pair of its denim jeans C2C certified – an elaborate process which involved the assessment of around 100 separate components.
Wear the Change
“Having successfully launched the Bio Cotton t-shirt – which retails at eight euros – under our Wear the Change banner, we decided to go for a bigger challenge,” explained C&A design manager Jens Hesse. “The stipulation was that the product had to be possible at a retail price point of twenty-nine euros per pair. The C2C certification program is without doubt the only holistic one on the market, but a huge list of chemicals involved in the denim jeans production chain had to go through this certification process.”
Components and raw materials for the jeans came from suppliers around the world, with India’s Arvind, for example, supplying the basic denim, Coats the sewing thread, Dystar the dyes and finishing chemicals, YKK various accessories and Freudenberg the cotton interlining for the waistband. Pacific Jeans in Bangladesh handled the cutting and sewing.
Challenges
One major challenge was in finding a suitable elastane just to add 1-2% stretch to the denims. This was eventually solved by using partner Asahi Kasei’s Roica V550, which is now registered C2C Gold.
However, once all the suitable components were identified and prototype pairs of the jeans were confirmed as C2C Gold, there was a further problem when it came to a full production run.
“The cotton thread we had selected for the stitching needed to be a lot stronger,” Hesse explained. “It was breaking far too much and totally slowing down production. Eventually, it had to be replaced with a polyester alternative, in order for production targets to be met and the price point retained.”
Unfortunately, due to the C2C stipulation that the lowest achievement level for a single component should represent a product’s overall mark, this meant that a proportion of the production run denims hit the stores bearing only Bronze labels.
So far, the C2C Certified Product Registry lists just 612 separate products – across all industrial categories – with 59 being Gold standard and just one having achieved Platinum. It’s that demanding.
Supportive
The C2C Platinum achievement of C&A and Rajby took place just before the COVID-19 pandemic struck, and the fashion retail industry has been hit hard by the pandemic, with many supply chain R&D projects left hanging.
C&A, however, has been very supportive of its supply chain, providing 100% compensation for all orders it was forced to cancel during the pandemic, so its pioneering work with suppliers on C2C is likely to resume in a good spirit once things return to normal.
Meanwhile, only one supplier to the automotive industry has so far achieved any C2C certified products – ZF Friederichshafen, Europe’s largest Tier One – for three small components unrelated to the textile industry. If imat-uve and its Intereg partners are successful with C2C certification this September, another milestone for sustainability will be set.