Forms of Cellulose, Including Waste, Have Potential to Offer Competitive Performance to Synthetics with Environmental Benefits
Novel forms of cellulose, including waste, are being developed to offer competitive performance to synthetics with environmental benefits. Some of these will be very familiar, such as cotton, but others such as lignin, less so. As the technology to manufacture these materials advances so is the exploration of application areas where they have the potential to reduce e-waste and reuse valuable metals currently being lost to landfill and waterways.
Fiber manufacturers, textile designers and traditional craft techniques from Japan are all exploring the use of cellulose waste in quite different ways. Cellulose materials such as wisteria, banana leaf, cotton and hemp were traditionally used and reused in Japan, while fiber manufacturers and contemporary textile designers are also turning to materials such as citrus peel, pineapple and seaweed to produce jacquard woven fabric.
At Asahi Kasei’s Sustainable Polymers Lab in Japan, researchers are developing cellulose nanofibers (CNFs). The company has successfully combined CNF with polyamide and polyacetal and lab manager Tomofumi Maekawa, they hope to be in a position to offer commercial quantities in the next two years. The process predominantly uses wood fiber, but the company is also working with cotton linter, the “fluff” around the seed that carries a high cellulose content. The CNF has very good sliding properties that make it ideal for applications where movement and wear are issues, such as composite gears. The company are looking at large-scale applications such as the replacement of glass fiber reinforced plastics (GFRPs), to offer a more sustainable alternative to glass fiber. First there are issues of strength, scale for commercialization and cost to be overcome. Transparency will also be important, showing evidence of the environmental impact of the production and chemicals used, but ahead of that the source of the cotton itself. At launch, the automotive interior is likely to be the first major sector to adopt. It is a market that is ready, but also one that is already becoming populated.
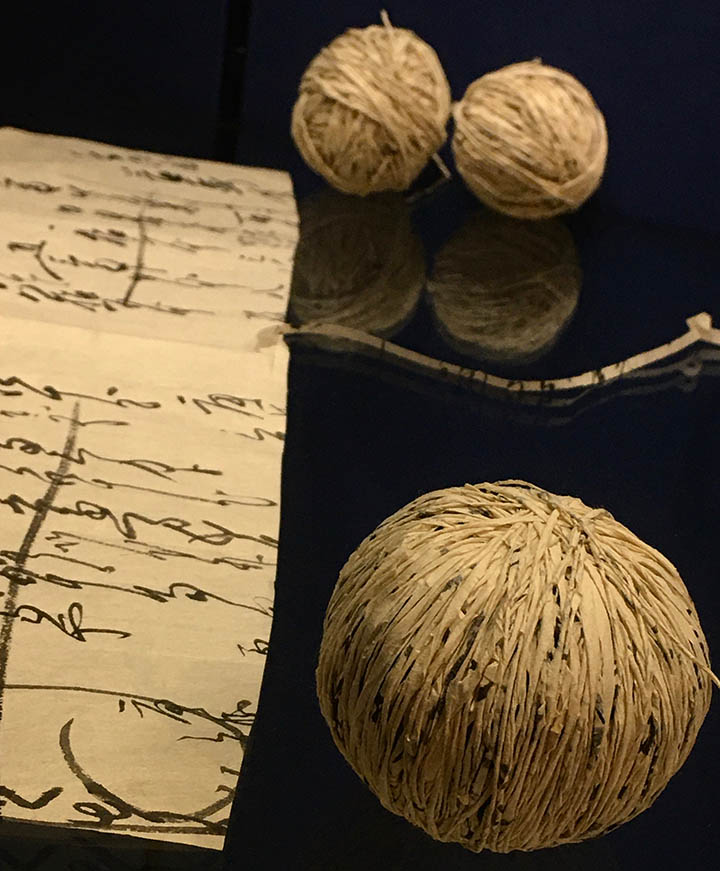
Researchers at the VTT Technical Research Center of Finland are addressing two environmental needs in their development of a biodegradable cellulose nanocomposite substrate for recyclable flexible hybrid electronics (FHE). FHE are most commonly printed onto a petroleum-based polymeric substrate such as thermoplastic polyurethane (TPU), with the use of different materials making it difficult to repair or recycle. There is a growing call for a green electronics industry, and as the sector grows and integration miniaturizes further. This development uses a composite comprised of a cellulose nanofilament (CNF) coupled with a hydroxyethyl cellulose (HEC). Studies so far indicate that it is well suited as a substrate for high-resolution printed electronics with good mechanical and optical properties. The researchers have used it to make an electrocardiograph (ECG) device and successfully tested it with human volunteers. Research has also been done on material degradation and the process for extracting metals with good results. The work looks to address limitations in paper as a source of cellulose for printed electronics where stretch, conformability and transparency are needed. E-waste is acknowledged to be one of the fastest growing waste streams with materials that are highly polluting such as mercury and lead, as well as high-value materials including gold, silver and lithium being released into the environment. The researchers at VTT tested the product for both soil and marine degradation finding that within weeks this could be achieved so that printing inks and electronic components recoverable and reusable.
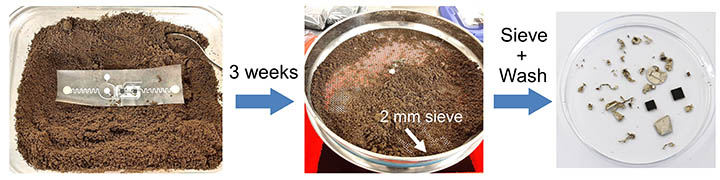
Lignin is derived from wood, usually extracted as a waste biproduct such as paper production. However, it has proven difficult to manufacture until now so that only an estimated 2% is being used commercially. The German Institutes of Textile and Fiber Research Denkendorf (DITF) have developed a process that allows them to manufacture carbon fibers from the cellulose. It offers energy-saving, environmental efficiencies and reduced cost. The process uses an aqueous solution of lignin.
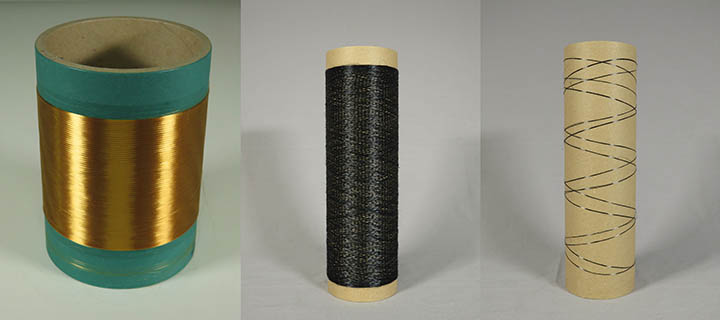
To do this the wood is separated into its components of lignin and cellulose. A sulfite digestion process enables the production of lignosulfate that is then dissolved in water. A dry spinning process is used to extrude the material through a nozzle and into a heated spinning shaft to produce a uniform continuous fiber, requiring no solvent or toxic additive. Following on from this, in order to produce a carbon fiber the lignin fibers are stabilized with hot air in an oven, achieved quickly and with relatively low temperature. This means an energy saving of around 50% compared with PAN. The resulting fibers offer sustainability and cost efficiencies, the DITF see the development as being of particular interest to the automotive and construction sectors.
European researchers in a recent paper in the International Journal of Molecular Sciences points to lignin as an environmentally benign building block that is under-utilized but with great possibilities across an array of applications, including Shape Memory Materials including polymers. The researchers from the Institute of Functional Materials in Germany, the laboratory of Polymers and Biomaterials and the Open University Affiliated Research Centre both at the Fondazione Instituto Italiano di Tecnologia, point to its potential in Shape Memory Polymers (SMP) in particular. A multifunctional lignin-based material based on maleic anhydride grafted polyethylene elastomer has been found to be sensitized to light with AL used as a photo-thermal agent. The smart composite has been shown to have excellent light-controlled self-repairing properties as well as a light-activated shape-memory performance with potential applications such as robotics and sensors. The lignin itself is not smart but contributes through its ability to convert light into heat. There is still much work to be done before reaching commercialization on lignin within SMPs. The lignin extraction process, the type of wood, its age, the environmental conditions where the wood is grown, and the different parts of the wood used are just some of the variables that can impact on behavior. The researchers are keen to point out in their paper “Lignin, the Lignification Process, and Advanced, Lignin-based Materials” that much of this is at proof-of-concept stage.
In Italy, Orange Fiber is using citrus juice by-products to produce sustainable yarns using a patented technology. The cellulose is obtained from the citrus pulp. The waste after extracting juice is referred to as “pastazzo,” and accounts for 60% of the weight of the fruit so that the company are creating value in a sustainable product while reducing waste in citrus growing regions, such as Sicily. Orange Fiber is developing fabrics with a number of partners including Tessitura Serica Taborelli, Tessuti di Sondrio and Candiani. Most recently they have collaborated with the Lenzing Group to create a Lyocell fiber using orange and wood pulp marketed under the brand TENCEL Limited Edition x Orange Fiber and used for apparel. The Danish textile designer, Tanja Kirst, specializes in textile weaving on a Jacquard loom. For the London Design Festival held in September this year, she created a collection of textile panels that combined hemp fiber with citrus peel as well as pineapple leaf fibers and seaweed yarns. All the yarns have been spun with bio-dyes at the TextielLab in The Netherlands.
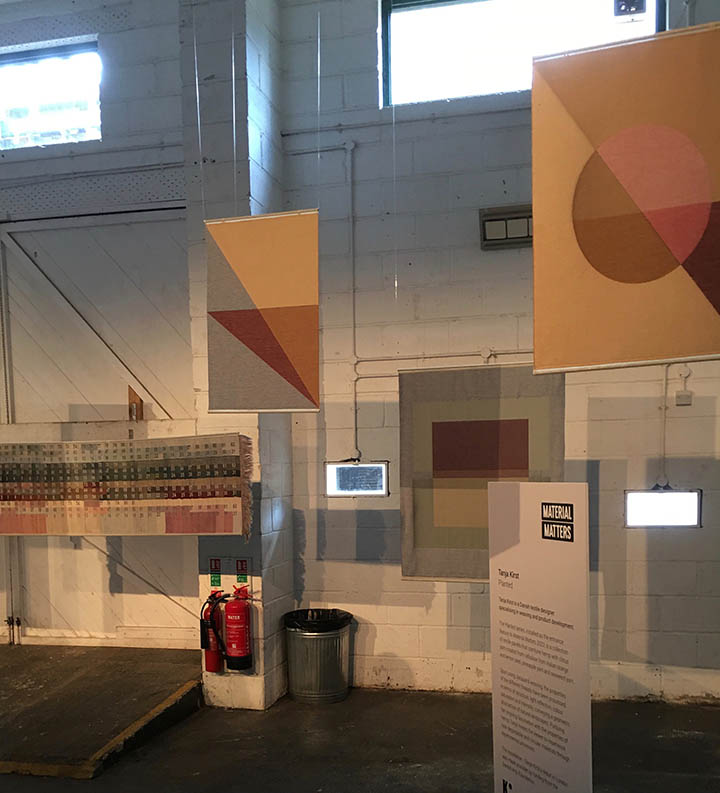
In Japan, wild banana leaves (Musa liukiuensis) have been used to provide fibers that are very fine and delicate. These were traditionally used to make a Basho-fu (banana fiber) jacket. Textile crafts such as this are being recognized as an important cultural tradition and afforded the title of Intangible Cultural Asset. In rural Japan, an ashehajiki is the name given to an undergarment referred to as a “sweat repeller.” The warp can be cotton and the thread for the weft made of paper. Siân Bowen is Artist-in-Residence (2022-2025) at London’s Kew Gardens. She is in the process of making a replica ashehajiki using abaca paper that is made from banana leaf and Japanese wheat starch.
The original garment dates from the nineteenth century and is housed in the Harry S. Parkes Collection of Japanese Paper in the garden’s Economic Botany Collection. Because the original garment has no seams, the only way that the artist could fully understand the garment was by the process of making it herself. This involves repeated plaiting, dividing and twinning four strands of the paper cord. A single line of plaits across the back of the garment takes around three hours to complete. This type of ethnographic research has an important role to play in inspiring new yarns and textiles. Not in a literal translation, but in their design, functionality, use and reuse of local material.
Twenty years ago, I visited Patagonia’s head office in California and one thing that I was not expecting to see was a small collection of ethnographic garments that I was told were the personal collection of the founder Yvon Chouinard. They included a Chinese fisherman’s bamboo jacket made of a lattice configuration not unlike the ashehajiki in the result, but a different structure made of tiny bamboo long “beads” brought together in a net-like structure. This became the inspiration for Patagonia’s Polartech grid fleece.
In a talk given to the American Society of Craftsmen in the middle of the last century, Charles Eames maintained that industry and craft had much to gain from one another. It would seem that we still have much to learn from one another.
*The Basho-fu jacket, as well as the ashehajiki jacket were exhibited at “The Japanese Aesthetics of Recycling” exhibition held at the SOAS Gallery, London July 13 – September 23, 2023.