The Focus of Asia Pacific Rayon Is on Sustainable Production of Viscose Rayon, says Tapan Kumar Sannigrahi
Asia Pacific Rayon (APR) is a leading integrated viscose rayon producer in Asia, with manufacturing operations in Riau province, in Sumatra, Indonesia. In November 2021, the company launched its APR2030 sustainability agenda, covering four main pillars, aiming for 20% recycled textile content, net zero land emissions, and halving product carbon intensity per ton of VSF production by 2030.
APR’s operations not only meet but surpass EU and industry standards like EU BAT, Polymer BREF, and RaoZero Discharge of Hazardous Chemicals Man-Made Cellulosic Fibres guidelines. It also undergoes yearly evaluations by groups like the Sustainable Apparel Coalition and other ESG reviews.
The company has adopted clean manufacturing processes as a key pillar of its APR2030 strategy. Efforts include capturing and re-using chemicals and chemical by-products, reducing and eventually eliminating the use of hazardous substances in production processes, treating and recycling wastewater, practicing proper waste management, and implementing air pollution control methods. In this issue we interviewed Tapan Kumar Sannigrahi VP, Marketing & Downstream Development, Asia Pacific Rayon.
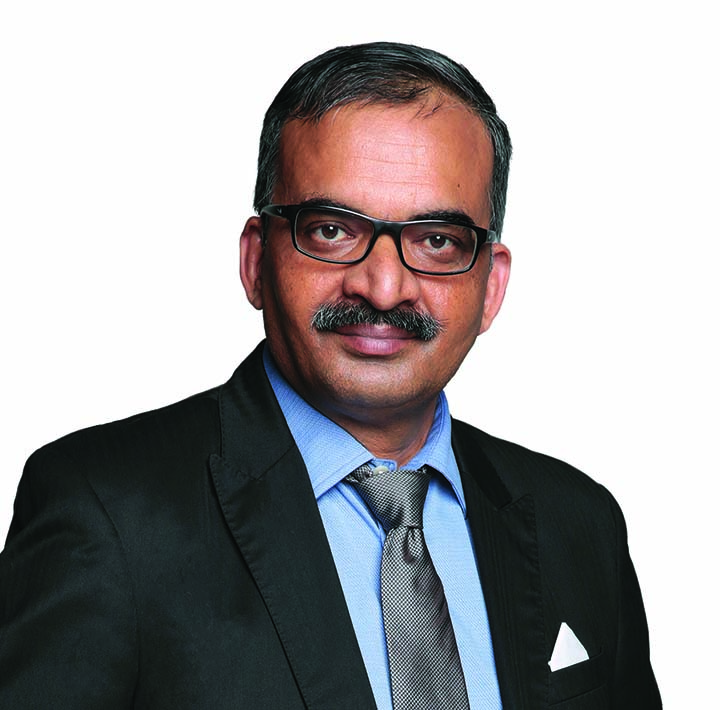
International Fiber Journal: Since we are doing an interview for the first time, please provide a history about your company, such as when it was started and about your facilities.
Tapan Kumar Sannigrahi: Asia Pacific Rayon (APR) was established in 2018 as a producer of viscose staple fiber (VSF) and is part of the RGE group of companies. Our manufacturing facility is located in Riau Province in Sumatra, Indonesia and our operations are vertically integrated from plantations to fiber, which is a unique differentiator for us. Our manufacturing plant, our VSF R&D department and our textile R&D facilities for spinning, knitting, weaving, dyeing and printing units are located in the same complex.
Sourcing from certified suppliers is critical to our activities and we are guided by APR’s Pulp Sourcing Policy commitments. We only source materials from suppliers with the necessary certification from the PEFC (Programme for the Endorsement of Forest Certification).
IFJ: Please share details about manufacturing infrastructure and annual capacity?
TKS: APR has two production lines and an annual cellulose fiber production capacity of 300,000 tons. We supply these fibers in 1.2 and 1.5 denier and in cut lengths of 32 mm, 38 mm, 44 mm and 51 mm. The first line was started in 2018 and had a manufacturing capacity of 200,000 tons per annum and then it was ramped up to 300,000 per year. With more than 50 percent market share, we are now the leading VSF player in Indonesia.
IFJ: What are the core company products and solutions you offer for the market?
TKS: Open End yarn manufacturers prefer 32 mm cut length, but some customers prefer 38 mm as well, while Ring and Vortex spinning mills opt for 38 mm. When cellulose fiber is blended with polyester fiber, the mills prefer 44 mm or 51 mm cut length, because it offers more productivity.
Our fiber is used in both knits and wovens. Knits are mainly used for womenswear and wovens are used in trousers, shirts, blouses and skirts. About 60 percent of cellulose fiber goes in to manufacturing 100 percent cellulose fiber fabrics or garments, while 40 percent is used in blending them with cotton, polyester, nylon or linen fibers.
IFJ: What is the role of R&D in developing products offered by your company?
TKS: Our R&D capabilities extend across the whole textile value chain beginning from plantations to fabrics. The R&D department has an automated pilot cellulose fiber production plant which replicates
the process of the main manufacturing plant. The R&D department also develops fibers based on customer demand. One example could be high tenacity fibers which help our customers attain higher productivity. The department also develops new strains of fibers for testing ahead of commercial production.
We also have a small spinning and fabric unit where the R&D department tests the various fibers that they develop by converting fibers first into yarns and then fabrics. These fabrics are further dyed or printed in the R&D department.
The department also develops various yarn types, like those which reduce yarn imperfections. The path adopted by our R&D department in developing a new yarn or fabric helps our customers develop their yarns and fabrics similarly. The R&D team also helps our fiber customers in improving quality and productivity and reducing costs, in line with our QPC – Quality, Productivity & Cost commitments.
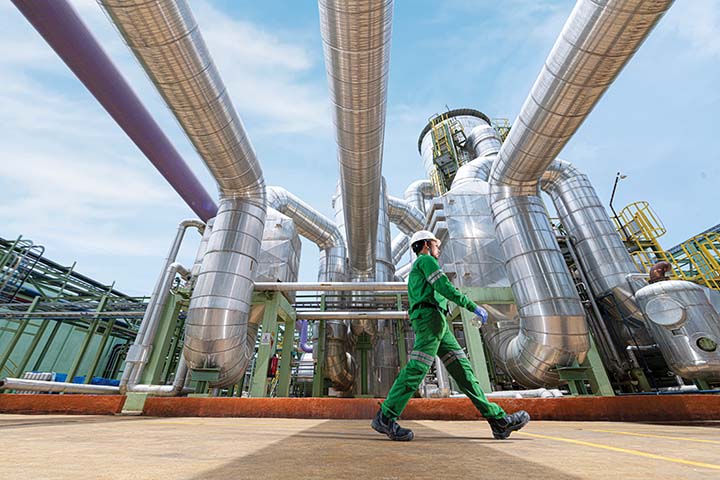
IFJ: Have you launched any new products recently or are planning to launch in the near future?
TKS: We are now coming out with Lyocell fibers which are third generation manmade fibers which have a manufacturing process different from other cellulose fibers. Lyocell is a stronger fiber and is closer to cotton, in properties. We also have plans to introduce recycled cellulose fibers as well.
IFJ: What were the main challenges faced by the cellulose fiber industry since the start of the pandemic and what more challenges do you foresee in the next few years?
TKS: COVID-19 created havoc across the whole value chain. There were significant supply chain disruptions, which affected our engagement with customers. However, our plant ran continuously during the two years of the pandemic, and we were very pro-active during the period in reaching out to customers to address their needs. So, there was relatively little impact on our operations
during the two years.
In terms of looking after our people, we created isolation wards for our infected employees within our complex and they received the best treatment. Testing was also done frequently and if anyone was infected, the people surrounding that person were tested. We had standard operating procedures in place to manage the wellbeing of our employees and stakeholders, overseen by a COVID-19 monitoring committee.
IFJ: Where do you see the cellulose fiber market share heading in the next few years in comparison with cotton and polyester fibers?
TKS: The market share of cellulose fibers is around 6.5-7.0 percent of overall fiber consumption which is around 110 million tons. The growth of overall fiber consumption in the last few years is around 3 percent, but that of cellulose fibers is around 6 percent. One reason for this higher rate of growth of cellulose fibers is because consumers now want comfortable, sustainable products and we are seeing this growth in our key global markets.
IFJ: What efforts is APR putting to increase per capita cellulose fiber consumption?
TKS: We have a very strong domestic cellulosic fiber textile and garment market in Indonesia and the Indonesian government is promoting “Made in Indonesia” products. We also have a Jakarta Fashion Hub, where the whole value chain is represented along with fashion designers and traders. We give a lot of support to the fashion hub in terms of sourcing, marketing, designing and new product development. For export markets, we take part in various international exhibitions as well as conduct customer meets to provide information and education on cellulose fibers.
In Indonesia, we have collaborated with a fashion retail chain called Matahari, where we have trained their
salespersons to talk about the benefits of buying cellulose fiber garments to consumers. We also release fashion trend collections every year to help our customers to visualize the upcoming trends of the next 12 months.
On a side note, our group manages a hotel in the same complex where our plant is located. All the textiles used in the hotel, like towels, bed sheets, table covers and napkins, are manufactured from our fibers.
“We are a relatively young company and we started out with sustainability at our core. In practice, this means we’re embedding sustainability in our policies, procedures, and in our approaches to everything we do.”
IFJ: APR has invested in circularity of its operations. Please share details of this project?
TKS: We have adopted a collaborative approach for circular textiles. We have partnered with spinning mills, weaving mills and garment factories to ensure that the pre-consumer waste is collected. We also have partners who segregate and sort the cotton or manmade and cellulose fibers pre-consumer waste. Once the cellulose fibers are sorted, they are recycled either through a manual or chemical process. In this too, we have partnered with Matahari, which collects used clothing, which is then sent to our sorters.
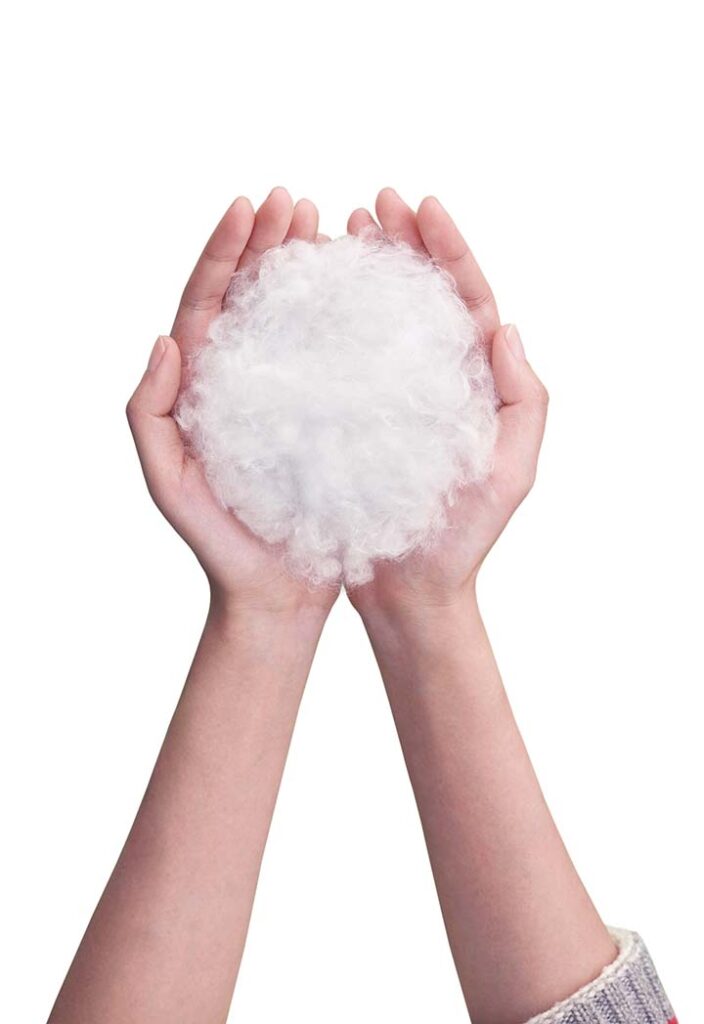
IFJ: How important is sustainability for your company? What sustainable products or solutions do you offer to your customers?
TKS: We are a relatively young company and we started out with sustainability at our core. In practice, this means we’re embedding sustainability in our policies, procedures, and in our approaches to everything we do.
In November 2021, we launched our APR2030 sustainability agenda, covering four main pillars and the corresponding targets for the next decade. Key targets include achieving 20 percent recycled textile content in our VSF production; net zero emissions from land use and halving our product carbon intensity per ton of VSF production.
We want to be seen as a world-class VSF facility. We continue to meet and exceed many requirements of the European Union Best Available Techniques (EU BAT) Polymer BREF and ZDHC MMCF guidelines, above and beyond local regulations. We have also submitted to annual assessments by the Sustainable Apparel Coalition and other ESG reviews.
We also look for independent, third-party certifications to confirm our sustainable production and approaches satisfy international requirements. For example, we look to improve the quality of our VSF and in turn the yarns, by adhering to standards that include OEKO-TEX®, FKT, and OK biodegradability labels.
Adopting clean manufacturing processes is a key pillar of our APR2030 strategy. Our efforts include capturing and re-using chemicals and chemical by-products, reducing and eventually eliminating the use of hazardous substances in our production processes, treating and recycling wastewater, practicing proper waste management, and implementing air pollution control methods.
Our efforts and processes comply with local regulations. They also align with international and industry standards, guidelines, and best practices, including World Health Organization guidelines, the Zero Discharge of Hazardous Chemicals Man-made Cellulosic Fibres (MMCF) guidelines. In 2022, we contracted an independent third party to assure our chemical recovery data ahead of new requirements coming into effect.
IFJ: Please share details on APR’s CSR activities?
TKS: In alliance with our main supplier, our sister company APRIL, we are also looking to eradicate extreme poverty within a 50-km radius of our operations. We are also looking to promote inclusive prosperity and gender equality, through livelihood initiatives aimed at women and young people, and better access to maternal health, integrated childhood development and nutrition programmes.
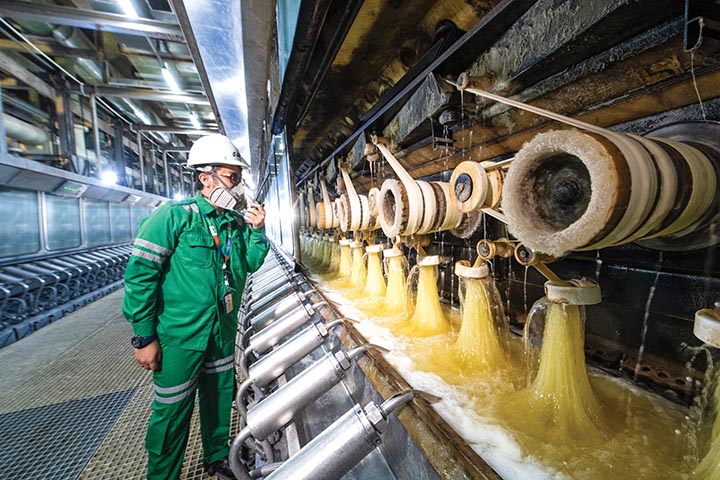
IFJ: What are the benefits of wearing a cellulose fiber garment vis-à-vis clothing made from either cotton or polyester fiber?
TKS: When buying clothing, everyone thinks of look, feel and comfort. The biggest advantage of cellulosic fiber clothing is that it drapes and looks well. The feel is also good and, when considering comfort, it has very good moisture management properties. It is also biodegradable. All these attributes make cellulosic fiber a very reasonable choice for consumers.
Cellulose fiber consumption in Indonesia is very high at around 20-25 percent of all fibers because Indonesia does not produce cotton. For example, one application is the sarong, a traditional men’s lower body dress which is made from cellulose fibers.
IFJ: What are the key trends in consumer demand and the growth trajectory of the Indonesian as well as global apparels market in context of cellulose fiber usage?
TKS: Consumers have now more disposable incomes and their lifestyles too have changed. Consumers now aspire for better quality apparels and also prefer more comfortable clothing. This is driving growth of cellulose fiber apparels. The growth projections of our group are matching the actual growth of demand for cellulose fibers worldwide. As of now, we expect cellulose fibers to grow at 6-7 percent annually.
IFJ: Please share details of your presence in the Indonesian domestic and export markets?
TKS: About 45 percent of our fiber production is sold in the domestic Indonesian market and the rest is earmarked for exports. We are now exporting to more than 16 countries with our main export markets being Turkey, Pakistan, Bangladesh, Vietnam etc.