Wearables & E-Textile Concepts Advance with Compelling Research & Development
Wearables are creating a demand for more sustainable and efficient energy, with energy harvesting high on the interest list. As functionalities increase, so does the demand for power. From the user’s point of view, this needs to be matched by invisibility in that the technology should be comfortable, lightweight, low bulk and generally unobtrusive to the wearer. Achieving this while maximizing energy density (the amount of energy that can be stored), is driving research and development towards flexible power and energy harvesting in particular.
Energy harvesting systems currently include perovskite solar cells, enhanced tribo-electric or piezo-triboelectric nanogenerators, biofuel cells, acoustic energy, piezoelectrics, thermoelectric generators and pyroelectric energy sources. In their ‘Diagnostic Wearables: the Future of Medical Monitoring’ report (2022), global electronics leader Molex found that energy generated by movement was seen by design engineers for wearables as the most promising alternative to solar for energy harvesting. While solar energy dominates the alternative energy sector, in the drive to incorporate energy more seamlessly into the fabric fiber and yarn are offering solutions that are both positive for the environment and the consumer.
One thing that most of the developments have in common is government, government body or inter-government backing. Many of the developments discussed in this feature have such funding and over a reasonably long timeline that is indicative of its importance, complexity and the work needed to reach full commercialization. GRAPHERGIA is a European consortium of eleven partners across six European nations looking to transform how energy is used and stored through the use of graphene. The 3.5-year project was launched in November 2023 with €4.5 million ($4.9 million) as part of the Horizon Europe Graphene Flagship initiative. The focus is on achieving scale and cost efficiencies envisaging a generation of wearables that can adapt to the body, connecting the wearer seamlessly while being self-charging. Research has shown that as the capabilities multiply, the demand for power also increases. The consortium are also developing the next generation electrodes for Li-ion batteries, looking to enhance battery life and performance while minimizing environmental impact. Prof Spyros Yannopoulos, the project coordinator for GRAPHERGIA describes the consortium ambition to bring pilot-scale innovations to the marketplace while setting new benchmarks for the energy sector.
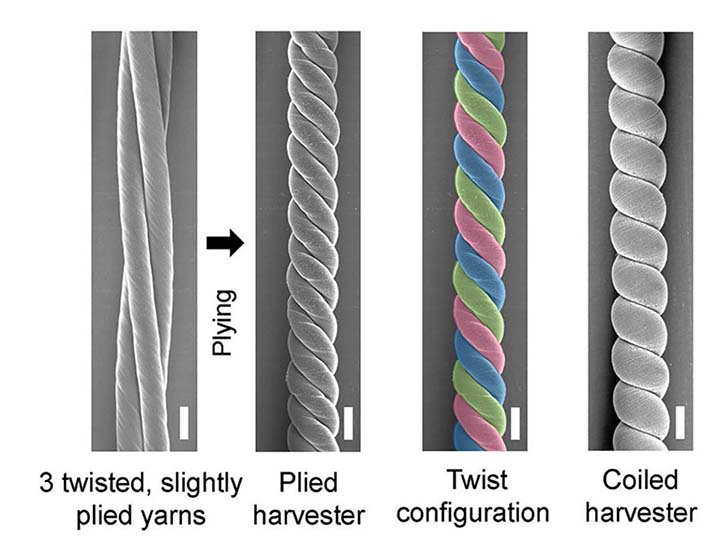
Spun carbon nanotubes (CNTs) is one of the processes being used to convert mechanical movement into electricity for energy harvesting yarns. At the University of Texas (UT) at Dallas, researchers are developing twistrons, an intertwining of three strands of spun CNT fibers to produce a single yarn for energy harvesting. These can be used to convert mechanical movement into electricity when they are stretched or twisted. The hollow nanotubes offer high strength to weight and mass, and they can incorporate electrolytes while retaining their nano scale that is 10,000 times smaller than a human hair in diameter. Initial development revolved around high twist that resulted in high elasticity with electricity generated by their repeated twist and release.
In the most recent development, researchers are looking at twist that replicates conventional ply yarns. One important difference is that while conventional yarns twist fibers in one direction then ply them in the opposite, the twistrons use the same direction for both, so that they are homochiral rather than heterochiral. The yarn is auxetic, becoming denser as it is stretched. This densification results in the CNTs being pushed closer together and enhances their energy harvesting capability. In tests the energy
conversion efficiency is 17.4% when stretched and 22.4% for twist reaching a peak of 7.6% energy conversion efficiency for both tensile (stretch) and torsional (twist) energy harvesting. Researchers have carried out a number of proof-of-concept experiments including one that simulates the generation of electricity by attaching the twistron between a balloon and the base of a salt-water aquarium. Repeated stretch of the lightweight yarns weighing just 3.2 milligrams has proven sufficient to power five small light-emitting diodes (LEDs) and a humidity/temperature sensor. The technology is patent pending.
Structure in Play
Researchers at Riga Technical University in Latvia are focused on the structure of the energy harvesting fiber to maximize its potential within a garment. They are developing flat coils that form a spiral, functioning as inductors by placing them in a sequence of four, and allowing the motion of permanent magnets placed along them to harness electrodynamic human motion energy. The sequence is placed is placed in a two-by-two formation to form a square with the induction coils placed in the corners and connected in a series circuit. This is motivated by the need to address the issue of clothing movement, allowing the spiral to move more dynamically with the wearer.
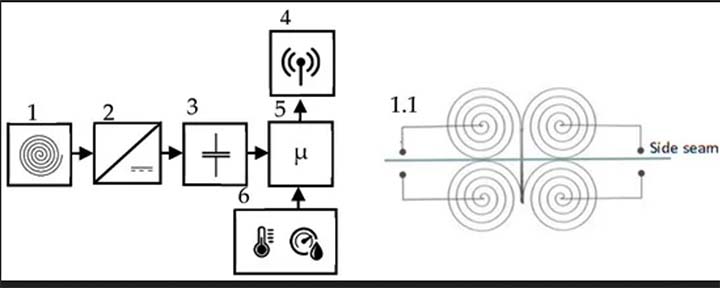
Examining the longevity and to reduce maintenance and laundry, the researchers are looking at protecting fibers against bacteria growth. They are doing this by using a sol-gel nanocoating. This is a multi-functional finishing treatment can be applied to offer water repellency, protection against microorganisms and dirt making it hydrophobic and self-cleaning thereby extending the lifetime of the
garment and electro-conductive yarns that would otherwise lose their electrical conductivity during wash-cycles and exposure to environmental bacterial and human sweat.
Structure is coming to the fore as an area of investigation, both of the fiber itself and the fiber matrix for self-charging power cells (SCPC) also referred to as piezoelectric SCs. The SC being an electro-chemical energy storage device that includes a polymeric separator that provides insulation and moves the electrolyte ions towards the opposite charged surface during the charging process and is also capable of reversing the action. Piezoelectric nanogenerators can include piezoelectric, triboelectric and hybrid forms that function by converting mechanical energy into electrical.
Part of the excitement around the technology is their potential to be combined with other technologies forming self-powered sensors and implantable medical devices for example. As a piezo-electric driven SCSPC the piezo-electric separator (such as PVDF, siloxane-polyvinylidene fluoride) replaces the polymer. The importance of this is that it allows the device to self-charge with the piezo potential across the separator acting as a power source when subjected to mechanical pressure.
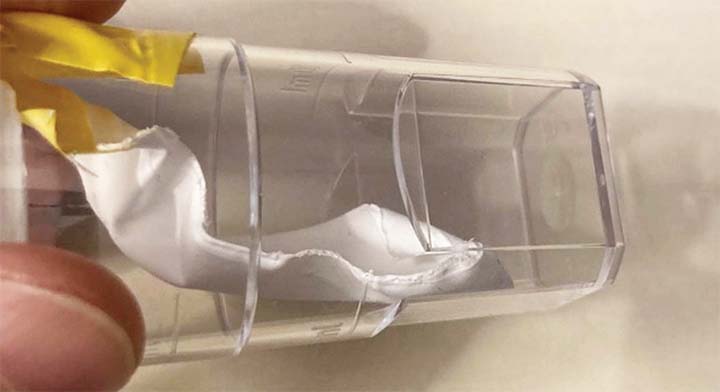
In research taking place at the Jeju National University, South Korea and funded by the National Research Foundation of Korea (NRF), the PVDF piezo fiber is fabricated by electrospinning to create a nonwoven-like matrix. This offers a number of benefits such as the control of thickness, density, surface texture and porosity. The researchers have noted that the mechanical stretching (produced using a cone jet process), coupled with electrical poling (with the polymer precursor solution is subjected to an electrical field) brought together in the electro-spinning process results in the formation of PVDF nanofibers with a high concentrate of electroactive ß phases.
This is one of the requirements for a strong piezo response and sensing capability. Although considerable progress has been made, the researchers acknowledge that there is still more to be done across many areas such as increasing the self-charge rates, investigating novel probing methods in addition to validation and testing.
Hybrid Energy Storage Devices
As the demands of wearables increases, one solution to energy may be in hybrid energy storage devices (HESD). Researchers at the University of Southampton in UK are looking at the potential for combining a textile secondary zinc ion battery in parallel with textile super capacitors to provide a HESD that is 100% textile.
The textile is prepared using a polymer membrane that fills the gaps in the woven textile structure. This allows for control of the amount and the absorbency depth of manganese oxide cathode and zinc anode that is then sprayed over the coated fabric. The uncoated area acts as the battery’s separator. The textile battery cell achieves good wettability of the electrodes with the electrolyte using a vacuum impregnation process.
Positive results are being found by combining a textile zinc ion battery (TZIB) in parallel with a textile super capacitor (TCT) in the HESD using a single polycotton fabric. In tests, the hybrid approach has been shown to deliver a 256% increase in energy density, with a 4.8% increase in power compared with a textile zinc ion battery alone. The addition of the TSC to the HESD is seen to improve the energy density above the sum of its parts.
The addition of a parallel connected textile supercapacitor offers further improvements to the energy storage as well as offering protection to the battery against high power spikes. The system offers flexibility and the potential to maximize energy and power densities alongside a low footprint making it well suited for future wearables.
Thermoelectric generators (TEGs) have the ability to convert body heat to electricity. Conventionally these are rigid devices, but researchers at NC State University’s ASSIST program have developed a flexible
TEG that is patented and now ready for licensing and full commercialization. The development uses industry-standard semiconductor pellets that are embedded in a flexible elastomer. Eutectic gallium-indium (EGain) liquid metal interconnects are used to connect the pellets and help to provide flex, stretch and electrical conductivity.
The amount of power generated is dependent on the size of TEG as well as temperature and air movement. This has potential across a range of wearables including sports performance, but because it is focused on body heat rather than physical movement, it is also well suited to medical and elderly monitoring. The group have also been developing analytical models in order to accurately predict the flexible TEG performance in a variety of scenarios. They are using a combination of analytic models and 3D numerical simulation. The first provides an understanding of the impact of different design considerations on performance, while the second delivers a more in-depth analysis of the TEG operation.
The modelling takes account of the human thermoregulation system as well as the device architecture, physical dimensions, thermoelectric materials and parasitic thermal and electrical resistances.
The model was launched in 2016 and has undergone a number of iterations since then. The current version takes account of the user’s age, gender, weight, and height with results indicating that older individuals generate around 30% less power than younger subjects. This has a bearing on the approach to design in maximizing the effectiveness of self-powered wearables in these sectors.
It seems not so long ago that the e-textile and wearables industry waited in eager anticipation for the advent of the lithium battery. In this new generation of energy harvesting there is clearly no one solution with each having its own set of benefits and challenges that have to be balanced. The end use and user will dictate which is more appropriate in a more nuanced way than we have seen previously, making cooperation between stakeholders, including design, at the early stage of development of great benefit.