Sustainability has been a dominant, if not the dominant presence in fiber and yarn developments throughout 2022 and shows no signs of abating in the near future. Manufacturers have, in the past, shown hesitancy to promote their environmental progress, often because of a wariness of being taken to task for not being fully circular, or even worse, accusations of greenwashing. What we are now seeing is a focus on very specific aspects of sustainability, rather than aim for full circularity all at once. This more targeted approach is being well received across markets. The common feature in each of the developments discussed in this feature is that they are all solution focused, addressing problems that exist in markets that range from geotextiles to apparel to transport.
Natural fibers for composites are receiving a much warmer reception today compared with a couple of decades ago. At this year’s JEC Composites trade show in Paris, booths such as CELC, The European Flax and Hemp Fibers Association attracted a great deal of attention.
Revered for their sustainable credentials, the fibers also offer a natural color pallet of cream to deep caramel, giving it a visual aesthetic quality that is quite distinct from the more established carbon fibers used. Part of the success might be attributed to an approach that does not try to compete with higher strength fibers, but instead emphasizes the environmental attributes as well as a color pallet that reinforces the message.
What we are now seeing is a focus on very specific aspects of sustainability, rather than aim for full circularity all at once. This more targeted approach is being well received across markets.
Bcomp is part of the next generation of manufacturers of sustainable fibers for composites and earned the 2022 JEC Innovation Award in the sports and leisure category. They began by using flax fibers to reinforce the balsa cores and improve shear stiffness for free rider skis. Based on the mechanical properties of flax fibers they achieved for this application, they expanded to develop sustainable lightweight solutions for the wider mobility market that now includes motorsports, automotive interiors, luxury sailing yachts, bridges and satellite panels.
In one development shown at JEC is a mini seat that was designed with Amplitex technical fabrics and Poweribs reinforcement. The thermoset composite is made using vacuum infusion. Aiming to achieve maximum stiffness with minimum weight, developers claim the result is the equivalent performance of a thin-walled monolithic carbon fiber composite achieved with an 85% lower CO2 footprint.
Biofibers Gain Momentum
Biofibers are increasing in popularity for high-performance applications offering an alternative to glass and carbon fibers. Bambooder has developed a technology to mechanically extract long bamboo fibers that are then processed to make an ‘endless’ thread without the addition of harmful chemicals. The use of the fibers carries a Young’s modulus up to three times that of the bamboo culm.
Bamboo native to temperate climates are being grown in the European region. Bamboo belongs to the grass family Poaceae, where the tribes of the woody bamboos, Bambuseae and Arundinarieae, and more precise the ‘giant bamboos’ (that can grow to 30 m with a diameter of up to 30 cm) are of special interest for composite applications. Bamboo genera that have been identified as potential sources for fibre extraction due to their anatomical characteristics and their common use in traditional construction are: Bambusa, Dendrocalamus, Gigantochloa, Guadua and Phyllostachys. Benefits are that it is fast-growing, abundant and can help with the reforestation of degraded land.
It is estimated that there are approximately 15 million hectares of ‘giant bamboo’ being grown and suited for fibre extraction. The high stiffness allows for less material to be used and is capable of producing very thin unidirectional prepegs, for example. The fiber has performed well in tests assessing the impact of moisture on its mechanical properties in a composite. Static conditioning revealed a smaller decrease in Young’s modulus with moisture content than other natural fiber reinforced composites such as flax. The behavior is attributed to the high lignin content. The influence of hygroscopic cycling was also assessed by Bambooder, with emphasis on the influence of the remaining parenchyma on the fiber. Clean fibers were shown to be beneficial for the long-term behavior with less deterioration in properties. Porosity analysis was performed via X-ray computed tomography to provide insight into the material structure of the composite and the effects of hygroscopic cycling.
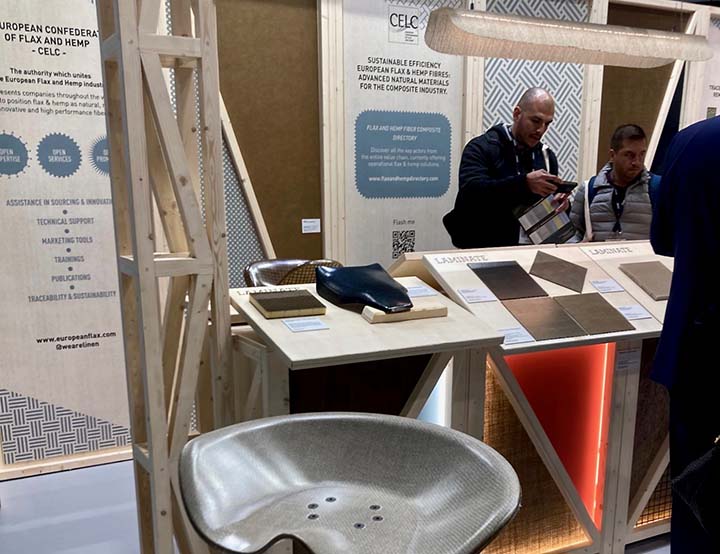
From Stone to Yarn
Basalt derived from stone is being produced by a number of manufacturers in yarn form. The AMANN Group has strong environmental policies across all products and offer some threads that have specific sustainable properties so that their basalt fiber sits within this product range. Basalt-tech is made from basalt stone fibers. It is corrosion, rot, chemical and UV-resistant. It is being manufactured in a natural grey stone color only at this time, with a high gloss appearance. The yarn is a reminder of the importance of technology alignment across the value chain. The yarn is smooth and slippery to work with so that weave, braiding and composite manufacturing processes in particular are crucial for market growth and development. JEC strongly featured sustainable options, including the basalt fibers.
Market for Sustainable Options
The global geotextiles market was estimated at $6.72 billion in 2021 and is expected to register a CAGR of 6.5% by 2030 according to a market research report by Grand View Research. The climate crisis is contributing to this growth, however, most of the geotextiles currently used are made using petroleum-based polymers that can take a very long time to decompose. Natural fibers do not offer an immediate solution as they can decompose too quickly – as soon as a few days. Biopolymers are attracting interest here with developments including a Lingnin coated natural fiber from the German Institutes of Textile and Fiber Research (DITF). Lingnin is a cellulose, a primary component of wood and can be sourced from the waste stream in paper production. It is thermoplastic and can be processed at 170°C, with additives that reduce inherent brittleness to create a homogeneous coating for natural fibers such as cotton intended for use in geotextiles, and flax for composites. The resulting yarn has good strength-absorbing properties with the coating adding a protective layer to bring longevity for the geotextile use-phase, at the end of which it will biodegrade. The yarn is currently in laboratory and open-air testing with positive results showing for each.
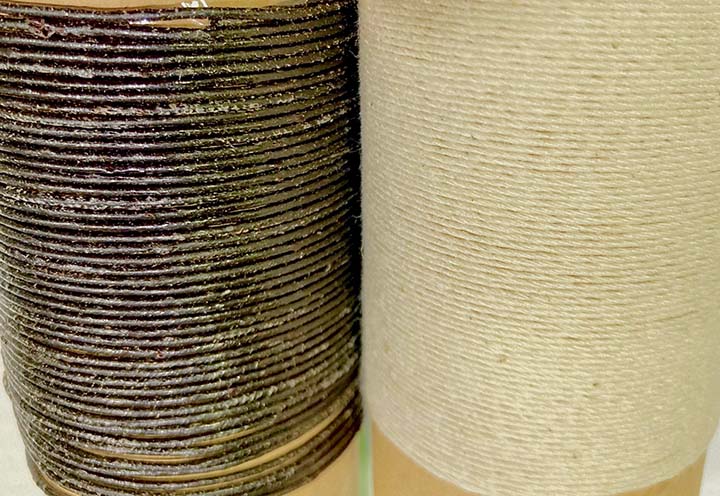
Identifying the potential of agriculture- and horticulture-related waste streams for textiles is a growing area of research and development for fibers. A prolific researcher, Yiqi Yang has worked throughout his career with farming communities in the Midwest, looking for ways to create value from what might otherwise be considered unusable waste. He received the Olney Medal in 2021, acknowledging his outstanding achievement in textile science. In one development, fibers are developed using poultry feathers with saccharide aldehydes used to perform cross-linking. Modifying the molecular structure of the aldehydes the keratin fibers produced from the feathers have been found to be stronger than other keratin-based fibers. Testing is showing good results for dry and wet strength as well as good dyeability and colorfast results when using acid dyes.
Uncorking the Possibilities
CORK-A-TEX takes cork waste and utilizes it as a coating for yarn resulting in a material that has a warm touch, is hypo-allergenic, with high friction resistance and good resilience. The initial funding came from the European Union (EU) and the Portuguese government. Portugal is the largest single producer of the material that comes from the cork oak tree and is a bio-based, renewable and natura. Although it is a recyclable material, used cork is very often simply burned.
The project has brought together the cork industry in the form of Sedacor (part of JPS Cork Group), and Téxteis Penedo with textile expertise, as well as Citeve and the Faculty of Engineering, University of Porto (FEUP) with a new company formed, Cork-a-tex to undertake R&D and bring about commercialization. Applications in clothing and home textiles are seen as well suited, with the non-reusable cork waste turned into paste and coated onto the yarn to form a special cork yarn.
Cork waste additives can be used on yarns and used in knitted, woven and nonwoven fabrics. This is now at the pilot stage, with the development receiving the accolade of an innovation award at the TechTextil trade show at Messe Frankfurt in 2019.
Reducing the environmental impact of fiber and yarn color and dyeing is a strong focus for the textile industry as well as brands that are looking at ways to reduce environmental impacts across the manufacturing process. The coloring of yarn and textiles can use 200 tonnes of water for every tonne of fabric. Low and fully waterless dyeing is attracting particular attention with processes such as ultrasonic, nano-dye and air-dye technologies eliminating or significantly reducing water use, pollution, as well as waste.
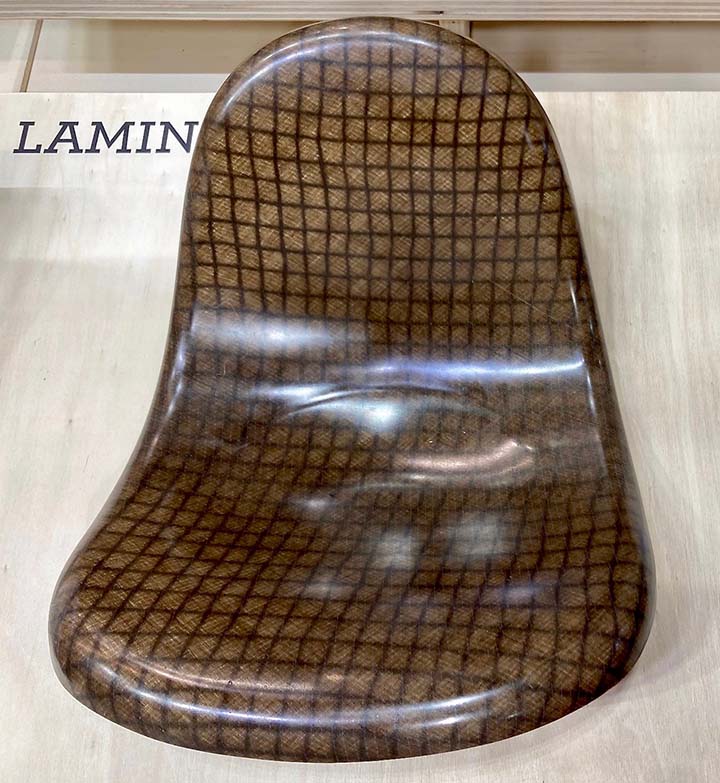
TWINE has developed a machine that offers a sustainable, waterless dye process for thread and yarn that utilizes inkjet printing technology. A wide range of colors can be used with color charts offered and users also given the opportunity to specify their own including multicolor options. Unlike many bespoke options for color, there are no minimum quantities needed, with only the amount of thread or yarn being colored that is required.
TWINE introduced the TS1800 to the North American market in January 2022 with several already installed. The white thread or yarn is used, and this starts by going through an industry standard tension. The next step inside the machine is to strip off the coating from the yarn or thread before it then goes into the dyeing chamber. The interface allows for a wide range of catalogue colors can be used as well as RGB, CYMK or LAB colors. The Coats catalogue colors are loaded onto the system, or the user can create their own. It then goes to be heated in the dye chamber and ensures the pigment penetrates and bonds with the thread or yarn fully. The yarn is then taken through a cooling chamber to capture any waste through condensation and removes it to the waste tray for disposal. The thread or yarn is then recoated with a lubricant and wound onto a bobbin or cone ready for use.
Let’s Be Clear
Transparency is an important issue that runs across industries whether to verify raw materials, authenticity, or other issues across the supply chain. Embedding a data check in the yarn is a much more effective way to achieve this than conventional paper systems that can be tampered with. Fiber Trace have developed a fiber-tracing technology that allows for data signatures to provide verification of a number of factors including provenance, the identification of base fiber content, the base fiber concentration, as well as the manufacturer and other specified data throughout the supply chain to the finished product. FiberTrace have just launched partnerships with Acatel advanced vertical finishing mill, and with the Suedwolle Group to provide verified, audited and real-time traceability for their patented luxury Escorial fiber.
Market drivers from across the textile value chain as well as application areas are converging to drive many of the new developments that we are seeing across areas such as biopolymers, biomimicry, transparency, inkjet printing and recycling.
As more stakeholders come together, it is clear that novel solutions are being found to a shared concern for the environment.